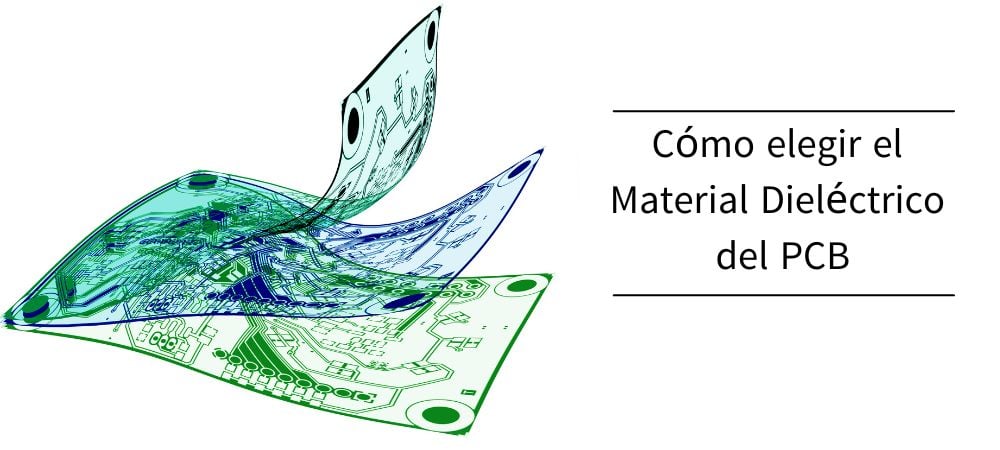
Los materiales dieléctricos constituyen la base de toda placa de circuito impreso, formando el sustrato no conductor que se inserta entre las capas conductoras del PCB, tal como se muestra en la Figura 1. Los materiales dieléctricos serán malos conductores de la electricidad y aportarán una capa aislante entre las capas conductoras. Tal como veremos de forma más detallada en el artículo, uno de los materiales dieléctricos de uso más generalizado es el FR-4, pero existen otros tipos de materiales que el diseñador debe conocer y seleccionar en función de las características de la aplicación concreta.
La selección del material dieléctrico debe efectuarse esencialmente en función de las propiedades eléctricas, térmicas y químicas del propio material.
y obtenga un presupuesto para su proyecto de PCBAs en 10 minutos!
Figura 1: Estructura básica de un PCB
Propiedades Eléctricas
Deben tenerse en consideración dos propiedades eléctricas principales a la hora de seleccionar un material dieléctrico, que son la constante dieléctrica y el factor de disipación.
Constante dieléctrica
Este parámetro, representado por el símbolo Dk, se indica también con el término permisividad relativa (Ɛr). La constante dieléctrica es una medida del grado de aislamiento eléctrico proporcionado por el material y es un factor fundamental para garantizar la integridad de la señal y el control de la impedancia. Los valores típicos de la constante dieléctrica que se encuentran en los materiales dieléctricos utilizados habitualmente en los PCB oscilan entre 3,5 y 5,5, pero este valor depende estrictamente de la frecuencia de la señal y disminuye según esta aumenta.
Al diseñar un PCB, es preferible seleccionar materiales con un bajo valor Dk, que puedan por tanto funcionar como aislante para las trazas de cobre y para los planos de alimentación eléctrica. Asimismo, el material seleccionado debe ser capaz de mantener el valor de Dk lo más constante que sea posible, tanto cuando la frecuencia operativa de la señal varía, como a lo largo de toda la duración prevista para el circuito.
A fin de asegurar un funcionamiento fiable y estable del circuito en el tiempo, se recomienda una constante dieléctrica que se mantenga estable en una amplia gama de frecuencias. La Figura 2 muestra la tendencia de Dk según varía la frecuencia en un material dieléctrico expresamente diseñado para altas frecuencias.
