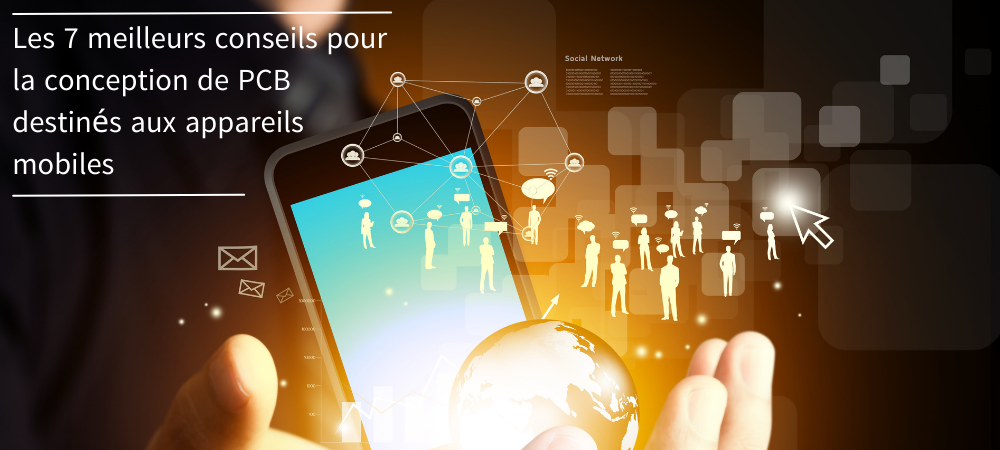
La multiplication progressive des fonctionnalités intégrées dans les appareils mobiles de dernière génération impose des exigences de plus en plus strictes en matière de conception de circuits imprimés. La connectivité Wi-Fi et Bluetooth, la prise en charge des réseaux mobiles 4G et 5G, et l’intégration d’un nombre croissant de capteurs représentent des défis technologiques sans précédent pour les concepteurs électroniques. Les appareils mobiles, notamment les smartphones, se caractérisent par un accroissement des capacités d’intelligence, de la miniaturisation et de la polyvalence. Ils nécessitent des circuits imprimés de plus en plus complexes, capables de satisfaire ces besoins. Le marché tend vers des appareils de plus en plus fins, dont l’épaisseur est généralement inférieure à un centimètre.
et recevez un devis pour votre projet de PCBA dans les 10 prochaines minutes !
Défis techniques
Le développement des smartphones actuels nécessite d’utiliser des circuits imprimés multicouches (composés de 10 couches ou plus) pour la réalisation de la carte mère et un ou plusieurs circuits imprimés ayant un nombre réduit de couches pour les cartes auxiliaires, éventuellement réalisées avec des circuits imprimés semi-rigides. L’utilisation de plus en plus répandue des composants des boîtiers-systèmes (SiP) et des puces-systèmes (SoC) multicœurs, également disponibles avec une architecture 64 bits, ainsi que la réduction de l’espacement des broches de 0,4 mm à 0,35 mm, sont probablement appelées à enrayer la croissance du nombre de couches, voire à en réduire le nombre.
Les concepteurs de circuits imprimés destinés aux appareils mobiles doivent accorder une attention particulière aux aspects technologiques dès les premières étapes du développement. Les principaux facteurs à prendre en compte lors de la conception de ce type de cartes sont les suivants :
- la définition de la topologie du circuit imprimé, des trous de positionnement et des repères nécessaires à la production et à l’assemblage automatiques
- la définition du panneau requis dans la phase de production du circuit imprimé
- la sélection des matériaux utilisés pour les substrats, sélection des composants adéquats et de leur emballage
- le positionnement des composants et l’espacement relatif entre eux.
1 - Topologie
Il convient de commencer par le positionnement des composants de plus forte puissance. Ils doivent être placés le plus près possible des composants qui leur sont associés, de manière à réduire au maximum la longueur des pistes à courant élevé. Il convient également de respecter une certaine distance minimale par rapport aux pistes sur lesquelles circulent les signaux à haut débit, car elles sont plus sensibles aux phénomènes d’interférence et de diaphonie.
