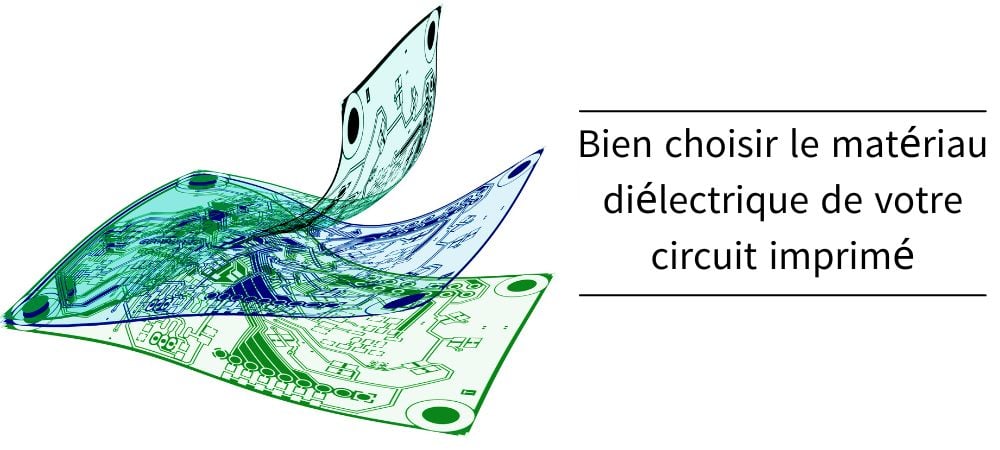
Les matériaux diélectriques constituent la base des circuits imprimés. Comme illustré sur l’image 1, ils forment le substrat non conducteur inséré entre les couches conductrices du circuit imprimé. Les matériaux diélectriques doivent très peu conduire l’électricité et former une couche isolante entre les couches conductrices. Comme nous le verrons plus en détail dans l’article, l’un des matériaux diélectriques les plus utilisés est le FR-4, mais il existe d’autres types de matériaux que les concepteurs doivent connaître et sélectionner en fonction des caractéristiques de l’application visée.
Le choix du matériau diélectrique s’effectue essentiellement en fonction des propriétés électriques, thermiques et chimiques du matériau en question.
et recevez un devis pour votre projet de PCBA dans les 10 prochaines minutes !
Image 1 : Structure de base d’un circuit imprimé
Propriétés électriques
Pour choisir un matériau diélectrique, il faut tenir compte de deux propriétés électriques principales, à savoir la constante diélectrique et le facteur de perte.
Constante diélectrique
Ce paramètre, représenté par le symbole Dk, est également appelé permittivité relative (Ɛr). La constante diélectrique est une mesure du niveau d’isolation électrique assuré par le matériau et constitue un facteur fondamental pour garantir l’intégrité du signal et l’ajustement des impédances. Les valeurs typiques de la constante diélectrique que l’on trouve dans les matériaux diélectriques couramment utilisés dans les circuits imprimés sont comprises entre 3,5 et 5,5, mais cette valeur dépend strictement de la fréquence du signal et diminue à mesure qu’elle augmente.
Lors de la conception d’un circuit imprimé, il est préférable de choisir des matériaux ayant une faible valeur Dk, qui peuvent donc servir d’isolant pour les pistes de cuivre et les plans d’alimentation. En outre, le matériau choisi doit être capable d’avoir une valeur Dk aussi constante que possible, aussi bien lorsque la fréquence de fonctionnement du signal varie que pendant toute la durée de vie prévue pour le circuit.
Pour garantir un fonctionnement fiable et stable du circuit dans le temps, il est recommandé d’utiliser une constante diélectrique qui demeure stable sur une large gamme de fréquences. L’image 2 montre l’évolution de Dk lorsque la fréquence varie dans un matériau diélectrique spécialement conçu pour les hautes fréquences.
Image 2 : Courbes de fréquence Dk pour certains matériaux de la série RO4000 (Source : Rogers Corporation)
Facteur de perte
Ce paramètre est représenté par le symbole Df et est également appelé tangente de perte (Tan δ). Il indique avec quelle facilité un matériau présente des pertes de puissance. Plus le facteur de perte est faible, moins le matériau diélectrique perd de puissance.
