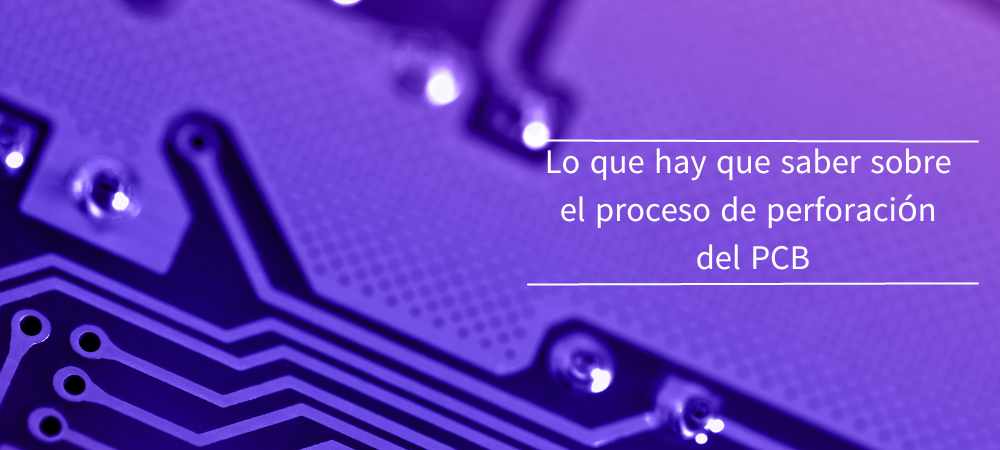
Una vez completado el proceso de laminado, el PCB pasa a la fase de perforación, que se lleva a cabo siguiendo las especificaciones incluidas en los archivos de perforación NC del PCB. El proceso de creación de orificios en la placa de circuito impreso se efectúa para facilitar la colocación de los componentes, la creación de vías y la conexión eléctrica entre las diversas capas del PCB. De los varios pasos que conlleva la producción de un PCB, la perforación es probablemente el más caro y el que más tiempo requiere. Este proceso, de hecho, debe efectuarse con la máxima precisión, ya que incluso el más mínimo error puede tener efectos catastróficos en la calidad del PCB.
La progresiva miniaturización y el aumento en la densidad de los componentes electrónicos han hecho que la fase de perforación del PCB sea aún más crucial y delicada. En el caso de las placas de circuito impreso de una sola cara o de doble cara, el proceso de perforación se lleva a cabo inmediatamente tras cortar el PCB, mientras que en el caso más general de PCB multicapa, la fase de perforación sigue al proceso de laminado.
y obtenga un presupuesto para su proyecto de PCBAs en 10 minutos!
Las máquinas perforadoras de control numérico específico (CNC) decodifican y aplican la información contenida en el archivo de perforación Gerber u ODB, como las coordenadas (X, Y) y el tamaño (diámetro y profundidad) de los orificios. Durante el proceso de perforación, se perfora un orificio cada vez, lo que ralentiza mucho este paso. A fin de optimizar las operaciones, se taladran varios paneles de PCB al mismo tiempo.
Tras la fase de perforación, se lleva a cabo el proceso de cepillado y desbarbado, cuya función consiste en eliminar el exceso de cobre que queda cerca de los bordes de cada orificio. La fase de desbarbado puede efectuarse mediante distintas técnicas, como el cepillado o la limpieza con plasma. Todos los orificios deberán quedar completamente libres de residuos para garantizar un chapado liso y uniforme.
Técnicas de perforación
Los orificios del PCB pueden crearse tanto mediante grabado electroquímico como por medios mecánicos, como la perforación, el corte por láser o el punzonado. El aumento de la densidad de los orificios pasantes y la progresiva reducción de su tamaño requieren técnicas de perforación capaces de crear incluso orificios muy pequeños con gran precisión y reproducibilidad.
Perforación mecánica
El elemento de perforación consiste en un mandril neumático que gira a velocidades próximas a 300 000 rpm. Al objeto de mantener la exactitud a velocidades elevadas, un factor esencial para conseguir una gran precisión incluso en orificios pequeños, la vibración de la broca se controla dentro de un rango de 10 micras. Para mantener la posición exacta del orificio en el PCB, el taladro se monta en un sistema servomecánico que puede desplazarse a lo largo de los ejes X e Y. En cambio, se utiliza un actuador específico para controlar el movimiento de la placa de circuito impreso a lo largo del eje Z. La perforación a alta velocidad garantiza unas paredes de los orificios limpias y lisas, y es necesaria para conseguir un buen chapado de las paredes de los orificios.
