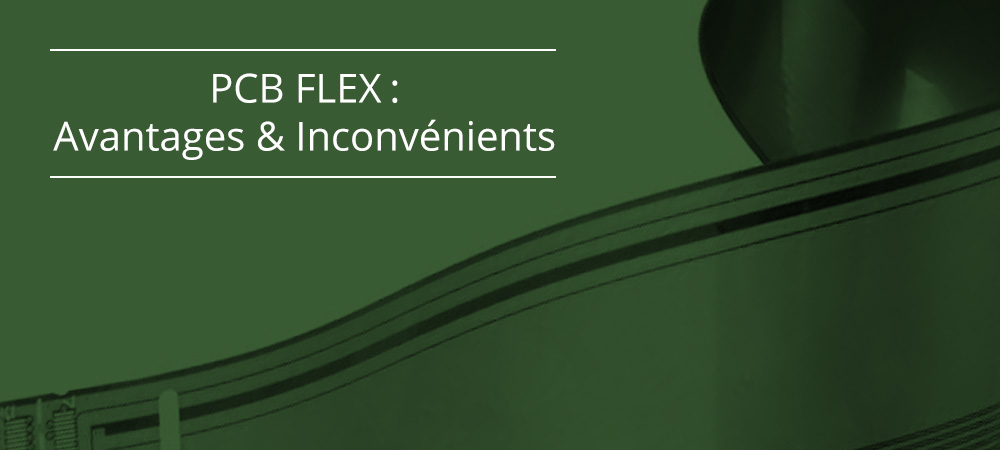
La technologie spécifique aux circuits imprimés flexibles (également connue sous le nom de FPC (Flexible Printed Circuit), est en croissance continue, avec des applications dans les principaux secteurs de l'électronique, tels que la consommation, l'automobile, les appareils électro-médicaux, les vêtements connectés, les télécommunications et l'aérospatiale. L'introduction de PCB flexibles a révolutionné les traditionnelles techniques d'interconnexion électrique, habituellement utilisées pour connecter plusieurs parties du même circuit ou de plusieurs appareils électroniques. Grâce à la nature flexible de la connexion, à sa compacité et à la haute densité de liaisons électriques réalisables, choisir des circuits flex permet d'obtenir une réduction considérable de l'espace, du poids et des coûts par rapport à une solution équivalente à base de PCB rigide. Ils ont remplacé de nombreux types de câblage, souvent à la main, dans plusieurs applications, réduisant le coût total du câblage électrique jusqu'à 70%. Le centre d'un FPC est représenté par des films souples et de fines couches de matériau conducteur qui effectuent la connexion électrique en remplaçant les fils traditionnels (pensez par exemple à la connexion entre une carte microcontrôleur et un écran LCD ou OLED), et sur lesquels les composants électroniques peuvent être fixés directement par soudure ou par adhésif conducteur. L’image 1 montre un exemple de circuit imprimé flexible.
Image 1 : Un circuit imprimé flexible (Source: Hoyogo)
Structure d'un PCB flexible
Comme pour les PCB rigides, les FPC peuvent être divisés en circuits simple couche, double face ou multicouches. Les principaux éléments d'un circuit imprimé flexible simple couche sont les suivants :
- film substrat diélectrique : le matériau de base du PCB. Le matériau le plus couramment utilisé est le polyimide (PI), caractérisé par une résistance élevée à la traction et à la température ;
- conducteurs électriques : en cuivre, ils représentent les pistes du circuit ;
- finition protectrice, réalisée avec une couche de matériau flexible qui protège et isole (coverlay ou cover coat)
- matériau adhésif (polyéthylène ou résine époxy), utilisé pour assembler les différentes parties du circuit.
La première phase de fabrication du FPC consiste à graver le cuivre pour obtenir les pistes, tandis que le revêtement protecteur (cover lay) doit être percé de façon à permettre l'accès aux plages d’accueil. Après un traitement nettoyant, les composants sont assemblés par laminage. Les bornes externes / pattes, nécessaires au raccordement électrique du circuit, sont protégées de l'oxydation par immersion dans de l'étain ou de l'or. Si le circuit a une complexité élevée, ou nécessite la présence de plans de masse en cuivre, il est nécessaire de passer à un FPC double face ou multicouche. La technique de fabrication est très similaire à celle utilisée pour les circuits flexibles simple couche, à la différence que dans les FPC multicouches, il est nécessaire d'insérer du PTH (Plated Through Hole), de manière à créer, le cas échéant, la connexion électrique entre différentes couches conductrices. L'assemblage de ces matériaux forme un circuit flexible, dans lequel le matériau adhésif sert à relier les pistes conductrices avec le substrat diélectrique ou, dans les circuits flexibles multicouches, à relier les couches individuelles ensemble. En outre, le film adhésif peut également être utilisé à des fins de protection, empêchant l'humidité, la poussière ou d'autres agents externes de corroder ou d'oxyder le circuit flexible. Sur l’image 2, nous pouvons observer la structure d'un FPC multicouches. L'exemple illustré comprend quatre couches de cuivre conductrices, des PTH (sur le côté droit de l'image) et des trous pour accéder au matériau conducteur (sur le côté gauche de l'image, sur les deux couches externes).