La tangente de perte des matériaux diélectriques couramment utilisés pour la fabrication des circuits imprimés est comprise entre 0,02 et 0,001 et sa valeur augmente avec la fréquence. Particulièrement significatif dans les circuits analogiques, ce paramètre prend une importance relative dans les circuits numériques, du moins aux fréquences inférieures à 1 GHz.
Propriétés thermiques
Lorsque des courants électriques parcourent un circuit imprimé, celui-ci produit une certaine quantité de chaleur qui provoque une contrainte thermique sur les matériaux diélectriques, les pistes et les composants. À terme, la chaleur peut entraîner la dilatation des matériaux, ce qui provoque des fissures, des dommages aux pistes et aux soudures, voire une panne.
Pour choisir un matériau diélectrique, il est essentiel d’évaluer sa conductivité thermique, c’est-à-dire sa capacité à dissiper la chaleur en toute sécurité sans compromettre le fonctionnement du circuit imprimé. Il existe d’autres propriétés thermiques importantes : le taux de dilatation thermique du matériau, également appelé coefficient de dilatation thermique (CTE), la température de transition vitreuse (Tg) et la température de décomposition (Td).
Tg
La température de transition vitreuse (Tg) indique le niveau de température au-delà duquel un matériau change de propriétés lorsqu’il est soumis à la chaleur. Plus précisément, un matériau diélectrique pour circuits imprimés se ramollit lorsqu’il est exposé à des températures supérieures à Tg, puis se durcit à nouveau lorsque la chaleur est évacuée et que la température baisse.
Le FR-4, couramment utilisé dans les circuits imprimés (image 3), a une Tg comprise entre 130 et 140 °C. Il existe également des matériaux à Tg moyenne (150-160 °C) et à Tg élevée (supérieure à 170 °C). Plus la Tg d’un matériau est élevée, plus celui-ci est résistant aux hautes températures.
Image 3 : le FR-4 est un matériau standard pour les circuits imprimés
Td
La température de décomposition (Td) indique le niveau de température au-delà duquel le matériau diélectrique commence à se décomposer. Contrairement à la température de transition vitreuse (où le matériau est capable de retrouver ses propriétés initiales lorsque la température repasse en dessous), les effets sont permanents et non réversibles dans le cas de la température de décomposition.
Les températures atteintes lors des opérations de soudure étant comprises entre 200°C et 250°C environ, il est préférable de choisir un matériau dont la Tg est inférieure à cette plage et supérieure à la Td.
CTE
Le coefficient de dilatation thermique (CTE) indique le taux de dilatation d’un matériau soumis à des températures supérieures à sa Tg. Le CTE se mesure en parties par million (ppm) et se situe généralement entre 10 et 20 ppm le long des axes X et Y. Il s’agit d’une valeur de référence. Sa valeur doit être la plus basse possible afin d’éviter que le matériau du circuit imprimé ne se dilate dans le plan X, Y.
K
La conductivité thermique (k) exprime la capacité d’un matériau à véhiculer la chaleur. Dans la plupart des matériaux diélectriques, la conductivité thermique (mesurée en W/mK ou en W/m°C) est généralement comprise entre 0,3 et 6 W/mK. À l’inverse, le cuivre a une conductivité thermique de 386 W/m°C. C’est donc un matériau capable de véhiculer la chaleur plus rapidement qu’un matériau diélectrique.
Propriétés chimiques
En général, il est préférable de choisir des matériaux qui absorbent peu l’humidité et présentent une résistance chimique élevée, notamment au chlorure de méthylène. Il est également très important de choisir des matériaux aux propriétés ignifuges, capables de résister aux flammes pendant plusieurs secondes (par exemple, le FR-4, un matériau aux propriétés ignifuges de niveau 4).