À titre indicatif, vous pouvez respecter l’ordre suivant pour placer les composants : connecteurs, composants de puissance, composants sensibles, composants critiques, autres composants. Tous les composants similaires doivent être orientés dans la même direction afin de limiter les risques de problèmes de soudure. Sur la face soudée de la carte, ne placez pas d’autres composants à proximité des bornes à trou traversant qui se trouvent sur la face opposée de la carte. Il convient de regrouper les composants montés en surface sur la même face du circuit imprimé. La même règle s’applique aux composants traversants afin de simplifier l’assemblage et d’en réduire les délais.
Après avoir positionné les composants, passez au routage des pistes correspondant à l’alimentation, aux signaux et à la masse. Il doit être hiérarchisé en fonction des niveaux de puissance et de la susceptibilité au bruit et aux interférences. Les composants de puissance doivent recourir à des plans de masse ou de puissance afin d’assurer une meilleure dissipation de la chaleur, tandis que les pistes acheminant les signaux doivent être aussi courtes et droites que possible, en évitant que leurs tracés soient parallèles sur de longues distances afin d’éviter les phénomènes de couplage. Les condensateurs de découplage doivent être positionnés près (ou en dessous) des broches d’alimentation afin qu’ils puissent absorber les pics de puissance parasites.
Les pistes qui acheminent des signaux nécessitant un haut degré d’isolation doivent être placées sur des couches séparées, éventuellement orthogonales entre elles avec un plan de masse pour les séparer. Le positionnement orthogonal des pistes minimise le couplage capacitif, tandis que le plan de masse assure un blindage électrique. Cette technique est largement utilisée pour obtenir des pistes à impédance contrôlée, où l’impédance caractéristique demeure constante en chaque point de la piste (par exemple, 50 Ω). Parmi les types très courants de pistes à impédance contrôlée, on trouve les microbandes et les lignes à rubans qui donnent des résultats similaires malgré des structures géométriques différentes. Le contrôle de l’impédance peut s’effectuer à l’aide de l’un des nombreux outils disponibles en ligne. Il nécessite souvent d’équilibrer la longueur des pistes. Dans des cas extrêmes, il peut s’avérer nécessaire de prévoir des « serpentins » appropriés sur le circuit imprimé, comme illustré sur l’image 1.
Image 1 : mise en place de « serpentins » en vue d’équilibrer la longueur des pistes.
2 - Séparation
La zone RF d’un circuit imprimé destiné à un usage mobile doit être séparée et isolée de manière appropriée des zones dédiées à l’alimentation électrique et des zones dédiées aux signaux logiques et numériques de faible puissance. Les signaux analogiques sensibles doivent également être éloignés le plus possible des signaux numériques à haut débit et des signaux RF. Les signaux numériques et analogiques doivent également disposer chacun de leur propre raccordement à la masse.
Dans la mesure du possible, il convient de séparer les circuits analogiques et numériques. En fait, les fronts montants rapides des signaux numériques risquent de créer des pointes de courant et de générer du bruit, deux phénomènes qui sont susceptibles d’endommager les circuits analogiques. L’image 2 montre un exemple de séparation entre la zone analogique et la zone numérique d’un circuit imprimé.
Image 2 : séparation entre la zone analogique et la zone numérique (source : Altium)
3 - Via et repères
Les pistes à courant élevé, notamment celles qui traversent plusieurs couches, doivent comporter au moins deux à quatre via afin d’améliorer la dissipation de la chaleur et de réduire les pertes inductives et résistives. Plus les trous sont grands, plus la carte peut tolérer des courants élevés et plus la conduction thermique est efficace. De même, pour les pistes à courant élevé, il est préférable de prévoir plusieurs trous plutôt qu’un seul.
En général, chaque face du circuit imprimé doit comporter au moins deux repères. Ils doivent généralement être de forme circulaire avec un diamètre de 1 mm (40 mils). En outre, leur couleur doit être identique à celle du fond interne afin d’être compatible avec le revêtement en cuivre.
