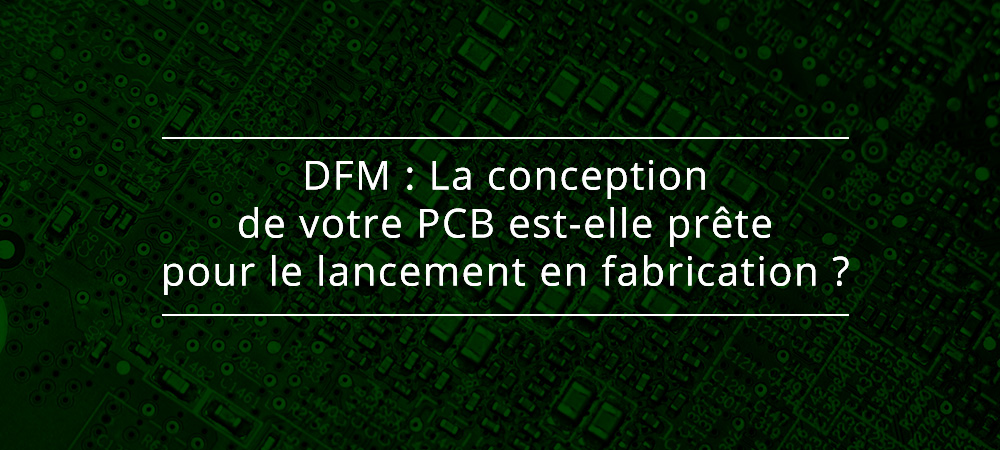
Le terme DFM (Design For Manufacturing) fait référence au processus par lequel un produit est conçu dans le but précis de simplifier sa fabrication, créant un meilleur produit à moindre coût. Idéalement, DFM devrait déjà être appliqué au cours des étapes initiales du projet et devrait impliquer toute l'équipe de développement de produits et pas seulement les concepteurs de matériel. Au fur et à mesure que le projet progresse à travers les différentes étapes du cycle de vie du produit, chaque modification du projet d'origine prend un poids et un coût croissants, parfois elle peut même devenir particulièrement complexe à mettre en œuvre.
D'autre part, l'application du DFM lors des étapes initiales du développement du PCB permet d'effectuer rapidement toute modification éventuelle, au coût le plus bas possible et en conservant les performances d'origine du produit. La technologie joue un rôle clé dans de nombreux aspects de nos vies. Smartphones, montres connectées, appareils électroménagers, voitures connectées, tout utilise une technologie et une connectivité intelligentes.
Ces applications et d'autres nécessitent des circuits imprimés d'une complexité croissante, avec la demande de les produire au moindre coût, dans les plus brefs délais et avec un niveau de qualité élevé.
Avantages DFM
La fabrication de PCB étant divisée en plusieurs étapes, il est nécessaire d'être certain, bien à l'avance, qu'une carte n'est affectée par aucun problème de conception pour la fabrication (DFM) qui pourrait causer de problèmes sérieux.
Pendant la phase de développement, les concepteurs doivent se soumettre à des contraintes électriques, telles que la valeur des tensions et courants impliqués, la consommation électrique et la gestion thermique. Dans le monde réel, cependant, d'autres facteurs entrent en jeu, comme la précision ou la tolérance des machines de fabrication de circuits imprimés et les caractéristiques des matériaux utilisés. DFM est précisément le procédé qui permet d'organiser la disposition du PCB dans le but d'être certain qu'il peut être produit. Un exemple est représenté par la bague annulaire, ou la zone de pastille de cuivre qui reste après avoir percé un trou à l'intérieur.
La taille de la bague est mesurée du bord du plot au bord du trou et représente un paramètre fondamental dans la conception du PCB, puisque le placage déposé dessus permet la connexion électrique entre un côté du trou et l'autre. Dans le cas des cartes multicouches, les anneaux annulaires doivent être alignés avec un recouvrement suffisant pour permettre la connexion entre différentes couches.
L'alignement parfait n'existe que sur le papier: même les perceuses laser les plus modernes ne peuvent pas avoir une précision égale à 100%. Le procédé DFM garantit que la largeur de la bague annulaire est telle qu'elle permet un léger désalignement entre les couches sans compromettre la connexion électrique.
Les principaux avantages du DFM appliqué à la conception et à la fabrication de PCB sont les suivants :
- une meilleure qualité du produit : DFM réduit le nombre de modifications nécessaires pour adapter la conception originale aux processus de fabrication et aux usines de PCB, modifications qui peuvent potentiellement compromettre la qualité du produit ;
- réduction du temps de mise sur le marché : le processus de fabrication est divisé en plusieurs étapes, chacune pouvant être à l'origine d'erreurs potentielles. DFM aide à réduire les retards causés par les produits défectueux, les erreurs et le temps passé à vérifier les revues et la documentation des projets ;
- réduction des coûts : DFM permet aux concepteurs de PCB de concevoir des cartes qui peuvent être facilement produites même avec de grands volumes de production. Les coûts inférieurs découlent également du nombre plus faible d'erreurs détectées pendant le processus de fabrication des PCB.