La perforación mecánica crea orificios de gran calidad, sin conicidad en los extremos. Asimismo, la velocidad de la perforación mecánica es mayor que la de otros métodos, lo que permite acelerar el proceso de fabricación del PCB. No obstante, si los orificios son excesivamente pequeños, puede suceder que la broca se rompa durante el proceso de perforación. Además, cada orificio deberá someterse a un desbarbado posterior para eliminar el exceso de cobre sobrante del proceso de perforación.
La figura 1 muestra una máquina de control numérico adecuada para la perforación mecánica.
Figura 1: Máquina CNC para perforación mecánica
Perforación láser
Los taladros láser utilizados en el proceso de perforación de PCB se basan en un complejo conjunto de ópticas, capaces de practicar orificios y microvías de diámetro inferior a 200 μm con gran precisión. El tamaño, o diámetro, del orificio a perforar en el PCB está determinado por la apertura del rayo láser, mientras que la profundidad del orificio está determinada por el tiempo de exposición. Se utiliza un juego de lentes concreto para concentrar la energía del rayo láser exactamente en el punto del PCB a perforar. Además de permitir la práctica de orificios sumamente pequeños (como microvías y vías ciegas), la perforación láser presenta la ventaja de eliminar la delaminación.
La perforación láser utiliza un rayo láser de alta densidad para practicar los orificios en el PCB. Si bien existen varios tipos de láser, que se eligen dependiendo del tipo de material del PCB, los dos tipos de láser más comunes son el UV y el CO2.
La principal ventaja de la perforación láser es permitir la ablación de una amplia gama de materiales, puesto que este método es capaz de perforar orificios de pequeño diámetro que no pueden crearse con la perforación mecánica convencional. Asimismo, la perforación láser es una técnica sin contacto y, como tal, no requiere la compleja selección de herramientas de perforación como en el caso del proceso de perforación mecánica.
Las desventajas del proceso de perforación láser incluyen la dificultad para obtener un control preciso de la profundidad del orificio si no hay una capa metálica como tope, y el efecto de quemadura producido por el láser en los bordes del orificio, que normalmente adquieren un aspecto oscuro.
Como con el sistema mecánico, incluso con la perforación láser es posible solapar más paneles, dependiendo de su grosor. Las máquinas perforadoras láser actuales son capaces de crear orificios pasantes con diámetros comprendidos entre 50 y 150 micrómetros.
La figura 2 muestra algunos orificios realizados con una perforadora láser para PCB. Obsérvese la extrema precisión de los orificios, prácticamente libres de imperfecciones o residuos, a pesar de su tamaño tan reducido.
Figura 2: Ejemplos de orificios y microvías hechos con el sistema láser (Fuente: Hitachi High-Tech)
Nuevas técnicas de perforación
El número de orificios a perforar en los PCB ha aumentado drásticamente en los últimos años. Mientras que la placa de circuito impreso de un teléfono móvil normal puede requerir de 30 000 a 50 000 orificios, una placa que utilice componentes de encapsulado a escala de chip (CSP) puede precisar 300 000 orificios o más. Por lo tanto, se necesitan técnicas de perforación que puedan proporcionar un alto rendimiento para la producción de PCB.
Una nueva técnica que puede emplearse para perforar orificios en la placa de circuito impreso es la exposición directa (conocida también como imagen directa). Basado en el principio del procesamiento de imágenes, este nuevo método aumenta tanto la precisión como la velocidad, creando una imagen digital del PCB y convirtiéndola en un mapa de posiciones que sirven de referencia al láser para los orificios a perforar. La técnica de exposición directa mejora la precisión de la alineación de los orificios, ya que el sistema de procesamiento digital de imágenes tiene en cuenta la posible expansión, contracción y deformación sufrida por la placa o el panel. La figura 3 muestra un equipo moderno para la fabricación de PCB que aplica el método de exposición directa.
