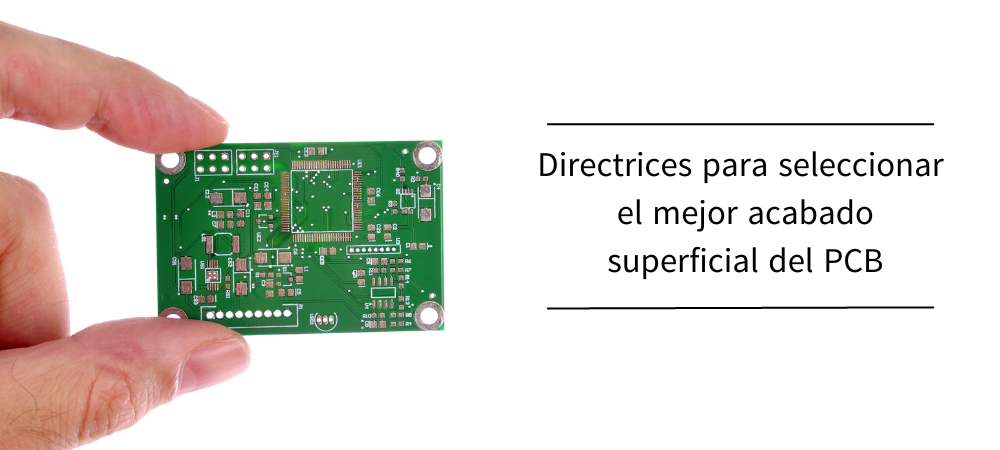
Las Placas de Circuito Impreso (PCB) proporcionan las interconexiones y el soporte necesarios para que los componentes electrónicos funcionen como una entidad cohesiva en los modernos dispositivos electrónicos. A medida que el tamaño, la complejidad y los requisitos de rendimiento de los dispositivos electrónicos siguen reduciéndose y aumentando, la elección del tratamiento superficial del PCB resulta cada vez más crucial. La calidad de la superficie no tan solo afecta a la soldabilidad de los componentes, sino también a la fiabilidad, durabilidad y rendimiento general del dispositivo.
Este artículo presenta un exhaustivo análisis de los factores que influyen en la selección del acabado superficial óptimo del PCB. Debate las opciones de tratamiento superficial disponibles, sus ventajas e inconvenientes, y proporciona a ingenieros y diseñadores directrices que les ayudarán a tomar decisiones con conocimiento de causa.
y obtenga un presupuesto para su proyecto de PCBAs en 10 minutos!
La finalidad del acabado superficial del PCB
El revestimiento de acabado superficial aplicado a las placas de circuito impreso desempeña diversas importantes funciones que pueden resumirse de la siguiente forma:
- Garantizar la soldabilidad. La soldabilidad es una de las principales funciones del acabado superficial del PCB. Durante el proceso de montaje, proporciona una superficie soldable para la fijación de los componentes electrónicos. En ausencia de un acabado superficial adecuado, es posible que las juntas soldadas no se formen con precisión, dando lugar a defectos como puentes de soldadura o conexiones deficientes.
- Prevenir la oxidación. El cobre, el material conductor más común en los PCB, es susceptible a la oxidación si se expone al oxígeno. Un tratamiento superficial adecuado evita que las trazas de cobre se oxiden formando una capa protectora sobre ellas. La oxidación puede dar lugar a conexiones eléctricas inadecuadas y degradación de la señal.
- Mejorar la fiabilidad. La textura superficial de los PCB desempeña un papel significativo en su fiabilidad. Deteriora el rendimiento de las juntas de soldadura, que son esenciales para soportar la tensión mecánica, las fluctuaciones de temperatura y las condiciones ambientales. Se requiere un acabado superficial duradero para garantizar la fiabilidad a largo plazo del PCB.
- Simplificar la unión de los cables. En ciertas circunstancias, la conexión de los dispositivos semiconductores al PCB se efectúa mediante la unión de cables. La calidad y fiabilidad de estas uniones de cables son susceptibles de verse afectadas por el acabado superficial que se ha seleccionado.
En la Figura 1 se muestra un aparato preparado para la aplicación del acabado superficial en el PCB.
Figura 1: Equipo para la aplicación de acabado superficial en PCB.
Tipos de acabados superficiales de PCB
El acabado superficial del PCB es una interfaz crucial entre los componentes electrónicos y el sustrato del PCB. Garantiza una soldadura fiable, evita la oxidación de las trazas de cobre e influye en el rendimiento eléctrico. La selección del acabado superficial influye en el rendimiento del conjunto, en la calidad de la junta de soldadura y en la fiabilidad a largo plazo.
