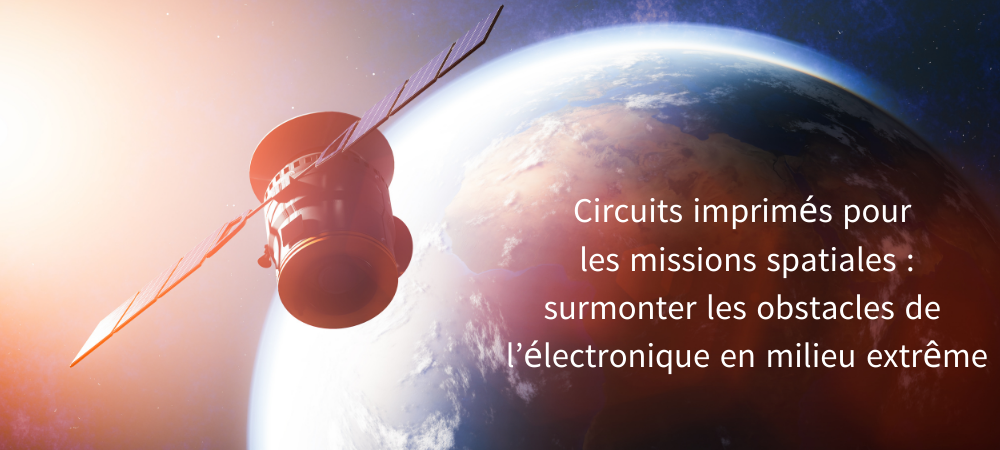
Pour la poursuite de l’exploration spatiale, il est devenu essentiel de disposer de systèmes électroniques capables de résister aux conditions extrêmes que l’on retrouve dans l’espace. Les circuits imprimés prévus pour ces missions doivent absolument assurer la fiabilité et l’efficacité des systèmes électroniques embarqués. Ils doivent endurer des contraintes mécaniques, des rayonnements, le vide spatial ainsi que des températures extrêmement variables, soulevant des problématiques particulières pour les ingénieurs et les concepteurs. Dans cet article, nous allons présenter toute la complexité qui se présente pour concevoir des circuits imprimés adaptés au domaine spatial. Nous allons également passer en revue les stratégies mises en œuvre par les ingénieurs pour surmonter les difficultés.
et recevez un devis pour votre projet de PCBA dans les 10 prochaines minutes !
Quels sont les défis posés par les circuits imprimés prévus pour les missions spatiales ?
Les circuits imprimés de ce type doivent impérativement résister à des conditions hostiles comme les rayonnements intenses, les fortes vibrations et les très grands écarts de température. Réalisés avec une précision méticuleuse, utilisant des matériaux de la plus haute qualité et des procédés de fabrication de pointe, ils offrent des performances et une fiabilité absolument hors du commun.
Températures extrêmes
Dans l’espace, nous sommes confrontés à de très grandes variations de température. Que ce soit pour les satellites, les sondes spatiales ou les véhicules d’exploration planétaire, ces équipements doivent endurer des écarts thermiques considérables, de -200 °C à l’abri du rayonnement solaire à plus de 200 °C sous l’exposition directe aux rayons du soleil. Il est donc indispensable de mettre en œuvre des solutions de gestion thermique de haute technologie, avec des matériaux à faible coefficient de dilatation thermique.
Pour ce genre de situations, les ingénieurs privilégient souvent les circuits imprimés en céramique en raison de leur faible coefficient de dilatation qui leur confère un excellent comportement face aux variations de température. Ce type de matériau garantit une stabilité et une fiabilité sans faille malgré les températures extrêmes rencontrées dans le vide spatial.
Rayonnements ionisants
Les rayonnements ionisants provenant du soleil et de l’espace cosmique peuvent sérieusement compromettre le fonctionnement des composants électroniques. Les circuits imprimés, en particulier, peuvent voir leurs performances diminuer à cause de ces rayonnements. Pour pallier ce problème, les circuits imprimés en milieu spatial sont conçus avec des matériaux résistant aux rayonnements, comme des substrats en céramique et des revêtements protecteurs spéciaux.
Contraintes mécaniques
Les circuits imprimés sont soumis à de violentes contraintes mécaniques au moment du lancement ou du déploiement des appareils spatiaux. Les vibrations engendrées lors de la mise en orbite et le déploiement d’éléments tels que les panneaux solaires peuvent produire des dommages structuraux. Afin de limiter ces risques et de protéger les composants électroniques, les concepteurs prévoient des solutions d’absorption des chocs comme des circuits flexibles et des revêtements conformes.
