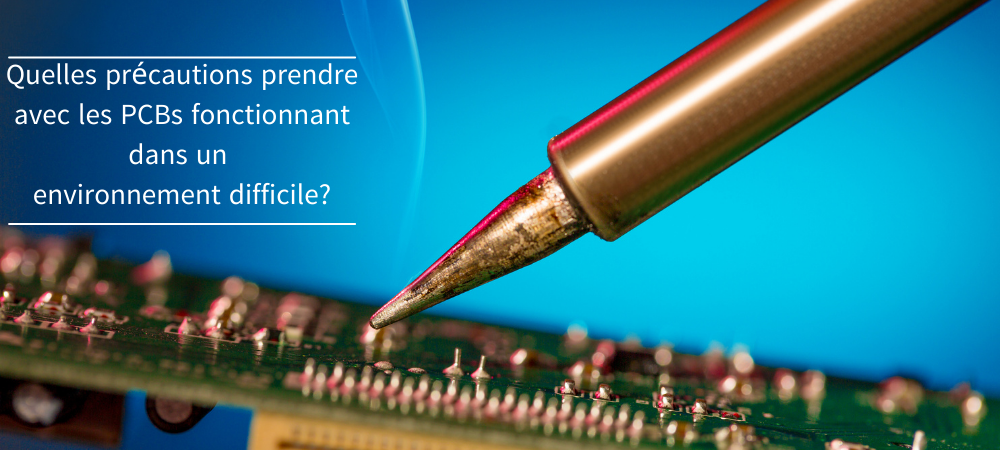
Certaines catégories d’appareils électroniques doivent fonctionner dans des conditions particulièrement difficiles, comme le brouillard salin, le sel, la poussière, le sable ou des températures extrêmes. Pour que le fonctionnement du circuit électronique demeure inchangé par rapport aux conditions normales, le circuit imprimé doit être prévu pour résister à ces événements sans être endommagé.
Les circuits imprimés utilisés dans les secteurs de l’automobile, de l’industrie ou de l’aérospatiale, par exemple, sont soumis en permanence à des vibrations, des contraintes mécaniques, des chocs, des écarts thermiques très importants, etc. Hormis certaines catégories d’appareils électromédicaux, peu d’appareils électroniques fonctionnent dans des environnements exempts de poussière, de vibrations, d’humidité et à des températures rigoureusement contrôlées. En réalité, il est nécessaire de gérer :
- les vibrations et les contraintes mécaniques
- les variations extrêmes de pression (variations d’altitude associées)
- les variations extrêmes de température
- les poussières, les graisses et autres agents chimiques
- l’humidité
- les rayonnements ionisants
- les interférences électromagnétiques, tant par rayonnement que par conduction
- les décharges électrostatiques et les transitoires de tension/courant.
et recevez un devis pour votre projet de PCBA dans les 10 prochaines minutes !
Problèmes à traiter
Les principaux problèmes auxquels les circuits imprimés sont confrontés dans les environnements difficiles peuvent se récapituler comme suit :
- Humidité, poussière et saleté: pour contrer ces facteurs environnementaux, il est souvent nécessaire de traiter les circuits imprimés à l’aide d’un procédé spécial appelé « revêtement conforme ». Avec cette méthode, le circuit imprimé est recouvert, après l’assemblage, d’une fine couche de matériau de protection non conducteur, tel que du silicone, de l’acrylique, de l’uréthane ou du p-xylène. Le revêtement permet de prolonger la durée de vie du circuit électronique en le protégeant des contaminants extérieurs.
- Températures élevées: si le circuit imprimé doit fonctionner en permanence à des températures supérieures à la norme, il est préférable d’utiliser des couches de cuivre plus épaisses (cuivre lourd). On combine généralement des épaisseurs de cuivre supérieures à 105 µm (3 oz) avec l’application d’un revêtement conforme afin de conférer au panneau un niveau élevé de protection en cas de fonctionnement continu à des températures élevées. L’utilisation de couches ayant une température de transition vitreuse (Tg) plus élevée, comme le FR-4 TG140 ou TG170, assure au circuit imprimé une protection supplémentaire contre la température.
