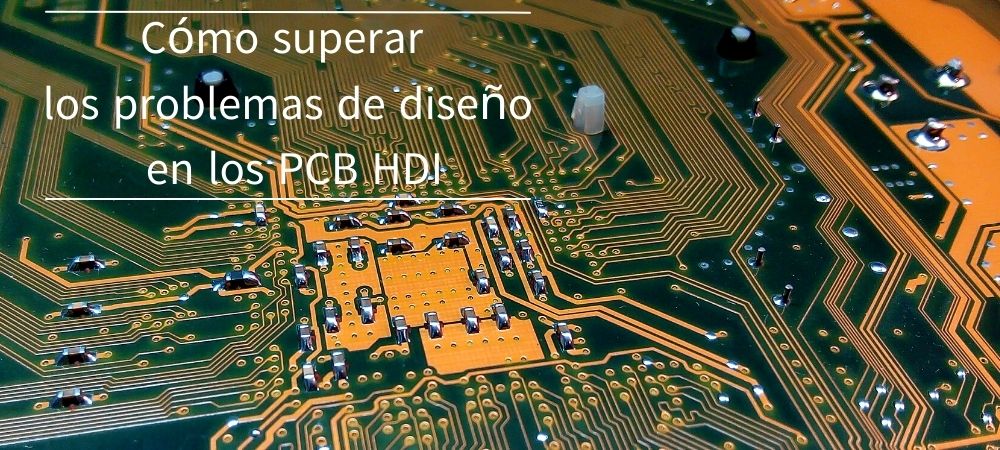
Las placas de circuito impreso con conexiones de alta densidad, también conocidas por el término HDI (High Density Interconnect), representan una de las tecnologías más avanzadas en este sector, capaz de satisfacer la creciente demanda de PCB cada vez más compactos y de mayor rendimiento. En comparación con los PCB estándar, los PCB HDI ofrecen un mayor número de conexiones eléctricas por superficie unitaria, que se obtienen cumpliendo los siguientes requisitos:
- ancho y distancia entre trazas menor de 100 µm
- ancho de vía inferior a 150 µm
- almohadillas de captura de tamaño inferior a 400 µm
- densidad de las almohadillas de captura superior a 20 almohadillas/cm2
y obtenga un presupuesto para su proyecto de PCBAs en 10 minutos!
La tecnología HDI permite a los diseñadores reducir drásticamente el tamaño del circuito y seguir garantizando la fiabilidad e integridad de la señal requeridas. Para los ingenieros, los desafíos a abordar son especialmente duros, sobre todo por lo que respecta a la fabricación. De hecho, al reducir el ancho de las trazas a menos de 65 µm, lo que corresponde a alrededor de 2,559 milésimas de pulgada, ya no es posible el uso del procedimiento de grabado tradicional, y deben adoptarse procesos especiales de producción, con el incremento de los costes que ello comporta.
Si se realiza correctamente, el enrutamiento de HDI no solo reduce significativamente el espacio ocupado en el PCB, sino que también resuelve muchos problemas relativos a interferencias electromagnéticas (EMI), reduciendo los costes generales del proyecto, las pruebas a realizar y el tiempo de comercialización.
Microvía
Un pilar fundamental de la tecnología HDI es la microvía, que es un orificio ciego con un diámetro inferior a 150 µm y un diámetro de almohadilla inferior a 350 µm, que normalmente se obtiene mediante un proceso de perforación láser. Mediante la aplicación de un haz láser con un diámetro típico de 20 micras (que corresponde a 1 milésima de pulgada) a un sustrato de cobre o fibra de vidrio es, de hecho, posible obtener microvías extremadamente pequeñas. En los PCB HDI, las microvías sustituyen los clásicos orificios pasantes, permitiendo la conexión entre múltiples capas en una superficie reducida, con el consiguiente incremento de la densidad de las interconexiones. Las microvías tienen una profundidad somera, por lo que son prácticamente inmunes a problemas debidos a los diferentes valores del coeficiente de expansión (CTE) entre el sustrato y el material conductor. La Figura 1 muestra la ampliación de una única microvía ciega, obtenida mediante perforación láser.
Figura 1: ejemplo de microvía (fuente: Micron Laser)
En las placas de circuito impreso HDI, las microvías sustituyen por completo las vías tradicionales, mejorando la densidad del enrutamiento en las capas internas y disminuyendo el número de capas requerido para la transmisión de las distintas señales. A fin de reducir el número de orificios pasantes y el número de capas internas, deben adoptarse medidas específicas a nivel de apilamiento. Los planos de tierra y alimentación, en los que existe un mayor número de vías, normalmente ocupan las primeras capas del apilamiento (por ejemplo, la segunda y tercera capa), mientras que las dos capas exteriores se reservan a la colocación de componentes. El plano de tierra es esencial para crear una ruta de retorno de corriente de baja impedancia, mientras que la colocación de las señales en las capas interiores sirve para reducir el fenómeno de diafonía. Una adecuada colocación de las microvías es esencial en el diseño del circuito impreso HDI, ya que asegura una mejor integridad de la señal y un mejor diseño de las capas más internas.
Contrariamente a los orificios pasantes o vías, que forman carga capacitiva capaz de provocar la degradación de la señal a altas frecuencias, las microvías tienen un tamaño inferior, ofreciendo una carga parasitaria reducida.
