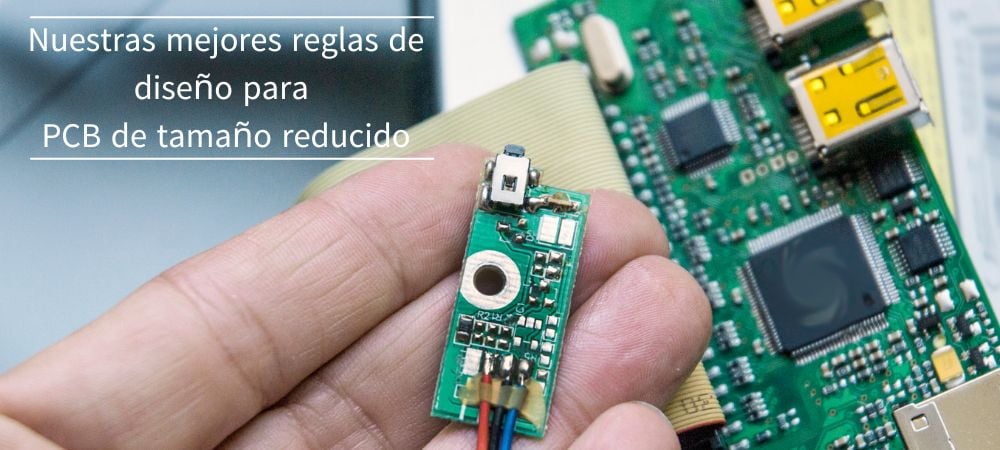
En los últimos años, el desarrollo de nuevas tecnologías electrónicas ha hecho posible una constante miniaturización de los dispositivos electrónicos, con unos PCB cada vez más pequeños y con mayor rendimiento. Tal y como veremos en este artículo, reducir el tamaño de un circuito electrónico presenta múltiples ventajas, además del ahorro de espacio.
Sin embargo, diseñar un PCB pequeño puede representar un verdadero desafío para muchos diseñadores. Además de vías y trazas más pequeñas (el ancho de una traza puede reducirse hasta 50 micras o menos), se necesitarán nuevas normas de diseño para gestionar la mayor complejidad de estos pequeños PCB.
y obtenga un presupuesto para su proyecto de PCBAs en 10 minutos!
Otro aspecto pertinente se refiere al coste del PCB. En la mayoría de los casos, reducir el tamaño de la placa de circuito impreso también conlleva una reducción de los costes de producción. En este artículo se describirán las directrices principales que permiten a los diseñadores reducir el tamaño del PCB sin comprometer su funcionamiento y su fiabilidad.
Ventajas de un PCB más pequeño
Una placa de circuito impreso más pequeña aporta múltiples y valiosos beneficios, que incluyen:
- Menor coste: el uso de componentes miniaturizados y un PCB de menor tamaño permite ahorrar en costes de material. Si bien los costes iniciales relativos al desarrollo pueden ser superiores, se obtiene un beneficio a largo plazo en los costes de producción del PCB. Cuanto mayor sea el número de unidades producidas, mayor será el ahorro materializado.
- Ahorro de espacio: en aplicaciones con limitaciones de espacio, como es el caso de los teléfonos móviles y los dispositivos portátiles, un PCB más pequeño constituye una ventaja esencial.
- Solución más ecológica: reduciendo la cantidad de material requerido para su producción, las emisiones de CO2 causadas por su fabricación se reducen, y existirá menos material a verter/reciclar cuando el producto alcance el fin de su ciclo vital.
- Mayor eficiencia: un PCB miniaturizado normalmente es más eficiente que una placa de circuito impreso más grande. Esto se debe a que el diseño más complejo ya ha abordado y solucionado los principales problemas relativos a la eficiencia de un PCB, tales como la generación y disipación de calor, la absorción de energía y las pérdidas de potencia.
Desafíos de diseño
Un primer desafío al que el diseñador debe enfrentarse al tratar de reducir el tamaño de un PCB se refiere a la geometría de las trazas.
Cuando el tamaño de una traza se reduce, normalmente también se produce una reducción de su grosor. Esto no debería representar un gran problema, si la corriente que fluye a través de la pista no es demasiado elevada. En este caso, las trazas más anchas solamente podrían utilizarse en trayectorias del PCB atravesadas por altas corrientes. En cualquier caso, para determinar la geometría correcta de las trazas, la norma de referencia para el diseñador es la IPC-2221.
