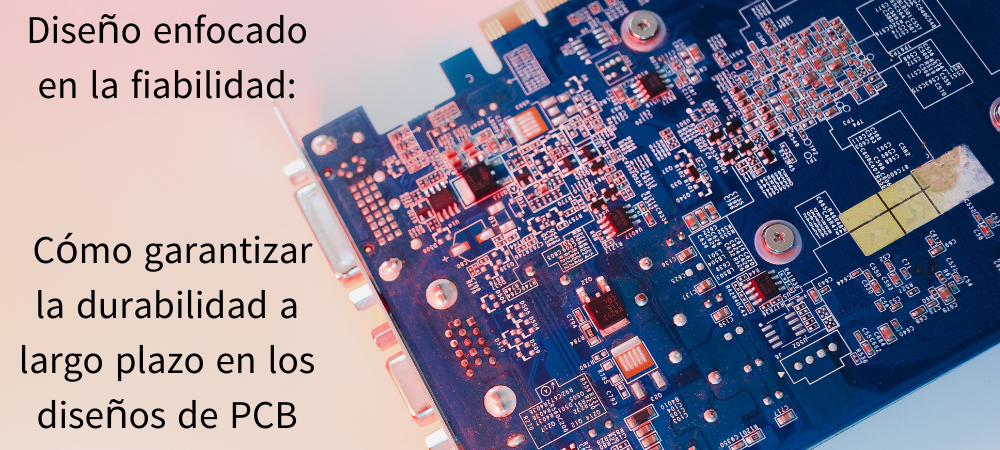
A la par con la evolución continua de los sistemas electrónicos, los PCB se aplican en entornos cada vez más exigentes, desde dispositivos de consumo hasta maquinaria industrial, sistemas de automoción y aplicaciones aeroespaciales. Garantizar la durabilidad a largo plazo de los PCB se ha convertido en una actuación crítica, ya que los fallos pueden provocar costosas reparaciones, retiradas del mercado o incluso riesgos para la seguridad.
La fiabilidad en el diseño de PCB se refiere a la capacidad de la placa para realizar la función prevista sistemáticamente a lo largo de su vida útil esperada, incluso en condiciones ambientales y operativas variables. La fiabilidad es un aspecto integral del proceso de diseño de PCB, que exige a los ingenieros anticiparse a los posibles modos de fallo y mitigar los riesgos de forma proactiva.
y obtenga un presupuesto para su proyecto de PCBAs en 10 minutos!
En la durabilidad a largo plazo influyen factores como la selección de materiales, la gestión térmica, la estabilidad mecánica y el cumplimiento de los principios del diseño para la fabricación (DfM). Si estos parámetros ya se tienen en cuenta inicialmente en la fase de diseño, los ingenieros pueden crear PCB robustos capaces de ofrecer un rendimiento constante en el tiempo.
Los fallos en los PCB suelen deberse a negligencias en el diseño, como la elección de materiales inadecuados, un enrutamiento ineficiente de las trazas o la insuficiente consideración de factores ambientales como la temperatura, la humedad y las vibraciones. Con el tiempo, estos problemas pueden provocar delaminación, fatiga de las juntas de soldadura o incluso fallos catastróficos.
Veamos en detalle cómo contribuyen estos factores a garantizar la fiabilidad y prolongar la vida útil de los modernos PCB.
Selección de materiales
La elección de los materiales desempeña un papel fundamental en la determinación de la longevidad y resiliencia de un PCB. Las distintas aplicaciones requieren sustratos diferentes sobre la base de sus propiedades mecánicas, térmicas y eléctricas.
El sustrato, normalmente fabricado con FR-4, es una opción comúnmente elegida debido a su equilibrio entre coste y rendimiento. Sin embargo, en aplicaciones de alta temperatura o alta frecuencia, pueden ser necesarios materiales alternativos como laminados de poliimida o rellenos de cerámica. Estos materiales ofrecen una estabilidad térmica superior y una menor pérdida de señal, lo que los hace ideales para aplicaciones aeroespaciales, automotrices o médicas en las que el fallo no es una opción. Además, en entornos difíciles, como las aplicaciones de los sectores aeroespacial y automotriz, son esenciales los materiales con temperaturas de transición vítrea (Tg) más elevadas y mejor resistencia a la humedad y a los productos químicos.
El grosor del cobre y la calidad del chapado también juegan un papel crucial (figura 1). Unas trazas de cobre más gruesas mejoran la capacidad de transporte de corriente y reducen el calentamiento resistivo, mientras que un chapado de alta calidad previene la oxidación y garantiza la solidez de las uniones soldadas. Los ingenieros deben calcular minuciosamente la capacidad de transporte de corriente de las trazas con herramientas como la norma IPC-2221, asegurándose de que el diseño se ajuste a estas directrices.
