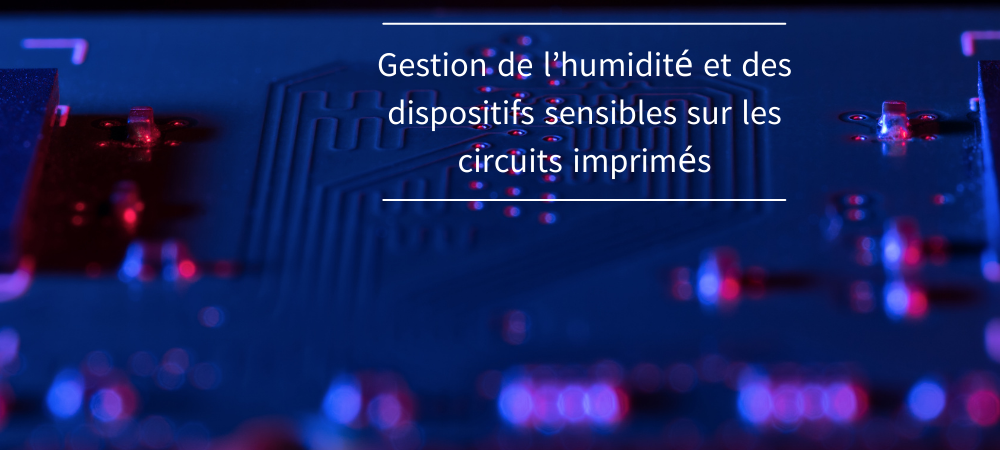
Ces dernières années, les dispositifs électroniques connaissent une évolution continue qui se traduit par un encombrement toujours plus réduit, accompagné de performances et de vitesses toujours plus élevées. Les circuits imprimés plus petits, plus complexes et plus denses nécessitent une protection particulière des composants électroniques afin d’éviter les éventuels problèmes de corrosion en cas d’exposition à l’humidité et aux contaminants. En effet, ces éléments peuvent dégrader les performances du circuit, ou provoquer des courts-circuits et des pannes.
L’humidité, par exemple, peut provoquer différents types de défaillances sur un circuit imprimé, en fonction des composants ou des pistes conductrices qui entrent en contact avec elle. Parmi les problèmes les plus courants liés à l’humidité figurent les retards dans la transmission des signaux, ainsi que l’allongement des délais de propagation. Au-delà d’un certain seuil, le circuit peut s’arrêter complètement de fonctionner.
et recevez un devis pour votre projet de PCBA dans les 10 prochaines minutes !
Les dispositifs électroniques peuvent subir des dommages internes s’ils ne sont pas manipulés et conservés conformément aux normes spécifiques du secteur. Les composants munis de matrices à billes (BGA) et de boîtiers à puce sont particulièrement sensibles à l’humidité. Pire encore, les dommages subis par ces composants peuvent être difficiles à détecter lors d’une inspection. L’image 1 montre un exemple de dommages provoqués par l’humidité sur le circuit imprimé.
Image 1 : dommages provoqués par l’humidité sur le circuit imprimé
Composants sensibles et dispositifs MSD
Quelques gouttes d’eau peuvent suffire à endommager irrémédiablement un circuit imprimé, mais une quantité d’humidité encore plus faible peut s’avérer dangereuse. L’humidité est problématique non seulement lorsque le circuit fonctionne, mais aussi pendant le stockage des cartes, avant leur installation.
La résistivité de l’eau pure ou déminéralisée est d’environ 1,8 x 107 Ω x m à 25 °C, ce qui en fait un bien meilleur isolant qu’un conducteur électrique. En fait, l’eau qui entre en contact avec un circuit imprimé contient des sels, des minéraux, des chlorures, des sulfates et des carbonates dissous. Ces composés rendent l’eau très conductrice, ce qui représente une menace pour l’intégrité du circuit imprimé, en entraînant des courts-circuits et des processus de corrosion.
La condensation, qui se forme lorsque la surface du circuit imprimé est plus froide que son environnement, constitue une menace encore plus grave. La condensation peut se former aussi bien sur les faces extérieures du carton qu’à l’intérieur des boîtiers de composants. Le choix de ces derniers doit donc tenir compte de ce facteur.
Les composants électroniques particulièrement sensibles à l’humidité, identifiés par le sigle MSD (Moisture Sensitive Device, dispositif sensible à l’humidité), nécessitent une protection particulière aussi bien pendant l’assemblage des circuits imprimés que lors du stockage des cartes finies dans l’entrepôt. Lorsque le coefficient d’absorption d’humidité d’un composant est trop élevé, il existe un risque d’endommager la carte, les composants ou les connexions électriques entre eux. Si l’humidité est excessive lors du soudage, le matériau utilisé pour le substrat de la carte risque de s’endommager. Il est difficile de détecter ces types de défauts qui ont tendance à se manifester uniquement sur le produit final ou après un certain temps d’utilisation, ce qui réduit considérablement la possibilité d’y remédier.