Otra posible fuente de preocupación para el diseñador son las vías. Estos pequeños orificios, de hecho, tienen unas dimensiones físicas más allá de las cuales no se puede descender. Por debajo de dos milésimas de pulgada (unas 50 micras), por ejemplo, es difícil recubrir adecuadamente la pared del orificio, reduciendo así la funcionalidad y el rendimiento de la vía. Asimismo, el grosor del laminado determina también el diámetro mínimo de las vías.
Directrices
Al diseñar una placa de circuito impreso de tamaño reducido, deben considerarse ciertos factores. Estos incluyen el ancho mínimo de las trazas, el ancho mínimo de la serigrafía del PCB, el espacio mínimo para la máscara de soldadura, el tamaño de las vías y las almohadillas, etc. En los siguientes párrafos, se analizarán los principales factores que contribuyen a determinar el tamaño mínimo de un PCB.
Microvía
Las microvías son vías especialmente pequeñas, obtenidas exclusivamente mediante perforación láser. Especialmente útiles para establecer conexiones entre las diferentes capas de un PCB multicapa, las microvías tienen un diámetro típico de unas 2-3 milésimas de pulgada (normalmente, empezamos a hablar de microvía cuando el diámetro del orifico es inferior a 6 milésimas de pulgada), mientras que la longitud normalmente no supera los 0,25 mm. Esta solución (se muestra un ejemplo en la Figura 1) es ampliamente utilizada para reducir el tamaño del PCB, puesto que crea conexiones entre trazas pertenecientes a distintas capas, reduciendo de este modo la superficie externa del circuito impreso.
Figura 1: Las microvías son de uso generalizado en los PCB multicapa.
Grosor del laminado
Pueden utilizarse los laminados de PCB más comunes para fabricar placas de circuito impreso de pequeño tamaño. Sin embargo, dado que presentan ciertas limitaciones, los diseñadores deben asegurarse de que los materiales seleccionados, como el FR-4 común, ofrezcan un grosor suficiente para permitir las microvías pasantes y mantener así las características de resistencia y rigidez requeridas.
Normalmente, las trazas de potencia y las trayectorias de corriente de retorno son atravesadas por corrientes elevadas y, por consiguiente, requieren un mayor grosor. Es preferible que estas trazas se enruten utilizando ambas caras externas, mientras que las trazas atravesadas por bajas corrientes o señales analógicas y digitales deben utilizar las capas más internas.
Figura 2: Placa fabricada con un PCB multicapa.
Si en el circuito que se va a diseñar es preciso disipar una gran cantidad de calor, las grandes zonas de cobre que suelen utilizarse como disipadores pueden eliminarse reduciendo el tamaño de la placa y aumentando el grosor de las capas de cobre (como sucede con la tecnología de cobre pesado).
Distancia entre trazas
Al utilizar herramientas de diseño CAD avanzadas, el diseñador es asistido en la optimización y reducción del tamaño del PCB. Por ejemplo, el espacio entre dos trazas puede reducirse a 0,006 pulgadas, o incluso menos.
Además, el tamaño de la placa de circuito impreso depende estrictamente de la aplicación final, de las características de la caja en la que se colocará el PCB, del tamaño de los componentes electrónicos seleccionados y de la posible presencia de disipadores térmicos.
Vías ciegas y enterradas
Además de las microvías, las vías tradicionales merecen asimismo una gran atención, ya que contribuyen a una significativa reducción en el tamaño del PCB. A fin de optimizar el enrutamiento, evitando que el tamaño de la placa crezca desproporcionadamente, la solución basada en vías ciegas ha demostrado ser muy válida. De la misma forma, el uso de vías enterradas permite la conexión entre múltiples capas internas.
No obstante, debe hallarse el equilibrio adecuado entre costes y beneficios. El coste de las vías internas, de hecho, es bastante elevado, lo que está vinculado a la mayor complejidad de la fabricación en comparación con el tipo de orificios pasantes. Si la placa de circuito impreso se produce a gran escala, estos costes pueden distribuirse fácilmente entre el número total de placas. Por el contrario, si el lote de producción es limitado, o solo deben producirse algunos prototipos, el impacto de los costes determinados por las vías ciegas y enterradas ya no es desdeñable.
