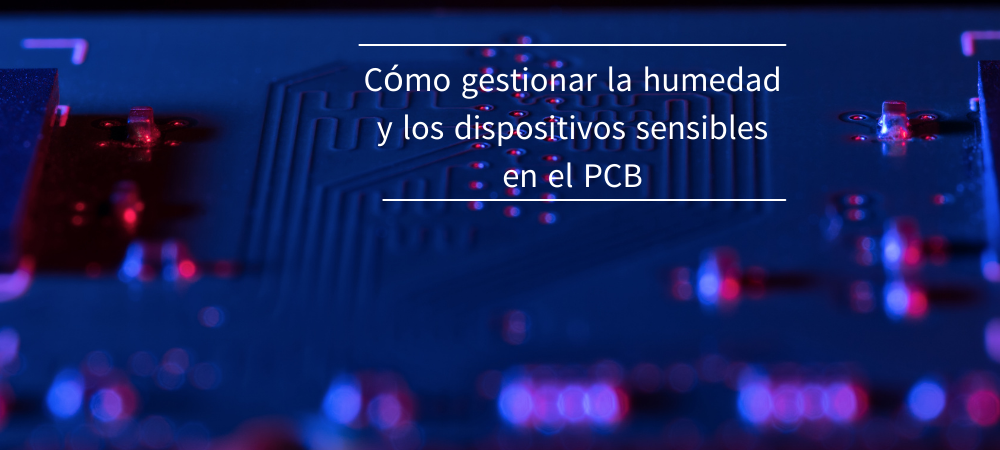
En los últimos años, los dispositivos electrónicos han sido objeto de una continua evolución que ha llevado a un tamaño cada vez más reducido, acompañado de unos rendimientos y unas velocidades cada vez mayores. Los PCB más pequeños, complejos y densos requieren una protección adecuada de las piezas electrónicas a fin de evitar posibles fenómenos de corrosión al exponerlos a la humedad y los contaminantes. Estos agentes, de hecho, pueden degradar el rendimiento de los circuitos o incluso provocar cortocircuitos y fallos.
La humedad, por ejemplo, puede provocar distintos tipos de fallos en un PCB, en función de los componentes o las pistas conductoras que entren en contacto con la placa. Los problemas más habituales relacionados con la humedad incluyen un desfase en la transmisión de señales, así como un aumento de los retrasos de propagación. Una vez superado cierto umbral, el circuito puede dejar de funcionar por completo.
y obtenga un presupuesto para su proyecto de PCBAs en 10 minutos!
Los dispositivos electrónicos pueden sufrir daños internos si no se manipulan y almacenan con la aplicación de los estándares específicos de la industria. Los componentes con matriz de rejilla de bolas o Ball Grid Array (BGA) y los paquetes a escala de chip son particularmente sensibles a la humedad y, lo que es peor, los daños en estos componentes pueden ser difíciles de detectar durante la inspección. La Figura 1 muestra un ejemplo de daños causados por la humedad en el PCB.
Figura 1: Daños producidos por la humedad en el PCB.
Componentes sensibles y MSD
Unas pocas gotas de agua pueden bastar para dañar irreparablemente un PCB, aunque una cantidad incluso inferior de humedad puede resultar nociva. La humedad representa un problema no solo durante el funcionamiento del circuito, sino también durante el almacenamiento de las placas, antes de su instalación.
El agua pura o desmineralizada tiene una resistividad de aproximadamente 1,8 x 107 Ω x m a 25°C, lo que la convierte en un aislante mucho mejor que un conductor de electricidad. En realidad, el agua con la que el PCB puede entrar en contacto contiene sales y minerales disueltos, cloruros, sulfatos y carbonatos. La presencia de estos materiales hace que el agua sea altamente conductora, lo que representa una potencial amenaza para la integridad de la placa de circuito impreso, provocando cortocircuitos y procesos de corrosión.
Una amenaza aún peor es la condensación, que se produce cuando la superficie del PCB está más fría que su entorno. La condensación puede formarse tanto en las caras externas de la placa como en el interior de los paquetes de componentes que, por tanto, deben seleccionarse teniendo en cuenta este aspecto.
Los componentes electrónicos especialmente sensibles a la humedad, identificados con el acrónimo MSD (Moisture Sensitive Device), requieren una protección adecuada tanto durante el proceso de montaje del PCB como durante la fase de almacenamiento de las placas terminadas en el almacén. Cuando un componente tiene un coeficiente de absorción de la humedad demasiado elevado, existe un potencial riesgo de dañar la placa, los componentes o las conexiones eléctricas entre ellos. Un exceso de humedad durante el proceso de soldadura puede causar daños en el material utilizado para el sustrato de la placa. Estos tipos de defectos no son fácilmente detectables y tienden a manifestarse solamente en el producto final o después de cierto tiempo de uso, lo que reduce drásticamente la posibilidad de remediarlos.
