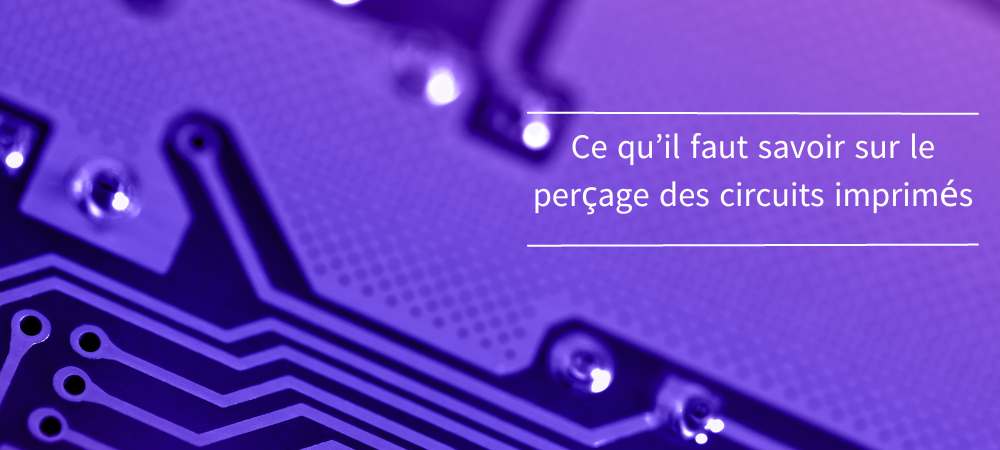
Le perçage intervient après le laminage du circuit. Ses caractéristiques sont déterminées par le fichier de perçage par commande numérique du circuit imprimé. Il consiste à créer des trous dans le circuit imprimé pour placer les composants, créer les via et assurer les liaisons électriques entre les différentes couches. Il s’agit sans doute de l’étape la plus onéreuse et la plus chronophage dans la fabrication d’un circuit imprimé. Il est essentiel de la réaliser avec une grande précision, car la moindre erreur peut avoir de graves conséquences sur la qualité du circuit imprimé.
La criticité et la complexité du perçage des circuits imprimés se sont accrues avec la miniaturisation et la densification des composants électroniques. Pour les circuits imprimés à une ou deux faces, le perçage est réalisé immédiatement après leur découpe, tandis que pour les circuits imprimés multicouches, le perçage est effectué après le laminage.
et recevez un devis pour votre projet de PCBA dans les 10 prochaines minutes !
Les machines de perçage spécifiques à commande numérique sont conçues pour décoder et appliquer les données contenues dans les fichiers de perçage Gerber et ODB, notamment les coordonnées (X, Y) et la taille des trous (diamètre et profondeur). Cette étape est très lente, car les trous sont percés les uns à la suite des autres. Pour accélérer le processus, plusieurs panneaux de circuit imprimé sont percés en même temps.
Après cette étape, il est nécessaire de procéder à un ébavurage pour éliminer les excès de cuivre autour des bords des trous. Différentes méthodes peuvent s’employer, par exemple le polissage et le nettoyage au plasma. Pour garantir une métallisation uniforme et sans défaut, il est essentiel que chaque trou soit complètement exempt de débris.
Techniques de perçage
Il existe plusieurs méthodes pour réaliser des trous sur un circuit imprimé, notamment la gravure électrochimique, le perçage, la découpe laser et la perforation. Lorsque la densité de trous traversants augmente et que leur taille diminue, il est nécessaire de recourir à des techniques de perçage qui permettent de former des trous de petite taille avec une grande précision et une répétabilité élevées.
Perçage mécanique
Pour obtenir un perçage précis à haute vitesse, il faut utiliser un mandrin pneumatique qui tourne à des vitesses proches de 300 000 tr/min. Pour garantir cette précision essentielle à la réalisation des petits trous, les vibrations du mandrin doivent rester dans une plage de 10 µm. Afin de placer les trous avec exactitude sur le circuit imprimé, la perceuse est montée sur un système servomécanique pouvant se déplacer le long des axes X et Y. Un actionneur spécifique permet par ailleurs de commander le mouvement du circuit imprimé le long de l’axe Z. Le perçage à grande vitesse offre des avantages considérables. En effet, il laisse des parois propres et lisses, ce qui est essentiel pour la qualité de la métallisation.