Figura 2: Curvas de frecuencia Dk para algunos materiales de la serie RO4000 (Fuente: Rogers Corporation)
Factor de disipación
Representado por el símbolo Df e indicado también como tangente de pérdidas (Tan δ), este parámetro indica la facilidad con la que un material introduce pérdidas de energía. Un material dieléctrico perderá menos energía cuanto menor sea el factor de disipación.
La tangente de pérdidas de los materiales dieléctricos utilizados habitualmente para la fabricación de PCB se sitúa entre 0,02 y 0,001 y este valor aumenta con la frecuencia. Particularmente relevante en los circuitos analógicos, este parámetro adquiere una importancia relativa en los circuitos digitales, como mínimo a frecuencias por debajo de 1 GHz.
Propiedades térmicas
Cuando las corrientes eléctricas atraviesan un PCB, este desarrolla una cierta cantidad de calor que causa tensiones térmicas en los materiales dieléctricos, las trazas y los componentes. Con el tiempo, el calor puede hacer que los materiales se expandan, provocando fisuras, daños en las pistas y soldaduras, o incluso fallos.
Al seleccionar un material dieléctrico, es esencial evaluar su conductividad térmica, que es su capacidad para disipar el calor con seguridad sin que ello afecte al funcionamiento del PCB. Otras propiedades térmicas importantes son el índice de expansión térmica del material, también conocido como coeficiente de expansión térmica (CTE), la temperatura de transición vítrea (Tg) y la temperatura de descomposición (Td).
Tg
La temperatura de transición vítrea (Tg) indica el umbral de temperatura por encima del cual un material cambia sus características si está sujeto a calor. Más concretamente, un material dieléctrico para PCB se ablanda cuando se expone a temperaturas por encima de la Tg, y vuelve a endurecerse cuando se elimina el calor y la temperatura cae.
El FR-4, el material habitualmente utilizado en los PCB (Figura 3) tiene un valor de Tg comprendido entre 130 y 140ºC. Existen también materiales con una Tg media (150-160ºC) y alta (por encima de 170ºC). Cuanto más elevada sea la Tg de un material, mejor será su resistencia a las altas temperaturas.
Figura 3: El FR-4 es un material estándar para PCB.
Td
La temperatura de descomposición (Td) indica el umbral de temperatura por encima del cual el material dieléctrico comienza a descomponerse. Contrariamente a lo que sucede con la temperatura de transición vítrea (donde el material es capaz de recuperar sus propiedades originales cuando la temperatura vuelve a situarse por debajo del umbral), en el caso de la temperatura de descomposición los efectos no son reversibles sino permanentes.
Las temperaturas alcanzadas durante la fase de soldadura oscilan entre 200ºC y 250ºC, por lo que es preferible seleccionar un material con una Tg por debajo de este rango y superior a la Td.
CTE
El coeficiente de expansión térmica (CTE) indica la tasa de expansión de un material expuesto a temperaturas por encima de su Tg. Medido en partes por millón (ppm), el CTE está normalmente entre 10 y 20 ppm a lo largo de los ejes X e Y. El valor de CTE debe minimizarse a fin de evitar que el material del PCB se expanda en el plano X, Y.
K
La conductividad térmica (k) expresa la capacidad de un material para transferir calor. En la mayoría de los materiales dieléctricos, la conductividad térmica (medida en W/mK o en W/mºC) generalmente está comprendida en el rango de 0,3 a 6 W/mK. En cambio, el cobre tiene una conductividad térmica de 386W/mºC y, por tanto, es capaz de transportar el calor más rápidamente que un material dieléctrico.
Propiedades químicas
En general, es preferible seleccionar materiales con una baja absorción de la humedad y una elevada resistencia química; en concreto, una gran resistencia al cloruro de metileno. También es muy importante la selección de materiales con propiedades ignífugas, capaces de resistir las llamas durante varios segundos (un ejemplo es el FR-4, un material con propiedades ignífugas de nivel 4).
