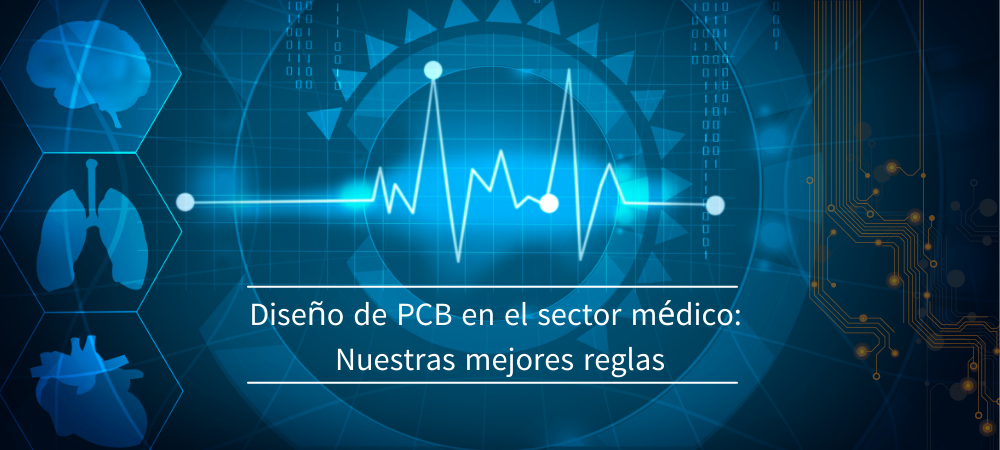
Las placas de circuito impreso han adquirido una importancia crítica en las aplicaciones electromédicas. De hecho, los avances significativos materializados en el campo de las tecnologías electrónicas han permitido el despliegue de dispositivos médicos con funciones cada vez más avanzadas, como marcapasos, desfibriladores, monitores cardíacos para el tratamiento de enfermedades cardiovasculares, equipos de diagnóstico por imagen, resonancia magnética, TAC y ultrasonidos, así como una amplia gama de soluciones portátiles y llevables, como termómetros, monitores de glucosa en sangre y equipos de electroestimulación muscular.
y obtenga un presupuesto para su proyecto de PCBAs en 10 minutos!
Para estar a la altura de estas innovaciones, los diseñadores deben garantizar que las placas de circuito impreso de uso médico cumplan los estándares de seguridad aplicables, sean seguros tanto para el paciente como para los profesionales sanitarios, y tengan una elevada fiabilidad y durabilidad.
Tecnologías para PCB médicos
Como ya ha sucedido en otros campos de la electrónica, también en los dispositivos electromédicos la tendencia actual apunta al desarrollo de productos cada vez de menor tamaño con una densidad de componentes cada vez mayor. Evidentemente, esto comporta varias consecuencias en el diseño de la placa de circuito impreso, como la disposición de los componentes y las distancias relativas, la longitud y la distancia entre las trazas, la disipación térmica del PCB. Como consecuencia, los márgenes de error en el diseño de una placa se han reducido drásticamente, requiriendo con frecuencia mayor flexibilidad tanto en la fase de diseño como en la de producción.
Una tecnología de PCB capaz de responder a esta necesidad es aquella que permite la creación de placas de conexión de alta densidad (HDI). Mediante la reducción del tamaño del PCB y el aumento del número y la complejidad de las funcionalidades implementadas, el área disponible para el enrutamiento de las trazas, que están cada vez más próximas unas de otras, se reduce.
Otra tecnología de uso generalizado en los PCB médicos se basa en las placas de circuito impreso flexibles y rígidas. Esto se debe a que los dispositivos médicos con frecuencia no se adaptan a la forma y el tamaño típicos de los PCB tradicionales y deben ser capaces de ajustarse al área más pequeña posible, asegurando los mismos niveles de fiabilidad y durabilidad. Los PCB flexibles están hechos de materiales más ligeros, con lo que se reduce el peso total del dispositivo. La capacidad de estos PCB para doblarse permite la optimización del espacio disponible y los costes de producción, concediendo más libertad al diseñador para elegir la forma de la carcasa. Aunque el diseño de un PCB flexible es más complejo que el de un PCB rígido, resulta mucho más fácil desarrollar un dispositivo ergonómico y robusto. De hecho, el PCB flexible ofrece ventajas mecánicas significativas respecto al PCB rígido en muchas aplicaciones médicas, especialmente en las portátiles. Además, los PCB flexibles pueden interconectarse con placas rígidas mediante finos cables planos, sin que requieran conectores altos y voluminosos.