Le perçage mécanique est une méthode très efficace pour obtenir des trous de qualité sans aspect conique aux extrémités. Cette méthode est également plus rapide que d’autres, ce qui permet d’accélérer la fabrication des circuits imprimés. Toutefois, il peut arriver que la mèche se casse lorsque les trous sont trop petits. De plus, chaque trou doit faire l’objet d’un ébavurage ultérieur pour éliminer tout excès de cuivre laissé par le perçage.
L’image 1 présente une machine à commande numérique spécialement conçue pour le perçage mécanique.
Image 1 : Machine à commande numérique adaptée au perçage mécanique
Perçage au laser
Les perceuses laser sont des outils sophistiqués permettant de percer des circuits imprimés avec une très grande précision. Elles sont capables de réaliser des trous et des microvia d’un diamètre inférieur à 200 μm, ce qui leur permet de créer des trous extrêmement petits, tels que les microvia et les via borgnes. La taille des trous est déterminée par l’ouverture du faisceau laser, tandis que la profondeur est déterminée par la durée d’exposition. Un jeu spécifique de lentilles concentre l’énergie du faisceau laser à l’endroit exact où le circuit imprimé doit être percé. En outre, le perçage laser présente l’avantage d’éviter les risques de délamination.
Le perçage laser est un procédé qui consiste à créer des trous dans un circuit imprimé au moyen d’un faisceau laser à haute densité. Il s’agit d’une technique très précise pouvant être utilisée avec divers matériaux. Bien qu’il existe différents types de lasers, les deux plus courants sont les lasers à ultraviolet (UV) et à dioxyde de carbone (CO2).
Le perçage laser est très pratique pour réaliser l’ablation d’une large gamme de matériaux, car elle permet de former des trous de petit diamètre impossible à obtenir par perçage mécanique conventionnel. Il s’agit également d’une technique sans contact. Elle ne nécessite donc pas de procéder à une sélection complexe d’outils de perçage comme c’est le cas avec le processus de perçage mécanique.
Le procédé de perçage au laser présente néanmoins un certain nombre de difficultés, notamment pour obtenir un trou d’une profondeur précise en l’absence de couche d’arrêt métallique. De plus, le laser peut produire un effet de brûlure sur les bords du trou, ce qui donne un aspect sombre.
À l’instar du perçage mécanique, le perçage au laser permet de superposer plusieurs panneaux, selon leur épaisseur. Les technologies modernes de perçage au laser permettent de réaliser des trous traversants dont le diamètre est compris entre 50 et 150 µm.
L’image 2 illustre quelques trous obtenus avec une machine de perçage au laser pour circuit imprimé. Il est remarquable de constater la précision de ces trous, ainsi que l’absence d’imperfection et de résidu, malgré leur taille très réduite.
Image 2 : Exemples de trous et de microvia réalisés par technologie laser (Source : Hitachi High-Tech)
Nouvelles techniques de perçage
Ces dernières années, le nombre de trous à percer sur les circuits imprimés a connu une croissance considérable. Alors qu’une carte de circuit imprimé d’un téléphone portable standard peut nécessiter entre 30 000 et 50 000 trous, une carte qui utilise des composants de type boîtier à puce peut nécessiter plus de 300 000 trous. Par conséquent, pour produire des circuits imprimés à une cadence élevée, il est nécessaire de recourir à des techniques de perçage appropriées.
La technologie d’exposition directe (également appelée « imagerie directe ») est une nouvelle méthode de perçage de trous dans les circuits imprimés. Cette technique innovante s’appuie sur le traitement des images et permet d’améliorer la précision et la vitesse de perçage. Elle consiste à créer une image numérique du circuit imprimé et à la convertir en une carte des positions servant de référence pour le laser afin de percer les trous. Cette méthode améliore la précision de l’alignement des trous. Elle se sert du traitement numérique des images pour tenir compte des variations de taille, de forme et de déformation qui peuvent affecter la carte ou le panneau. L’image 3 illustre un équipement moderne qui utilise la méthode d’exposition directe pour la fabrication de circuits imprimés.
