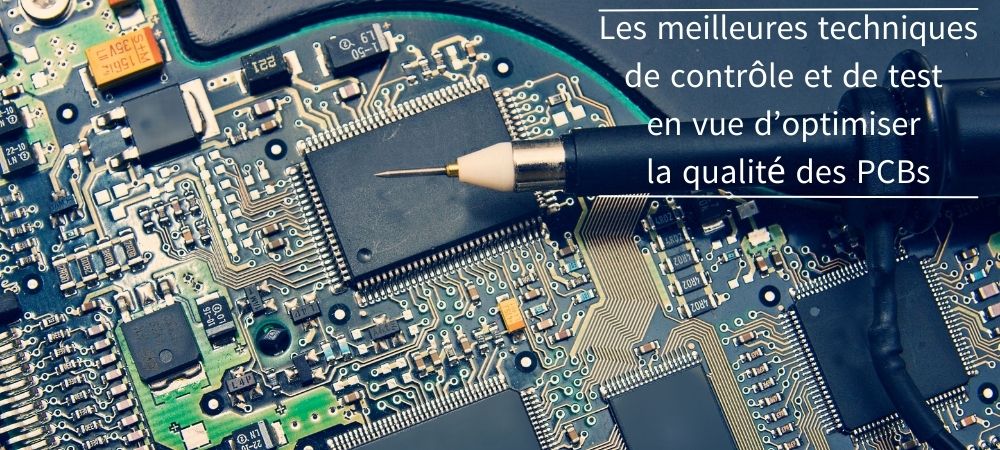
Le contrôle et le test portent sur deux étapes essentielles de la fabrication de chaque circuit imprimé et permettent une évaluation objective de la qualité du produit final. Bien que les ingénieurs respectent toutes les règles et tiennent compte de tous les conseils en matière de conception, il existe toujours un risque de défaillance, de bogue ou d’erreur humaine. Pour garantir les caractéristiques, les fonctionnalités et la fiabilité du produit, il est essentiel de détecter et de résoudre ces problèmes avant que le circuit imprimé n’atteigne la dernière étape du développement.
Il existe aujourd’hui des équipements capables d’effectuer des tests entièrement automatisés sur des circuits imprimés et pouvant être exécutés directement dans le même environnement de fabrication que le circuit imprimé. Les principales techniques actuellement disponibles sont les tests fonctionnels, le contrôle optique par caméra et l’inspection aux rayons X. Il est également possible de tester les circuits imprimés après l’étape d’assemblage, avec tous les composants correctement placés et soudés.
et recevez un devis pour votre projet de PCBA dans les 10 prochaines minutes !
Le contrôle optique balaie le circuit imprimé à la recherche d’éventuels problèmes de soudure : ponts, courts-circuits ou connexions électriques de mauvaise qualité, etc. Ces systèmes utilisent des caméras mobiles à haute résolution qui sont généralement capables de détecter jusqu’aux composants mal placés ou manquants. Certains systèmes de test font également appel à l’inspection aux rayons X en trois dimensions afin de détecter des problèmes non visibles avec le contrôle optique standard. Par exemple, les systèmes à rayons X sont capables de détecter les imperfections des soudures réalisées sous les matrices à billes (BGA) et les puces retournées (l’image 1 montre un exemple de boîtier de puce retournée).
Image 1 : circuit intégré avec un boîtier de puce retournée (flip chip)
Contrôle optique automatique
Le contrôle optique automatique (Automatic optical inspection, AOI) consiste à analyser le signal optique détecté par une seule caméra (vision 2D) ou par plusieurs caméras (vision 3D) afin de surveiller les défauts des circuits imprimés, avec une résolution pouvant atteindre quelques µm. Cette méthode fournit des résultats qui ne sont valables que sur les cartes de circuits imprimés où les soudures, les connexions, les points de contact et les pistes à surveiller peuvent faire l’objet d’un contrôle optique. La technique AOI s’avère également très efficace pour détecter en amont les problèmes d’assemblage, tels que les courts-circuits, les circuits ouverts, les soudures trop fines et les rayures sur les pistes.