La absorción de humedad expresa la capacidad de un material dieléctrico para resistir la inmersión en agua. La mayoría de los materiales dieléctricos utilizados en la fabricación de PCB tienen un valor de absorción de humedad comprendido entre el 0,01% y el 0,20%.
La resistencia a la absorción de cloruro de metileno es, en cambio, un indicador de la resistencia química de un material dieléctrico. Esta propiedad, medida por el índice MCR (Resistencia al Cloruro de Metileno), generalmente tiene valores comprendidos entre el 0,01% y el 0,20% en la mayoría de los materiales.
Selección de materiales
Examinaremos ahora los principales materiales que pueden utilizarse como dieléctricos en la fabricación de un PCB.
FR-4
El FR-4, acrónimo de retardante de llama de nivel 4, es actualmente el material estándar utilizado para la fabricación de PCB. Este material, elaborado con laminado epoxi reforzado con fibra de vidrio tejida, tiene propiedades ignífugas y cumple la norma UL94V-0.
Dado que se trata del material más ampliamente utilizado en la fabricación de circuitos impresos, el FR-4 es particularmente conveniente para los ciclos de producción de gran volumen. Sin embargo, este material presenta limitaciones en aplicaciones de señales de alta frecuencia y no es adecuado para disipar grandes cantidades de calor. Asimismo, la constante dieléctrica del FR-4 no se mantiene constante con las variaciones de frecuencia y ello puede generar problemas de integridad de la señal.
DPI/PPO
Los laminados de hidrocarburos termoestables (DPI y PPO) ofrecen una buena estabilidad mecánica, gran durabilidad y son fáciles de fabricar. Además de su excelente resistencia química, estos materiales dimensionalmente estables tienen una gran resistencia a la temperatura y representan una solución ideal para todas las aplicaciones cuya resistencia al calor soporta hasta 110ºC y que poseen una gran resistencia al impacto en un amplio rango de temperaturas. La absorción de humedad es muy baja y el material tolera también el contacto directo con agua hirviendo.
PTFE
Los materiales de Politetrafluoretileno (PTFE) se proponen como una alternativa válida al más habitual FR-4. Obtenido con un compuesto de carbono y flúor, el PTFE tiene una elevada temperatura de transición vítrea (de unos 120ºC).
El PTFE tiene excelentes propiedades dieléctricas que se mantienen incluso a muy altas frecuencias, convirtiéndolo en una solución adecuada para aplicaciones de RF de alta velocidad, alta frecuencia, microondas y alta potencia. La pérdida de señal es muy baja, se simplifica el control de la impedancia, y el rendimiento de la señal es excelente.
Poliimidas
Los materiales de poliimida se utilizan normalmente para fabricar las capas flexibles en los PCB flexibles y rígido-flexibles, ya que pueden doblarse y girarse fácilmente alrededor de los componentes sin comprometer el funcionamiento y el rendimiento del circuito. La poliimida ofrece también una excelente resistencia a las altas temperaturas, una buena disipación térmica, y resistencia a la humedad y química.
CEM-1, CEM-2 y CEM-3
CEM es una familia de materiales de PCB enumerados por NEMA que incluye tres categorías de materiales: CEM-1, CEM-2 y CEM-3.
Debido a su bajo coste, el CEM-1 es el material más ampliamente utilizado para la fabricación de PCB de una sola cara. Es un material compuesto hecho con una combinación de celulosa (papel) y una sola capa de fibra de vidrio entretejida con resina epoxi (FR-4). Este material no tolera la aplicación de agujeros chapados de orificios pasantes y, por tanto, solamente puede utilizarse para PCB monocapa. Como el FR-4, el CEM-1 es también ignífugo, pero las características mecánicas son inferiores debido a la mayor fragilidad del material.
La Figura 4 muestra un PCB fabricado con material CEM-1 (obsérvese el típico color blanquecino del mismo).
