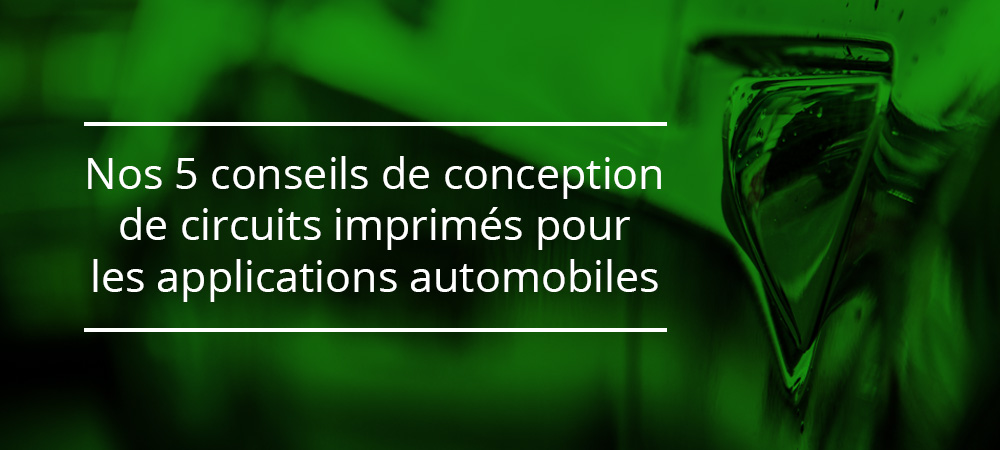
La conception de circuits imprimés automobiles est sans aucun doute l'un des défis les plus difficiles pour les ingénieurs en électronique. Les systèmes électroniques embarqués doivent en effet fonctionner dans les conditions les plus exigeantes, tout en garantissant une grande fiabilité et une longue durée de vie. Le poids, la taille et le coût de la solution doivent être maîtrisés, avec des circuits capables de gérer des signaux analogiques, numériques ou mixtes. Le nombre de couches, le routage des pistes, la terminaison du signal et la désignation des chemins du courant ne sont que quelques-uns des choix auxquels le concepteur de PCB doit faire face. Il convient également de souligner que les circuits imprimés pour l’automobile doivent être conçus dès les étapes initiales pour répondre aux exigences de compatibilité électromagnétique (EMI) et se conformer aux normes automobiles internationales telles que l'AECQ100, et l'ISO / TS 16949 qui est basée sur les normes automobiles ISO 9001.
Types de circuits imprimés dans le secteur automobile
Afin de répondre aux exigences strictes d'espace, de poids et de coût, l'industrie automobile utilise différents types de PCB qui diffèrent les uns des autres à la fois par la structure et par le type de matériau ou de substrat utilisé. Les principaux types de PCB pour les applications automobiles sont les suivants :
- PCB rigides : ce sont les PCB traditionnels, non flexibles et usuellement fabriqués en FR4. Les applications comprennent les moniteurs d'affichage et les écrans de caméra de recul;
- PCB Flex : ces cartes de circuits imprimés sont construites avec des substrats plastiques haute performance et flexibles ; elles utilisent des matériaux tels que des films polyamide, polyétheréthercétone (Peek) ou polyester transparent. L'avantage de ces cartes est qu'elles peuvent être tordues et pliées. Les applications sont nombreuses, en particulier là où l'espace est limité ou de forme irrégulière, et comprennent la connexion d'écrans, de panneaux de commande et d'interrupteurs d’éclairage ;
- PCB flexibles rigides : ils correspondent à une combinaison des deux types de PCB mentionnés ci-dessus et offrent donc les avantages des deux. Les circuits imprimés flex-rigides sont beaucoup utilisés, par exemple, dans les systèmes d'éclairage;
- PCB LED : l'utilisation de plus en plus massive de LED haute puissance et haute luminosité nécessite des PCB avec une excellente dissipation thermique, généralement fabriqués avec un substrat métallique tel que l'aluminium. Les PCB de ce type sont utilisés dans les clignotants de voiture, les phares et les feux de freinage;
- PCB HDI : HDI, acronyme de High Density Interconnect, indique des cartes de circuits imprimés à haute densité de connexions électriques par unité de surface. Ces PCB ont des espaces et des lignes plus fins, de petits vias, des pastilles de capture et une densité de pastilles de connexion plus élevée. Largement utilisés dans les systèmes d'info-divertissement, les PCB HDI aident à améliorer la qualité du câblage, réduisant le poids et la taille de la solution.
Sélection des substrats
Les circuits imprimés automobiles, avant d'être installés sur le véhicule, doivent passer une série de tests rigoureux, tels que le cyclage thermique, le choc thermique et l'humidité de la température. Le choix du matériau de support le plus adapté à l'application spécifique est donc fondamental. Les PCB de cuivre lourds, par exemple, utilisent des couches avec un cuivre plus épais, afin de mieux résister aux conditions critiques telles que les températures élevées, les fréquences et les variations de courant. Alors que les cartes normales ont une épaisseur comprise entre 25 µm et 50 µm, les PCB en cuivre lourd ont une épaisseur comprise entre 150 µm et 200 µm. Ces PCB sont utilisés dans les systèmes destinés à la sécurité et à la signalisation. Les PCB à substrat céramique, obtenus par combustion à haute température d'alumine et de nitrure d'aluminium, peuvent résister à des températures extrêmement élevées et sont donc utilisés dans le compartiment moteur. Les circuits imprimés à noyau métallique, où le noyau métallique est une couche de base en alliage d'aluminium, sont particulièrement adaptés aux applications de transfert de chaleur. La couche de base en aluminium, en fait, agit comme un dissipateur thermique, fournissant une isolation électrique et une conductivité thermique. Un exemple d'application est les systèmes de freinage antiblocage (ABS). Enfin, les PCB en PTFE, à base de matériau polytétrafluoroéthylène, sont particulièrement adaptés aux applications haute fréquence, telles que les systèmes de sécurité, anticollision et radar.