Los mayores riesgos se producen durante el proceso de soldadura por reflujo, cuando los componentes MSD se colocan en el PCB. Incluso las grandes variaciones bruscas de la temperatura ambiente pueden provocar la expansión o fisuras en el paquete. Un efecto muy común producido por la humedad es la deslaminación interna del material utilizado para construir el PCB. El FR-4 común, por ejemplo, es un material altamente higroscópico y, por consiguiente, es especialmente sensible a la humedad ambiental, con independencia de los métodos de encapsulado. Toda humedad que no se elimine durante las fases de soldadura se convierte en vapor, provocando deslaminación y microcavidades en las zonas más sensibles de la placa.
Normas del IPC para dispositivos sensibles
Las primeras normas relativas al control de la humedad en el PCB se publicaron en 2010 por el IPC, la organización inicialmente conocida como Instituto de Circuitos Impresos. Siguiendo estas normas, las placas electrónicas pueden durar más tiempo, siempre que se empleen técnicas adecuadas para disipar la humedad. Además, las placas protegidas por un revestimiento adecuado pueden mantener su soldabilidad durante períodos más prolongados, siempre que se tomen medidas para evitar que la humedad penetre en su interior.
Con arreglo a las mismas directrices, el horneado es un método práctico para eliminar la humedad de los PCB si no ha sido posible evitar su entrada anteriormente. Sin embargo, el horneado inevitablemente representa un aumento de los costes, una ampliación de los tiempos de producción y una menor soldabilidad. Este método, por tanto, debería evitarse en la medida de lo posible, siendo preferible en empleo en su lugar de las técnicas de mantenimiento preventivo durante el montaje y almacenamiento de los PCB.
Actualmente, existen dos normas publicadas por el ICP que pueden orientar a los fabricantes de productos electrónicos en la manipulación de componentes sensibles a la humedad: IPC/JEDEC J-STD-020E y IPC/JEDEC J-STD-033D.
IPC/JEDEC J-STD-020E
Esta norma ofrece un sistema de clasificación para determinar la calificación inicial de fiabilidad. Tras la identificación, los fabricantes pueden encapsular, almacenar y manipular los dispositivos para reducir los daños térmicos y mecánicos durante el proceso de reflujo.
IPC/JEDEC J-STD-033D
Esta norma proporciona una metodología de usuario final para la manipulación, el encapsulado y el envío de los MSD, así como procedimientos para aumentar el rendimiento y limitar la degradación de la fiabilidad.
Ambas normas dividen los niveles de sensibilidad a la humedad, o MSL, en clases numeradas del 1 al 6, dependiendo de su susceptibilidad a los daños inducidos por la humedad. Los niveles más elevados se aplican a los componentes sensibles que ofrecen mayor resistencia a la humedad. En particular, para cada clase, se indica cuándo tiempo puede permanecer el componente fuera de un sistema de protección frente a la humedad antes de requerir el horneado a fin de eliminar la humedad absorbida.
Como puede observarse en la tabla de la Figura 2, el nivel MSL 6 corresponde a los componentes más sensibles, que precisan hornearse incluso antes de su uso.
Figura 2: Las clases de MSL (Fuente: TI)
Los PCB, así como las placas terminadas, deben almacenarse y enviarse con el empleo de bolsas protectoras especiales (que por lo general proporcionan tanto protección ESD como contra la humedad), conocidas como bolsas MBB (Moisture Barrier Bag). En la Figura 3 se muestra un ejemplo de este tipo de bolsas.
Figura 3: Bolsas protectoras MBB
Cómo proteger los componentes y el PCB
A fin de proteger el PCB frente a la humedad, el mejor enfoque es intervenir adecuadamente en todas las fases de fabricación del PCB, así como en las fases posteriores de almacenamiento o envío.
Fabricación
Durante la producción de los PCB, el proceso de laminación debe realizarse en un entorno con temperatura y humedad controladas, utilizando, si es preciso, agentes desecantes adecuados. El personal debe llevar siempre guantes limpios al inicio de un nuevo lote de producción, evitando así la contaminación entre diferentes componentes. Durante el proceso de laminación, las diferentes capas que conforman el PCB se colocan y encolan para formar una única placa. Durante esta fase, algunos fabricantes aplican un efecto de vacío a baja presión, evitando la formación de huecos que podrían atrapar la humedad en su interior.
