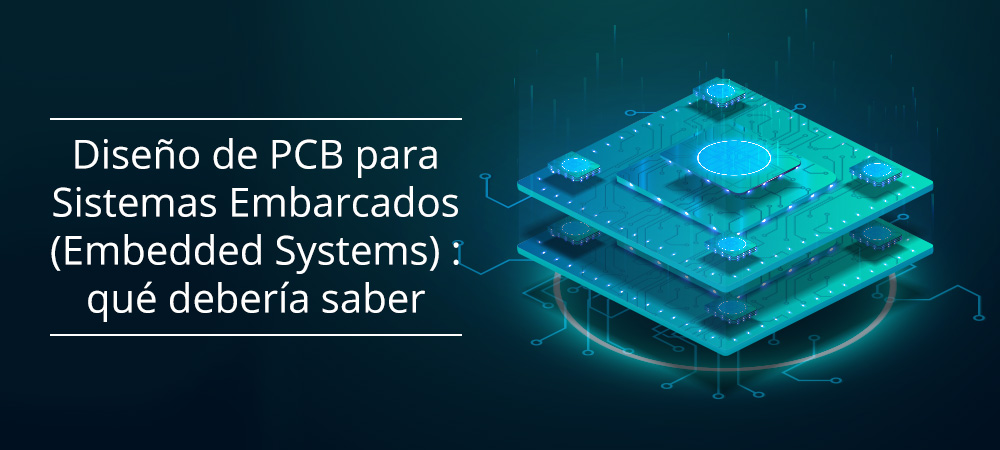
En los últimos años, la creciente demanda de dispositivos móviles, portátiles y electromédicos ha llevado a una reducción progresiva en el tamaño de los circuitos electrónicos integrados. Los requisitos relativos a nuevas funciones, incluida la conectividad inalámbrica y el uso de pantallas de alta resolución, han aumentado inevitablemente la densidad de los componentes, planteando unos desafíos sin precedentes a los diseñadores electrónicos. Alta integración, bajo consumo energético y una gestión térmica excelente son solo algunos de los requisitos que deben cumplir muchas aplicaciones integradas de última generación. La reducción del tamaño de la PCB no solo permite satisfacer los requisitos de miniaturización del mercado, sino que además permite materializar unos ahorros significativos en términos de costes de producción. Este artículo presentará las principales técnicas de fabricación y los trucos que pueden utilizar los diseñadores a la hora de tener éxito en la creación de un circuito impreso para aplicaciones integradas.
Tamaño de la PCB
El tamaño es una de las limitaciones más evidentes e importantes en el diseño de la PCB. El diseño y el tamaño de la PCB deben acordarse con las personas implicadas en el diseño mecánico, a fin de permitir una fácil instalación del circuito en el interior de la carcasa del producto final. En cualquier caso, la PCB no puede ser demasiado pequeña, ya que debe garantizar el correcto posicionamiento de los componentes y evitar el sobrecalentamiento de la placa. Debido a que la mayoría de los componentes individuales de un sistema integrado son pasivos, la utilización de la tecnología SMD es prácticamente obligatoria. Esto reduce la huella y la distancia entre componentes, traduciéndose en un diseño muy compacto de la PCB. Un segundo aspecto sobre el cual el diseñador puede trabajar al objeto de optimizar el tamaño de la PCB es el enrutamiento. Siempre que los requisitos de espacio lo permitan, una tendencia muy difundida consiste en la fabricación de PCB de doble cara. De hecho, esta solución permite un fácil montaje de los componentes SMD en ambas caras de la PCB, implica una complejidad de enrutamiento no especialmente elevada y simplifica mucho la comprobación, reparación y reelaboración del circuito. Un mayor número de capas incrementa el espacio disponible para la colocación de las trazas y, en consecuencia, puede conseguirse un enrutamiento más eficiente. Esto explica por qué la mayoría de dispositivos portátiles altamente integrados, como los relojes inteligentes, incorporan una PCB con hasta seis capas. No obstante, existe un inconveniente que hay que tener en cuenta: cuanto mayor sea el número de capas, mayor será la complejidad del circuito y el tiempo requerido para la depuración o la aplicación de modificaciones en el diseño original. Un buen compromiso para muchos tipos de sistemas embarcados lo representan las PCB de cuatro capas, cuya estructura típica (también conocida como apilamiento o «stackup») se muestra en la Figura 1. Las dos caras externas no se usan solamente para el posicionamiento y la conexión de los componentes en las trazas microstrip, sino también para crear planos de tierra (GND). Las capas internas se utilizan en cambio para el enrutamiento de señales a través de trazas stripline y para crear planos de potencia (POWER).
Normalmente, las trazas que transportan señales de potencia o que se utilizan como rutas de retorno de tierra son las que implican las corrientes más elevadas y, por lo tanto, tendrán un mayor grosor con respecto a las demás trazas. Su ancho normalmente no es inferior a 40 mils y puede calcularse con una de las diversas calculadoras de ancho de trazas, disponibles también en línea. Estas trazas pueden colocarse en las dos capas exteriores, mientras que las trazas que transportan bajas señales de potencia son más adecuadas para ocupar las capas internas.
Figura 1: Un apilamiento de PCB de 4 capas.