Figura 1: Los ingenieros deben calcular el ancho de las trazas en función de los requisitos de corriente
En entornos con temperaturas fluctuantes, los materiales con un bajo coeficiente de expansión térmica (CET) son cruciales. Un CET desajustado entre el PCB y sus componentes puede generar tensiones, causando fallos en las juntas de soldadura y el alabeo de la placa. Además, el sistema de resina utilizado en el laminado influye significativamente en la absorción de humedad y la resistencia química. La poliimida, por ejemplo, ofrece una estabilidad térmica y una resistencia química superiores en comparación con las resinas epoxi estándar, lo que la convierte en el material idóneo para entornos difíciles. Además, la calidad y el espesor de la lámina de cobre son fundamentales. El cobre de alta pureza garantiza una conductividad óptima, mientras que un espesor adecuado evita la generación excesiva de calor y las caídas de tensión.
La selección de la máscara de soldadura y el acabado superficial adecuados -como ENIG (oro por inmersión en níquel electrolítico) o HASL (nivelación de soldadura por aire caliente)- puede mejorar la resistencia a la corrosión y la soldabilidad, prolongando aún más la vida útil del PCB.
Diseño del PCB
Un diseño de PCB bien ejecutado influye significativamente en su fiabilidad a largo plazo. La colocación adecuada de los componentes, el enrutamiento de las trazas y el cumplimiento de los principios de diseño para la fabricación (DFM) reducen la probabilidad de defectos y fallos.
La ubicación de los componentes debe planificarse de modo que se minimicen los puntos calientes térmicos y los puntos de tensión mecánica. Los componentes de alta potencia, como reguladores de tensión, procesadores y transistores de potencia, deben colocarse en zonas donde la disipación térmica sea eficiente, como próximos a disipadores de calor o en zonas abiertas con buena circulación de aire (figura 2). Además, los circuitos analógicos y digitales sensibles deben estar separados para evitar interferencias de ruido y garantizar un rendimiento constante en el tiempo.
Figura 2: La colocación y separación de componentes reduce el riesgo de defectos y sobrecalentamiento
El enrutamiento de trazas es igualmente importante a la hora de mantener la integridad de la señal y prevenir la degradación a largo plazo. Las trazas de señales de alta velocidad deben seguir técnicas de enrutamiento de impedancia controlada, mientras que los planos de alimentación y tierra deben diseñarse adecuadamente al objeto de reducir las fluctuaciones de tensión. Si se evitan los ángulos de trazado pronunciados, se garantiza un ancho de trazado adecuado y se emplean múltiples vías para las conexiones de alimentación y tierra es posible mejorar significativamente la durabilidad de un PCB.
Gestión térmica
El calor excesivo es una de las principales causas de fallo de los PCB. Los componentes que se sobrecalientan pueden degradarse con el tiempo, provocando fallos intermitentes o averías completas. Por consiguiente, es esencial evitar el sobrecalentamiento, que puede degradar las juntas de soldadura, debilitar los materiales de la placa y traducirse en fallos prematuros.
Una gestión térmica eficaz parte de la colocación correcta de los componentes, garantizando el espaciado adecuado de las piezas generadoras de calor y su ubicación próxima a elementos de alivio térmico como vías o disipadores de calor.
Una de las formas más eficaces de gestionar el calor en un diseño de PCB es por medio del uso de vías térmicas y vaciados de cobre. Las vías térmicas actúan a modo de conductos de calor, transfiriendo el exceso de calor de los componentes a las capas internas o a los disipadores de calor. Los vaciados de cobre y los grandes planos de tierra también contribuyen a una distribución más uniforme del calor, reduciendo los picos de temperatura localizados que podrían causar deformaciones o fatiga del material. Además, la incorporación de almohadillas térmicas y el uso de materiales con alta conductividad térmica pueden ayudar a disipar el calor de manera más eficiente.
La distribución de potencia es otra consideración clave. El diseño apropiado del plano de potencia y los condensadores de desacoplamiento minimizan las fluctuaciones de tensión y el ruido, aumentando la fiabilidad de los componentes. La integridad de la señal, especialmente en diseños de alta velocidad, exige una atención meticulosa. Las trazas de impedancia controlada, los planos de tierra y la minimización de la longitud de las trazas son esenciales para evitar reflexiones de la señal y la diafonía. Asimismo, es posible evitar los fallos mecánicos teniendo en cuenta el estrés mecánico durante la fase de diseño, por ejemplo, colocando los componentes alejados de las zonas propensas a la flexión.
Otra consideración esencial es garantizar que el diseño pueda soportar los ciclos de temperatura, una fuente común de estrés mecánico en los PCB. Los ciclos de temperatura se producen cuando la placa se expone a repetidos ciclos de calentamiento y enfriamiento, lo que provoca la expansión y contracción de los materiales. De no corregirse, puede dar lugar a microfisuras y posibles averías. Para combatirlo, los ingenieros pueden utilizar materiales con coeficientes de expansión térmica (CTE) ajustados y diseñar la placa para minimizar la tensión térmica.
