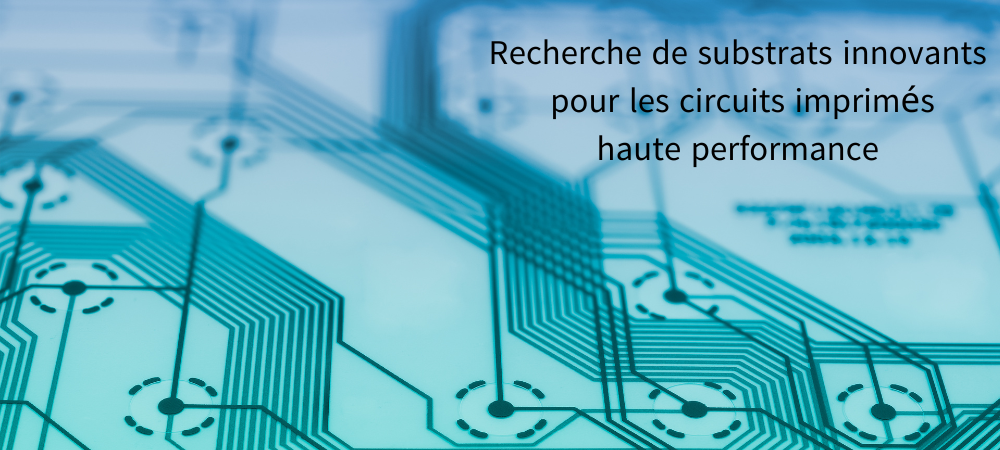
Les dispositifs électroniques reposent essentiellement sur les circuits imprimés qui assurent les connexions entre les multiples composants électroniques. Les avancées technologiques des appareils électroniques nécessitent des circuits imprimés plus efficaces, optimisés et dotés de fonctionnalités élargies. Pour ce faire, il est indispensable de recourir à de nouveaux substrats adaptés aux circuits de pointe. Cet article se penche sur l’avancement et les orientations futures possibles liés à l’adoption de nouveaux matériaux comme substrat de circuit imprimé.
et recevez un devis pour votre projet de PCBA dans les 10 prochaines minutes !
Substrats conventionnels
Prisé pour son coût modique et ses performances satisfaisantes, le FR-4 est le choix traditionnel pour les substrats de circuits imprimés. Cependant, avec la complexification et la miniaturisation croissantes des appareils électroniques, les inconvénients des substrats conventionnels prennent de l’ampleur, notamment en ce qui concerne la conductivité thermique et l’intégrité des signaux à haute fréquence.
Le FR-4, reconnu pour ses propriétés de retardateur de flamme, répond aux normes de sécurité en cas d’incendie et se trouve donc largement répandu là où la résistance au feu est primordiale. Sa constante diélectrique, allant de 4,2 à 4,7, est déterminante pour la vitesse de propagation des signaux électriques dans le substrat. Ce matériau se distingue également par sa bonne tenue en température, sans altération majeure, et par une robustesse mécanique et une longévité impressionnantes. Le FR-4, d’un coût abordable et facilement accessible, demeure donc une solution privilégiée pour de nombreuses applications standard.
Toutefois, ce matériau est sujet aux limites suivantes :
- Une conductivité thermique restreinte par rapport à certains substrats plus récents. Dans les applications à forte puissance, cette limite peut provoquer une accumulation thermique préjudiciable à la performance et à la fiabilité du dispositif.
- Intégrité des signaux à haute fréquence : le FR-4 risque de ne pas préserver une qualité de signal idéale, se traduisant par des pertes et des altérations du signal.
- Pour les applications exigeant des dispositifs électroniques souples ou pliables, le FR-4 perd de son intérêt en raison de sa rigidité. Le polyimide, par exemple, est alors souvent privilégié pour sa flexibilité.
Substrats avancés
Polyimide
Le polyimide, un matériau aussi polyvalent qu’avancé, s’est établi comme un pilier de l’industrie électronique en raison de ses caractéristiques uniques. Étant remarquable pour sa résistance à la chaleur et sa grande flexibilité, le polyimide figure parmi les éléments clés d’une multitude d’applications.
Sa capacité à tenir tête aux températures extrêmes fait du polyimide un choix privilégié dans des secteurs exigeants tels que l’aérospatiale, l’automobile et l’industrie manufacturière, où les dispositifs électroniques doivent souvent résister à de fortes températures.
Le polyimide se distingue par sa flexibilité. À l’opposé des substrats rigides conventionnels, il facilite la conception de circuits imprimés souples et pliables, ce qui représente un atout essentiel lorsque l’espace est limité ou que des formes spécifiques sont nécessaires.
Les circuits en polyimide sont couramment employés dans le secteur aérospatial en raison de leur légèreté et de leur capacité à épouser des formes complexes. Pour le domaine automobile aussi, sujet à des vibrations et des extrêmes thermiques, la flexibilité du polyimide confère aux circuits imprimés une meilleure résistance. L’image 1 illustre un exemple de circuit imprimé souple conçu en polyimide.
Image 1 : Exemple de circuit imprimé souple conçu en polyimide (Source : Cadence)
Le polyimide excelle non seulement par ses caractéristiques physiques, mais aussi par ses remarquables propriétés diélectriques. Avec des performances électriques stables, il est tout indiqué pour les applications à haute fréquence. Dans les secteurs comme les télécommunications, où l’intégrité du signal est primordiale, les circuits imprimés en polyimide assurent un fonctionnement optimal.
