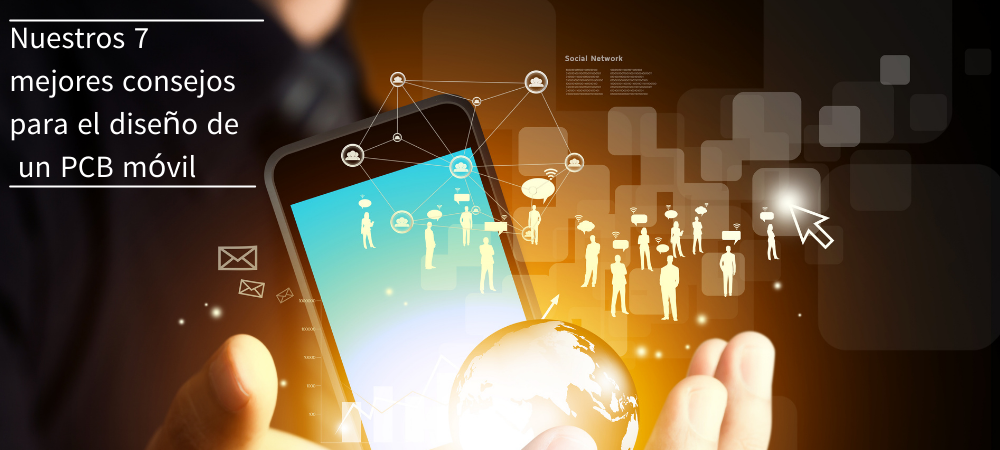
El progresivo aumento de las funciones integradas en los dispositivos móviles de última generación está imponiendo requisitos aún más estrictos en el diseño de placas de circuito impreso. La conectividad Wi-Fi y Bluetooth, soporte para redes móviles 4G y 5G, la integración con cada vez más sensores, representan desafíos tecnológicos sin precedentes para los diseñadores electrónicos. Los dispositivos móviles, comenzando por los smartphones, están evolucionando hacia una mayor inteligencia, miniaturización y multifuncionalidad, lo que requiere placas de circuito impreso cada vez más complejas, capaces de soportar estas demandas (la tendencia impuesta por el mercado es contar con dispositivos cada vez más delgados, con grosores normalmente inferiores a un centímetro).
y obtenga un presupuesto para su proyecto de PCBAs en 10 minutos!
Desafíos técnicos
La tendencia de desarrollo de los smartphones actuales requiere necesariamente placas multicapa (compuestas por 10 o más capas) para crear la placa base y uno o más PCB con un número reducido de capas para las placas auxiliares, posiblemente fabricadas con PCB rígido-flexibles. El uso cada vez más extendido de componentes SiP (System-in-Package, o Sistema en Cápsula) y SoCs (System-on-Chip o Sistema en Chip) de núcleo múltiple, también disponibles con arquitectura de 64 bits, así como la reducción del espaciado de las clavijas de 0,4mm a 0,35mm, están probablemente destinados a contrarrestar el crecimiento del número de capas, si es que no llevan incluso a su reducción.
Los diseñadores de PCB móviles deben prestar mucha atención a los aspectos tecnológicos, desde las etapas más tempranas del desarrollo. Entre los principales factores que hay que tener en consideración a la hora de diseñar este tipo de placas de circuito impreso se incluyen:
- definición del diseño del PCB, posicionamiento de los orificios y marcadores de referencia requeridos para la producción y el montaje automáticos
- definición del panel requerido en la fase de producción del PCB
- selección de los materiales utilizados para los sustratos, selección de los componentes correctos y su empaquetado
- posicionamiento de los componentes y espaciado relativo entre ellos.
1 – Diseño
El posicionamiento debe comenzar por los componentes de mayor potencia, que deben colocarse lo más cerca posible de las piezas que les acompañan, a fin de crear las trazas de alta corriente más cortas posible. Deben mantener también una cierta distancia mínima respecto a las trazas en las que viajan señales de alta velocidad, ya que son más sensibles a las interferencias y fenómenos de diafonía.