Généralement en polyimide, les circuits imprimés flexibles améliorent l’absorption des chocs comparativement aux versions rigides, Les revêtements conformes, pour leur part, fournissent une protection supplémentaire contre les dommages physiques lors des différentes phases de lancement et de déploiement. De plus, un soin particulier est apporté à la topologie des circuits imprimés afin de répartir uniformément les contraintes mécaniques.
Dégazage
Le dégazage est un vice de fabrication où l’air emprisonné dans un circuit imprimé se libère, formant des cavités ou des bulles susceptibles d’affecter son fonctionnement. Ce phénomène peut survenir lors du brasage manuel ou par refusion. Il est exacerbé sous l’effet du vide intense de l’espace. La plupart du temps, le dégazage des circuits imprimés résulte d’un choix de matériaux inadéquat ou à d’erreurs dans le processus de fabrication. Dans le vide quasi absolu de l’espace, où air et fluides sont inexistants, un problème comme le dégazage (illustré à l’image 1) peut contaminer des composants optiques délicats, tels que les caméras.
Image 1 : défaut de dégazage sur un joint de soudure après une soudure manuelle (Source : YouTube)
Les matériaux sélectionnés pour la fabrication de circuits imprimés destinés aux missions spatiales présentent de faibles caractéristiques de dégazage. Des composites tels que le polyimide et le PTFE (téflon) sont privilégiés pour leurs excellentes propriétés en la matière, limitant ainsi les risques de contamination dans le vide spatial et assurant la fiabilité des systèmes électroniques sur le long terme.
Contraintes liées à l’encombrement et à la masse
Les contraintes liées à l’encombrement et à la masse sur les vaisseaux spatiaux imposent de concevoir des systèmes électroniques compacts et légers. Il faut trouver un juste équilibre entre compacité et fonctionnalité en optimisant l’architecture des circuits de manière à exploiter au mieux l’espace disponible. En recourant à des circuits imprimés multicouches, à des méthodes de miniaturisation sophistiquées et à des techniques de packaging 3D, les ingénieurs parviennent à préserver les performances essentielles, même sous l’effet de contraintes sévères.
Le montage en surface (SMT) et d’autres procédés avancés de miniaturisation facilitent la mise au point de composants électroniques plus compacts et plus légers. Ces innovations trouvent une solution au casse-tête posé par les limites physiques. Elles exploitent les avantages des solutions de packaging 3D, telles que les boîtiers système (SiP) ou le montage direct des puces (COB) qui densifient l’intégration des différentes fonctions.
Substrats spéciaux pour les applications spatiales
Ces circuits nécessitent des substrats spéciaux, capables de résister aux conditions extrêmes que l’on rencontre dans l’espace. Les substrats les plus couramment employés sont présentés ci-après.
Céramique
Des matériaux comme l’alumine (Al2O3) et le nitrure d’aluminium (AlN) sont souvent utilisés. Leur faible coefficient de dilatation thermique assure une stabilité remarquable dans des conditions de températures extrêmes. En outre, ces céramiques conduisent bien la chaleur et favorisent donc la dissipation thermique. Les substrats céramiques se distinguent également par leur résistance aux rayonnements, faisant d’eux une solution de choix pour les applications spatiales.
Vitrocéramique
Les vitrocéramiques, dont les céramiques cuites à basse température (LTCC), sont reconnues pour leurs caractéristiques électriques, leur faible dilatation thermique et leur excellente conductivité thermique. Les LTCC s’adaptent particulièrement bien aux dispositifs nécessitant d’intégrer une multitude de composants dans un espace restreint.
Polyimide
Le polyimide est un polymère qui se distingue par sa souplesse et sa légèreté. Les substrats de polyimide sont particulièrement adaptés aux circuits imprimés flexibles, capables de supporter les contraintes mécaniques appliquées lors du lancement et de la mise en service des équipements. Offrant aussi une bonne stabilité thermique, ces substrats résistent sans problème aux variations de température. Cependant, ils peuvent se montrer moins adéquats pour les applications fortement exposées aux rayonnements.
Matériaux résistants aux rayonnements
Afin de contrer les effets nocifs des rayonnements, qui peuvent altérer ou endommager les composants électroniques sur le long terme, on intègre des matériaux spécifiques dans la conception des circuits imprimés destinés aux missions spatiales. L’époxy résistant aux rayonnements est un exemple de matériau spécialement conçu pour résister aux dommages causés par les rayonnements ionisants. Il conserve ses propriétés électriques et mécaniques, même exposé aux rayonnements. Les stratifiés époxy résistant aux rayonnements accroissent considérablement la durabilité et la fiabilité des circuits imprimés dans l’espace.