Asimismo, no siempre resulta posible o fácil encontrar una ruta directa, normalmente utilizada por las vías enterradas, para conectar dos capas internas del PCB, ya que ello depende del número de capas del PCB y de cómo se hayan enrutado las señales en las diversas trazas.
Figura 3: Vías ciegas, enterradas y de orificios pasantes
Tamaño del encapsulado
La selección de los componentes y su encapsulado es fundamental para el diseño de una placa de circuito impreso compacta. De hecho, en electrónica, los mismos componentes (por lo general resistencias y condensadores) están disponibles con encapsulados de distintos tamaños.
Normalmente, los primeros prototipos de un PCB utilizan componentes con encapsulados de mayor tamaño y, por tanto, colocados a una distancia superior a la que podrían tener. Esto viene esencialmente determinado por la necesidad de comodidad en la fase de soldadura y montaje de los componentes, así como para simplificar las pruebas y la depuración de la placa.
Posteriormente, cuando la placa pasa de la fase de prototipado a la de producción, los componentes pueden sustituirse por otros similares, pero con un encapsulado más pequeño, reduciendo así el tamaño del PCB. Puesto que las máquinas de recogida y colocación estándar empleadas en la fase de montaje de un circuito electrónico pueden presentar limitaciones en cuanto al tamaño mínimo del encapsulado, es conveniente abstenerse de seleccionar componentes con encapsulados inferiores a 0402.
Otro factor que afecta al tipo de encapsulado es el nivel de potencia. Los encapsulados más pequeños pueden no ser capaces de manejar las corrientes requeridas, desarrollando así cantidades excesivas de calor o sufriendo daños. Mediante el uso de componentes SMD se puede introducir cierta flexibilidad en la selección del encapsulado mediante la creación de almohadillas de mayor superficie, compatibles con múltiples formatos de encapsulado.
Otra solución, especialmente adecuada para circuitos que utilizan transistores de potencia, es el uso de módulos de potencia (o paquetes con múltiples componentes) en lugar de componentes discretos. Actualmente, existen módulos que, con una huella muy pequeña, sustituyen a circuitos enteros (tales como las fases PFC de la fuente de alimentación o los convertidores AC-DC y DC-DC) que, de otro modo, requerirían un gran número de componentes discretos y más espacio en el PCB.
Una consideración similar se aplica a las resistencias. Si el circuito utiliza varias resistencias del mismo tipo situadas en zonas confinadas del PCB, puede ser conveniente sustituirlas por un único componente, como una red de resistencias (Figura 4).
Figura 4: Una red de resistencias SMD (4x 10 kOhm, 0,0625 W)
Retirada de los puntos de prueba
Al diseñar el PCB de una nueva placa, es muy conveniente introducir muchos puntos de prueba, almohadillas, cabezales o clavijas a fin de simplificar las fases de depuración y pruebas del circuito. De hecho, estos expedientes permiten una rápida adquisición de señales (mediante un osciloscopio u otro tipo de instrumentación), sin necesidad de realizar soldaduras al vuelo o utilizar pinzas de difícil manejo. Cuando la placa ha superado las pruebas funcionales y está lista para la producción, los puntos de prueba pueden retirarse.
Sin embargo, conviene mantener los puntos de prueba y las almohadillas expuestas para permitir una prueba automática de la placa mediante un lecho de clavos, o para facilitar posibles intervenciones de mantenimiento del hardware.
Selección de los conectores
Los conectores no solo satisfacen una función de conexión eléctrica, sino que también son un componente mecánico y, como tal, ocupan cierto espacio. Mientras que para algunos conectores de formato estándar el diseñador no tiene alternativa (como en el caso de los conectores Ethernet, USB o BNC, entre otros), para otros (por ejemplo, para la conexión de cables a la placa) existen diferentes alternativas comerciales. Con mucha frecuencia, los conectores en ángulo de 90º o los bloques de terminales permiten reducir el tamaño de la placa, si bien el coste puede ser superior al de una solución tradicional.
Por consiguiente, también en este caso, el diseñador debe dar con el equilibrio adecuado entre tamaño reducido y coste de las soluciones adoptadas, al objeto de ajustarse al presupuesto de gastos previsto.
22.02.2023