Les images haute résolution acquises par les caméras 2D/3D sont comparées aux images d’une carte modèle (soit le prototype validé) ou à une base de données d’images contenant des cartes valides ou défectueuses. Cette technique est capable d’exécuter tous les contrôles (qui, autrement, devraient être effectués manuellement) de manière complètement automatique, précise et rapide. En outre, il est possible de vérifier que les composants sont bien placés après l’assemblage, tant sur le plan du circuit imprimé que sur l’axe vertical. En effet, la technique AOI 3D permet également de détecter la hauteur des composants. L’AOI présente l’avantage de pouvoir être ajoutée directement au bout de la ligne de production des circuits imprimés afin de détecter rapidement les éventuels défauts. Cependant, comme il s’agit d’une méthode passive, elle ne peut détecter que les défauts qui se trouvent à la surface des circuits imprimés.
Inspection aux rayons X
Par rapport à d’autres méthodes d’inspection, l’inspection automatique aux rayons X (Automatic X-Ray Inspection, AXI) permet de détecter les imperfections des circuits imprimés impossibles à déceler à l’œil nu ou avec un système optique AOI. Les rayons X sont en effet capables de pénétrer aussi bien les couches du circuit imprimé que le boîtier des composants pour générer des images 2D ou 3D très détaillées. Il est ainsi possible, par exemple, de détecter les problèmes de soudure sur les matrices à billes (BGA) ou sur les points de contact cachés. Lors de la production de petits lots de circuits imprimés ou lors du prototypage, il suffit souvent de procéder à une inspection aux rayons X sur les composants dont les points de contact ne sont pas visibles.
Bien qu’il s’agisse probablement de la technique qui offre les meilleurs résultats, l’AXI est un processus long et coûteux qui nécessite du personnel qualifié, ce qui justifie son emploi pour les circuits imprimés produits à grande échelle ou pour des applications particulièrement critiques et complexes. Cette technique offre d’excellents résultats pour les composants BGA (l’image 2 montre un exemple) en permettant de vérifier les points de soudure cachés entre le composant lui-même et la surface du circuit imprimé.
Image 2 : inspection aux rayons X d’un composant BGA
Inspection aux rayons infrarouges
L’inspection aux rayons infrarouges des circuits imprimés, autrement dit la thermographie, utilise la chaleur dégagée par les composants et par le circuit imprimé lui-même. Cette technique est particulièrement adaptée aux applications de puissance qui font intervenir des courants plus élevés. L’inspection par infrarouge s’effectue au moyen de caméras thermiques spécifiques, par exemple FLIR. Elle peut fournir des informations impossibles à obtenir par le biais d’un simple contrôle optique.
Certains défauts sur les circuits imprimés, comme les soudures incomplètes, peuvent augmenter la résistance électrique en certains points du circuit et entraîner une augmentation de la température pouvant être détectée par une caméra infrarouge.
Un procédé couramment utilisé en thermographie est la soustraction d’image. Un logiciel adapté capture une image avant d’allumer l’appareil, créant ainsi un profil thermique idéal. Cette image de référence est ensuite soustraite des images suivantes, obtenues après la mise sous tension de l’appareil. Les valeurs statiques de température réfléchie sont ainsi éliminées pour ne laisser que les écarts de température réels liés à l’échauffement de la carte et de ses composants.
Il est important de souligner que la thermographie et l’inspection aux rayons X permettent également de détecter les éventuelles contrefaçons ou le clonage non autorisé du circuit imprimé.
Test sur circuit
Le test sur circuit (In-Circuit Testing, ICT) est un test entièrement automatisé capable de détecter les défauts de fabrication ou d’assemblage des circuits imprimés grâce à un processus de vérification précis par rapport au schéma.
En plaçant le circuit imprimé sur un lit de clous, ce test permet d’accéder à des points précis du circuit et de mesurer les caractéristiques de chaque composant, sans tenir compte des autres composants qui lui sont connectés. Il est possible de mesurer des paramètres tels que la résistance, la capacité et l’impédance, ainsi que le fonctionnement de certains composants analogiques, tels que les amplificateurs opérationnels. Il est également possible de mesurer le comportement de certains circuits numériques, bien que leur complexité empêche généralement que les vérifications complètes soient rentables. La technique ICT permet d’effectuer un test complet du circuit imprimé, en s’assurant que le circuit a été réalisé correctement. Parmi les défauts constatés, citons les courts-circuits, les circuits ouverts, les composants manquants ou mal orientés et les défauts de soudure. Pour les lots importants de circuits imprimés, il est possible de créer des masques de test personnalisés afin de réaliser les tests ICT de manière plus rapide et plus efficace. Un autre atout est le niveau élevé de couverture des défauts, qui peut atteindre 98 %.
