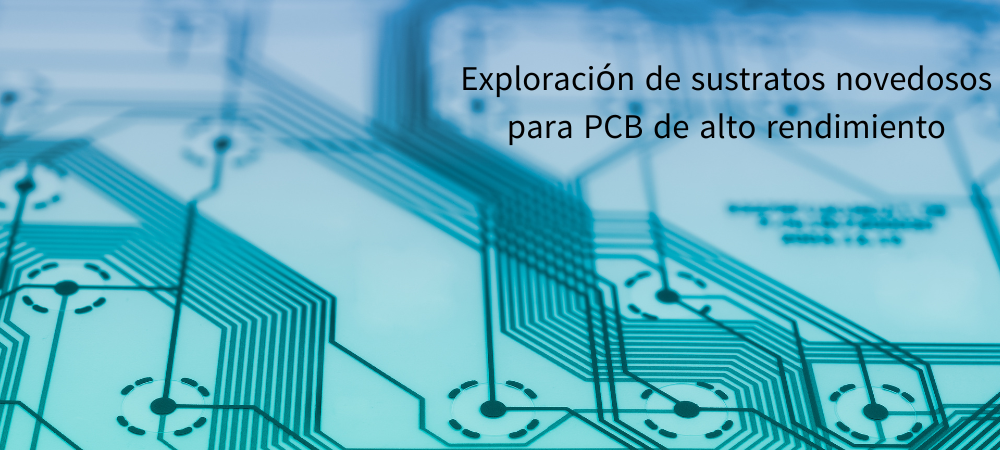
Las placas de circuito impreso (PCB) actúan como una infraestructura fundamental para los dispositivos electrónicos al facilitar la conexión de diversos componentes electrónicos. El avance de los dispositivos electrónicos requiere PCB que ofrezcan un rendimiento mejorado, con diseños racionalizados y capacidades expandidas. El estudio de nuevos sustratos para PCB de alto rendimiento es un factor crucial para materializar estos objetivos. En este artículo se exploran los avances y posibles desarrollos futuros asociados a la utilización de materiales novedosos como sustratos para PCB.
y obtenga un presupuesto para su proyecto de PCBAs en 10 minutos!
Sustratos tradicionales
El FR-4 (retardante de llama 4) ha sido históricamente el material de sustrato estándar para PCB debido a su bajo coste y a un rendimiento relativamente excelente. No obstante, a medida que los dispositivos electrónicos se vuelven más complejos y compactos, las limitaciones de los sustratos tradicionales, como la limitada conductividad térmica y la mala integridad de la señal a altas frecuencias, se han hecho evidentes.
Como material retardante de llama, el FR-4 cumple las normas de seguridad contra incendios y es ampliamente utilizado en aplicaciones en las que la resistencia ignífuga es un requisito esencial. La constante dieléctrica del FR-4 se sitúa por lo general entre 4,2 y 4,7. Esta propiedad es crucial porque determina la rapidez con que las señales pueden propagarse a través de un material. En relación con la estabilidad térmica, el FR-4 responde de forma admirable, ya que soporta un amplio rango de temperatura sin presentar una degradación sustancial. Asimismo, el FR-4 posee una resistencia mecánica y una durabilidad excepcionales. Además de ser un material de sustrato económico y ampliamente disponible, también se ve favorecido para una variedad de aplicaciones de uso general.
Sin embargo, el FR-4 tiene las siguientes limitaciones:
- Conductividad térmica relativamente baja en comparación con algunos sustratos modernos. En aplicaciones de alta potencia, esta restricción puede contribuir a la acumulación de calor, lo que posiblemente afecte al rendimiento y la fiabilidad del dispositivo.
- Integridad de la señal a altas frecuencias: El FR-4 puede ser incapaz de mantener una integridad óptima de la señal a altas frecuencias, dando lugar a una pérdida de señal y causando distorsión.
- El FR-4 no es adecuado para dispositivos electrónicos maleables o plegables debido a su falta de flexibilidad. En aplicaciones que requieren flexibilidad, la poliimida se sustituye frecuentemente por otros materiales.
Sustratos avanzados
Poliimida
La poliimida, un material de sustrato versátil y sofisticado para los PCB, ha cobrado protagonismo en la industria electrónica como resultado de su distintivo conjunto de propiedades. La poliimida, conocida por su extraordinaria estabilidad térmica y flexibilidad, es un componente crucial en diversas aplicaciones.
La poliimida, que se distingue por su resistencia a las altas temperaturas, es estable incluso en entornos severos. Esta característica la hace ideal para aplicaciones en los sectores aeroespacial, automovilístico e industrial, donde los componentes electrónicos pueden estar expuestos a temperaturas elevadas.