De forma indicativa, para el posicionamiento de los componentes, se puede proceder en el siguiente orden: conectores, componentes de potencia, componentes sensibles, componentes críticos, resto de piezas de los componentes. Todos los componentes similares deben orientarse en la misma dirección a fin de reducir la probabilidad de que surjan problemas de soldadura. En el lado soldado de la placa, no deben colocarse otros componentes cerca de las terminales del orificio pasante (PTH), situadas en el lado opuesto de la placa. Los componentes montados en superficie (SMD) deben concentrarse en el mismo lado del PCB; la misma norma debe aplicarse a los componentes PTH (orificio pasante), simplificando y reduciendo el tiempo requerido para el montaje.
Tras colocar los componentes, debe procederse con el enrutamiento de las trazas relativas a potencia, señales y tierra. El enrutamiento de las trazas debe priorizar en función de niveles de potencia y susceptibilidad al ruido y las interferencias. Los componentes de potencia deben utilizar planos de tierra o de potencia para una mejor disipación térmica, mientras que las trazas que transportan las señales deben ser lo más cortas y rectas posible, evitando así que viajen en paralelo en largas distancias, al objeto de evitar un fenómeno de acoplamiento. Los condensadores de desacople deben posicionarse cerca (o debajo) de las clavijas de suministro eléctrico, para que puedan absorber cualquier pico de potencia espurio.
Las trazas que transportan señales que requieren un alto grado de aislamiento deben enrutarse en capas separadas, posiblemente ortogonales entre sí con un plano de tierra que las separe. El posicionamiento ortogonal de las trazas minimiza el acoplamiento capacitivo, mientras que el plano de tierra proporciona un blindaje eléctrico. Esta técnica es ampliamente utilizada a fin de obtener trazas con impedancia controlada, en las que la impedancia característica permanece constante en cada punto de la traza (por ejemplo, 50Ω). Dos tipos muy comunes de trazas con impedancia controlada son las microstrips y striplines que, a pesar de tener diferentes estructuras geométricas, producen resultados similares. El control de la impedancia, que puede realizarse mediante una de las muchas herramientas disponibles online, a menudo implica la necesidad de equilibrar la longitud de las trazas. En casos extremos, esto puede requerir la introducción de “serpentinas” adecuadas en el PCB, como se muestra en la Figura 1.
Figura 1: introducción de “serpentinas” para equilibrar la longitud de la traza
2 – Separación
La sección de RF de un PCB móvil debe separarse y aislarse adecuadamente de las secciones de suministro eléctrico y de las secciones digitales o analógicas de baja potencia. Las señales analógicas sensibles deben mantenerse también lo más alejadas posible de las señales digitales de alta velocidad y de las señales de RF. Las señales digitales y analógicas deben tener cada una de ellas sus propias conexiones de tierra.
Los circuitos analógicos y digitales, siempre que sea posible, deben mantenerse separados. De hecho, el rápido aumento de los flancos de las señales digitales podría crear picos de corriente y generar ruido, dos factores que potencialmente pueden dañar los circuitos analógicos. La Figura 2 muestra un ejemplo de cómo puede realizarse la separación entre la sección analógica y digital de un PCB.
Figura 2: separación entre la sección analógica y digital (Fuente: Altium)
3 – Vías pasantes y marcadores de referencia
Las trazas de alta corriente, especialmente aquellas que atraviesan múltiples capas, deben incluir al menos de dos a cuatro orificios pasantes. Esto mejora la disipación térmica y reduce las pérdidas tanto inductivas como resistivas. Utilizar orificios más grandes permite a la placa soportar corrientes más elevadas y optimiza la conducción térmica. Asimismo, para las pistas con altas corrientes, es mejor utilizar múltiples orificios en lugar de uno solo.