4 - Gestion thermique
La gestion thermique est une question importante qui mérite une attention particulière afin d’éviter de dégrader le circuit imprimé, voire de l’endommager. Le concepteur doit donc consulter les fiches techniques correspondantes afin de déterminer les valeurs de résistance thermique de chaque composant et de savoir quels sont les composants qui dissipent le plus de chaleur. Il convient alors de s’assurer que les composants les plus critiques sont placés à une distance suffisamment grande des composants qui dégagent de la chaleur.
La première astuce pour éviter la production de chaleur consiste à utiliser des pistes plus larges. Les composants de puissance, susceptibles de surchauffer davantage, doivent être placés au centre de la carte afin de favoriser la dissipation de la chaleur, tout en restant séparés des autres composants chauds. Enfin, si la taille de la conception le permet, il convient également de prévoir des ventilateurs de refroidissement, des dissipateurs thermiques, des plans de masse et d’alimentation solides, ainsi qu’un nombre adéquat de via thermiques. Il peut également s’avérer nécessaire d’augmenter l’épaisseur des stratifiés ou d’utiliser des matériaux différents présentant une meilleure résistance et une meilleure dissipation de la chaleur.
5 - Plans de masse
Les plans de masse fournissent une tension de référence commune, assurent un blindage, permettent la dissipation de la chaleur et réduisent l’inductance parasite (bien qu’ils accroissent la capacité parasite). Idéalement, chaque circuit imprimé devrait comporter au moins une couche entièrement dédiée au plan de masse. Les meilleurs résultats sont atteints lorsque ce plan est solide, c’est-à-dire sans aucune discontinuité.
Comme les plans de masse occupent généralement une grande surface du circuit imprimé, leur résistance est minimale. À basse fréquence, le courant emprunte le trajet présentant la plus faible résistance, tandis qu’à haute fréquence, le courant emprunte le trajet présentant la plus faible impédance. Les plans de masse et d’alimentation doivent être symétriques, centrés et placés dans les couches les plus internes du circuit imprimé.
6 - Matériaux
La technologie mise en œuvre pour la fabrication des circuits imprimés multicouches est largement utilisée dans les applications médicales. Les couches du circuit imprimé sont obtenues par un procédé soustractif. L’interconnexion entre les couches est obtenue par des étapes de laminage, de perçage mécanique, de cuivrage chimique et de cuivrage. Le procédé se termine par la création du masque de soudure, du revêtement de protection du circuit imprimé (revêtement conforme) et de la sérigraphie.
À l’heure actuelle, les circuits imprimés multicouches sont extrêmement fins. La largeur et l’espacement des pistes sont très faibles et la densité des composants et des pistes est particulièrement élevée.
7 - Panneau
Pour bien concevoir un circuit imprimé, il convient de prévoir dans le développement la réalisation d’un modèle de panneau pour la phase d’assemblage. Une fois la conception du circuit imprimé achevée, l’étape suivante consiste à envoyer les informations relatives au circuit imprimé à une entreprise de fabrication, ainsi que les spécifications de conception du panneau, afin de s’assurer que le format de réception du circuit imprimé est conforme aux attentes. Ces informations doivent comprendre :
- La taille maximale du panneau pouvant être gérée par les machines de production.
- Des repères supplémentaires pour permettre aux systèmes d’alignement visuel des machines de savoir exactement où se trouve le circuit imprimé (en général, on ajoute trois repères sur le panneau, dans trois des quatre coins de chaque côté du circuit imprimé afin que la machine puisse déterminer si le circuit imprimé a été chargé correctement ou non).
- Si les machines l’exigent, prévoyez des trous spéciaux (trous d’outillage) près des bords du panneau afin de permettre l’usinage du circuit imprimé.
- Courbez les coins du panneau pour éviter de briser les joints lorsque les panneaux de circuits imprimés sont emballés sous vide.
L’image 3 montre un exemple de panneau correctement conçu.
Image 3 : exemple de panneau de circuit imprimé
26/11/2021