La flexibilidad de la poliimida es otra característica notable. La poliimida, a diferencia de los sustratos rígidos tradicionales, permite la fabricación de PCB maleables y flexibles. Esta cualidad es especialmente ventajosa en aplicaciones donde el espacio es limitado o donde se requieren diseños conformados.
Los PCB de poliimida se utilizan frecuentemente en la industria aeroespacial debido a su ligereza y capacidad de adaptación a complejas geometrías. En las aplicaciones automovilísticas, donde predominan las vibraciones y el estrés térmico, la flexibilidad de la poliimida garantiza la durabilidad de los PCB. La figura 1 muestra un PCB flexible con sustratos de poliimida.
Figura 1: PCB flexible fabricado con sustratos de poliimida (fuente: Cadence)
Adicionalmente a sus propiedades físicas, la poliimida posee magníficas propiedades dieléctricas. Mantiene un rendimiento eléctrico constante, lo que hace que sea apropiado para aplicaciones de alta frecuencia. En telecomunicaciones y otros sectores en los que la integridad de la señal reviste una importancia extrema, los PCB de poliimida son útiles para mantener el máximo rendimiento.
No obstante, la poliimida presenta algunas limitaciones. Mientras que rinde excepcionalmente bien en entornos de altas temperaturas, su conductividad térmica es relativamente inferior si la comparamos con otras opciones. En aplicaciones con producción térmica intensiva de calor, puede ser necesaria la adopción de medidas adicionales para gestionar y disipar el calor con eficacia.
Además, la poliimida puede ser más cara que los sustratos convencionales como el FR-4. Este factor de coste puede afectar a la selección del material del sustrato, especialmente en la electrónica de consumo de producción en masa, donde las consideraciones relativas a los costes son cruciales.
Laminados de alta frecuencia de Rogers Corporation
Los laminados de alta frecuencia de Rogers Corporation representan un avance significativo en el campo de los sustratos de PCB, al ofrecer un conjunto único de características que cumplen los estrictos requisitos de las aplicaciones de alta frecuencia.
La baja constante dieléctrica es una de las características distintivas de los laminados de Rogers Corporation, que contribuye a la transmisión eficiente de señales. Esta característica los convierte en ideales para aplicaciones en las que es esencial mantener la integridad de la señal a altas frecuencias, como los sistemas de comunicación, los sistemas de radar y los circuitos de alta frecuencia.
El bajo factor de disipación de estos laminados permite la fabricación de PCB de alto rendimiento con una pérdida de señal mínima. Esta propiedad es esencial para aplicaciones en las que la precisión y la fiabilidad de las señales transmitidas son fundamentales, como los dispositivos de comunicación inalámbrica y los sistemas de radar avanzados.
La excepcional estabilidad dimensional de los laminados de Rogers (figura 2) garantiza que las propiedades eléctricas del material se mantengan constantes a través de todo un rango de temperaturas y condiciones ambientales. Esta estabilidad es crucial para mantener la eficacia de los circuitos de alta frecuencia, especialmente en aplicaciones con importantes variaciones de temperatura.
Figura 2: Laminados RO4500 (fuente: Rogers Corporation)
Estos laminados de alta frecuencia tienen un uso generalizado en el diseño y la producción de antenas, sistemas de comunicación por satélite y sensores de alta frecuencia. En particular, la industria de las telecomunicaciones se beneficia de las propiedades eléctricas superiores de los laminados de Rogers Corporation para garantizar un rendimiento óptimo en la transmisión de datos.
Sin embargo, las propiedades avanzadas de estos laminados de alta frecuencia suelen ir acompañadas de un precio superior al de los materiales de sustrato convencionales. Esto puede afectar al coste total del dispositivo electrónico, influyendo así en las decisiones sobre electrónica de consumo de producción en masa.
Además, la fabricación de laminados de alta frecuencia puede precisar el uso de procesos especializados, planteando posibles retos en cuanto a escalabilidad e integración con los flujos de trabajo de fabricación existentes.
Pyralux de DuPont
Pyralux, un material para circuitos flexibles fabricado por DuPont, destaca como sustrato pionero para PCB. Pyralux se caracteriza por su flexibilidad, que permite a los diseñadores crear circuitos que se adaptan a unas formas y unos diseños poco ortodoxos. Esta cualidad es especialmente ventajosa en sectores en los que las limitaciones de espacio y los factores de forma complejos son consideraciones esenciales.
Pyralux normalmente se compone de una película de poliimida, que funciona como base flexible, y capas de cobre para las trazas conductoras. Esta composición confiere una estabilidad térmica excepcional, garantizando que el material pueda soportar un amplio rango de temperaturas sin degradación de su rendimiento. Pyralux es idóneo para aplicaciones en dispositivos aeroespaciales, automovilísticos y productos sanitarios, donde la flexibilidad y la fiabilidad revisten una importancia extrema debido a su robusta estabilidad térmica.