La actual tendencia de muchos dispositivos portátiles, como los que monitorizan las constantes vitales con fines de entrenamiento, fitness o clínicos, está impulsando el desarrollo de dispositivos con factores de forma del PCB no estándar, como redondos o elípticos. En otros momentos, el PCB puede adoptar formas completamente irregulares. La integración de PCB flexibles y rígidos-flexibles (muy compactos y con alta densidad de componentes) permite a los diseñadores gestionar con facilidad las formas más dispares de placas de circuito impreso. La Figura 1 muestra un ejemplo de PCB rígido-flexible.
Figura 1: PCB rígido-flexible
En los siguientes párrafos se presentarán algunas reglas sencillas que pueden ayudar al diseñador en el desarrollo de PCB médicos, simplificando su diseño, las pruebas y el mantenimiento.
1 – Componentes SMD y PTH
Aunque la tecnología de montaje en superficie, también conocida como SMT, por el acrónimo «Surface Mount Technology» se ha convertido en el estándar de facto para la mayoría de aplicaciones electrónicas, todavía existen algunos dispositivos en los que tiene sentido utilizar la tecnología de montaje de orificios pasantes chapados (PTH, por sus siglas en inglés), especialmente en placas de alimentación o cuando se utilizan múltiples conectores.
En general, en aplicaciones médicas es preferible el empleo de tecnología SMT, ya que permite el uso de componentes más pequeños, reduciendo así el tamaño del PCB y aumentando la densidad de los componentes en la placa. Además, para el montaje de los componentes SMD no es necesario perforar ningún orificio, lo que reduce tanto los costes como el tiempo necesario para la fabricación y el montaje de la placa de circuito impreso. Uno de los paquetes SMD más pequeños disponibles actualmente en el mercado es el 008004, que se muestra en la figura 2, y que tiene un tamaño de tan solo 0,25 mm x 0,125 mm.
Figura 2: algunos de los paquetes SMD más pequeños
2 – Materiales
Dada la importancia de los productos sanitarios, de cuyo funcionamiento seguro y fiable suele depender la vida de muchos pacientes, la elección de los materiales empleados para la fabricación del PCB es especialmente crítica. Los principales factores que impulsan la elección de los materiales y sustratos más adecuados para una aplicación médica concreta son los siguientes:
- cumplimiento de la normativa RoHS
- disponibilidad de señales de radiofrecuencia (RF) y/o señales de alta frecuencia/velocidad de transmisión
- temperatura de servicio máxima
- opciones de conectividad (WiFi, Bluetooth, etc.)
- tamaño y forma de la carcasa.
Para soportar la alta densidad de componentes requerida, es frecuente el uso de la tecnología HDI, lo que se traduce en un número elevado de interconexiones y orificios de paso, tanto ciegos como enterrados. La tecnología HDI permite reducir drásticamente el tamaño del PCB, gracias a la posibilidad de practicar orificios de paso con láser, además de via in-pad y pistas con un ancho y un espaciado de tan solo 5 mil.
La tecnología via-in-pad, principalmente utilizada con componentes muy integrados (como los BGA) o con un elevado número de clavijas y un paso muy estrecho, permite la creación de los orificios directamente en las pastillas, conectándolas de este modo con las capas internas. La Figura 3 muestra un ejemplo de aplicación de la tecnología via-in-pad, con orificios de paso practicados directamente en algunas pastillas del componente.
Figura 3: ejemplo de tecnología via-in-pad
Sin embargo, conviene subrayar que la producción de PCB HDI para uso médico exige inversiones en equipos costosos, como la imagen láser directa (LDI) y los procesos aditivos y semiaditivos (mSAP), que implican un mayor coste de fabricación del PCB. Dichos equipos son necesarios para cumplir los estrictos requisitos relativos al ancho y el espaciado de las trazas.