Los acabados superficiales utilizados más habitualmente en los PCB se clasifican en las siguientes clases:
- Pasivado Orgánico (OSP: Organic Solderability Preservatives) Fina capa orgánica que protege el cobre y permite la soldadura directa.
- Níquel químico por inmersión en oro (ENIG: Electroless Nickel Immersion Gold): Acabado de doble capa, con una capa inferior de níquel y una capa superior de oro (Figura 2), que proporciona una excelente soldabilidad y resistencia a la corrosión.
- Estañado por Inmersión (ImSn): Acabado económico sin plomo que ofrece una buena soldabilidad, pero requiere una manipulación cuidadosa debido a la formación de briznas de estaño.
- Níquel-Oro Galvanizado (Ni/Au): Robusto acabado con excelente resistencia a la corrosión y capacidad de unión de cables.
- Nivelación de Soldadura de Aire Caliente (HASL): Acabado tradicional que implica una capa de soldadura aplicada sobre el cobre expuesto (Figura 3), adecuado para placas sencillas.
- Estañado galvánico: Alternativa sin plomo al HASL, que ofrece un mejor aplanado y planitud de superficie.
- Protector Orgánico de Superficies (OSP): Acabado respetuoso con el medio ambiente que proporciona soldabilidad y protege contra la oxidación.
- Plata de Inmersión (ImAg): Acabado con buena conductividad y soldabilidad (Figura 4), sensible a las condiciones de almacenamiento y a la formación de sulfuro de plata.
- Revestimiento superficial metálico tricapa de níquel, paladio y oro (ENEPIG): Complejo acabado de elevada fiabilidad, adecuado para aplicaciones avanzadas.
Figura 2: PCB tratado con acabado ENIG.
Figura 3: PCB tratado con acabado HASL.
Figura 4: PCB tratado con acabado ImAg.
Directrices clave para la selección del acabado superficial
La elección del acabado superficial adecuado para una placa de circuito impreso (PCB) es un paso muy importante que depende de una serie de distintos aspectos, como la aplicación prevista, el método de soldadura (por ejemplo, sin plomo o con plomo), las condiciones ambientales, los requisitos de integridad de la señal, las consideraciones en cuanto a costes y el cumplimiento normativo.
En la siguiente lista se enumeran los factores principales que influyen en la selección del acabado superficial:
- La aplicación y el uso previsto de la placa de circuito impreso. Las características fundamentales del dispositivo electrónico y la finalidad prevista son de suma importancia. Debe considerarse si el PCB que se está considerando se integrará en un producto de consumo, un sistema de automoción, una aplicación aeroespacial de alta fiabilidad o un producto sanitario. Diversas aplicaciones presentan especificaciones distintas en términos de durabilidad, rendimiento térmico y resistencia ambiental.
- Tipo de soldadura: sin plomo o con plomo La adopción de la soldadura sin plomo se ha visto impulsada por normas reglamentarias como la directiva sobre sobre Restricción de Sustancias Peligrosas (RoHS). Es indispensable verificar la compatibilidad del acabado superficial seleccionado con el proceso de soldadura empleado, ya sea con o sin plomo. Los diseñadores deben asegurarse de que el acabado superficial cumple las normas reglamentarias (como RoHS y REACH), especialmente en lo que respecta al uso de sustancias restringidas.
- Duración de la vida útil y requisitos de almacenamiento. El diseñador es responsable de tener en cuenta la vida útil del PCB, así como sus circunstancias de almacenamiento. Ciertos acabados superficiales son más susceptibles a los efectos de las condiciones de almacenamiento y pueden deteriorarse con el tiempo, lo que puede afectar a su capacidad para ser soldados.
- Preocupación por el medio ambiente. La selección del acabado superficial puede verse influida por diversas variables ambientales, que incluyen la exposición a la humedad, los productos químicos y las temperaturas extremas. Es crucial seleccionar un acabado que posea la capacidad de soportar las diversas circunstancias meteorológicas a las que probablemente vaya a estar expuesto su equipo.
- La fiabilidad de las juntas de soldadura. El diseñador debe evaluar el nivel necesario de fiabilidad de las juntas de soldadura para la aplicación específica. Ciertos acabados superficiales presentan una mayor resiliencia a los ciclos térmicos y al estrés mecánico, lo que los hace muy adecuados para aplicaciones expuestas a condiciones ambientales extremas.