Les risques les plus importants se produisent pendant le processus de soudage par refusion, lorsque les composants MSD sont placés sur le circuit imprimé. Même les variations importantes et soudaines de la température ambiante peuvent provoquer une dilatation ou une fissuration du boîtier. L’un des effets très courants de l’humidité est le décollement interne du matériau utilisé pour construire le circuit imprimé. Le FR-4 ordinaire, par exemple, est un matériau fortement hygroscopique. Il est donc particulièrement sensible à l’humidité ambiante, quelles que soient les méthodes de conditionnement. L’humidité non éliminée lors du soudage se transforme en vapeur, ce qui provoque du décollement et des microcavités dans les zones les plus sensibles de la carte.
Normes IPC pour les dispositifs sensibles
Les premières normes relatives au contrôle de l’humidité dans les circuits imprimés ont été publiées en 2010 par l’IPC, l’organisme anciennement appelé Institute for Printed Circuits. Si l’on respecte ces normes, les cartes électroniques peuvent durer plus longtemps, à condition d’employer des techniques adéquates pour disperser l’humidité. En outre, les cartes protégées par un revêtement approprié peuvent conserver leur aptitude au soudage pendant de plus longues durées, à condition de prendre des mesures pour empêcher l’humidité d’y pénétrer.
Selon les mêmes lignes directrices, l’étuvage est un procédé pratique pour éliminer l’humidité des circuits imprimés s’il n’a pas été possible de l’empêcher de pénétrer au préalable. Toutefois, l’étuvage entraîne inévitablement une augmentation des coûts, un allongement des délais de production et une baisse de l’aptitude à la soudure. Il convient donc d’éviter le plus possible de recourir à cette méthode et de privilégier des techniques de maintenance préventive lors de l’assemblage et du rangement des circuits imprimés.
Il existe actuellement deux normes publiées par l’ICP qui peuvent orienter les fabricants d’électronique dans la gestion des composants sensibles à l’humidité : IPC/JEDEC J-STD-020E et IPC/JEDEC J-STD-033D.
IPC/JEDEC J-STD-020E
Cette norme propose un système de classification permettant de déterminer la qualification initiale de la fiabilité. Une fois l’identification effectuée, les fabricants peuvent emballer, stocker et manipuler les dispositifs de manière à réduire les dommages thermiques et mécaniques pendant le processus de refusion.
IPC/JEDEC J-STD-033D
Cette norme définit une méthodologie pour la manipulation, l’emballage et l’expédition des dispositifs MSD, ainsi que des procédures visant à accroître le rendement et à limiter la dégradation de la fiabilité.
Les deux normes subdivisent les niveaux de sensibilité à l’humidité (MSL, moisture sensitivity level) en classes numérotées de 1 à 6 en fonction de leur sensibilité aux dommages causés par l’humidité. Les niveaux les plus élevés s’appliquent aux composants sensibles qui offrent une plus grande résistance à l’humidité. Il est notamment indiqué, pour chaque classe, la durée pendant laquelle le composant peut rester en dehors d’un système de protection contre l’humidité avant de devoir subir un étuvage afin d’éliminer l’humidité absorbée.
Comme le montre le tableau de l’image 2, le niveau MSL 6 correspond aux composants les plus sensibles qui doivent subir un étuvage avant même d’être utilisés.
Image 2 : Les classes MSL (source : TI)
Les circuits imprimés, ainsi que les cartes finies, doivent plutôt être stockés et expédiés dans des sacs de protection spéciaux (qui assurent généralement une protection contre les décharges électrostatiques et l’humidité), appelés sacs MBB (Moisture Barrier Bag, sac de protection contre l’humidité). L’image 3 présente un exemple de ce type de sac.
Image 3 : sacs de protection MBB
Protection des composants et des circuits imprimés
Pour protéger les circuits imprimés de l’humidité, la meilleure approche consiste à intervenir de façon adaptée dans toutes les phases de fabrication des circuits imprimés, ainsi que dans les phases ultérieures de stockage ou d’expédition.
Fabrication
Lors de la fabrication d’un circuit imprimé, le laminage doit s’effectuer dans un environnement à température et humidité contrôlées, en utilisant, si nécessaire, des agents de séchage appropriés. Pour éviter toute contamination entre les différents composants, le personnel doit toujours porter des gants propres lors du démarrage d’un nouveau lot de production. Au cours du processus de laminage des circuits imprimés, les différentes couches qui composent le circuit imprimé sont positionnées et collées de manière à former une seule carte. Dans cette phase, certains fabricants appliquent un effet de vide à basse pression pour éviter la formation d’interstices susceptibles de retenir l’humidité à l’intérieur.