5 conseils de conception de circuits imprimés
Les PCB utilisés dans l'industrie automobile nécessitent non seulement la sélection d'un matériau approprié, mais également une conception soignée qui garantit à la fois le respect des exigences imposées par les normes applicables et la capacité à ne pas rencontrer de problèmes pendant la production. Il est donc recommandé de suivre quelques règles de base, dont cinq (les plus importantes) seront maintenant décrites.
et recevez un devis pour votre projet de PCBA dans les 10 prochaines minutes !
1. Placement et orientation des composants
Le placement et l'orientation des composants jouent un rôle fondamental dans la détermination des performances, de la fiabilité et de la fabricabilité d'une carte. La règle générale est de placer des composants similaires dans la même direction, facilitant ainsi à la fois le routage du PCB et le processus de soudage lors de l'assemblage. Lorsque la soudure à la vague est utilisée (comme illustré à l'image 1), les composants doivent être orientés dans la direction parallèle à la direction de la vague afin d'éviter les ponts de soudure ou les circuits ouverts.
Image 1: Orientation suggérée avec soudure à la vague.
Les composants SMD doivent être placés du même côté de la carte, tandis que tous les composants à trou traversant (TH) doivent être placés sur la face supérieure de la carte afin d'optimiser la procédure d'assemblage.
2 - Acheminement du signal
Les composants qui absorbent plus de 10 mW ou conduisent plus de 10 mA doivent nécessiter une gestion thermique appropriée, ainsi que des composants de gestion de l'alimentation qui doivent utiliser des plans de masse ou des plans d'alimentation pour le flux de chaleur. Les plans d'alimentation et de masse doivent être placés sur des couches internes, si possible de manières symétrique et centrée, évitant ainsi la courbure de la carte. Les signaux sensibles (tels que l'horloge) doivent être protégés des sources de bruit avec des plans et être contrôlés par impédance. Les connexions entre couches conduisant des courants élevés doivent être réalisées à l'aide de deux à quatre vias par couche; l'utilisation de plusieurs vias permet en effet d'augmenter la fiabilité, de réduire les pertes résistives et inductives et d'améliorer la conductivité thermique.
En ce qui concerne le routage, la recommandation générale est d'utiliser les pistes les plus courtes et les plus droites possibles. En ce qui concerne les circuits imprimés à double couche, si le routage force les pistes à être horizontales d'un côté, assurez-vous que les pistes sont disposées verticalement sur le côté opposé. Dans le cas des PCB multicouches, des pistes horizontales doivent être alternées avec des pistes verticales. La largeur de piste peut être déterminée en prenant la norme IPC comme référence. Normalement, une largeur comprise entre 10 et 20 mils est utilisée pour les pistes qui conduisent des courants de 10 à 20 mA, tandis qu'une largeur comprise entre 5 et 8 mils est adéquate pour les pistes qui conduisent moins de 10 mA.
3 - Commande et composants distincts
Les composants plus grands (généralement les plus importants) doivent être placés en premier, suivis des composants plus petits. De plus, les composants analogiques ou mixtes doivent être placés sur une zone dédiée du PCB, les séparant des composants numériques. La hauteur des composants est également importante : les composants hauts (tels que les condensateurs électrolytiques) ne doivent pas être placés à côté de composants plus petits, car cela évite des soudures mal connectées. La règle de base est de maintenir un angle de vue supérieur à 45 degrés, car cela facilite l'inspection manuelle des joints de soudure.
4 - Gestion thermique
La première étape consiste à identifier les composants qui dissipent la plus grande quantité de chaleur, à la recherche des indices de résistance thermique indiqués dans la fiche technique. La chaleur est transférée des composants aux couches de cuivre et, par conséquent, la gestion thermique idéale se produit lorsque la carte entière est à la même température. L'épaisseur des pistes, le nombre de couches, la continuité des chemins thermiques et la surface de la carte sont autant de facteurs qui influencent la température de fonctionnement des composants.
Pour améliorer la conductivité thermique, des vias thermiques et des plans en cuivre sont généralement utilisés. En utilisant plusieurs plans de masse et de puissance connectés directement aux sources de chaleur via des vias thermiques, la température de fonctionnement peut être considérablement réduite. S'il y a plusieurs composants générant une grande quantité de chaleur, mieux vaut les répartir uniformément sur la carte, évitant ainsi la formation de points chauds. Si, par contre, la génération de chaleur est concentrée dans quelques composants, il est préférable de les placer au centre de la carte, de sorte que la chaleur puisse être dissipée uniformément dans toutes les directions. L'image 2 montre l'analyse thermique réalisée sur la carte Raspberry Pi 4. Comme on peut le voir, la chaleur est concentrée à proximité du SoC, le cœur de la carte, placé non par hasard dans une position centrale.
Image 2 : Analyse thermique du Raspberry Pi 4
5 - Application des règles de la RDC
La vérification des règles de conception doit être effectuée afin d'identifier les problèmes ou les erreurs qui ne pourraient pas correspondre aux exigences de fabrication courantes, aux exigences électriques à grande vitesse ou à d'autres exigences pour votre application particulière. Il est fortement suggéré d'exécuter DRC (Design Rule Checking) tout au long du processus de conception, plutôt qu'à la fin, identifiant ainsi les problèmes de conception potentiels à un stade précoce et les résolvant rapidement.