Por lo que respecta a los materiales de laminado, el FR-4 (retardante de llama de nivel 4) también es una opción habitual para los PCB médicos, en virtud de su bajo coste y su fabricación relativamente sencilla. En el caso de equipos más sofisticados, o dispositivos pertenecientes a clases de mayor riesgo, el PCB puede requerir laminados especiales, como poliamida, teflón, PTFE o materiales de tipo cerámico. Estos materiales son especialmente adecuados para todas las aplicaciones electrónicas de alta frecuencia. La constante dieléctrica del material FR-4 (aproximadamente igual a aprox. 4,5) resulta ser demasiado elevada en estos casos, lo que da lugar a pérdidas de señal significativas durante la transmisión a través de la placa de circuito impreso. En cambio, materiales como el teflón ofrecen valores de constante dieléctrica de 3,5 o inferiores. Además de una reducción de la constante dieléctrica, estos materiales también ofrecen unas características térmicas excepcionales, alcanzando valores de Tg de hasta 280°C.
3 – Longevidad
En la fase de diseño de un PCB médico, es esencial que los diseñadores, en colaboración con proveedores y fabricantes de PCB, puedan predecir la obsolescencia de los componentes que intervienen en el circuito. Lo que debemos evitar es el fin prematuro de la vida útil del proyecto causado por la imposibilidad de encontrar ciertos componentes. Si esto sucede, y la modificación requerida a nivel de componente o esquemática es lo suficientemente significativa, el producto puede tener que repetir todo el proceso de homologación de nuevo para obtener las conformidades requeridas (la aprobación por parte de los organismos competentes puede tardar varios meses).
4 – Mantenimiento
Cada fase del diseño del PCB debe apuntar a facilitar el montaje y el mantenimiento. Obviamente, esto afecta a varios aspectos, como la colocación de los componentes, la disposición del PCB y el enrutado de las trazas.
Debe prestarse especial atención a los conectores, de modo que los instaladores o el personal de mantenimiento puedan acceder a ellos fácilmente sin que representen un obstáculo. Todas las pastillas deben hallarse en una posición y tener un tamaño tal que permita simplificar la fase de soldadura. Además, todos los componentes integrados con un elevado número de clavijas deberán estar correctamente orientados. Por otra parte, es necesario mantener en el PCB un perfil de altura lo más uniforme posible, separando los componentes de mayor altura de los demás.
Finalmente, se recomienda crear un modelo en 3D de todo el circuito, operación que actualmente pueden realizar casi automáticamente muchas herramientas de desarrollo de PCB. Este modelo permite al diseñador evaluar el tamaño real y global de la placa, apuntando importantes sugerencias para la fase de montaje e instalación en el interior de la carcasa.
5 – Pruebas y depuración
Toda la placa debe diseñarse de modo que se simplifiquen tanto las pruebas como la depuración del circuito. Los diseñadores deberán proporcionar suficientes puntos de prueba para facilitar la fase de diagnóstico, tanto en la fábrica como en el campo. Los puntos de prueba deben colocarse principalmente en las trazas que transportan señales, en las señales de reloj y de control y en las líneas de alimentación. La experiencia demuestra que siempre es mejor disponer de unos cuantos puntos de prueba de más a que falte alguno en los puntos más críticos del circuito. Además, si es posible, siempre es mejor colocar los puntos de prueba en las caras exteriores de la placa. Cuando la placa de circuito impreso esté montada e instalada en el contenedor, la fase de prueba y verificación será mucho más fácil.
6 – Simulación
Las técnicas de simulación, como Digital Twin, reportan considerables beneficios al diseño de PCB de uso médico, reduciendo tanto los costes de desarrollo como el tiempo de comercialización. La principal ventaja de la simulación es que ayuda a identificar posibles errores, incluso antes de la entrega del primer prototipo de placa. La tecnología Digital Twin crea esencialmente un modelo virtual del circuito, tomando datos del mundo real como entrada y produciendo una simulación o predicción sobre cómo se comportará el circuito como consecuencia de la aplicación de esos estímulos de entrada. Esto permite el análisis de los datos y la monitorización del sistema, haciendo posible que los ingenieros eviten posibles problemas antes de que se produzcan, evalúen el tiempo de inactividad y optimicen el rendimiento del producto. La misma importancia reviste la simulación térmica del circuito, que permite la detección precoz de posibles puntos conflictivos cuando el circuito opera bajo diferentes condiciones de carga y ambientales. Siempre es mejor dedicar unas horas a introducir algunos cambios en el esquema y reiniciar la simulación térmica que llevar a cabo un costoso análisis térmico con cámaras de infrarrojos en el producto final, constatando la necesidad de introducir cambios en el circuito a fin de satisfacer los requisitos sobre fiabilidad y seguridad impuestos por las normas aplicables.