L’absorption d’humidité exprime la capacité d’un matériau diélectrique à résister à l’immersion dans l’eau. La plupart des matériaux diélectriques utilisés dans la fabrication des circuits imprimés ont une valeur d’absorption d’humidité comprise entre 0,01 % et 0,20 %.
La résistance à l’absorption du chlorure de méthylène est plutôt un indice de la résistance chimique d’un matériau diélectrique. Cette propriété, mesurée par l’indice MCR (Methylene Chloride Resistance, résistance au chlorure de méthylène), présente généralement des valeurs comprises entre 0,01% et 0,20% pour la plupart des matériaux.
Choix des matériaux
Examinons maintenant les principaux matériaux pouvant servir de diélectriques dans la fabrication d’un circuit imprimé.
FR-4
Le FR-4, sigle correspondant à Flame Retardant Level 4 (retardateur de flamme de niveau 4), est aujourd’hui le matériau standard employé dans la fabrication des circuits imprimés. Ce matériau est constitué d’un stratifié époxy renforcé par des fibres de verre tissées. Il possède des propriétés ignifuges et respecte la norme UL94V-0.
Étant le matériau le plus largement utilisé dans la fabrication de circuits imprimés, le FR-4 est particulièrement adapté aux cycles de production en grande série. Toutefois, ce matériau présente des limites dans les applications de signaux à haute fréquence et ne permet pas de dissiper de grandes quantités de chaleur. En outre, la constante diélectrique du FR-4 n’est pas constante en fonction de la fréquence, ce qui peut entraîner des problèmes d’intégrité du signal.
DPI/PPO
Les stratifiés hydrocarbonés thermodurcissables (DPI et PPO) offrent une bonne stabilité mécanique, une grande durabilité et sont faciles à fabriquer. Outre une excellente résistance chimique, ces matériaux indéformables présentent une résistance élevée à la température et constituent une solution idéale pour toutes les applications nécessitant une résistance à la chaleur jusqu’à 110 °C et une résistance élevée aux chocs dans une large gamme de températures. L’absorption d’humidité est très faible et le matériau supporte également le contact direct avec l’eau bouillante.
PTFE
Les matériaux en polytétrafluoroéthylène (PTFE) peuvent tout à fait remplacer le FR-4, plus courant. Obtenu avec un composé de carbone et de fluor, le PTFE présente une température de transition vitreuse élevée (environ 120 ˚C).
Le PTFE possède d’excellentes propriétés diélectriques qui le restent même à des fréquences très élevées, ce qui en fait une solution appropriée pour les applications à grande vitesse, à haute fréquence, à micro-ondes et à haute puissance RF. La perte de signal est très faible, l’ajustement des impédances est simplifié et les caractéristiques du signal sont excellentes.
Polyimides
Les matériaux polyimides sont généralement utilisés pour fabriquer les couches souples des circuits imprimés souples et semi-rigides, car ils peuvent être facilement pliés et tournés autour des composants sans compromettre le fonctionnement et les performances du circuit. Le polyimide offre également une excellente résistance aux hautes températures, une bonne dissipation de la chaleur, une résistance à l’humidité et aux produits chimiques.
CEM-1, CEM-2 et CEM-3
Les matériaux CEM sont une famille de matériaux pour circuits imprimés répertoriés par la NEMA qui comprend trois catégories de matériaux : CEM-1, CEM-2 et CEM-3.
Compte tenu de son faible coût, le CEM-1 est le matériau le plus largement utilisé pour la fabrication de circuits imprimés simple face. Il s’agit d’un matériau composite composé d’une combinaison de cellulose (papier) et d’une seule couche de fibre de verre entrelacée de résine époxy (FR-4). Ce matériau ne permet pas l’application de trous métallisés traversants et ne peut donc être utilisé que pour les circuits imprimés à une seule couche. Tout comme le FR-4, le CEM-1 est ignifuge, mais ses caractéristiques mécaniques sont moindres en raison de la plus grande fragilité du matériau.
L’image 4 montre un circuit imprimé fabriqué avec du CEM-1 (notez la couleur blanchâtre caractéristique de ce matériau).
