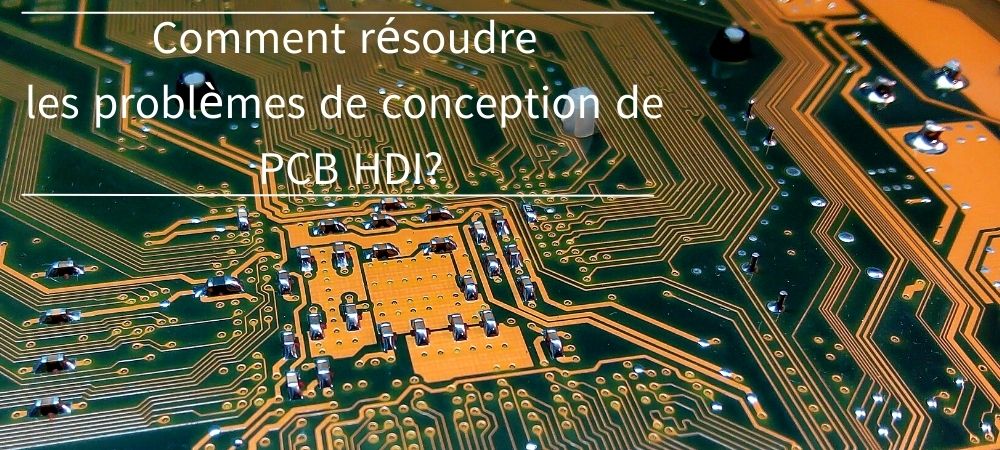
Les circuits imprimés à haute densité d’interconnexion (High Density Interconnect, HDI) comptent parmi les technologies les plus avancées du secteur. Ils permettent de répondre à la demande croissante de circuits imprimés toujours plus compacts et efficaces. Comparés aux circuits imprimés standard, les circuits imprimés HDI offrent un plus grand nombre de connexions électriques par unité de surface, et ce, en respectant les contraintes suivantes :
- largeur et distance entre les pistes inférieures à 100 µm
- taille de via inférieure à 150 µm
- points de capture de taille inférieure à 400 µm
- densité des points de capture supérieure à 20 points/cm2
et recevez un devis pour votre projet de PCBA dans les 10 prochaines minutes !
La technologie HDI permet aux concepteurs de réduire considérablement la taille des circuits, tout en garantissant les exigences en matière de fiabilité et d’intégrité du signal. Les défis que doivent relever les ingénieurs sont particulièrement difficiles, principalement en ce qui concerne le processus de fabrication. En effet, lorsque la largeur des pistes est inférieure à 65 µm (environ 2,559 mils), il n’est plus possible de recourir au procédé traditionnel de gravure, mais il convient d’adopter des procédés de production particuliers, ce qui entraîne une forte hausse des coûts.
Lorsqu’il est réalisé dans les règles de l’art, le routage HDI permet non seulement de réduire considérablement l’espace occupé sur le circuit imprimé, mais aussi de résoudre de nombreux problèmes liés aux interférences électromagnétiques (EMI), réduisant ainsi les coûts globaux du projet, les tests à effectuer et les délais de commercialisation.
Microvia
Les microvia constituent un élément essentiel de la technologie HDI. Il s’agit d’un trou borgne d’un diamètre inférieur à 150 µm et dont le diamètre du point de contact est inférieur à 350 µm, généralement obtenu par un procédé de perçage au laser. En appliquant un faisceau laser d’un diamètre caractéristique de 20 µm (1 mil) sur un substrat en cuivre ou en fibre de verre, il est en effet possible d’obtenir des microvia extrêmement petits. Dans les circuits imprimés HDI, les microvia remplacent les trous traversants classiques, permettant ainsi de connecter plusieurs couches sur une surface très réduite, avec une augmentation considérable de la densité des interconnexions. Compte tenu de leur faible profondeur, les microvias sont pratiquement insensibles aux problèmes liés aux différences de valeurs du coefficient de dilatation thermique entre le substrat et le matériau conducteur. L’image 1 montre l’agrandissement d’un microvia unique et borgne, obtenu par perforation laser.
Image 1 : exemple de microvia (source : Micron Laser)
Dans les cartes de circuits imprimés HDI, les microvia remplacent complètement les via traditionnels, améliorant la densité de routage dans les couches internes et diminuant le nombre de couches nécessaires à la transmission des différents signaux. Afin de réduire le nombre de trous traversants et le nombre de couches internes, des mesures particulières sont adoptées au niveau de l’empilage. Les plans de masse et les plans d’alimentation, sur lesquels on trouve un plus grand nombre de vias, occupent normalement les premières couches de l’empilage (par exemple, la deuxième et la troisième couche), tandis que les deux couches extérieures sont réservées au placement des composants. Le plan de masse est essentiel pour assurer un retour de courant à faible impédance, tandis que le placement des signaux sur les couches internes permet de réduire les phénomènes de diaphonie. Pour concevoir un circuit imprimé HDI, il est essentiel de placer correctement les microvia afin d’assurer une meilleure intégrité du signal et une meilleure topologie des couches les plus internes.
Contrairement aux trous de via qui entraînent la formation de charges capacitives susceptibles de dégrader la qualité du signal à haute fréquence, les microvia présentent une plus faible quantité de charges parasites en raison de leur taille réduite.