De plus, on privilégie les alliages de cuivre réputés pour leur grande résistance aux rayonnements. Des alliages comme le cuivre-tungstène (CuW) et le cuivre-molybdène (CuMo) se distinguent par leur résistance à la dégradation et à la fragilisation provoquées par les rayonnements. Ces matériaux permettent de préserver les caractéristiques électriques et l’intégrité structurelle des circuits imprimés, même dans des conditions de forte exposition aux rayonnements.
Feuilles de cuivre
Les circuits imprimés destinés aux missions spatiales intègrent des feuilles de cuivre pour assurer leur fonctionnement. Elles servent de couches conductrices, essentielles à la transmission des signaux électriques. Pour garantir la transmission du signal et minimiser les pertes, les circuits comportent des feuilles de cuivre de très haute performance.
Ces feuilles de cuivre se distinguent par des caractéristiques de premier plan. Leur grande conductivité thermique permet de dissiper la chaleur de façon efficace. Cet aspect est particulièrement important dans l’espace où les équipements doivent gérer efficacement un niveau élevé de rayonnement généré par les composants eux-mêmes. Outre leur faible affaiblissement d’insertion, ces feuilles réduisent la distorsion et l’affaiblissement du signal, assurant une transmission fiable, à haute fréquence.
Circuits imprimés à partie centrale métallique
Les circuits imprimés à partie centrale métallique, souvent composés d’un noyau en cuivre ou en aluminium enveloppé d’une couche diélectrique, sont adaptés aux applications nécessitant une bonne dissipation thermique, laquelle est assurée par une excellente conductivité thermique. Cette caractéristique est d’autant plus importante dans l’espace où la régulation de la chaleur représente un défi considérable.
Série RO4000 de Rogers
La série RO4000 de Rogers, qui inclut les modèles RO4350B et RO4003C, constitue une sélection de matériaux stratifiés adaptés aux fréquences élevées, notamment aux environnements micro-ondes et radiofréquence (RF). À haute fréquence, leur efficacité électrique est remarquable, ce qui en fait une solution de choix pour les missions spatiales nécessitant des capacités RF et micro-ondes.
PTFE (Téflon)
Le polytétrafluoroéthylène, plus communément appelé Téflon, se distingue par sa faible constante diélectrique et sa faible perte diélectrique, ce qui le rend idéal pour les applications haute fréquence. Sa résistance exceptionnelle aux agents chimiques et son faible dégazage en font une excellente solution pour les environnements proches du vide absolu comme l’espace.
FR-4 à Tg élevée
Le FR-4, matériau standard composé de fibre de verre et de résine époxy, se décline également dans des versions à haute température de transition vitreuse (Tg) qui offrent une meilleure résistance aux températures élevées. Sa stabilité thermique étant supérieure à celle du FR-4 standard, il est envisageable de l’utiliser pour certaines applications spatiales.
Traitements de surface
Soigneusement choisis pour les circuits imprimés destinés à l’espace, les traitements de surface protègent de l’oxydation et assurent la fiabilité des points de soudure. On utilise souvent de l’argent chimique ou de l’or chimique (image 2).
Le traitement à l’argent chimique se distingue par son excellente conductivité et sa résistance accrue à la corrosion. Il forme une couche de protection efficace sur les pistes en cuivre, préservant ainsi leur intégrité contre l’oxydation et assurant la fiabilité des raccordements électriques. En raison de son intégrité de signal supérieure et de son faible affaiblissement d’insertion, l’argent chimique est spécialement adapté aux applications haute fréquence.
Quant à l’or chimique, il fournit une surface de qualité supérieure, avec une fiabilité et une durabilité accrues des soudures. La capacité de l’or à résister à l’oxydation garantit une soudabilité de premier ordre et une stabilité sur le long terme. De plus, grâce à sa conductivité électrique élevée, ce procédé est fréquemment employé pour des applications nécessitant des connexions d’une fiabilité sans faille.
Image 2 : circuit imprimé comportant un traitement à l’or chimique (Source : Linkedin)
Conclusion
La création de circuits imprimés adaptés aux missions spatiales constitue une tâche complexe et exigeante qui requiert une connaissance pointue des conditions extrêmes de l’espace. Face aux températures extrêmes, aux rayonnements intenses, au vide spatial, aux contraintes mécaniques et aux limites strictes imposées en matière d’encombrement et de masse, les ingénieurs doivent redoubler d’inventivité. Pour ce faire, ils utilisent des matériaux de dernière génération, des systèmes de gestion thermique performants, des composants résistants aux rayonnements et des techniques de conception extrêmement précises. Ces mesures leur permettent de concevoir des systèmes électroniques adaptés aux conditions extrêmes que l’on retrouve dans l’espace.
11.01.2024