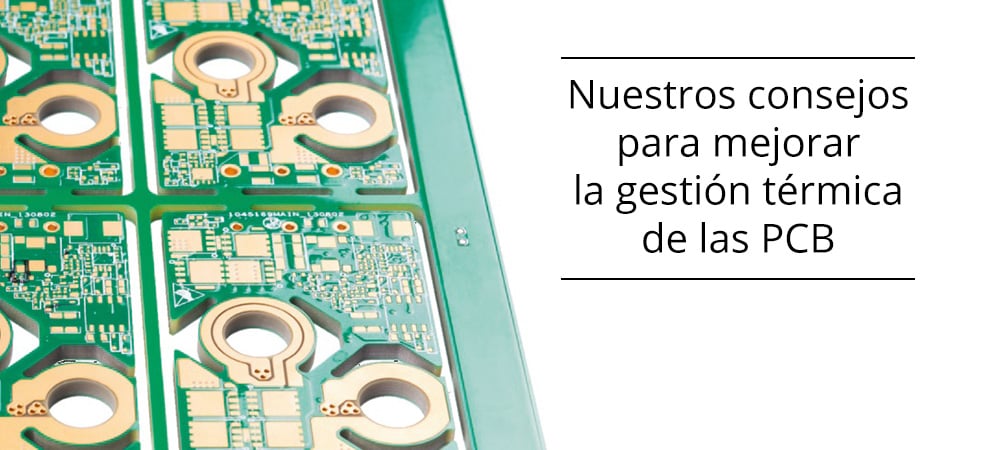
Las placas de circuito impreso, el corazón de cualquier dispositivo electrónico, están diseñadas para permitir la conducción eléctrica y la transmisión de señales analógicas y digitales entre diferentes componentes electrónicos. Durante su viaje por el interior de la PCB, la electricidad genera una cantidad más o menos elevada de calor, que depende de la cantidad de resistencia que encuentre. Además de las trazas, los componentes de potencia, tales como MOSFET, IGBT, convertidores y controladores, son principalmente responsables de la generación térmica. A pesar de que los voltajes de alimentación de los dispositivos lógicos altamente integrados, como DSP, SoC y FPGA están disminuyendo progresivamente, estos dispositivos también generan una cantidad de calor nada insignificante, debido tanto a las altas frecuencias operativas como al uso intensivo de algoritmos muy complejos. La gestión térmica es uno de los aspectos más críticos e insidiosos con los que los diseñadores se enfrentan en el diseño de una PCB. Por un lado, es necesario asegurar el funcionamiento correcto y la fiabilidad del circuito con cualquier valor de voltaje, corriente y frecuencia admisible; por otro lado, es necesario respetar las restricciones presupuestarias impuestas por el fabricante, limitando el uso de soluciones de refrigeración engorrosas y caras, como es el caso de los disipadores térmicos, ventiladores o refrigeración líquida.
Importancia de la gestión térmica
Los actuales componentes con base de silicona tienen una temperatura de unión comprendida entre unos 125°C y 200°C. Sin embargo, es necesario evitar alcanzar este valor, de lo contrario la vida residual del componente se deteriorará rápidamente. De hecho, se estima que un aumento en la temperatura operativa de 20°C, debido a una gestión térmica ineficiente, puede reducir la vida del componente hasta en un 50%. Los sistemas de iluminación LED de gran luminosidad, por ejemplo, convierten más del 60% de la energía absorbida en calor y, por lo tanto, requieren placas de circuito impreso especiales, capaces de soportar altas temperaturas sin causar daños a los componentes. La creciente popularidad de los semiconductores wide bandgap (WBG) o de banda ancha prohibida, como el arseniuro de galio (GaN) y el carburo de silicio (SiC), ha permitido a los componentes alcanzar temperaturas operativas más altas que la tecnología basada en silicona. No obstante, esto no ha eliminado la necesidad de una gestión térmica precisa, capaz de distribuir uniformemente el calor generado, evitar la formación de puntos de acumulación de calor (puntos calientes) que representen un peligro y minimizar la pérdida de energía. La Figura 1 muestra un circuito electrónico sujeto a escaneo térmico por cámara de infrarrojos: las piezas en color rojo corresponden a los puntos de mayor concentración de calor.
Figura 1: Imágenes térmicas de la PCB.
Consejos para una gestión térmica adecuada
El primer paso para conseguir una gestión térmica satisfactoria incluso en presencia de cargas de potencia elevadas es identificar la temperatura de unión TJ del semiconductor y la resistencia térmica RT, en función de las características técnicas de cada componente. La primera puede deducirse de la ficha técnica del componente, mientras que la segunda se define como la diferencia de temperatura que se produce a lo largo de la trayectoria térmica. En particular, RT puede minimizarse reduciendo la longitud de la trayectoria térmica, o incrementando la conductividad térmica del material y la superficie de las pastillas de la PCB. Ambos factores afectan al diseño de la PCB que, por tanto, debe diseñarse desde el principio para satisfacer estos requisitos. La carrera desenfrenada hacia la miniaturización de los circuitos eléctricos impone serias limitaciones al aumento de las superficies de las pastillas. Por lo tanto, para mejorar la gestión térmica, el diseñador puede intervenir en relación con los siguientes dos factores:
- la longitud de la trayectoria térmica en la PCB debe ser lo más corta posible;
- los materiales y sustratos que integran la PCB, así como cualquier disipador de calor, deberán tener la conductividad térmica más elevada posible.
El primer requisito puede cumplirse adoptando precauciones especiales durante el diseño de la placa de circuito impreso, mientras que el segundo requiere efectuar una minuciosa elección de materiales durante las fases preliminares del proyecto, por ejemplo, en el estudio de viabilidad.