Image 4 : exemple de CEM-1 pour circuit imprimé
Les matériaux CEM-2 offrent des températures de transition vitreuse plus élevées que les matériaux CEM-1. Ils sont composés d’une partie centrale à isolation de papier cellulose et d’une surface en fibre de verre tissée. Les matériaux CEM-3 sont des composés époxy-verre largement utilisés pour les circuits imprimés double face à trous métallisés.
Rogers
Les matériaux Rogers, produits par la société Rogers Corporation, offrent plusieurs avantages par rapport aux matériaux diélectriques traditionnels, notamment de plus faibles pertes de puissance et pertes diélectriques, une meilleure gestion thermique, une large gamme de valeurs de constante diélectrique (d’un minimum d’environ 2,55 à un maximum supérieur à 10), un meilleur ajustement des impédances. Bien que leur coût soit plus élevé, les matériaux Rogers sont largement utilisés dans les circuits imprimés destinés aux applications RF et haute fréquence.
Circuits imprimés à partie centrale métallique
Les circuits imprimés à partie centrale métallique, également appelés MCPCB, contiennent un cœur métallique ayant pour fonction d’évacuer la chaleur des composants les plus chauds. La partie centrale est généralement composée d’une plaque métallique d’une certaine épaisseur fabriquée en aluminium ou en alliages spéciaux. L’aluminium représente généralement la solution la plus économique si l’on tient compte de la conductivité thermique, de la rigidité et du coût. Les parties centrales ont généralement une épaisseur comprise entre 0,76 et 3,18 mm (entre 30 et 125 mils), mais il est possible d’en fabriquer de plus épaisses ou de plus fines.
La principale différence entre un circuit imprimé FR-4 et un MCPCB est le matériau diélectrique à haute conductivité thermique qui se trouve dans ce dernier et qui agit comme un pont thermique entre les composants du circuit intégré et la plaque métallique de support. L’image 5 montre un exemple de MCPCB destiné aux applications d’éclairage électrique.
Image 5 : exemple de MCPCB
Critères de sélection
La sélection du matériau diélectrique le plus approprié dépend des besoins de l’application visée, notamment les niveaux de tension et de courant, la fréquence maximale des signaux, la puissance développée par les composants, la quantité de chaleur à dissiper.
Durant cette étape, les concepteurs peuvent s’aider des lignes directrices suivantes :
- Utilisez des matériaux ayant des constantes diélectriques très proches. Si vous utilisez des matériaux ayant des valeurs Dk très différentes, vous pouvez rencontrer des problèmes d’intégrité du signal et obtenir un comportement anormal lorsque la fréquence varie.
- Utilisez des matériaux ayant des coefficients de dilatation thermique (CTE) très proches. Sinon, les matériaux risquent de se dilater à des rythmes différents ou dans des proportions différentes par rapport aux deux axes X et Y, ce qui peut endommager le circuit imprimé et affecter la valeur Dk.
- Assurez-vous que les matériaux diélectriques présentent des surfaces parfaitement lisses afin de ne pas modifier la valeur Dk.
- Recherchez toujours le meilleur compromis entre le coût et les performances. Le FR-4 est un excellent matériau pour de nombreuses applications, alors que dans certains cas précis (comme les applications RF haute fréquence, les LED de puissance ou les circuits HDI, pour n’en citer que quelques-uns), il est nécessaire de se tourner vers des matériaux plus performants, malgré leur coût plus élevé.
Choisir le bon matériau diélectrique, c’est essentiel pour produire des circuits imprimés fiables, capables de conserver leurs performances au fil du temps et en fonction des variations électriques et thermiques imposées aux circuits.
Conclusion
Les performances fournies par les circuits imprimés, ainsi que leur fiabilité et leur longévité, dépendent fortement des types de matériaux diélectriques utilisés pour leur fabrication. Les propriétés thermiques, électriques, chimiques et mécaniques sont des paramètres essentiels pour choisir un matériau diélectrique. Par conséquent, il convient d’en tenir compte dès la phase de conception afin de garantir un fonctionnement optimal des circuits imprimés et des dispositifs électroniques dans lesquels ils sont utilisés.
15.12.2022