Figura 3: Equipo para fabricación de PCB por exposición directa
Tipos de orificios
A la hora de perforar orificios en el PCB, deben considerarse dos aspectos importantes. El primero es la relación de aspecto, que influye directamente en la capacidad de efectuar el chapado de cobre en el interior de los orificios. Este proceso se vuelve problemático si el diámetro se reduce y la profundidad del orificio aumenta. La relación de aspecto (RA), definida como la relación entre la profundidad del orificio y su diámetro, asume el valor típico de 10:1 para los orificios pasantes y 0,75: 1 para las microvías. El valor RA generalmente debe mantenerse muy reducido, al objeto de simplificar el proceso de perforación y evitar un excesivo desgaste de la broca en caso de perforación mecánica.
El segundo aspecto se refiere a la distancia entre el borde de un orificio y la zona de cobre más próxima del PCB (puede ser una traza, una almohadilla u otra). El valor mínimo de esta distancia, a fin de evitar posibles averías del circuito, normalmente será igual a 8 milésimas de pulgada.
Los principales tipos de orificios que pueden perforarse en el PCB pueden dividirse en tres categorías:
- Orificios de paso. Estos pequeños orificios de chapa metálica se utilizan para transmitir señales eléctricas, alimentación y masa a través de las diversas capas del PCB. En función del tipo, puede haber vías pasantes, que atraviesan por completo varias capas del PCB, vías enterradas (orificios que quedan completamente en el interior del apilamiento del PCB, sin prolongación en las dos capas superficiales), vías ciegas (que parten de las capas superficiales y a continuación se detienen en una capa interna) y microvías (que tienen un tamaño inferior a las anteriores y que pueden practicarse exclusivamente mediante perforación láser).
- Los orificios para el paso de componentes con orificios pasantes, como conectores, interruptores y otros componentes mecánicos que requieren un robusto montaje garantizado por un encapsulado con orificios pasantes. Este tipo de encapsulado es muy adecuado para componentes de potencia como grandes resistencias, condensadores, amplificadores operacionales y reguladores de voltaje, que generan una cantidad de corriente y calor nada despreciable.
- Orificios mecánicos Son los orificios practicados para el montaje mecánico de la carcasa, ventiladores, disipadores térmicos u otros. Además, estos orificios pueden perforarse para facilitar la alineación del PCB con máquinas de fabricación automatizada.
Pasos de la perforación
El proceso de perforación del PCB puede dividirse en cuatro pasos, que se describen a continuación.
1 - Orificios de posicionamiento
Los orificios de posicionamiento sirven como puntos de referencia durante el proceso de fabricación y pruebas de un PCB. Antes de la perforación, la placa de soporte, el sustrato y la película de aluminio se colocan en la mesa de perforación de alta velocidad, clasificados de abajo a arriba. Con arreglo a las especificaciones de producción, se perforan algunos orificios de posicionamiento con un diámetro de pocos milímetros en el borde de la placa.
2 - Inserción de los pines
A fin de aumentar la eficiencia de la producción, se apilan varios tableros o paneles unos encima de otros antes de realizar la perforación. Los paneles se fijan en la mesa de la perforadora mediante los pines adecuados, evitando así posibles desplazamientos durante el proceso de perforación.
3 - Perforación de los orificios
El proceso de perforación se realiza con máquinas automáticas de control numérico. Por lo tanto, es suficiente con introducir los archivos que contienen los parámetros de perforación convertidos en comandos CAM para realizar los orificios correspondientes. La perforación mecánica es uno de los métodos más habitualmente utilizados para la perforación de orificios en PCB. La broca, que gira a alta velocidad, perfora varios tipos de orificios, incluidos los orificios pasantes chapados (PTH, por sus siglas en inglés), los orificios pasantes sin chapar (NPTH, por sus siglas en inglés) y los orificios pasantes. Antes de la perforación, se coloca un panel de soporte bajo el panel a perforar para proteger la superficie del taladro, mientras que se extiende una película de aluminio por encima para aplanar los orificios de la película de cobre y evitar el sobrecalentamiento del taladro.
4 - Inspección de los orificios
Tras la perforación, hay que comprobar con precisión la posición y la apertura de cada orificio. Después de verificar la inexistencia de problemas, como orificios adicionales, falta de orificios o desplazamiento de la posición de los orificios, el PCB está listo para pasar a la siguiente fase de fabricación.
10.05.2023