Otra técnica habitual consiste en el uso de placas de cobre con una estructura entretejida, para crear uniones más fuertes y evitar el movimiento de la humedad entre las diferentes placas del PCB. Sin embargo, debe tenerse en cuenta que estas estructuras pueden afectar al rendimiento eléctrico de la placa y su uso debe, por tanto, considerarse adecuadamente.
Tras la fabricación del PCB, puede aplicarse un acabado superficial con fines de protección. De esta forma, las propiedades del PCB se mantienen intactas hasta la siguiente fase de montaje.
Montaje
A fin de evitar que la humedad ambiental afecte negativamente al PCB, la soldadura de los componentes debe realizarse a elevadas temperaturas con un nivel de humedad inferior al 0,1%, o a bajas temperaturas con un nivel de humedad inferior al 0,2%. La soldadura a alta temperatura se realiza a una temperatura de alrededor de 260ºC, mientras que la soldadura a baja temperatura tiene lugar en torno a los 230ºC.
Tras completar el montaje de los componentes de la placa, el horneado es una práctica habitual y eficaz para eliminar la humedad. Sin embargo, es preciso asegurar que no se supere el coeficiente de expansión térmica (CET) del material utilizado para el PCB, evitando así la deslaminación o las fisuras.
Podría afirmarse que la mejor forma de protección para un PCB montado consiste en aplicar uno de los diversos tipos de revestimiento conformado disponibles. El revestimiento conformado no solo protege frente a la humedad, sino también de los fluidos, los contaminantes e incluso de los rayos ultravioleta.
El revestimiento conformado consiste en una fina película de polímero que se aplica al PCB para protegerlo y proteger sus componentes del entorno y la corrosión. La película suele tener un grosor comprendido entre 25 y 250 µm y tiene la propiedad de adaptarse a la forma de la placa y sus componentes, cubriendo y protegiendo frente a la corrosión los puntos de soldadura, los terminales y las patillas de los dispositivos electrónicos, las trazas expuestas y otras zonas de cobre, lo que prolonga la vida útil del PCB.
La figura 4 muestra los efectos corrosivos producidos en el PCB por la humedad u otros agentes agresivos en el caso de una placa sin revestimiento conformado (imagen de la izquierda) y con revestimiento conformado (imagen de la derecha). Estos revestimientos forman una capa uniforme que cubre las superficies de la placa, proporcionando una excelente repelencia de la humedad, los aceites, la suciedad, las huellas dactilares y otros contaminantes ambientales. El revestimiento conformado proporciona protección frente a diversos agentes corrosivos tales como la humedad, el agua, la niebla salina, la bruma y el azufre.
Figura 4: Placa con y sin revestimiento conformado (Fuente: 3M)
El encapsulado, que consiste en la completa introducción de un PCB montado en el interior de una carcasa protectora, también puede resultar un método muy eficaz, siempre que la carcasa permita que la humedad atrapada salga al exterior, por ejemplo, a través de respiraderos.
Una alternativa al encapsulado completo consiste en el recubrimiento parcial de la placa mediante resinas epoxi adecuadas que cubren sólo algunas zonas del PCB especialmente sensibles a la humedad.
Almacenamiento
Las placas de circuito impreso (montadas o no) deben almacenarse en bolsas protectoras MBB adecuadas y no en sobres que solamente proporcionan protección ESD.
Los diseñadores también deben observar las directrices contenidas en las normas del IPC, que proporcionan valiosas recomendaciones para el encapsulado y el almacenamiento de dispositivos electrónicos, minimizando así la posibilidad de difusión de la humedad.
Si no se aplica la protección contra la humedad a los PCB, pueden producirse fallos en los PCB, generándose costes innecesarios en concepto de reparaciones o sustituciones. Sin embargo, aplicando las técnicas enumeradas anteriormente para la fabricación, el montaje y el embalaje o almacenamiento, es posible reducir en gran medida la posibilidad de que la humedad y otros agentes similares amenacen el funcionamiento y la fiabilidad del PCB.
Conclusión
Con la tendencia actual hacia la miniaturización y el crecimiento de la densidad de componentes, los diseñadores se enfrentan a nuevos desafíos para dotar a los PCB de un nivel adecuado de protección contra la humedad y los agentes corrosivos. Los Dispositivos Sensibles a la Humedad, o MSD, tienen una mayor sensibilidad a la humedad, que puede hacer que los dispositivos devengan inoperativos. En el artículo se han descrito las principales técnicas que, aplicadas durante las fases de producción, montaje, almacenamiento y transporte de una placa electrónica, permiten proporcionar una protección válida y duradera al circuito electrónico.
20.03.2023