Conception des circuits HDI
Les microvia, qui peuvent être de type borgne ou enterré, sont fabriqués d’une manière différente des via traditionnels. Alors que ces derniers sont obtenus en perçant l’empilage déjà complet avec toutes les couches superposées, les microvia sont réalisés par un perçage laser effectué sur chaque couche individuelle avant de composer l’empilage. Les microvia permettent de relier plusieurs couches en utilisant des trous et des points de contact les plus petits qui soient. Ils sont donc particulièrement adaptés aux boîtiers à haut niveau d’intégration tels que les matrices à billes (BGA) dont le pas peut atteindre 0,8 mm ou moins.
Les boîtiers BGA, de plus en plus courants, comportent un grand nombre de broches (1 500 et plus) et présentent donc une densité extrême. Bien qu’ils constituent une solution relativement peu coûteuse à la demande croissante de miniaturisation des circuits, les boîtiers BGA compliquent considérablement le routage des circuits imprimés. Le nombre de couches peut alors augmenter, ce qui entraîne des problèmes d’intégrité du signal et une hausse des coûts.
Les pistes transportant des signaux à haute vitesse doivent être aussi courtes que possible, notamment le retour à la masse. Le bon placement des microvias permet de circonscrire le parcours du signal à une zone plus restreinte, réduisant ainsi les risques d’EMI. Les microvia permettent d’atteindre une densité de connexion très élevée en utilisant un nombre inférieur de couches, puisque la taille des pistes et des microvia est beaucoup plus faible. Les principaux avantages offerts par la technologie HDI sont les suivants :
- Densité de pistes plus élevée permettant de réduire la taille et la masse des circuits imprimés.
- Intégrité du signal de meilleure qualité. La longueur réduite des pistes et la haute densité des connexions permettent de réduire la consommation d’énergie et d’améliorer l’intégrité du signal. La transmission du signal est plus rapide, avec une réduction significative des pertes de signal et des délais de propagation.
- Réduction des coûts. Par le biais d’une conception minutieuse, la technologie HDI permet de réduire les coûts grâce à une utilisation moindre des matériaux nécessaires aux couches.
- Simplification du routage grâce à des pistes de courte longueur.
- Réduction des interférences inductives et capacitives (EMI).
- Possibilité d’utiliser des composants avec des boîtiers ultra-compacts.
- Réduction des délais de mise sur le marché. L’utilisation d’une plus petite quantité de matériaux se traduit par une réduction des délais de production et de mise sur le marché. Sur les circuits imprimés HDI, les composants sont relativement plus faciles à placer et les excellentes caractéristiques électriques réduisent le temps nécessaire aux tests et au dépannage.
L’image 2 montre un exemple de circuit imprimé réalisé avec la technologie HDI : notez la compacité et la haute densité des composants et des connexions qui s’y trouvent.
Image 2 : exemple de circuit imprimé HDI (source : Cadence)
En ce qui concerne les normes applicables à la conception des circuits imprimés HDI, la norme IPC-2226 (« Sectional Design Standard for High Density Interconnect Printed Boards ») constitue la référence et remplace l’ancienne norme IPC-2315 (« Design Guide for High Density Interconnects & Microvias »). En plus de fournir des directives pour le choix des microvia, la norme définit six types différents d’empilages pouvant être utilisés dans la conception de circuits imprimés HDI. Les différents empilages sont répartis en catégories, de I à VI, à la complexité et aux coûts croissants. Chacune de ces catégories définit le nombre et la position de chaque couche dans l’empilage HDI et fournit des recommandations concernant le matériau à utiliser pour le substrat. Notez également comment les microvia, tout comme dans le mode simple présenté dans l’image 1, peuvent se superposer (occuper la même position) sur plusieurs couches adjacentes. Dans ce cas, nous parlons de « microvia empilés ». L’image 3 en donne un exemple : les microvia superposés occupent les couches 1, 2 et 3 d’un circuit imprimé multicouche hypothétique composé de 14 couches.
Image 3 : microvia superposés (source : Cadence)
Applications
En utilisant la technologie HDI, les concepteurs de circuits imprimés peuvent compter sur une plus grande flexibilité, puisqu’ils peuvent placer davantage de composants sur les deux couches extérieures du circuit imprimé. La solution innovante du microvia permet de placer un plus grand nombre de composants à des distances très courtes, réduisant ainsi le temps de transmission du signal, le retard de transmission qui en résulte et les pertes de puissance.
La possibilité d’utiliser des composants avec des boîtiers à pas très étroit augmente encore la densité des composants, ce qui permet d’obtenir des circuits imprimés dont les surfaces et les épaisseurs sont beaucoup plus petites que dans les circuits imprimés traditionnels. La compacité, la haute fréquence et la vitesse élevée du signal sont autant de facteurs qui ouvrent la voie à des applications telles que les dispositifs à écran tactile, les téléphones mobiles, les systèmes de communication 5G, les appareils photo numériques, les ordinateurs portables, les dispositifs portables et les appareils électromédicaux. La technologie HDI est également largement utilisée dans le secteur de l’électronique grand public, avec des applications importantes telles que les consoles de jeux, les lecteurs multimédias, les appareils de réalité virtuelle et de réalité augmentée.
12.02.2022