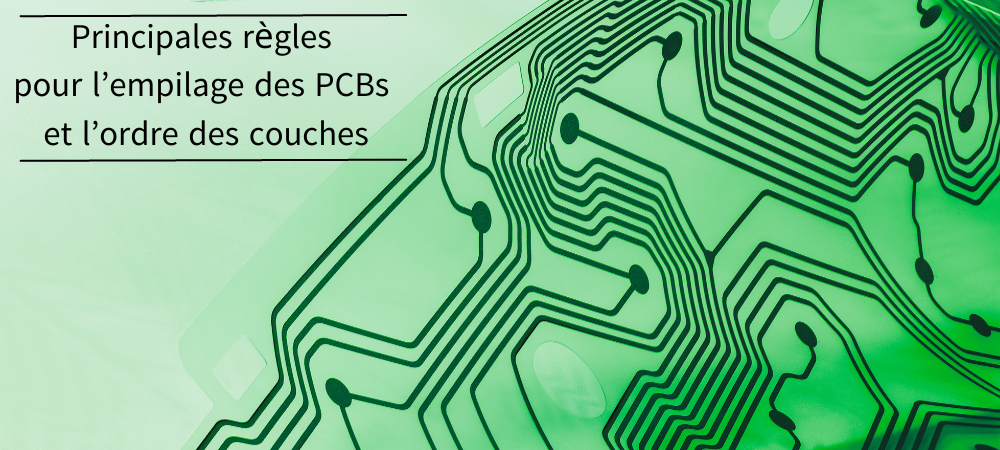
Les circuits imprimés sont essentiels au fonctionnement de la plupart des appareils électroniques actuels. Chacune de leurs couches est disposée physiquement dans un empilage et joue un rôle essentiel dans le fonctionnement général du circuit imprimé.
Cet article examine les règles de base à respecter pour effectuer l’empilage des circuits imprimés et ordonner ses couches, en tenant compte des caractéristiques particulières de la conception qui peuvent donner lieu à certains ajustements.
et recevez un devis pour votre projet de PCBA dans les 10 prochaines minutes !
Comprendre les différentes couches d’un circuit imprimé
Pour qu’un circuit imprimé fonctionne de manière efficace, il faut bien choisir son empilage et la disposition de ses couches. Mais avant de voir comment agencer les couches entre elles, il est nécessaire de connaître les différents types de couches qui forment un circuit imprimé.
On distingue trois types de couches : les couches de signal, les plans d’alimentation/de masse et les plans de séparation. Les couches de signal comportent les éléments du circuit, tels que les condensateurs, les résistances et les circuits intégrés. Les plans d’alimentation/de masse permettent qu’un flux de courant régulier passe dans le dispositif, et les plans de séparation réduisent les perturbations entre les signaux de potentiels différents. Pour définir l’ordre des couches, il est essentiel de comprendre la fonction assurée par chacune des couches. De cette façon, vous pourrez améliorer le fonctionnement de votre carte et donner à votre produit un atout supplémentaire face à la concurrence.
Facteurs à prendre en compte avant de concevoir un circuit imprimé
Avant de se lancer dans la conception d’un circuit imprimé, il faut tenir compte de quelques facteurs clés pour garantir que la conception est adaptée à l’application,
à savoir :
- Nombre de couches : les concepteurs doivent déterminer le nombre de couches du circuit imprimé. Les cartes à deux ou quatre couches sont courantes pour les petits composants, mais les cartes plus complexes peuvent avoir besoin de six ou même huit couches.
- Matériau du substrat : le matériau du substrat de la carte doit être choisi avec soin. Les plus utilisés sont le FR-4 époxy, le Rogers 4003 et le polyimide. Selon les caractéristiques de chaque matériau, il convient de sélectionner celui qui correspond aux critères de fréquence, de budget et de consommation d’énergie.
- Ordre des couches : l’intégrité des signaux et les performances dépendent de l’ordre des couches du circuit imprimé. Les signaux critiques, par exemple, doivent être situés sur les couches intérieures plutôt que sur les couches extérieures, de manière à renforcer l’intégrité des signaux.
- Définition de l’empilage : la définition de l’empilement permet de déterminer l’espace alloué entre chaque couche et de blinder ou isoler les signaux pour éviter les perturbations. Pour cette étape de la conception de la carte, les concepteurs doivent prendre en compte le poids en cuivre des pistes et la dimension des trous ou des fentes.
Principes de base de l’ordre des couches et de leur empilage
Pour résoudre les problèmes liés à l’ordre des couches et à leur empilage, les concepteurs doivent suivre certains principes fondamentaux.
1) Prise en compte du cahier des charges
Avant de mettre au point un empilage de circuits imprimés, il faut tenir compte du cahier des charges. Parmi les éléments importants à prendre en compte, on peut citer la taille de la carte, le mode de transmission du signal, les fréquences visées et le nombre de couches. Selon les exigences, l’empilage doit comporter un certain nombre et un certain type de couches.