Diseño de la HDI
Las microvías, que pueden ser de tipo ciego o enterrado, se realizan de forma diferente a las tradicionales. Mientras que, de hecho, estas últimas se obtienen perforando el apilamiento ya completo con todas las capas superpuestas, las microvías se practican mediante perforación láser en cada capa individual antes de componer el apilamiento. Las microvías permiten la conexión de múltiples capas, por medio de orificios y almohadillas más pequeños que nunca, y por tanto son especialmente adecuadas para paquetes altamente integrados como las matrices de rejilla de bolas (ball grid array - BGA), alcanzando un paso de 0,8 mm o inferior.
Los cada vez más comunes paquetes de BGA tienen un mayor número de clavijas (1.500 y más) y, en consecuencia, son extremadamente densos. Si bien constituyen una solución relativamente económica para la creciente demanda de miniaturización de circuitos, las BGA complican en gran manera el enrutamiento, lo que puede provocar un aumento en el número de capas, dando lugar a problemas de integridad de la señal y generando mayores costes.
Las trazas que transportan señales de alta velocidad deben ser lo más cortas posible, incluida la ruta de retorno a tierra. La correcta colocación de las microvías permite englobar la ruta de la señal en una superficie más pequeña, reduciendo el riesgo de EMI. Las microvías permiten alcanzar una densidad de conexión muy elevada utilizando un menor número de capas, ya que tanto las trazas como las microvías tienen un tamaño muy inferior. Las ventajas principales ofrecidas por la tecnología HDI son las siguientes:
- mayor densidad de la traza, lo que da lugar a un menor tamaño y peso del PCB.
- mejor integridad de la señal. La longitud reducida de las trazas y la alta densidad de las conexiones permiten un menor consumo de energía, mejorando la integridad de la señal. La transmisión de la señal se produce más rápidamente, con reducciones significativas en pérdidas de señal y retrasos de propagación.
- Reducción de costes. A través de un esmerado diseño, la tecnología HDI permite una reducción en los costes gracias al menor uso de materiales requeridos para las capas
- enrutamiento simplificado gracias a las trazas de corta longitud
- reducción de la interferencia inductiva y capacitiva (EMI)
- posibilidad de utilizar componentes con paquetes ultrapequeños
- Reducción del tiempo de comercialización. El menor uso de materiales se traduce en una producción más rápida y un menor tiempo de comercialización. En un PCB HDI, los componentes son relativamente fáciles de colocar y el alto rendimiento eléctrico reduce el tiempo requerido para la realización de pruebas y la resolución de problemas.
La Figura 2 muestra un ejemplo de PCB fabricado con tecnología HDI: véanse el tamaño compacto y la alta densidad de los componentes y las conexiones presentes en el mismo.
Figura 2: ejemplo de PCB HDI (fuente: Cadence)
Respecto a las normas aplicables al diseño de placas de circuito impreso HDI, la referencia está representada por la norma IPC-2226 ("Estándar de Diseño Seccional para placas de interconexión de alta densidad"), que sustituye y anula la anterior norma IPC-2315 (“Guía de diseño para interconexiones de alta densidad y microvías"). Además de proporcionar orientación para la selección de microvías, la norma identifica seis tipos diferentes de apilamientos que pueden usarse para el diseño de los PCB HDI. Los distintos apilamientos se dividen en categorías, de la I a la VI, con una complejidad y unos costes incrementales. Cada una de estas categorías define el número y la posición de cada capa en el apilamiento HDI, y aporta recomendaciones sobre el material de sustrato a utilizar. Téngase asimismo en cuenta que las microvías, además del modo individual que se muestra en la Figura 1, también pueden superponerse (ocupando la misma posición) en varias capas adyacentes. En este caso hablamos de "microvía apilada". Puede verse un ejemplo de ello en la Figura 3, donde las microvías superpuestas ocupan las capas 1, 2 y 3 de una hipotética placa de circuito impreso multicapa constituida por 14 capas.
Figura 3: microvías superpuestas (fuente: Cadence)
Aplicaciones
Con el empleo de la tecnología HDI, los diseñadores de PCB pueden contar con una mayor flexibilidad, al tener la posibilidad de colocar más componentes en ambas capas externas del PCB. La innovadora solución de la microvía permite la colocación de un mayor número de componentes a distancias muy cortas, reduciendo el tiempo de transmisión de la señal, el consiguiente retraso en la transmisión y las pérdidas de energía.
La capacidad de utilizar componentes con paquetes de paso ultraestrecho aumenta aún más la densidad del componente, dando lugar a unos PCB con unas superficies y grosores mucho más pequeños que los de los PCB tradicionales. El tamaño reducido, la elevada frecuencia y la alta velocidad de la señal son factores que preparan el camino para aplicaciones tales como dispositivos de pantalla táctil, teléfonos móviles, sistemas de comunicación 5G, cámaras digitales, ordenadores portátiles, dispositivos portátiles y productos electromédicos. La tecnología HDI también se utiliza de forma generalizada en el sector de la electrónica de consumo, con aplicaciones de relevancia tales como consolas de juegos, reproductores multimedia, dispositivos de realidad virtual (RV) y de realidad aumentada.
12.02.2022