- Integridad de la señal y control de la impedancia. Es posible que el acabado superficial tenga un efecto en la integridad de la señal, así como en la gestión de la impedancia en aplicaciones de alta frecuencia o alta velocidad. Por lo tanto, es necesario seleccionar un revestimiento que pueda cumplir las especificaciones establecidas por el rendimiento eléctrico del circuito concreto.
- Compatibilidad con el proceso de montaje. Existen muchos procedimientos de montaje distintos, que incluyen la soldadura por reflujo, la soldadura por ola y la unión de cables. Los diferentes acabados superficiales interactúan de forma distinta con cada uno de estos procesos. Asegúrese de que el acabado que elija pueda funcionar con los procedimientos que utilice para fabricar el producto.
- Coste y presupuesto. Los gastos del acabado superficial incluyen los del material, la aplicación y el montaje asociado. Es preceptivo dar con el equilibrio adecuado entre coste, rendimiento y fiabilidad.
Análisis comparativo de acabados superficiales
Cada uno de los diferentes acabados superficiales mencionados presenta su propio conjunto de ventajas e inconvenientes, así como diferentes escenarios de uso que son los más adecuados para ellos. Dado que los diseños de PCB suelen tener requisitos muy concretos, los ingenieros y diseñadores responsables de crearlos deben seleccionar muy cuidadosamente el tratamiento superficial adecuado.
Es necesario tener una sólida comprensión de los muchos acabados superficiales que están disponibles, así como de las ventajas e inconvenientes asociados a cada uno de ellos. A continuación, presentamos una breve comparación y estudio los distintos tratamientos superficiales que se utilizan con frecuencia en electrónica.
Tipo de acabado superficial |
Ventajas |
Inconvenientes |
Pasivado Orgánico (OSP Organic Solderability Preservatives) |
Proceso sencillo, económico, sin plomo y adecuado para componentes de paso fino (FPT) |
La vida útil limitada y la sensibilidad a la manipulación pueden descalificar los productos para entornos difíciles |
Níquel químico por inmersión en oro (ENIG: Electroless Nickel Immersion Gold): |
Soldabilidad, resistencia a la corrosión y planitud superiores; adecuado para componentes de paso fino |
En comparación con algunas alternativas, este procedimiento es más complicado y más caro |
Estañado por Inmersión (ImSn) |
Sin plomo, con una superficie uniforme y una excelente soldabilidad |
Sensible a la manipulación, con formación de rebabas de estaño, e inadecuado para múltiples reflujos |
Níquel-Oro Galvanizado (Ni/Au) |
Robusto, con una excelente resistencia a la corrosión, adecuado para la unión de hilos |
Más costoso y no óptimo para la soldadura sin plomo |
Nivelación de Soldadura de Aire Caliente (HASL) |
Proceso sencillo y rentable, adecuado para componentes con orificios pasantes |
No exento de plomo, puede dar lugar a superficies irregulares, no apto para componentes FPT |
Estañado galvánico |
Sin plomo, rentable, adecuado para placas sencillas |
Más costoso y no óptimo para soldadura sin plomo |
Protector Orgánico de Superficies (OSP) |
Sin plomo, ecológico y adecuado para componentes de paso fino |
Vida útil limitada, sensibilidad a la manipulación, inadecuado para entornos difíciles |
Plata de Inmersión (ImAg) |
Excelente conductividad, exenta de plomo y adecuada para aplicaciones de alta frecuencia |
Sensibilidad a las condiciones de almacenamiento y formación de sulfuro de plata |
Revestimiento superficial metálico tricapa de níquel, paladio y oro (ENEPIG) |
Fiabilidad superior, idóneo para aplicaciones avanzadas y sin plomo |
Procedimiento complejo y costoso |
Conclusión
La elección del tratamiento superficial óptimo del PCB es un paso crucial en su proceso de diseño. Teniendo en consideración la aplicación, la compatibilidad del proceso de soldadura, la fiabilidad, la resiliencia medioambiental, la integridad de la señal, el coste y la conformidad normativa, puede garantizar el rendimiento y la fiabilidad de sus dispositivos electrónicos. Tenga en cuenta que cada aplicación es única, por lo que se requiere una exhaustiva evaluación de sus necesidades específicas para realizar la mejor elección.
En la industria electrónica actual, en rápida evolución, también es esencial mantenerse al día de las tecnologías y materiales de acabado superficiales emergentes. Evalúe con regularidad sus opciones de acabado superficial para asegurarse de que estén alineadas con las más recientes innovaciones y estándares de la industria. Una decisión bien informada con respecto al tratamiento de superficies del PCB en última instancia contribuirá al éxito y la durabilidad de sus productos electrónicos.
07.11.2023