Las aplicaciones de Pyralux incluyen dispositivos electrónicos miniaturizados y ligeros. Su flexibilidad permite la fabricación de circuitos plegables, convirtiéndolo en ideal para uso en tecnología portátil, pantallas flexibles y sensores médicos. En particular, la industria médica se beneficia del uso de Pyralux en la creación de circuitos flexibles para implantes y dispositivos de diagnóstico.
Pese a sus numerosos beneficios, Pyralux no está exento de desventajas. Este sofisticado material puede resultar más costoso que los sustratos rígidos convencionales, lo que afecta al coste total del dispositivo electrónico. Además, los procesos de fabricación de Pyralux pueden diferir de los de los PCB rígidos, requiriéndose el uso de aparatos y conocimientos especializados. Esto puede plantear dificultades en cuanto a escalabilidad y producción en masa, especialmente para industrias con requisitos de volumen de producción elevados.
PCB con Núcleo Metálico
Los PCB con núcleo metálico, también conocidos como MCPCB, adoptan un enfoque único en el diseño de los PCB al incorporar un núcleo metálico que normalmente es de aluminio o cobre. Esta decisión de diseño confiere una serie de características que hacen que los MCPCB resulten especialmente idóneos para aplicaciones con requisitos de alta potencia o condiciones térmicas exigentes.
Los PCB con núcleo metálico evacuan con eficacia el calor generado por los componentes electrónicos debido a su conductividad térmica mejorada. El interior metálico funciona como disipador térmico, facilitando la eliminación del calor de los componentes vitales. Esta capacidad de gestión térmica es esencial en aplicaciones como la iluminación LED, las fuentes de alimentación y la electrónica de automoción, donde la disipación térmica efectiva es esencial para la fiabilidad y longevidad de los dispositivos.
Además de contribuir a la robustez mecánica de los MCPCB, el núcleo metálico proporciona un soporte robusto a los componentes. Esto resulta especialmente ventajoso en aplicaciones sometidas a tensiones físicas o vibraciones, como es común en entornos automovilísticos e industriales.
Los PCB con núcleo metálico (figura 3) tienen aplicaciones en áreas con altas densidades de potencia, como convertidores de potencia y accionadores de motores. La eficiencia térmica de los MCPCB garantiza que los componentes electrónicos puedan funcionar de manera óptima en condiciones difíciles, reduciendo así el peligro de sobrecalentamiento y mejorando el rendimiento general del sistema.
Figura 3: PCB LED con base de aluminio
No obstante, el núcleo metálico puede hacer que estas placas sean más pesadas y potencialmente más costosas que las placas FR-4 convencionales, limitando así su aplicación en ciertos productos electrónicos de consumo en los que el peso y el coste son cruciales. Asimismo, el núcleo metálico reduce la flexibilidad de estos PCB en comparación con sustratos flexibles como la poliimida.
Tecnologías emergentes
La conductividad eléctrica y la robustez mecánica del grafeno lo convierten en una opción prometedora para los PCB de alto rendimiento. Estos PCB utilizan grafeno, un entramado hexagonal de átomos de carbono, para proporcionar múltiples cualidades únicas que podrían revolucionar los dispositivos eléctricos.
La conductividad eléctrica del grafeno lo convierte en excelente para PCB de alto rendimiento. Su mayor movilidad de electrones que los materiales típicos hace que el grafeno sea más rápido y eficiente en la transmisión de señales. Esta característica beneficia a los sistemas de comunicación avanzados y a las unidades de tratamiento de datos que necesitan un transporte rápido de datos.
La alta conductividad térmica del grafeno hace que la disipación térmica sea eficiente, resolviendo así uno de los mayores problemas del diseño de dispositivos eléctricos. En aplicaciones de alta potencia, los PCB basados en grafeno pueden reducir el sobrecalentamiento y mejorar la fiabilidad y durabilidad de los componentes electrónicos.
La estructura bidimensional de las capas de grafeno permite fabricar unos PCB ultrafinos y ligeros, convirtiéndolos en ideales para dispositivos de superficie y peso limitados. Esto podría dar lugar a unos dispositivos electrónicos más pequeños y ligeros. Muchos sectores industriales podrían beneficiarse de los PCB basados en grafeno. Las propiedades eléctricas y térmicas del grafeno mejoran los sistemas electrónicos de aeronaves, telecomunicaciones, equipos médicos y electrónica de consumo.
Los PCB basados en grafeno se enfrentan a numerosos obstáculos para su implementación generalizada. La síntesis de grafeno de alta calidad a gran escala requiere tecnologías de fabricación rentables. La adaptación y optimización del grafeno a los métodos de producción de PCB plantea problemas de escalabilidad y compatibilidad con los actuales equipos de fabricación.
