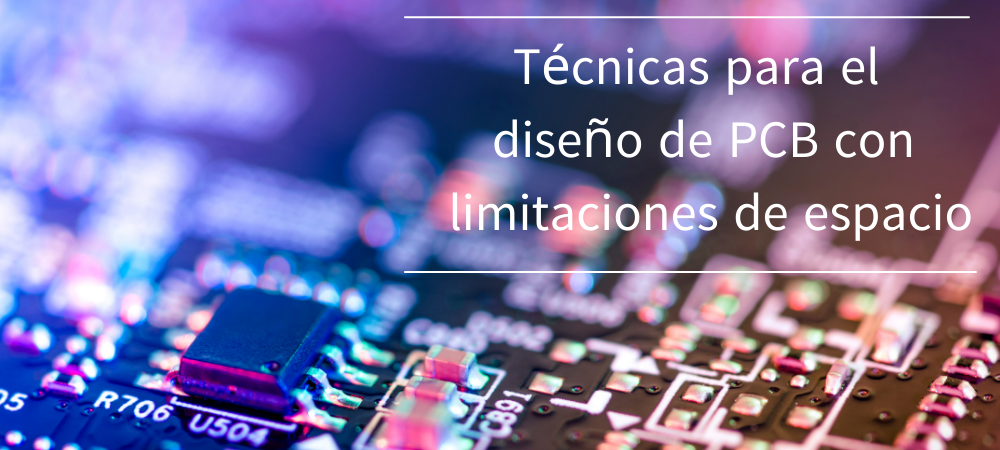
Con los avances materializados en tecnología de chips, los diseños de PCB han experimentado cambios significativos en cuanto a tamaño y forma. Estos cambios han llevado a una demanda exponencial de rendimiento óptimo en un factor de forma compacto, lo que ha representado un verdadero desafío para las metodologías convencionales de las técnicas de diseño de PCB.
Durante la fase de diseño del circuito, encontrar la forma óptima de utilizar el espacio asignado para el trazado requiere decisiones cruciales en muchos aspectos. Estas decisiones tendrán un gran efecto en la calidad del producto a lo largo de su vida útil. Por consiguiente, las limitaciones de enrutamiento de los PCB son uno de los factores principales en la tecnología del PCB de gran valor añadido para el diseño.
y obtenga un presupuesto para su proyecto de PCBAs en 10 minutos!
Seguidamente, la miniaturización es evidente en todos los sectores industriales y crea nuevos desafíos de diseño a los ingenieros a quienes se encomiendan las soluciones de adaptación en diseños con limitaciones de espacio. Por tanto, el diseñador debe asegurarse de que no se comprometa la salida deseada del circuito eléctrico y el PCB, resolviendo a su vez los problemas de limitación de espacio.
Diseño y esquematización del PCB
La esquematización de la placa de circuito impreso es el primer paso, y uno de los más importantes, en la creación de un diseño de PCB. Es esencial crear un esquema abstracto que contenga las regiones del PCB con límites de altura/ancho, componentes utilizados en los circuitos y el número de trazas empleadas, ya que el esquema del PCB representa la forma mecánica final de la placa a fabricar.
Recortes: El diseño debe efectuarse con precisión en la Capa Mecánica para representar el tamaño y la forma exactos del recorte. Durante este proceso hay que tener en cuenta las dimensiones correctas y cualquier tolerancia eléctrica específica. Inicialmente, el diseñador puede crear el contorno con el empleo de una pequeña línea (de 0,5 mm de ancho), donde el centro de la línea puede utilizarse para representar el contorno exacto del recorte.
Esquinas internas de un recorte: El recorte debe fresarse utilizando una herramienta de 2,00 mm, lo que garantiza que la esquina interna tenga un radio mínimo de 1,00 mm. Si un requisito exige un radio inferior, deben realizarse los correspondientes cambios en la capa mecánica.
Asegurar el tamaño de la ranura: Las ranuras del PCB son orificios en la placa del circuito que son demasiado grandes para formarse mediante métodos normales de perforación. Deben realizarse con precisión en la Capa Mecánica para representar el tamaño y el ancho exactos de la ranura junto con sus tolerancias. Existen principalmente dos tipos de ranuras:
- Ranuras chapadas: En la fabricación de PCB, las ranuras chapadas constan de un chapado de cobre. Siempre que las ranuras de PCB están chapadas con cobre en la base y en la parte superior se denominan ranuras chapadas.
- Ranuras sin chapar: Las ranuras sin chapar constan de un orificio mayor que el tamaño del cobre de la almohadilla. En las ranuras sin chapar, existen superposiciones de almohadillas ya que el fabricante perfora la parte no chapada tras el proceso de cobre no electrolítico.