Debe prestarse especial atención a la altura de los componentes (en particular, los capacitadores electrolíticos y conectores), un aspecto a menudo ignorado, ya que la mayoría de las herramientas de software para el diseño de PCB funcionan en dos dimensiones, con una vista del diseño desde arriba.
Colocación de los componentes
La colocación de los componentes debe reflejar las reglas generales aplicables al diseño de PCB, tales como la alineación (que permitirá simplificar los procesos de soldadura y montaje) y la separación entre dispositivos analógicos y digitales. Asimismo, se evitará colocar los componentes más pesados cerca de los bordes de la PCB, ya que la placa tendería a doblarse. A fin de reducir la tensión mecánica en los puntos de soldadura, estos componentes deben colocarse en el lado de la PCB que normalmente está cara arriba. Si es posible, los dispositivos de potencia no deben concentrarse en la misma zona, sino distribuirse de la forma más uniforme posible en el plano de la placa, favoreciendo así la disipación térmica. La elección del paquete correcto para cada componente es también muy importante. Los componentes pasivos SMD están disponibles en gran cantidad de paquetes con huellas muy diferentes, tal y como se muestra en la Figura 2.
Mientras que durante el diseño del prototipo es preferible utilizar paquetes con mayor huella (simplificando así el montaje y la comprobación del circuito), para la versión de producción es aconsejable utilizar paquetes que ocupen menos espacio. Los diseñadores deben confirmar también cuál es el paquete mínimo soportado por el proceso de montaje, ya que no todas las máquinas de recogida y colocación manejan todos los tipos de formatos.
Figura 2: Dispositivos SMD con diferentes paquetes.
Gestión térmica
Cuando fluye una corriente de alta intensidad a través de la traza de una PCB, se produce una cantidad de calor nada insignificante. Para mejorar la dispersión térmica manteniendo el tamaño de la PCB tan reducido como sea posible, el diseñador puede utilizar dos técnicas, que ofrecen la posibilidad de combinarse entre sí:
- incrementar el grosor de la traza;
- Crear en la PCB zonas o planos de cobre completos con el fin de disipar el calor.
Como sugiere la norma IPC2221A, los planos de cobre deben tener un grosor de 10 onzas (35 µm), pero este valor puede incrementarse eventualmente. Por ejemplo, al duplicar el grosor (20 onzas o 70 µm), el ancho de la traza podría reducirse en un 50%, manteniendo el mismo valor de corriente. Además, un grosor de 20 onzas mejora enormemente la disipación térmica. Si el sistema integrado tiene que gestionar altas potencias, como en el caso de los convertidores, inversores o accionadores de motores, puede utilizarse la tecnología de cobre pesado, que implica un grosor del cobre comprendido entre 4 y 10 onzas.
Debe evitarse la formación de puntos con una alta concentración de calor, denominados también puntos calientes, manteniendo la temperatura máxima alcanzada por la PCB por debajo de los 170 °C. Esta condición puede detectarse realizando un análisis termográfico con un generador de imágenes térmicas, o a través de un modelo y un software de simulación térmica adecuados. Otra técnica utilizada habitualmente para mejorar la disipación térmica consiste en insertar orificios apropiados en las pistas, denominados vías térmicas. En el caso de las PCB de doble cara, las vías térmicas conectan las capas superior e inferior entre sí, incrementando tanto la superficie como el volumen capaz de disipar calor. En el caso de una PCB con múltiples capas, las vías térmicas conectan varias capas entre sí, incluso en el interior de la PCB. Al objeto de que sean más eficaces, las vías térmicas deben colocarse lo más cerca posible de los componentes que generan la mayor cantidad de calor, si es posible debajo de ellos.
y obtenga un presupuesto para su proyecto de PCBAs en 10 minutos!
Componentes integrados
Los sistemas embarcados de última generación se caracterizan por una alta densidad del dispositivo y una huella extremadamente pequeña. Para simplificar tanto el diseño como las fases de montaje de la PCB, cada vez son más los diseñadores que adoptan la tecnología de componentes embarcados.
Mediante esta técnica, los inductores, resistencias y condensadores se incrustan directamente en la PCB. Esto reduce la longitud de las trazas, el número de puntos de soldadura y los costes, mejorando el rendimiento eléctrico del circuito y su fiabilidad. Las resistencias, los condensadores y los inductores se colocan en las capas internas, por impresión o grabado, durante el proceso de fabricación de la PCB. Posteriormente, se incorporan en la PCB durante el proceso de laminado del circuito impreso multicapa. Los inductores incluyen también modelos equipados con un núcleo magnético. Los núcleos ferromagnéticos se integran en un sustrato de la PCB, mientras que el bobinado inductivo se realiza por fotolitografía y otros procesos estándar de fabricación de PCB. En lugar de construirse uno a uno, los componentes se disponen en un panel de PCB y se fabrican mediante un proceso automatizado. En la mayoría de los casos, el núcleo integrado tiene forma de aro (toroidal). Los núcleos toroidales son relativamente fáciles de fabricar y generalmente económicos en comparación con otras formas de núcleos. Los materiales empleados habitualmente son ferritas cerámicas prensadas y metales amorfos envueltos en cinta adhesiva. La Figura 3 muestra el bobinado de un inductor con diez vueltas, totalmente integrado en la PCB.
Figura 3: Ejemplo de componentes integrados en una PCB.