Une autre technique courante consiste à utiliser des plaques de cuivre avec une structure maillée, afin de créer des liens plus forts et d’empêcher que l’humidité ne se déplace entre les différentes couches du circuit imprimé. Toutefois, il convient de noter que ces structures peuvent avoir une incidence sur les caractéristiques électriques de la carte et que leur emploi doit donc être bien réfléchi.
Après la fabrication du circuit imprimé, il est possible d’appliquer une finition de surface à des fins de protection. De cette manière, les propriétés du circuit imprimé sont préservées jusqu’à la prochaine étape d’assemblage.
Assemblage
Pour éviter que l’humidité ambiante ne nuise au circuit imprimé, il est recommandé de souder les composants à des températures élevées avec un taux d’humidité inférieur à 0,1 %, ou à des températures basses avec un taux d’humidité inférieur à 0,2 %. La soudure à haute température est réalisée autour de 260 °C, tandis que la soudure à basse température se fait autour de 230 °C.
Après avoir terminé l’assemblage des composants sur la carte, il est courant et efficace d’éliminer l’humidité par étuvage. Toutefois, il faut veiller à ne pas dépasser le coefficient de dilatation thermique du matériau utilisé pour le circuit imprimé afin d’éviter les risques de décollement ou de fissures.
La meilleure manière de protéger un circuit imprimé assemblé consiste à appliquer l’un des nombreux types de revêtement conforme disponibles. Les revêtements conformes protègent non seulement de l’humidité, mais aussi des fluides, des contaminants et même des rayons ultraviolets.
Les revêtements conformes consistent en un mince film polymère appliqué sur le circuit imprimé afin de protéger le circuit et ses composants de l’environnement et de la corrosion. Le film a généralement une épaisseur comprise entre 25 et 250 µm et peut épouser la forme de la carte et de ses composants. Il recouvre et protège de la corrosion les points de soudure, les bornes et les broches des dispositifs électroniques, les pistes à découvert et les autres zones de cuivre, ce qui prolonge la durée de vie du circuit imprimé.
L’image 4 montre les phénomènes de corrosion causés par l’humidité ou d’autres agents agressifs sur le circuit imprimé en l’absence de revêtement conforme (image de gauche) et avec un revêtement conforme (image de droite). Ces revêtements forment une couche uniforme qui recouvre les surfaces de la carte. Ils confèrent une excellente résistance à l’humidité, aux huiles, à la saleté, aux empreintes digitales et à d’autres contaminants environnementaux. Les revêtements conformes assurent une protection contre divers agents corrosifs tels que l’humidité, l’eau, le brouillard salin, la brume et le soufre.
Image 4 : Carte avec et sans revêtement conforme (source : 3M)
L’encapsulation, qui consiste à insérer entièrement un circuit imprimé assemblé à l’intérieur d’un boîtier de protection, peut également s’avérer très efficace, à condition que le boîtier permette à l’humidité piégée de s’échapper vers l’extérieur, par exemple par des évents.
Une autre solution que l’encapsulation intégrale consiste à recouvrir partiellement la carte au moyen de résines époxy appropriées qui ne couvrent que certaines zones du circuit imprimé particulièrement sensibles à l’humidité.
Stockage
Les circuits imprimés (assemblés ou non) doivent être stockés dans les sacs de protection MBB prévus à cet effet et non dans des pochettes qui n’assurent qu’une protection contre les décharges électrostatiques.
Les concepteurs doivent également respecter les lignes directrices énoncées dans les normes IPC qui fournissent des recommandations utiles pour l’emballage et le stockage des appareils électroniques, en minimisant les risques de propagation de l’humidité.
Si vous n’appliquez pas de protection contre l’humidité sur les cartes, vous risquez de provoquer des défaillances des circuits imprimés ainsi que des coûts inutiles de réparation ou de remplacement. Cependant, il est possible de réduire considérablement les risques que l’humidité et d’autres agents similaires nuisent au fonctionnement et à la fiabilité du circuit imprimé en appliquant les techniques susmentionnées lors de la fabrication, de l’assemblage, de l’emballage ou du stockage.
Conclusion
La tendance actuelle à la miniaturisation et à la densification des composants place les concepteurs devant de nouveaux défis pour assurer aux circuits imprimés un niveau de protection adéquat contre l’humidité et les agents corrosifs. Les dispositifs sensibles à l’humidité (MSD) sont particulièrement sensibles à l’humidité, ce qui peut les empêcher de fonctionner. Dans cet article, nous avons décrit les principales techniques qui permettent d’assurer une protection efficace et durable des circuits électroniques lorsqu’on les applique pendant les phases de production, d’assemblage, de stockage et d’expédition.
20.03.2023