Fig.: 1: Tamaño de las ranuras del PCB
Fuente: protoexpress.com
Limitaciones de enrutamiento en los PCB
Últimamente el enrutamiento del PCB se ha convertido en un problema importante debido a la creciente complejidad de los circuitos electrónicos. Existen diferentes reglas que se aplican al diseño y la producción de un PCB, que contribuyen a que el diseñador ensamble diferentes componentes presentes en el circuito y ayudan en la comunicación de los datos que se efectúa desde diferentes partes del circuito a la salida deseada. Estas reglas se aplican para evitar problemas durante la producción en serie y el proceso de fabricación, a fin de garantizar un rendimiento eléctrico al más alto nivel.
A continuación, se enumeran algunos de los parámetros limitantes en el enrutamiento en los PCB.
Componentes: Existen varias limitaciones que los diseñadores pueden regular para componentes como resistencias, condensadores, transistores, circuitos integrados, etc., que incluyen holguras con respecto a otras piezas y objetos, partes recortadas de la placa del circuito impreso, etc. La holgura ideal para los componentes, salvo que se especifique lo contrario, es de 0,25 mm. Los componentes de tamaño inferior a 1,6 mm deben tener una holgura de 0,15 mm. El diseñador puede establecer limitaciones para la parte del PCB que debe restringirse a una zona concreta a causa de diversos factores eléctricos, como los niveles de potencia, la transferencia de calor, etc.
Ancho de traza:
Figura 2: Ancho de traza
Fuente: designwanted.com
Los diseñadores pueden configurar el ancho de una traza para distintas secciones del circuito. El ancho de traza se utiliza principalmente para la impedancia controlada. En condiciones en las que haya una potencia variable, la traza de enrutamiento debe tener anchos extragrandes y para los diseños de RF, deben existir anchos con cambios frecuentes.
Enrutamiento de las trazas:
Figura 3: Enrutamiento de las trazas
Fuente: pcbdesignworld.com
Además del ancho y la holgura básicos, los PCB requieren un control más preciso de la forma de enrutar la traza. Utilizando el enrutamiento de serpentín, el diseñador puede hacer coincidir la longitud de una traza con la de otra, lo que puede incluir asimismo las longitudes mínima y máxima de una traza. También pueden aplicarse restricciones de topología al PCB para asegurarse de que sigue un patrón concreto, como la topología en T.
Planos: Una descarga térmica adecuada puede asegurarse con regulaciones que permitan conexiones entre planos de potencia y tierra. Puede permitirse una cantidad mínima de anchos del metal en el plano junto con sus diferentes patrones. Los planos presentan una serie de ventajas, entre ellas:
- Mejora del desacoplamiento entre circuitos: La superficie de un plano puede actuar como condensador de desacoplamiento de placas paralelas entre la capa de aislamiento y tierra, lo que contribuye a evitar la propagación del ruido a través de la alimentación de energía a diferentes partes del circuito.
- Rutas de retorno cortas: Las rutas de retorno más cortas tienen una mejor compatibilidad electromagnética (EMC) debido a la facilidad de seguir una vía, justo desde la capa de señal hasta el plano de potencia, y desde el plano de potencia hasta alimentar el circuito.
- Mayor capacidad de transmisión de potencia: Los planos pueden gestionar una mayor capacidad de transmisión de potencia en comparación con las trazas o pistas, lo que reduce la temperatura operativa del PCB.
Interconexión de alta densidad (HDI)
En el mundo de los PCB, el término HDI hace referencia a la interconexión de alta densidad, una tecnología que asiste en la fabricación de PCB pequeños, ligeros y compactos. En el escenario actual, los dispositivos electrónicos son cada vez más pequeños y compactos. De manera local, se computan complejos procesos de cálculo con estos pequeños dispositivos. En tales circunstancias, el uso de PCB multicapa fabricados con el método normal creará problemas como la diafonía, la mala integridad de la señal, etc. Estos problemas pueden solucionarse con la tecnología HDI que se utiliza en dispositivos pequeños y compactos.
Por qué HDI
La diferencia básica entre los PCB normales y los fabricados con tecnología HDI es que los PCB HDI tienen una mayor densidad de cableado por superficie, en comparación con los PCB normales, permitiendo por tanto la producción de dispositivos electrónicos más pequeños y ligeros, pero potentes. La tecnología HDI emplea materiales delgados y capas mínimas para su composición, en comparación con los PCB normales, lo que los hace perfectos para su uso como pequeños dispositivos complejos.