- Rayonnements ionisants: outre les rayonnements électromagnétiques provenant du soleil et d’autres corps célestes, les circuits imprimés destinés aux applications aérospatiales sont bombardés de particules de différents types. Ces rayonnements peuvent provoquer des perturbations temporaires (telles que des inversions de bits ou des suppressions de mémoire) ou des dommages permanents aux composants.
- Chocs et vibrations, notamment dans les applications automobiles et aérospatiales.
- Corrosion: il s’agit de l’un des principaux dangers pour toutes les pièces métalliques. La corrosion se produit lorsque les atomes d’oxygène et de métal se lient les uns aux autres par un processus dit d’oxydation. Ce phénomène fait apparaître de la rouille ; le métal perd ses propriétés chimiques et se dégrade au fil du temps. Comme les circuits imprimés contiennent une grande quantité de métal, ils sont sensibles à la corrosion en cas d’exposition à de l’oxygène.
Revêtement conforme
Pour éviter les dommages causés par les agents atmosphériques, un revêtement de protection non conducteur, appelé revêtement conforme, est appliqué sur le circuit imprimé après l’assemblage (Image 1). Il s’agit d’une application courante pour les circuits imprimés destinés aux consommateurs, aux appareils électroménagers et aux dispositifs mobiles qui fonctionnent souvent en présence d’humidité, de poussière ou d’autres facteurs environnementaux difficiles. La couche de protection appliquée sur le circuit imprimé permet à l’humidité présente dans les couches du circuit de s’écouler vers l’extérieur, tout en empêchant les agents extérieurs d’atteindre la carte et ses composants et de compromettre leur fonctionnement. En plus d’augmenter la fiabilité, le revêtement conforme prolonge la durée de vie du circuit.
Image 1 : application d’un revêtement conforme
Les types les plus courants de revêtement conforme sont le silicone, la résine acrylique, le polyuréthane et le p-xylène, chacun étant capable de fournir un certain niveau de protection. Le silicone, par exemple, peut couvrir la plus large gamme de températures et constitue donc le meilleur choix pour les applications aux températures extrêmes. En revanche, le silicone présente une faible adhérence sur certains types de substrat et une résistance chimique inférieure à celle de la résine acrylique qui, elle, n’est pas particulièrement adaptée aux chocs et aux vibrations en raison de sa structure rigide. Les polyuréthanes offrent une grande résistance à l’humidité, à l’abrasion et aux vibrations. Ils résistent bien aux basses températures, mais pas aux hautes températures. Par conséquent, ils sont principalement utilisés dans des applications dont les températures vont de -40 °C à +120 °C. Le p-xylène est un matériau homogène qui offre une protection élevée, mais il est coûteux et doit être appliqué sous vide en raison de sa sensibilité aux contaminants.
En ce qui concerne l’application du revêtement conforme du circuit imprimé, quatre techniques peuvent être utilisées : l’application au trempé, le revêtement sélectif automatisé, la pulvérisation et le brossage. Chacune de ces solutions permet d’atteindre le même objectif : recouvrir entièrement le circuit imprimé, notamment les arêtes vives et tous les bords de la carte. Après l’application, le revêtement conforme est durci par séchage à l’air, au four ou par lumière ultraviolette.
Températures élevées
La densité croissante des composants sur le circuit imprimé entraîne une augmentation inévitable des températures de fonctionnement, une situation qui, à long terme, peut compromettre l’intégrité des soudures ou des couches elles-mêmes en raison de la dilatation et de la contraction de matériaux ayant des propriétés physiques différentes. Un circuit imprimé résistant aux hautes températures doit donc utiliser un matériau diélectrique dont la température de transition vitreuse (Tg) est supérieure ou égale à 170 °C. Une règle normalement appliquée est de permettre des températures de fonctionnement jusqu’à environ 25 °C inférieures à la valeur Tg du matériau utilisé. Outre le choix du matériau, la température élevée du circuit imprimé peut être gérée en évacuant la chaleur produite et en la transférant vers d’autres zones du circuit imprimé. Si le composant chaud est monté sur la face supérieure du circuit imprimé et présente une surface suffisamment grande, il est possible d’installer sur celui-ci un dissipateur thermique capable d’évacuer la chaleur par conduction (du composant vers le dissipateur), puis par convection (des surfaces du dissipateur vers l’air environnant, plus froid).
