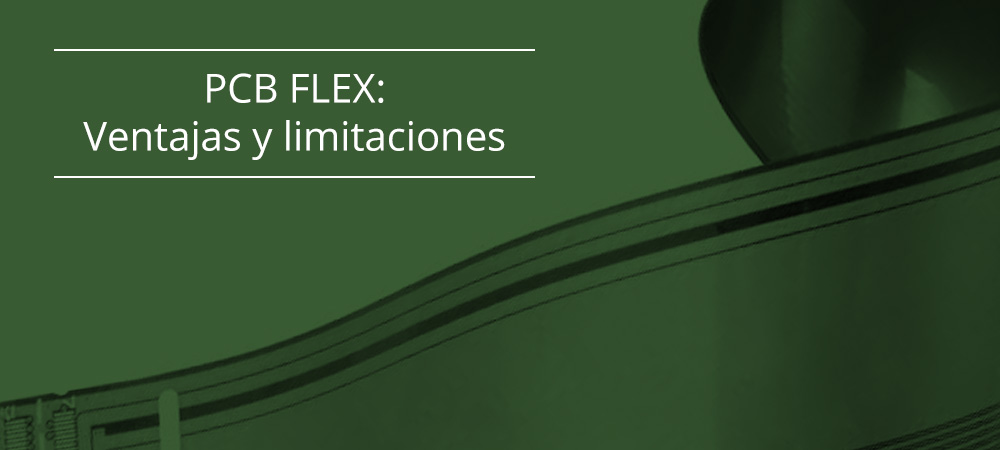
La tecnología específica de los circuitos impresos flexibles también conocida como FPC (Flexible Printed Circuit), está en crecimiento continuo, con aplicaciones en los principales sectores de la electrónica, tales como el consumo, el automóvil, equipamiento médico, ropa inteligente, telecomunicaciones y aeroespacial. La introducción de PCB flexibles ha revolucionado las técnicas tradicionales de interconexión eléctrica, utilizadas habitualmente para conectar varias partes del mismo circuito o de varios dispositivos electrónicos. Gracias a la naturaleza flexible de la conexión, a su compacidad y a la alta densidad de enlaces eléctricos realizables, elegir circuitos flex permite obtener una reducción considerable del espacio, del peso y de los costes en comparación con una solución equivalente a base de PCB rígido. Reemplazaron muchos tipos de cableado, a menudo hecho a mano, en varias aplicaciones, reduciendo el coste total del cableado eléctrico hasta un 70%. El centro de un FPC está realizado por películas suaves y finas capas de material conductor que realizan la conexión eléctrica sustituyendo los cables tradicionales (piense por ejemplo en la conexión entre una tarjeta micro controlada y una pantalla LCD u OLED) y en los que los componentes electrónicos puedan fijarse directamente mediante soldadura o adhesivo conductor. La imagen 1 muestra un ejemplo de circuito impreso flexible.
Imagen 1: Un circuito impreso flexible (Fuente: Hoyogo)
Estructura de un PCB flexible
Al igual que en el caso de los PCB rígidos, los PFC pueden dividirse en circuitos de capa única, de doble cara o multicapa. Los principales elementos de un circuito impreso flexible de una sola capa son los siguientes:
- Película de sustrato dieléctrico: el material de base del PCB. El material más utilizado es la poliimida (PI), caracterizada por una alta resistencia a la tracción y a la temperatura;
- conductores eléctricos: de cobre, representan las pistas del circuito;
- acabado protector, realizado con una capa de material flexible que protege y aísla (coverlay o cover coat)
- material adhesivo (polietileno o resina epoxi), utilizado para unir las diferentes partes del circuito.
La primera fase de fabricación del FPC consiste en grabar el cobre para obtener las pistas, mientras que el revestimiento protector (cover lay) debe ser perforado de manera que permita el acceso a las playas de acogida. Después de un tratamiento de limpieza, los componentes se ensamblan por laminación. Los bornes externos/patas, necesarios para la conexión eléctrica del circuito, están protegidos de la oxidación por inmersión en estaño u oro. Si el circuito tiene una complejidad elevada, o requiere la presencia de planos de masa de cobre, es necesario pasar a un FPC doble cara o multicapa. La técnica de fabricación es muy similar a la utilizada para los circuitos flexibles de una sola capa, con la diferencia de que en los FPC multicapa es necesario insertar PTH (Plated Through Hole), para crear, en su caso, la conexión eléctrica entre diferentes capas conductoras. El ensamblaje de estos materiales forma un circuito flexible, en el que el material adhesivo sirve para conectar las pistas conductoras con el sustrato dieléctrico o, en los circuitos flexibles multicapa, para conectar las capas individuales juntas. Además, la película adhesiva también se puede utilizar con fines de protección, evitando la humedad, el polvo u otros agentes externos de corroer o oxidar el circuito flexible. En la imagen 2 podemos observar la estructura de un FPC multicapa. El ejemplo ilustrado incluye cuatro capas de cobre conductoras, PTH (en el lado derecho de la imagen) y agujeros para acceder al material conductor (en el lado izquierdo de la imagen, en las dos capas externas).