2) Détermination du type de couche
Il faut ensuite déterminer le type de couches nécessaire au circuit imprimé. Pour un circuit imprimé, les trois différents types de couches sont les plans de masse, les plans de signaux et les plans d’alimentation. Les plans de masse servent à fournir une voie de retour à faible impédance pour les signaux. Les couches de signaux servent à transmettre les signaux entre les composants. Les couches d’alimentation servent à alimenter les composants.
Pour concevoir un circuit imprimé, il faut commencer par la couche de signaux, la première couche de l’empilage où la plupart des signaux sont dirigés. La couche de signal doit se trouver à côté des couches d’alimentation et de masse. Le nombre de couches du circuit imprimé doit concilier le coût et la complexité de la conception avec les exigences en matière d’intégrité des signaux et d’interférence électromagnétique.
3) Détermination de l’ordre des couches
Après avoir déterminé les types de couches à employer, il faut déterminer leur ordre. Les couches de signaux se placent entre deux plans de masse selon l’ordre habituel d’empilage des circuits imprimés. Cette disposition protège bien les couches de signaux et limite les interférences électromagnétiques.
Pour maintenir une impédance uniforme et réduire les interférences électromagnétiques dans la carte, il est conseillé d’alterner les couches d’alimentation et de masse. Les signaux à grande vitesse doivent aussi être proches de la masse. Dans le cas des signaux à grande vitesse, tels que ceux des circuits numériques, il est important de placer la couche de signal au plus près d’un plan de masse afin de réduire le bruit et de préserver l’intégrité du signal.
Si le circuit imprimé contient des signaux analogiques et numériques, il est important de les placer sur des couches différentes afin de réduire les interférences entre eux. Si la conception exige des raccordements supplémentaires à l’alimentation et à la masse, il est recommandé d’ajouter à l’empilage des couches particulières d’alimentation et de masse.
4) Définition de l’épaisseur des couches et de leur matériau
Pour construire un empilage de circuits imprimés, il faut choisir avec soin l’épaisseur des couches et leur matériau. En effet, ces paramètres affectent les propriétés électriques des pistes : l’épaisseur détermine l’impédance, et le matériau la constante diélectrique et la tangente de perte. Voici une liste de substrats possibles :
- Pour fabriquer des circuits imprimés, on utilise souvent le FR-4, un matériau constitué de résine époxyde et de fibre de verre. Il offre des caractéristiques diélectriques intéressantes, une bonne résistance mécanique et un coût raisonnable. Sa constante diélectrique est égale à 4,3 et sa tangente de perte à 0,02.
- Le FR-4 haute température est une variante du FR-4 standard qui peut résister à des températures allant jusqu’à 170°C sans se dégrader thermiquement de manière significative. Il est donc adapté aux applications de haute performance.
- Flex PCB : pour les applications qui nécessitent une conception plus petite et plus légère, comme les dispositifs médicaux ou portables, le Flex PCB est une excellente solution. Il peut se plier, se tordre ou se rabattre selon les besoins.
- Résistant à la chaleur et aux environnements hostiles, le polyimide est un matériau robuste et stable. Compte tenu de ses propriétés, il convient parfaitement aux applications aérospatiales, militaires et médicales.
- Le matériau de marque Rogers se distingue par ses excellentes propriétés diélectriques, sa forte conductivité thermique, sa stabilité et sa faible tangente de perte. Il est souvent employé dans les domaines qui requièrent des fréquences élevées, comme les télécommunications, l’aérospatiale et la défense. L’image 1 présente un circuit imprimé qui utilise le RO4003C de Rogers comme matériau de substrat.
5) Détermination de la largeur des pistes et de leur espacement
L’impédance et les performances du circuit imprimé dépendent fortement de deux facteurs : la largeur des pistes et leur espacement. La largeur doit permettre au courant de circuler sans provoquer de surchauffe, et l’espacement doit éviter les phénomènes de diaphonie et d’interférences entre les pistes.
6) Vérification de l’intégrité du signal dans la conception de l’empilage
Pour s’assurer que les signaux se transmettent correctement dans l’empilage de circuits imprimés, il est nécessaire de procéder à une analyse minutieuse. Des phénomènes comme l’atténuation, les réflexions et la diaphonie peuvent nuire au bon fonctionnement du circuit. Il est possible de simuler la conception et de la valider au moyen d’un outil d’analyse de l’intégrité des signaux.
Image 1 : circuit imprimé avec substrat Rogers RO4003C
Avantages et inconvénients des circuits imprimés multicouches
Par rapport aux circuits imprimés à une ou deux couches, les circuits imprimés multicouches, comme ceux à 4 ou 6 couches, présentent des avantages et des inconvénients. Ils permettent une plus grande densité, une meilleure intégrité des signaux et un meilleur fonctionnement, mais ils sont plus coûteux et plus complexes à concevoir et à fabriquer. Le choix d’un circuit imprimé multicouche dépend des besoins du circuit et des moyens disponibles pour le réaliser.