Las herramientas de simulación, como el análisis de elementos finitos (FEA), permiten a los ingenieros modelar el comportamiento térmico antes de la fabricación, identificando posibles puntos calientes y optimizando el diseño en consecuencia.
Robustez mecánica
Los PCB a menudo sufren estrés mecánico durante el montaje, funcionamiento y transporte. Las vibraciones, los golpes y la flexión pueden provocar fracturas en las juntas de soldadura, delaminación de las trazas o desprendimiento de componentes. Para mitigar estos riesgos, los diseñadores deben reforzar las zonas de alto estrés con el uso de sustratos de mayor espesor, añadiendo rigidizadores o empleando PCB flexibles en aplicaciones dinámicas.
Los componentes deben colocarse evitando los bordes de la placa, donde es más probable que se doblen. Los elementos de alivio de tensión, como las esquinas redondeadas y las trazas fileteadas, pueden reducir las concentraciones de estrés. Los revestimientos conformados proporcionan una capa adicional de protección contra la humedad, el polvo y la abrasión mecánica, aumentando aún más la durabilidad. En el caso de aplicaciones de misión crítica, las fijaciones mecánicas o los compuestos de encapsulado pueden afianzar los componentes en su lugar, evitando así fallos inducidos por el movimiento.
Las juntas de soldadura son particularmente vulnerables al estrés mecánico que se produce con el tiempo. El uso de materiales de relleno bajo los componentes con matriz de rejilla de bolas (BGA) y la aplicación de juntas de soldadura fileteadas pueden aumentar significativamente la resiliencia mecánica. Además, las técnicas de montaje amortiguadoras, como el uso de juntas elastoméricas o soportes flotantes para PCB, ayudan a reducir el riesgo de daños por impacto.
Integridad de la señal y consideraciones sobre EMI
La integridad de la señal y las interferencias electromagnéticas (EMI) son factores cruciales a la hora de garantizar la funcionalidad y fiabilidad de los PCB, especialmente en diseños de alta velocidad o alta frecuencia. La degradación de la señal, la diafonía y las EMI pueden provocar comportamientos erráticos o fallos, en particular en aplicaciones sensibles como telecomunicaciones y productos sanitarios.
Para preservar la integridad de la señal, los ingenieros deben focalizarse en el enrutamiento de las trazas, el control de la impedancia y una conexión a tierra adecuada. Las trazas de alta velocidad deben tenderse con una longitud y curvatura mínimas para reducir la reflexión y la pérdida de señal. Los pares diferenciales deben trazarse con espaciado y longitud uniformes a fin de mantener la simetría de la señal. Además, puede alcanzarse una impedancia controlada mediante el diseño de apilamientos adecuados con espesores dieléctricos y de cobre perfectamente definidos.
Las EMI pueden mitigarse mediante técnicas adecuadas de apantallamiento, filtrado y conexión a tierra. El apantallamiento consiste en el aislamiento de los componentes o trazas sensibles en materiales conductores para bloquear la radiación electromagnética. El filtrado puede realizarse mediante condensadores de desacoplamiento o perlas de ferrita para suprimir el ruido en las líneas de alimentación y señal. Los planos de tierra deben ser continuos y carecer de interrupciones para proporcionar unas vías de retorno eficaces para las señales y minimizar la radiación electromagnética.
Diseño para la fabricación (DFM) y pruebas
Un diseño de PCB fiable también debe tener en cuenta la fabricación (figura 3). Las tolerancias estrechas, los enrutamientos excesivamente complejos o las holguras insuficientes pueden provocar defectos de producción que comprometan el rendimiento a largo plazo. La colaboración con los fabricantes en las fases iniciales del diseño garantiza que los procesos de fabricación y montaje se alineen a los objetivos de fiabilidad.
Figura 3: Gracias al DFM se mitigan los defectos que podrían dificultar la fabricación
Las pruebas son igualmente cruciales. La inspección óptica automatizada (AOI) y la inspección por rayos X ayudan a detectar defectos de soldadura, mientras que el control de estrés ambiental (ESS) somete los PCB a pruebas de ciclos térmicos, vibración y humedad para simular las condiciones reales. Las pruebas de estrés eléctrico o burn-in, en las que las placas se someten a un estrés elevado durante periodos prolongados, ayudan a detectar los fallos prematuros antes del despliegue.
Las pruebas eléctricas, como las pruebas en circuito (ICT) y las pruebas funcionales, verifican el correcto funcionamiento del PCB y el cumplimiento de las especificaciones de rendimiento. Las pruebas ambientales, que incluyen pruebas de humedad, temperatura y choque, evalúan la capacidad de la placa para soportar factores estresantes externos. Al someter el PCB a estas rigurosas pruebas, los ingenieros pueden identificar y abordar las debilidades antes de la producción en serie, reduciendo así el riesgo de fallos sobre el terreno.
17.04.2025