En general, cada lado del PCB debe incluir al menos dos marcadores de referencia. Estos normalmente deben tener una forma circular con un diámetro de 1 mm (40 mil). Asimismo, los marcadores de referencia deben ser del mismo color para el fondo interno, siendo así compatibles con el revestimiento de cobre.
4 – Gestión térmica
La gestión térmica es un aspecto importante que merece especial atención, ya que una gestión térmica inadecuada podría degradar o incluso dañar el PCB. Por tanto, el diseñador debe evaluar (consultando las fichas técnicas pertinentes) los valores de resistencia térmica de cada componente y determinar qué componentes disipan más calor. A continuación, debe asegurarse que los componentes más críticos se posicionen a una distancia lo bastante grande de los componentes que generan calor.
Utilizar pistas de mayor tamaño es el primer truco para combatir la generación de calor. Los componentes de potencia, sujetos a un mayor sobrecalentamiento, deben posicionarse en el centro de la placa para ayudar a disipar el calor, permaneciendo separados de otros componentes calientes. Eventualmente, si el diseño lo permite, deben considerarse también incluso los ventiladores de refrigeración, disipadores térmicos, planos de tierra y potencia sólidos, y un número adecuado de vías térmicas. Puede que también sea necesario aumentar el grosor de los laminados o utilizar diferentes materiales con una mejor resistencia y disipación térmica.
5 – Planos de tierra
Un plano de tierra ofrece una tensión de referencia común, proporciona blindaje, permite la disipación térmica y reduce la inductancia parasitaria (aunque aumenta la capacitancia parasitaria). En la situación ideal, todo PCB debe tener al menos una capa totalmente dedicada al plano de tierra. Los mejores resultados se obtienen si el plano es sólido, es decir, sin ninguna interrupción.
Dado que los planos de tierra generalmente ocupan una gran superficie del PCB, su resistencia es mínima. A bajas frecuencias, la corriente tomará el camino con la resistencia más baja, mientras que a altas frecuencias la corriente seguirá el camino con la impedancia más baja. Los planos de tierra y de potencia deben ser simétricos, centrados y colocados en las capas más internas del PCB.
6 – Materiales
La tecnología empleada para la fabricación de los PCB multicapa se utiliza de forma generalizada en aplicaciones médicas. Al fabricar un PCB multicapa, se aplica un proceso sustractivo para generar las capas del PCB. La interconexión entre las capas se obtiene a través de etapas de laminación, perforación mecánica, chapado de cobre químico y chapado de cobre. El proceso se completa con la creación de la máscara de soldadura, el recubrimiento protector del PCB (recubrimiento conformado) y la serigrafía.
Las placas de circuito impreso multicapa de hoy en día son excepcionalmente delgadas, tienen un ancho y espaciado de trazas muy pequeños y presentan una densidad de trazas y componentes particularmente alta.
7 – Panel
Un buen diseñador de PCB debería incluir en el desarrollo el lanzamiento de un diseño de panel para la fase de montaje. Una vez finalizado el diseño del PCB, el siguiente paso consiste en enviar la información relacionada con el mismo a una empresa de fabricación, junto con una especificación de diseño de panel para garantizar que el formato de recepción del PCB sea el previsto. Dicha información debe incluir:
- el tamaño máximo de panel que la maquinaria de producción puede gestionar
- marcadores de referencia adicionales a los sistemas de alineación visual de la maquinaria, para saber exactamente dónde está el PCB. La práctica estándar dicta agregar tres marcadores de referencia al panel en tres de las cuatro esquinas a cada lado del PCB para que la máquina pueda determinar si el PCB se ha cargado correctamente o no.
- introducir, si la maquinaria lo requiere, orificios especiales (orificios de referencia) cerca de los bordes del panel, para permitir el procesamiento del PCB
- curvar las esquinas del panel al objeto de que, al envasar al vacío los paneles del PCB, las esquinas no puedan romper los sellos.
La Figura 3 muestra un ejemplo de un panel diseñado correctamente.
Figura 3: ejemplo de un panel de PCB
26/11/2021