Imagen 2: Estructura de un PCB Multicolor flexible (Fuente: Altium)
Ventajas de los PCB flexibles
Al ser flexibles, los FPC se pueden plegar y flexionar, lo que permite una mayor libertad en el diseño y funcionamiento de la aplicación. Estos circuitos también pueden ajustarse en espacios muy pequeños o de forma irregular, característica no admitida por los circuitos rígidos estándar. Las FPP también ocupan menos espacio, lo que reduce el peso en la placa base de la aplicación. El uso óptimo de los espacios libres permite también una mejor gestión térmica, reduciendo la cantidad de calor a disipar. En comparación con los PCB rígidos, los circuitos impresos flexibles también pueden ser más fiables y duraderos, especialmente en aplicaciones en las que los circuitos están sometidos a vibraciones continuas y a tensiones mecánicas. Las técnicas de interconexión estándar, basadas en hilos soldados y conectores cableados a mano, se sustituyen por circuitos impresos flexibles, caracterizados por un peso y un espesor extremadamente bajos, que van acompañados de una resistencia mecánica elevada, resistencia a las altas temperaturas y a los agentes atmosféricos, así como una buena inmunidad electromagnética (ECM). Piense, por ejemplo, en el cableado de varios dispositivos electrónicos en el sector automovilístico, como el salpicadero, la pantalla y las interfaces hombre-máquina (controles rotativos, botones, etc.). Todos estos dispositivos requieren una conexión fiable en todas las condiciones de funcionamiento del vehículo, además de estar sometidos a tensiones y vibraciones mecánicas continuas. En este sector, los circuitos impresos flexibles garantizan fiabilidad, durabilidad e intervenciones de mantenimiento tendentes a cero. La imagen 3 muestra una aplicación automotriz de la tecnología FPC, usada aquí en un interruptor de iluminación del coche.
Imagen 3: ejemplo de aplicación FPC en la industria del automóvil
Además, el uso de FPC puede reducir la incidencia de errores humanos durante el cableado, con una mejora consecuente de la calidad y una reducción de los costes. Esta tecnología ayuda a reducir considerablemente el tamaño y el peso de la aplicación, un factor clave para la creación de dispositivos electrónicos fiables, compactos y altamente integrados.
Limitación de PCB flexibles
Aunque existen varias ventajas significativas, la tecnología FPP presenta, sin embargo, algunas desventajas. En primer lugar, en comparación con los PCB rígidos tradicionales, las FPP tienen un alto coste inicial. Dado que los circuitos flexibles están diseñados para aplicaciones muy específicas, los costes iniciales de diseño de los circuitos y prototipos son superiores a los de los PCB rígidos. Si el costo es un factor determinante en la elección del tipo de PCB, es preferible utilizar esta tecnología únicamente para volúmenes de producción no demasiado bajos. También es difícil reparar o modificar el PCB cuando es necesario mejorarlo. En este caso, en efecto, es necesario primero quitar la película protectora que envuelve el circuito, efectuar la intervención y luego volver a poner la protección. Al ser una tecnología relativamente nueva, no todos los fabricantes están equipados para suministrar este tipo de producto a sus clientes. Además, durante la fase de ensamblaje, hay que tener mucho cuidado, ya que el circuito puede dañarse fácilmente si se manipula incorrectamente o por personal no cualificado.
Conclusión
Los circuitos impresos flexibles se utilizan en varias aplicaciones que encontramos en la vida cotidiana, como teléfonos inteligentes, tabletas, cámaras, impresoras y portátiles. Incluso pueden ser alojados dentro de nuestro cuerpo, constituyendo un elemento fundamental para la creación de marcapasos, implantes cocleares y desfibriladores. En los últimos años, la industria de FPC se ha desarrollado considerablemente, impulsada por la propagación de dispositivos portátiles y electrónicos médicos cada vez más pequeños y ligeros. En muchas aplicaciones, los PCB flexibles pueden eliminar la necesidad (y el coste) de conectores y cables, mejorando la fiabilidad de la conexión y reduciendo el tiempo de montaje, los costes de montaje y las dimensiones globales del aparato.
En conclusión, podemos afirmar que los PCB flexibles han permitido la creación de aplicaciones nuevas e interesantes, no realizables con los PCB rígidos tradicionales. Sin embargo, en el análisis preliminar de cada nuevo diseño, es necesario evaluar cuidadosamente las ventajas y los límites derivados del uso de un PCB flexible, en comparación con un PCB rígido. Para muchas aplicaciones, la elección de un PCB flexible es obligatoria, para otros dependerá de los resultados del análisis de costes y beneficios.
y obtenga un presupuesto para su proyecto de PCBAs en 10 minutos!