Quels sont les avantages et les inconvénients des empilages de circuits imprimés multicouches ?
Avantages :
- Densité accrue : les circuits imprimés multicouches permettent de réduire la taille du circuit imprimé en augmentant sa densité. Ils peuvent, en effet, contenir plus de composants et de circuits sur une surface plus petite.
- Meilleure intégrité des signaux : en ajoutant des plans de masse et d’alimentation et en augmentant le nombre de couches pour le routage des signaux, les circuits imprimés multicouches réduisent les perturbations du circuit causées par le bruit, la diaphonie et les interférences électromagnétiques. Ils assurent, ainsi, une meilleure intégrité des signaux.
- Fonctionnement amélioré : les circuits imprimés multicouches améliorent le fonctionnement et les fonctionnalités, comme la présence de plusieurs plans de masse et d’alimentation, la maîtrise de l’impédance du routage et l’utilisation de paires différentielles.
- Rentabilité : les circuits imprimés multicouches sont plus onéreux que les monocouches ou les bicouches, mais ils peuvent s’avérer plus rentables. Ils permettent en effet de réduire la taille et le poids du circuit imprimé, ainsi que le nombre de composants à utiliser.
Inconvénients :
- Coût : les circuits imprimés multicouches coûtent plus cher que les circuits imprimés monocouches ou bicouches, car ils nécessitent plus de couches, ainsi que des procédés de fabrication particuliers.
- Complexité : pour assurer un fonctionnement optimal et la plus grande fiabilité, la complexité des circuits imprimés multicouches exige une expertise et une planification de la conception et de la fabrication plus poussées que celles des circuits imprimés monocouches ou bicouches.
- Disponibilité : tous les fabricants de circuits imprimés ne proposent pas des circuits imprimés multicouches, et d’autant moins que le nombre de couches est élevé que les demandes sont particulières.
- Difficultés de fabrication : la fabrication des circuits imprimés multicouches nécessite plusieurs étapes à la fois difficiles et chronophages, notamment le perçage, la métallisation et le laminage. Elles peuvent donc engendrer des retards de livraison et des erreurs de fabrication.
Empilage de circuits imprimés à 4 couches
Les circuits imprimés à quatre couches (image 2) sont couramment utilisés pour leur équilibre entre coût et fonctionnalité qui leur permettent de s’adapter à diverses applications électroniques. Ils comportent quatre couches de pistes et de plans en cuivre intercalées entre des couches isolantes. Les couches sont classées de la couche supérieure à la couche inférieure, et la disposition habituelle des couches d’un circuit imprimé à 4 couches est la suivante :
- Couche supérieure : il s’agit de la couche supérieure du circuit imprimé correspondant à la face supérieure de la carte, où sont situés les composants et le routage des pistes.
- Couche de signal 1 : il s’agit de la première couche intérieure permettant aux signaux de passer entre la couche supérieure et la couche inférieure, par le biais de son routage et de ses composants.
- Plan de masse ou d’alimentation : il s’agit de la deuxième couche interne qui a pour fonction de servir soit de plan de masse, soit de plan d’alimentation, selon les besoins du circuit. Le plan de masse permet d’assurer un retour de signal à impédance faible, alors que le plan d’alimentation fournit l’énergie nécessaire aux composants.
- Couche inférieure : il s’agit de la couche inférieure du circuit imprimé correspondant à la face inférieure de la carte, où sont situés les composants et le routage des pistes.
Les couches de cuivre sont séparées par des couches isolantes en matériau diélectrique, comme du FR-4 ou un autre matériau composite. L’épaisseur de ces couches dépend du cahier des charges et des besoins du circuit.
Pour raccorder les couches de cuivre, les circuits imprimés à 4 couches peut disposer de via, c’est-à-dire des petits trous pratiqués dans le circuit imprimé. Il existe deux types de via : les trous traversants métallisés et les trous traversants non métallisés, qui servent à acheminer les signaux et l’alimentation entre les couches.
Image 2 : Schéma d’un circuit imprimé à 4 couches courant
Conclusion
Pour obtenir un circuit imprimé performant et fiable, l’empilage de ses couches doit être étudié avec soin. Le fonctionnement du circuit imprimé est optimisé lorsque l’on choisit bien les caractéristiques de chaque couche (type, ordre, épaisseur, matériau, largeur et espacement des pistes) et que l’on respecte les contraintes liées à la conception et à l’intégrité des signaux. Il est possible de se servir d’un outil de conception de circuits imprimés pour créer et vérifier la conception de l’empilage.
20.09.2023