Le principal inconvénient de cette technique est son coût élevé, qui ne se justifie que pour une production à grande échelle. À cela s’ajoute la nécessité de préparer un lit de clous spécial pour chaque circuit imprimé, et la possibilité de n’effectuer la vérification qu’en certains points du circuit imprimé correspondant aux points de test fournis par le concepteur.
Test à sonde mobile
Par rapport au test sur circuit, le test à sonde mobile a l’avantage d’être moins coûteux. Cette technique consiste à utiliser une sonde mobile qui est mise en contact, de manière entièrement automatique et configurable, avec des points d’intérêt électriques appropriés sur le circuit imprimé. Il peut s’agir de broches de composants, de via, de points de contact, etc. Par rapport à l’ICT, le test à sonde mobile présente l’avantage de pouvoir tester un grand nombre de points sur le circuit imprimé et pas uniquement les points de test prévus par le concepteur sur le circuit imprimé. En outre, il n’est pas nécessaire d’utiliser un dispositif fabriqué sur mesure (comme le lit de clous). Les modifications apportées aux composants ou à la conception initiale du circuit imprimé ne nécessitent qu’une mise à jour du logiciel.
Grâce au nombre élevé de points qui peuvent être vérifiés, le test à sonde mobile garantit une meilleure couverture des défauts que le test ICT. Cependant, il s’agit d’un processus beaucoup plus lent qui peut se révéler inadapté à la production à grande échelle de circuits imprimés. L’image 3 montre un dispositif de test automatique de circuits imprimés à sonde mobile.
Image 3 : Test PCB à sonde mobile
Test fonctionnel
Le test fonctionnel d’un circuit imprimé est normalement réalisé en fin de projet. Il permet de vérifier le fonctionnement et le comportement du circuit imprimé dans différentes conditions de fonctionnement simulées sur banc. Très souvent, le test fonctionnel vise à vérifier des comportements spécifiques indiqués par le client, en soumettant le circuit imprimé à différents types de contraintes électriques et environnementales.
Ce test permet de s’assurer que le dispositif à l’essai fonctionne comme prévu. En fonction de la complexité du projet et des critères à tester, le test fonctionnel peut aller d’un simple contrôle de l’alimentation électrique (mise sous tension/hors tension) à un test complet avec des protocoles de communication spécifiques et un logiciel dédié au test. En raison de sa souplesse, le test fonctionnel peut être utilisé comme substitut à des procédures de test plus coûteuses. Grâce à une simulation précise des conditions réelles de fonctionnement, le test fonctionnel fournit des résultats immédiats sur la qualité du projet. C’est pourquoi il est de plus en plus utilisé dans la production de petits lots, ce qui permet de s’assurer que chaque carte qui sort de la ligne de production est prête à être utilisée sur le terrain.
Bien qu’il s’agisse d’une procédure relativement peu coûteuse et applicable à tout type de circuit imprimé, la couverture des défauts par le test fonctionnel dépend rigoureusement des contrôles effectués pendant le test. En outre, la carte peut tomber en panne peu après avoir passé les tests fonctionnels si elle est soumise à des contraintes élevées.
Test de déverminage
Le test de déverminage a certains points communs avec le test fonctionnel. Il vérifie les caractéristiques du circuit imprimé et recherche les défauts non apparents avant que le circuit ne soit utilisé sur le terrain. Pendant les tests de déverminage, les cartes sont soumises à des conditions extrêmes qui excèdent les conditions de fonctionnement nominales. L’objectif est de détecter rapidement les éventuelles défaillances et de tester le fonctionnement du dispositif sous forte charge afin d’anticiper les problèmes susceptibles de survenir lors d’une utilisation réelle. Contrairement aux autres méthodes d’inspection, qui ne vérifient que les indicateurs de défaillances potentielles, le test de déverminage simule des conditions de fonctionnement extrêmes susceptibles de déclencher d’éventuelles défaillances.
Parmi ces conditions de fonctionnement extrêmes figurent généralement des variations de température, de tension, de courant, de fréquence de fonctionnement ou toute autre condition de fonctionnement pertinente pour le dispositif à l’essai. Les résultats de ce test sont très utiles aux concepteurs, car ils peuvent obtenir des informations précises pour comprendre la cause des défauts et optimiser le processus de conception ou de fabrication.
10.12.2021