Image 2: Structure d’un PCB Flexible multi-couches (Source: Altium)
Avantages des PCB flexibles
Étant flexibles, les FPC peuvent être pliés et fléchis, ce qui permet une plus grande liberté dans la conception et le fonctionnement de l'application. Ces circuits peuvent également s’ajuster dans des espaces très petits ou ayant une forme irrégulière, caractéristique non prise en charge par les circuits rigides standards. Les FPC prennent également moins de place, ce qui réduit le poids sur la carte mère de l'application. L'utilisation optimale des espaces libres permet également une meilleure gestion thermique, en réduisant la quantité de chaleur à dissiper.
Comparés aux PCB rigides, les circuits imprimés flexibles peuvent également s'avérer plus fiables et durables, en particulier dans les applications où les circuits sont soumis à des vibrations continues et à des contraintes mécaniques. Les techniques d'interconnexion standard, basées sur des fils soudés et des connecteurs câblés à la main, sont remplacées par des circuits imprimés flexibles, caractérisés par un poids et une épaisseur extrêmement faibles, qui s'accompagnent d'une résistance mécanique élevée, d'une résistance aux températures hautes et aux agents atmosphériques ainsi que d'une bonne immunité électromagnétique (EMI). Pensez, par exemple, au câblage de plusieurs appareils électroniques dans le secteur automobile, tels que le tableau de bord, l'affichage et les interfaces homme-machine (commandes rotatives, boutons, etc.). Tous ces dispositifs nécessitent une connexion fiable dans toutes les conditions de fonctionnement du véhicule, étant en outre soumis à des contraintes et vibrations mécaniques continues. Dans ce secteur, les circuits imprimés flexibles garantissent fiabilité, durabilité et interventions de maintenance tendant à zéro. L’image 3 montre une application automobile de la technologie FPC, utilisée ici dans un interrupteur d'éclairage de voiture.
Image 3: Exemple d'application FPC dans l'industrie automobile
De plus, l'utilisation du FPC peut réduire l'incidence des erreurs humaines pendant le câblage, avec une amélioration conséquente de la qualité et une réduction des coûts. Cette technologie contribue à réduire considérablement la taille et le poids de l'application, un facteur clé pour la création d'appareils électroniques fiables, compacts et hautement intégrés.
Limitation des PCB flexibles
Bien qu'il existe plusieurs avantages significatifs, la technologie FPC présente cependant certains inconvénients. Tout d'abord, par rapport aux PCB rigides traditionnels, les FPC ont un coût initial unique élevé. Les circuits flexibles étant conçus pour des applications très spécifiques, les coûts initiaux liés à la conception des circuits et des prototypes sont plus élevés que pour les PCB rigides. Si le coût est un facteur déterminant dans le choix du type de PCB, il est préférable d'utiliser cette technologie uniquement pour des volumes de production pas trop faibles.
Il est également difficile de réparer ou de modifier le PCB quand il doit être retravaillé. Dans ce cas, en effet, il faut d'abord retirer le film protecteur qui enveloppe le circuit, effectuer l'intervention puis remettre la protection. Etant une technologie relativement nouvelle, tous les fabricants ne sont pas équipés pour fournir ce type de produit à leurs clients. De plus, pendant la phase d'assemblage, il faut être très prudent, car le circuit peut être facilement endommagé s'il est manipulé incorrectement ou par du personnel non qualifié.
Conclusion
Les circuits imprimés flexibles sont utilisés dans plusieurs applications que nous rencontrons dans la vie quotidienne, comme les smartphones, tablettes, appareils photo, imprimantes et ordinateurs portables. Ils peuvent même être hébergés à l'intérieur de notre corps, constituant un élément fondamental pour la création de stimulateurs cardiaques, d'implants cochléaires et de défibrillateurs. Au cours des dernières années, l'industrie des FPC s'est considérablement développée, tirée par la propagation d'appareils portables et électro médicaux de plus en plus petits et plus légers. Dans de nombreuses applications, les PCB flexibles peuvent éliminer le besoin (et le coût) de connecteurs et de câbles, améliorant la fiabilité de la connexion et réduisant le temps d'assemblage, les coûts d'assemblage et les dimensions globales de l'appareil.
En conclusion, nous pouvons affirmer que les PCB flexibles ont permis la mise en œuvre d'applications nouvelles et intéressantes, non réalisables avec les PCB rigides traditionnels. Cependant, lors de l'analyse préliminaire de chaque nouvelle conception, il est nécessaire d'évaluer soigneusement les avantages et les limites découlant de l'utilisation d'un PCB flexible, par rapport à un PCB rigide. Pour de nombreuses applications, le choix d'un PCB flexible est obligatoire, pour d'autres il dépendra des résultats de l'analyse des coûts et bénéfices.
et recevez un devis pour votre projet de PCBA dans les 10 prochaines minutes !