Figura 4: Ejemplo de PCB de CEM-1
Los materiales CEM-2 ofrecen mayores temperaturas de transición vítrea que los CEM-1 y están compuestos por un núcleo de papel celulósico y una superficie de fibra de vidrio tejida. Los materiales CEM-3 son compuestos epoxídicos de vidrio muy utilizados para PCB de doble cara con agujeros chapados.
Rogers
Los materiales Rogers, producidos por la empresa Rogers Corporation, aportan varias ventajas con respecto a los materiales dieléctricos tradicionales, como unas pérdidas de energía inferiores y menores pérdidas dieléctricas, mejor gestión térmica, amplio rango de valores de constante dieléctrica (desde un mínimo de unos 2,55 hasta un máximo superior a 10) y un mejor control de la impedancia. Aunque el coste es superior, los materiales Rogers son ampliamente utilizados en PCB para aplicaciones de RF y de alta frecuencia.
PCB con Núcleo Metálico
Los PCB con Núcleo Metálico, también conocidos como MCPCB, contienen un núcleo metálico cuya función es redirigir el calor alejándolo de los componentes más calientes. El núcleo normalmente está compuesto por una placa metálica de cierto grosor hecha de aluminio o aleaciones especiales. El aluminio es normalmente la opción más económica considerando la conductividad térmica, la rigidez y el coste. El grosor de los núcleos metálicos oscila normalmente entre 30 y 125 mil, pero pueden fabricarse núcleos más gruesos o más finos.
La principal diferencia entre un PCB de FR-4 y un MCPCB es el material dieléctrico con una alta conductividad térmica presente en el MCPCB, que actúa como puente térmico entre los componentes del circuito integrado y la placa metálica de soporte. La Figura 5 ilustra un ejemplo de MCPCB para aplicaciones de iluminación eléctrica.
Figura 5: Ejemplo de MCPCB
Criterios de selección
La selección del material dieléctrico más adecuado depende de los requisitos de la aplicación en concreto, tales como los niveles de tensión y corriente, la frecuencia máxima de las señales, la potencia desarrollada por los componentes y la cantidad de calor que debe disiparse.
Las siguientes directrices pueden ayudar al diseñador en esta fase:
- Uso de materiales con una constante dieléctrica muy similar. Si se utilizan materiales con valores de Dk muy diferentes, pueden generarse problemas de integridad de la señal y un comportamiento anómalo si la frecuencia varía.
- Uso de materiales con un coeficiente de expansión térmica (CTE) muy similar. Si esto no se produce, los materiales podrían expandirse con diferentes velocidades o en una medida distinta con respecto a los dos ejes X e Y, causando posibles daños al PCB y afectando al valor de Dk.
- Asegurar que los materiales dieléctricos produzcan superficies perfectamente lisas y suaves, a fin de no alterar el valor de Dk.
- Buscar siempre el compromiso correcto entre presupuesto y rendimiento. El FR-4 es un material excelente para muchas aplicaciones, mientras que en casos concretos (tales como aplicaciones RF de alta frecuencia, los LED de potencia o los circuitos HDI, por nombrar algunos) es preciso centrarse en materiales con un mayor rendimiento, aunque sean más caros.
La elección del material dieléctrico correcto permite la creación de PCB fiables y capaces de garantizar el mismo nivel de rendimiento en el tiempo y en condiciones eléctricas y térmicas variables a las que se somete al circuito.
Conclusión
El rendimiento ofrecido por un PCB, así como su fiabilidad y duración con el tiempo, dependen estrictamente de los tipos de materiales dieléctricos utilizados para su fabricación. Las propiedades térmicas, eléctricas, químicas y mecánicas son parámetros esenciales para la selección de un material dieléctrico y, por tanto, deben considerarse adecuadamente en la fase de diseño a fin de garantizar un funcionamiento óptimo del circuito impreso y del dispositivo electrónico en el que se utiliza.
15.12.2022