Diseño de la PCB
Las técnicas disponibles para el diseñador electrónico a fin de reducir la longitud de la trayectoria térmica en la PCB son diferentes. En primer lugar, es recomendable aumentar la distancia entre las pistas, obteniendo así una distribución más uniforme del calor en la capa y reduciendo el riesgo de creación de puntos calientes. No obstante, esta solución se ve a menudo limitada por la necesidad (como en el caso de los consumibles) de obtener un tamaño de PCB miniaturizado. Además de la distancia, la geometría de las pistas también es un factor muy importante. Las pistas que conectan componentes eléctricos deben ser lo más cortas y anchas posible, utilizando cobre con alturas gruesas en las pistas atravesadas por altas corrientes. Los valores mínimos recomendados para el ancho de las pistas, que están en función de la intensidad de la corriente que fluye a través de ellas, pueden obtenerse en los diagramas incluidos en la norma IPC-2221 para el diseño de PCB. Si se utilizan pistas demasiado pequeñas para una corriente determinada, existe el riesgo de obtener un rendimiento degradado o incluso de destruir algunos componentes electrónicos; en caso de duda, siempre es preferible utilizar pistas de mayor anchura. Otra técnica utilizada habitualmente consiste en insertar vías térmicas a lo largo de la trayectoria térmica. Las vías térmicas, que pueden ser chapadas o sin chapar, conectan las diferentes capas entre sí, permitiendo la circulación de aire fresco y evacuando el calor. Las vías térmicas chapadas son más eficientes, ya que el revestimiento de cobre permite acumular más calor. Además de las vías térmicas, otra técnica capaz de sustraer calor de los componentes consiste en crear grandes planos de cobre en la PCB, incrementando así la superficie capaz de dispersar el calor. Aunque la mejor disipación se obtiene con planos de cobre realizados en las capas superior e inferior de la PCB, allí donde la cantidad de calor intercambiado con el entorno circundante es mayor, estos planos también pueden crearse en las capas internas de la PCB. En aplicaciones eléctricas, una forma de conseguir una disipación térmica eficaz es mediante el empleo de tecnología de cobre pesado, desarrollada para incrementar la corriente y la resistencia térmica máximas tolerables de la PCB, sin incurrir en fallos u operaciones degradadas. Mientras que las PCB estándar tienen unas pistas con un espesor de 0,5 a 3 onzas (105 µm), la tecnología de cobre pesado utiliza trazas que pueden tener un grosor de hasta 60 onzas (2,1 mm), capaces de soportar corrientes de varios amperios. La Figura 2 muestra un ejemplo de una PCB fabricada con tecnología de cobre pesado.
Figura 2: PCB de cobre pesado.
Selección de materiales
Aunque el FR-4 (Nivel 4 de Retardo de Llama) es capaz de cumplir los requisitos de disipación térmica de muchos tipos de circuitos electrónicos, existen varias aplicaciones en las que es necesario utilizar materiales y sustratos específicos. Dichas aplicaciones incluyen circuitos en los que están presentes altas frecuencias y/o señales eléctricas, aplicaciones y dispositivos de radiofrecuencia (RF) donde, debido a su diseño sumamente compacto, no es posible utilizar disipadores térmicos u otros sistemas de refrigeración (electromédicos y consumibles, principalmente). Para obtener una mejor disipación térmica, el material debe tener una constante dieléctrica elevada (Dk). Si bien implican un mayor coste, los laminados Rogers cumplen este requisito gracias a un valor de Dk comprendido entre 6,15 y 11, en comparación con una Dk de alrededor de 4,5 que ofrece el FR-4. Además, este material posee una gran estabilidad ante variaciones de temperatura y frecuencia, reduciendo por tanto las pérdidas de potencia en todas las condiciones operativas. Otra técnica de fabricación, conocida como MCPCB (Metal Core Printed Circuit Board - Placa de Circuito Impreso de Núcleo Metálico), consiste en combinar sustratos de materiales con diferentes conductividades térmicas con planos metálicos, normalmente hechos de cobre. La tecnología MCPCB utiliza un preimpregnado térmicamente conductivo situado entre las capas de la PCB, cuya función consiste en extraer calor de los componentes y dirigirlo hacia los planos metálicos. La técnica MCPCB, que puede emplear un plano metálico individual o doble (tanto en la capa superior como en la inferior de la PCB), se emplea de forma generalizada en aplicaciones de iluminación con LED potentes o que dispensan amplia luminosidad. Si el calor producido se concentra en un pequeño número de componentes, también puede utilizarse la tecnología denominada copper coin. Aprovechando la gran conductividad térmica del cobre, se insertan piezas del mismo material en el interior o en la superficie de la PCB, normalmente bajo componentes de alta potencia.
y obtenga un presupuesto para su proyecto de PCBAs en 10 minutos!
Conclusión
El éxito en la gestión térmica parte de un diseño adecuado de la PCB. Actualmente, los diseñadores cuentan con una amplia variedad de técnicas disponibles para reducir la cantidad de calor generado y mejorar su dispersión. La elección de los materiales, las técnicas de fabricación y la definición del diseño son los pasos principales que hay que seguir para obtener unos resultados satisfactorios. La disponibilidad de herramientas de software capaces de realizar un análisis térmico CFD (Computational Fluid Dynamics - Mecánica de Fluidos Computacional), también en 3D, permite a los diseñadores simular cómo se produce la transferencia térmica en todo el circuito, orientándolos de antemano hacia la solución más adecuada para la aplicación concreta.