Además, pese a la notable resistencia mecánica del grafeno, carece de la flexibilidad de algunos materiales basados en polímeros. Esta restricción puede afectar a su aplicabilidad en dispositivos que requieren flexibilidad o adaptabilidad, como la electrónica portátil o las pantallas flexibles.
Los sustratos de polímero de cristal líquido (LCP) son materiales de PCB adaptables y de alto rendimiento. El LCP es reconocido positivamente por sus características eléctricas como la baja constante dieléctrica y el factor de disipación. Los sustratos de LCP son ideales para aplicaciones de alta frecuencia que requieren integridad de la señal. Las telecomunicaciones, la aviación y la comunicación de datos a alta velocidad se benefician de la transmisión fiable de señales a altas frecuencias del LCP.
Otro de los beneficios del LCP es su estabilidad térmica. El LCP tiene una temperatura de transición vítrea elevada y mantiene sus cualidades estructurales y eléctricas a muchas temperaturas. Los sustratos de LCP son ideales para la electrónica de automoción y los sistemas de control industrial debido a su resistencia térmica.
Las propiedades mecánicas del LCP contribuyen a su uso generalizado en el diseño de PCB. Los sustratos de LCP pueden fabricarse como láminas finas y flexibles, permitiendo la producción de placas de circuito impreso flexibles y rígido-flexibles. Esta adaptabilidad es especialmente beneficiosa en industrias como la de productos sanitarios y la electrónica portátil, donde los diseños conformes y ligeros son esenciales.
Los sustratos de LCP se utilizan en una amplia variedad de industrias. Desde implantes médicos y electrónica portátil hasta dispositivos de comunicación de alta frecuencia y antenas, la versatilidad del LCP cubre las necesidades de los sistemas electrónicos contemporáneos.
Sin embargo, el coste de fabricación de PCB basados en LCP puede ser más elevado en comparación con materiales tradicionales como el FR-4. Este factor de coste puede influir en la selección del material del sustrato, especialmente en la electrónica de consumo, donde las consideraciones relativas a los costes juegan un papel significativo.
Los sustratos impresos en 3D representan una nueva frontera en la fabricación de productos electrónicos y marcan el inicio de un cambio de paradigma en la flexibilidad y la personalización del diseño. Junto con la adaptabilidad de la fabricación aditiva, las características de los sustratos impresos en 3D permiten la creación de dispositivos electrónicos adaptados a requisitos específicos.
Los sustratos impresos en 3D se distinguen por su capacidad para producir diseños intrincados y complejos con relativa simplicidad. Esta versatilidad permite la integración directa de rasgos tridimensionales en el sustrato, lo que posibilita la construcción de componentes electrónicos compactos y con formas personalizadas. Esta capacidad es especialmente ventajosa en aplicaciones en las que las limitaciones de espacio y los factores de forma poco convencionales juegan un papel significativo.
Numerosas industrias, incluidas la sanitaria, la aeroespacial y la robótica, pueden beneficiarse de los sustratos impresos en 3D. En el ámbito médico, por ejemplo, los sustratos impresos en 3D facilitan la creación de productos sanitarios implantables que se adaptan a las necesidades específicas de cada paciente. En el sector aeroespacial, la impresión en 3D contribuye a la construcción de componentes electrónicos altamente eficientes y optimizados para el espacio debido a su ligereza y flexibilidad geométrica.
La creación rápida de prototipos es otro campo en el que la adaptabilidad de los sustratos impresos en 3D es evidente. Los ingenieros y diseñadores están en condiciones de iterar y probar rápidamente varios diseños de PCB sin que se requiera la introducción de amplias modificaciones en las herramientas. Ello acelera el ciclo de desarrollo del producto y permite una exploración más eficiente del diseño.
Sin embargo, los materiales de impresión en 3D pueden tener propiedades eléctricas y térmicas distintas a las de los sustratos de PCB convencionales. Para alcanzar el mismo nivel de rendimiento y fiabilidad que los materiales convencionales, la tecnología de impresión en 3D y la ciencia de los materiales pueden requerir un desarrollo continuado.
Además, la escalabilidad de la impresión en 3D para la producción en masa sigue planteando un reto. Si bien la impresión en 3D es óptima para la creación de prototipos y la producción de bajo volumen, puede que no sea tan eficiente o rentable para la producción en masa de dispositivos electrónicos como las técnicas de fabricación tradicionales.
Conclusión
La evolución de los sustratos de PCB es un campo dinámico impulsado por la creciente demanda de dispositivos electrónicos contemporáneos. La exploración de nuevos sustratos es esencial para ampliar los límites del rendimiento y, a la par con el desarrollo de la tecnología, es probable que el panorama de los materiales de PCB sufra cambios significativos. Se debe equilibrar el rendimiento, el coste y la capacidad de fabricación para que estos sustratos novedosos sean extensamente adoptados.
07.03..2024