Image 3 : Équipement utilisant l’exposition directe pour la fabrication de circuits imprimés
Types de trous
Lorsque l’on parle de perçage de trous dans un circuit imprimé, il est important de tenir compte de deux facteurs. Le premier est le rapport longueur sur largeur qui a une influence directe sur la possibilité d’effectuer un cuivrage à l’intérieur des trous. Plus le diamètre du trou diminue et sa profondeur augmente, plus ce processus est compliqué. Le rapport longueur sur largeur se définit comme le rapport entre la profondeur du trou et son diamètre. Il a généralement une valeur standard de 10:1 pour les trous traversants et de 0,75: 1 pour les microvia. Il est important que cette valeur reste très faible afin de simplifier le perçage et d’éviter une usure excessive de la mèche lors du perçage mécanique.
Le deuxième point à prendre en compte est la distance entre le bord du trou et la zone de cuivre la plus proche sur le circuit imprimé. Il peut s’agir d’une piste, d’un point de contact ou d’autres éléments. Pour éviter tout dysfonctionnement du circuit, cette distance doit être d’au moins 8 mils (0,2 mm), ce qui correspond à la valeur minimale acceptée.
Les différents types de trous pouvant être percés sur un circuit imprimé sont généralement classés en trois catégories principales :
- Les petits trous métallisés permettent de transmettre des signaux électriques, l’alimentation et la masse à travers les différentes couches du circuit imprimé. Selon le type, il existe différents types de via, notamment les via traversants qui traversent complètement plusieurs couches du circuit imprimé, les via enterrés qui se trouvent complètement à l’intérieur de l’empilage du circuit imprimé sans atteindre les deux couches de surface, les via borgnes qui partent d’une couche de surface et s’arrêtent sur une couche interne et les microvia dont la taille est inférieure à celle des précédents trous et qui ne peuvent être réalisés que par perçage laser.
- Trous pour le passage de composants à trous traversants, comme les connecteurs, les interrupteurs et autres composants mécaniques qui nécessitent un assemblage robuste garanti par un boîtier à trous traversants. Ce type de boîtier est particulièrement adapté aux composants de puissance, tels que les grandes résistances, les condensateurs, les amplificateurs opérationnels et les régulateurs de tension qui sont traversés par de forts courants et peuvent générer une quantité considérable de chaleur.
- Trous mécaniques. Les trous mécaniques sont des ouvertures créées pour l’assemblage mécanique de divers composants, tels que des boîtiers, des ventilateurs, des dissipateurs thermiques et autres. Ils permettent également un meilleur alignement des circuits imprimés avec les machines de fabrication automatisée.
Étapes de perçage
Le perçage d’un circuit imprimé peut se décomposer en quatre étapes distinctes décrites ci-après.
1 - Trous de positionnement
Les trous de positionnement sont des points de référence essentiels pour la fabrication et le test des circuits imprimés. Avant de procéder au perçage, la plaque de support, le substrat et la feuille d’aluminium sont disposés sur le banc de perçage à grande vitesse, en les plaçant du bas vers le haut. En fonction des caractéristiques de production, des trous de positionnement d’un diamètre de quelques millimètres sont percés sur le bord de la carte.
2 - Insertion des broches
Pour accroître la productivité, plusieurs cartes ou panneaux sont empilés les uns sur les autres avant de procéder au perçage. Pour éviter tout déplacement lors du perçage, les panneaux sont fixés sur la table de la perceuse à l’aide des broches appropriées.
3 - Perçage des trous
Le perçage est effectué par des machines automatiques à commande numérique. Il suffit donc de charger les fichiers contenant les paramètres de perçage convertis en commandes FAO pour réaliser les trous correspondants. Le perçage mécanique est l’une des méthodes les plus courantes pour percer des trous dans les circuits imprimés. Les trous traversants, qu’ils soient métallisés ou non, peuvent être percés grâce à la mèche qui tourne à grande vitesse. Avant de commencer le perçage, une plaque de support est placée sous le panneau à percer afin de protéger la surface de la perceuse, tandis qu’une feuille d’aluminium est posée sur le dessus pour aplanir les trous dans la feuille de cuivre et éviter que la mèche ne chauffe trop.
4 - Inspection des trous
Après avoir percé les trous, il est nécessaire de vérifier avec soin la position et l’ouverture de chacun d’entre eux. Une fois que cette étape a été achevée et que vous vous êtes assuré qu’il n’y a pas de problèmes tels que des trous supplémentaires, des trous manquants ou un écart dans la position d’un trou, le circuit imprimé peut passer à l’étape de fabrication suivante.
10.05.2023