DFM contre RDC
Les concepteurs de circuits imprimés exécutent souvent une procédure appelée vérification des règles de conception (DRC). À ce stade, on peut se demander si, après avoir mené avec succès la RDC, il est nécessaire de réaliser également le DFM.
La réponse est oui, car les deux procédures sont en fait différentes, et les deux sont nécessaires pour démarrer avec succès le projet d'un PCB vers la production. La RDC est en fait un processus d'analyse automatique qui compare le projet aux règles imposées par la fonderie. Ces règles définissent les exigences physiques minimales pour le PCB, les couches et les réseaux, qui peuvent avoir des impacts sur les performances du système. Le but de la RDC est de détecter tout écart ou erreur.
Le DFM, quant à lui, identifie tous les aspects susceptibles de créer des problèmes pendant le processus de fabrication des PCB. Si le processus DRV détecte une erreur, elle sera présente sur chaque copie du tableau. Les problèmes rencontrés par DFM, en revanche, ne peuvent se produire que sur certaines unités de la carte et même après une longue période de production.
Comment appliquer les principes DFM aux PCBs
Même si les normes de fabrication des PCB peuvent être différentes pour chaque fabricant, certaines règles générales DFM doivent être respectées avant d'appliquer tout processus de fabrication. Afin de déclarer une conception de PCB prête pour la fabrication, certains principes de base DFM doivent être appliqués. Voici une liste des directives les plus pertinentes :
- espacement entre les composants : les composants trop proches les uns des autres sur le circuit imprimé peuvent poser des problèmes aux systèmes automatiques utilisés pour l'assemblage, tels que les machines pick-and-place, rendant la retouche de la conception plutôt problématique. Il en va de même pour les connecteurs, qui doivent être correctement positionnés afin de simplifier les connexions de la carte avec l'extérieur ;
- positionnement et rotation des composants : la manière dont les composants sont positionnés sur le PCB peut affecter le processus de soudage, en particulier si les composants sont disposés de manière irrégulière ou inégale. Tous les composants similaires doivent être orientés dans la même direction, en s'assurant que tous les composants sont correctement soudés lorsqu'ils sont passés dans un four de soudage ;
- taille de PAD incorrecte : des tailles de PAD incorrectes peuvent provoquer un échauffement irrégulier de la plage d'accueil pendant le soudage par refusion. Ceci, à son tour, peut provoquer le détachement partiel du composant du PCB, phénomène connu sous le nom de "tombstoning" ;
- pièges à acide : le routage des traces de PCB doit éviter les angles aigus, ce qui peut causer de graves problèmes lors du nettoyage des produits chimiques de gravure de la carte, entraînant une réduction de l'épaisseur des traces elles-mêmes. En s'assurant que les angles entre les pistes sont toujours inférieurs à 90 degrés, évite les traces de délaminage de la carte après la fabrication du PCB ;
- optimisation des trous : de nombreuses conceptions de PCB utilisent trop de tailles de trous différentes, un aspect à éviter afin de réduire les coûts de production des PCB ;
- absence de masque de soudure entre les plots : ce qui peut produire des ponts de soudure et potentiellement court-circuiter deux plots qui ne doivent pas être connectés. Par conséquent, vérifiez toujours soigneusement que chaque pastille a un masque de soudure suffisant pour garantir le jeu requis ;
- sérigraphie sur pastilles : le chevauchement, même partiel, de la sérigraphie sur les pastilles crée des problèmes lors du soudage, avec des conséquences potentiellement désastreuses sur le long terme. La figure 3 montre un exemple de cette condition qu'il faut absolument éviter ;
Image 1 : Exemple de sérigraphie sur PADs
- contrôle en boucle ouverte : cette condition se produit généralement lorsque le projet d'origine est retravaillé pour apporter des modifications. En fait, connecter un nouveau réseau sans supprimer l'existant crée généralement une boucle sans fin ;
- validation des fichiers utilisés pour le projet : bien qu'il s'agisse d'un format de fichier assez ancien, Gerber est toujours utilisé dans de nombreux projets PCB. Bien que répandus, les fichiers Gerber peuvent présenter des problèmes lorsque le projet est traduit en objet physique. Par exemple, l'utilisation de fichiers Gerber nécessite un fichier séparé pour chaque couche du PCB: cela signifie que vous devez garder une trace de nombreux fichiers en évitant qu'ils soient mélangés ou confondus les uns avec les autres.
et recevez un devis pour votre projet de PCBA dans les 10 prochaines minutes !