Una de las mayores inquietudes sobre la tecnología HDI es la integridad de la señal, ya que estas están colocadas muy juntas. Esto se soluciona utilizando microvías, que transportan una capacitancia e inductancia parásita menor simplemente debido a su pequeño tamaño. Las microvías tienen un diámetro inferior a 150 micras y, por ello, se perforan con láser. Por lo tanto, pueden colocarse juntas muchas capas sin aumentar la diafonia y la fuerza de acoplamiento del ruido y, por lo tanto, manteniendo la integridad de la señal.
Fig. 4: Diferentes vías del PCB
Fuente:mistralsolutions.com
Materiales utilizados para la HDI
En la selección del material para producir el PCB, debe tenerse en cuenta que el material elegido para el sustrato debe tener una baja constante dieléctrica, debido a lo cual, el acoplamiento capacitivo entre las dos capas adyacentes se reduce y también las señales viajan mucho más rápido a través de estas placas. Como consecuencia, la integridad de la señal se mantiene reduciendo la diafonía entre las capas adyacentes, lo que es de suma importancia en la HDI, ya que las trazas están colocadas todas juntas en un área pequeña y densa.
El éter epoxi se ha empleado de forma predominante como sustrato debido a su bajo coste y a sus buenas propiedades térmicas, químicas y eléctricas. Aparte, debido a sus bajos valores de Dk (constante dieléctrica) y Df (factor de pérdida dieléctrica), también se utilizan resinas de poliimida y de éster de cianato. Además de estas resinas termoestables, también se utilizan resinas termoplásticas como la poliimida (PI) y el politetrafluoroetileno (PTFE) a causa de su naturaleza flexible.
Tecnología del PCB flexible
Las placas de circuito impreso flexibles (FPC) constituyen un avance en el creciente campo de la tecnología de PCB, y solucionan la mayor parte de los problemas causados por las limitaciones de espacio en un PCB. Múltiples tipos de cableado que se efectúan en los PCB para diversas aplicaciones se han sustituido con éxito por las placas de circuito impreso flexibles, lo que reduce los costes del cableado eléctrico prácticamente en un 70%. Debido a su compacidad y flexibilidad, puede efectuarse con éxito un elevado número de conexiones eléctricas y técnicas de conexión utilizando los FPC.
Figura 5: Placa de Circuito Impreso Flexible
Fuente: raypcb.com
Estructura de una Placa de Circuito Impreso Flexible
De la misma forma que una placa de circuito impreso rígida, las que son flexibles pueden dividirse ent simples, de una capa, de doble capa y multicapa. En comparación con la placa de circuito impreso rígida, el espacio para el trazado de las almohadillas, el espaciado del ancho de las trazas y el tamaño de las almohadillas de las vías son los mismos, lo que se debe a los materiales flexibles empleados y al proceso de chapado para la fabricación de FPC. La composición de una placa de circuito impreso flexible es la siguiente:
- Película de sustrato dieléctrico: La película de sustrato dieléctrico es el material base de la película de sustrato. La poliamida (PI) es el material utilizado más habitualmente para fabricar la película debido a su alta resistencia a la tracción y a la temperatura.
- Conductores eléctricos: Los conductores eléctricos son de cobre. Se utilizan para formar las trazas del FPC.
- Material adhesivo: Hechos de polietileno o resina epoxídica, los materiales adhesivos se emplean para unir distintas partes de los FPC.
Figura 6: Estructura de una Placa de Circuito Impreso Flexible
Fuente: proto-electronics.com
Conclusión
Algunas de las técnicas de limitación de espacio pueden solventarse asegurándose de que los componentes que se colocan tengan una holgura absoluta respecto a otros componentes, es decir, 0,25 mm, y que se aplican limitaciones de enrutamiento adecuadas para el ancho de traza mediante cálculos adecuados con arreglo a varios parámetros eléctricos. Pueden utilizarse planos para garantizar que la temperatura de la placa permanezca bajo control, lo que eventualmente mejorará la capacidad de transporte de energía y el desacoplamiento entre circuitos.
La tecnología HDI en los PCB asegura un ancho de trazas y vías en los PCB fabricados delgado y pequeño, lo que garantizará que la integridad de la señal de la placa permanezca intacta.
La mejor alternativa a los problemas de limitaciones de espacio en los PCB puede resolverse con el uso de Circuitos Impresos Flexibles (FPC), que tienen aplicaciones en casi todos los dispositivos que utilizamos en nuestra vida cotidiana, como smartphones, cámaras, tabletas, impresoras, ordenadores portátiles, e incluso pueden colocarse en el interior del cuerpo humano para marcapasos y diversos implantes.
11.04.2022