Si le composant chaud est monté sur la face inférieure du circuit imprimé et qu’il n’est pas possible de monter un dissipateur thermique, la technique généralement utilisée par les concepteurs consiste à insérer un grand nombre de chemins thermiques sur le circuit imprimé afin de transférer la chaleur du composant chaud vers une couche de cuivre sur le dessus du circuit imprimé, d’où elle peut être transférée vers un dissipateur thermique adapté. En général, les dissipateurs thermiques montés sur circuit imprimé sont de grande taille, avec des surfaces à ailettes ou ondulées permettant d’augmenter la surface de dissipation. Des ventilateurs peuvent être ajoutés afin d’améliorer le refroidissement par convection forcée, par rapport au refroidissement par convection naturelle.
L’une des méthodes traditionnellement utilisées pour contrer les effets produits par les hautes températures consiste à utiliser la technique du cuivre lourd qui permet d’augmenter le courant maximal pouvant être supporté par les pistes du circuit imprimé et, compte tenu de la moindre résistance, de réduire les pertes thermiques.
Mesures de protection contre les rayonnements
Pour les missions spatiales de longue durée, la seule option disponible est d’utiliser des composants durcis contre les rayonnements ionisants (rad-hard). Ces composants sont beaucoup plus rares et donc plus chers que les composants standard. Pour les missions spatiales de courte durée (jusqu’à un an), il est possible d’autoriser l’utilisation de composants commerciaux standard, sous réserve d’analyse et de vérification de leur résistance aux rayonnements. Vous pouvez ainsi réduire les coûts de conception des équipements spatiaux et élargir le choix des composants disponibles pour la conception. Il est possible de contrer les effets causés par les rayonnements en employant différentes techniques de conception matérielle. Au niveau de la conception du circuit imprimé, par exemple, il est important de garantir une mise à la terre adéquate de toutes les pièces métalliques.
Protection mécanique et corrosion
Pour assurer une protection contre les chocs et les vibrations, il est possible d’installer le circuit imprimé dans un conteneur dans lequel de la résine est versée afin d’obtenir une encapsulation complète. Plus la couche de résine est épaisse, plus le degré de protection est élevé. Si tous les composants du circuit imprimé n’ont pas une hauteur uniforme, l’épaisseur de la couche de résine variera toutefois d’un bout à l’autre de la carte, offrant des niveaux de protection légèrement différents pour chaque composant. La couche de résine la plus fine correspond donc, dans le pire des cas, au niveau de protection offert sur l’ensemble du panneau. Avant même d’envisager une encapsulation en résine, il convient de nettoyer le circuit imprimé avec soin. La contamination de la surface peut avoir une incidence négative sur les niveaux de protection offerts par l’encapsulation, en particulier dans les cas de résistance chimique (car elle facilite l’entrée des produits chimiques). En outre, les contaminants auront un effet négatif sur la capacité de la résine à absorber les chocs physiques et thermiques en raison de la faiblesse de la formation des couches entre la résine et le circuit imprimé, ce qui conduit finalement à des problèmes de décollement. Pour assurer la protection du circuit imprimé contre la rouille et les contaminations ioniques, il convient de le maintenir propre et sec. La corrosion peut être évitée par l’application du revêtement conforme, ainsi que par des finitions de surface telles que le procédé HASL (le circuit imprimé est plongé dans un alliage d’étain et de plomb liquéfié, puis les dépôts d’alliage sont nivelés par des jets d’air chaud) et le procédé ENIG (application d’or au trempé). L’image 2 montre le détail d’un circuit imprimé ayant une couche de finition obtenue par le procédé ENIG.
Image 2 : circuit imprimé ayant une couche de finition obtenue par le procédé ENIG