Néanmoins, le polyimide présente des contraintes. Si ses performances à haute température sont exceptionnelles, sa conductivité thermique demeure modeste si on la compare à d’autres matériaux. Pour les dispositifs générant beaucoup de chaleur, des solutions spécifiques de gestion thermique peuvent être requises.
Qui plus est, le coût du polyimide peut être supérieur à celui de substrats traditionnels tels que le FR-4. Ce facteur peut influencer le choix du substrat, surtout dans le cadre de la production de masse de produits électroniques grand public où le budget est un critère déterminant.
Stratifiés haute fréquence de Rogers Corporation
Les stratifiés haute fréquence proposés par Rogers Corporation marquent un progrès notable dans les substrats pour circuits imprimés adaptés aux contraintes imposées par les applications à haute fréquence.
Leur faible constante diélectrique constitue l’une de leurs qualités principales qui assurent l’efficacité de la transmission des signaux, un atout précieux pour des secteurs exigeants comme les télécommunications, les systèmes radars et les appareils électroniques haute fréquence.
En outre, leur faible facteur de dissipation est déterminant dans les circuits haute performance devant présenter très peu de pertes de signal. Cette caractéristique est indispensable lorsque la précision et la fiabilité des signaux sont essentielles, comme pour les dispositifs en communication sans fil et les systèmes radars de pointe.
Quant à leur stabilité dimensionnelle, elle est remarquable (image 2), assurant la constance des caractéristiques électriques du matériau face aux changements de températures et aux diverses contraintes environnementales. Cette propriété est capitale pour préserver la performance des circuits haute fréquence, spécialement lorsque les écarts de température sont conséquents.
Image 2 : Laminés RO4500 (Source : Rogers Corporation)
Ces laminés haute fréquence occupent une place de choix dans l’élaboration et la fabrication d’antennes, de dispositifs de communication satellite et de capteurs fonctionnant à haute fréquence. Le secteur des télécommunications tire notamment avantage de la qualité électrique supérieure de ces produits Rogers Corporation afin d’accroître l’efficacité de la transmission des données.
Toutefois, le coût de ces laminés haute fréquence est généralement plus élevé que celui des substrats conventionnels, ce qui peut se répercuter sur le prix final des appareils électroniques, et susciter des hésitations lors de l’achat pour le grand public.
De plus, le processus de fabrication des laminés haute fréquence peut demander des techniques spécialisées, suscitant des interrogations quant à leur capacité à s’adapter et à s’intégrer dans les chaînes de production actuelles.
Pyralux de DuPont
Le Pyralux, un substrat conçu par DuPont pour les circuits souples, émerge en tant que solution de choix dans l’industrie des circuits imprimés. Sa souplesse permet de concevoir des circuits qui épousent des formes inédites et s’adaptent à des contraintes spatiales particulières, un atout majeur dans les secteurs où l’optimisation de l’espace et l’adoption de configurations atypiques sont des enjeux essentiels.
Constitué d’un film de polyimide comme support souple et de couches de cuivre pour les pistes conductrices, Le Pyralux offre une résistance thermique remarquable, capable de résister à des variations de température sans altérer ses performances. Ce matériau est ainsi parfaitement adapté aux applications exigeantes comme dans l’aéronautique, l’automobile et les équipements médicaux où la flexibilité et la fiabilité sont primordiales.
Le Pyralux trouve toute son utilité dans les dispositifs compacts et légers. Sa nature souple est essentielle pour concevoir des circuits étirables ou pliables, le rendant idéal pour les appareils connectés portables, les affichages souples et les capteurs médicaux. Le secteur médical profite notamment du Pyralux pour mettre au point des circuits souples destinés aux implants et aux appareils diagnostics.
Toutefois, le Pyralux présente également certaines limites. Sa sophistication signifie souvent un coût supérieur comparé aux substrats rigides conventionnels, ce qui influe sur le coût global des appareils électroniques. De plus, les méthodes de production du Pyralux peuvent différer de celles employées pour les circuits rigides, nécessitant ainsi des équipements spécialisés et une expertise technique pointue. Cet aspect peut poser des difficultés en matière de mise à l’échelle et de fabrication en grande quantité pour des industries exigeant de grands volumes de production.
Circuits imprimés à partie centrale métallique
Les circuits imprimés à partie centrale métallique, souvent appelés MCPCB, comprennent une partie centrale métallique, généralement de l’aluminium ou du cuivre, changeant ainsi la conception des circuits. Cette caractéristique particulière les rend parfaitement adaptés à des applications qui exigent de hautes performances énergétiques ou qui évoluent dans des chaleurs intenses.
Les MCPCB se distinguent par leur aptitude à dissiper efficacement la chaleur émise par les composants électroniques grâce à une conductivité thermique accrue. La partie centrale métallique agit comme un radiateur, évacuant la chaleur loin des composants clés. Cette gestion de la température est essentielle dans des secteurs tels que l’éclairage à LED, les dispositifs d’alimentation ou l’électronique automobile, où la qualité de la dispersion thermique est synonyme de fiabilité et de durabilité pour les équipements.
La partie centrale métallique renforce également la solidité mécanique des MCPCB, assurant ainsi un support stable pour les composants. Cet atout est particulièrement important en cas de contraintes physiques ou de vibrations, comme c’est le cas dans les milieux industriels ou automobiles.
Les MCPCB trouvent leur place dans des applications gourmandes en énergie, comme les convertisseurs de puissance et les commandes de moteur. L’efficacité thermique des MCPCB permet aux composants électroniques de fonctionner de façon optimale, même dans des conditions extrêmes, ce qui réduit les risques de surchauffe et améliore les performances générales du dispositif.
Image 3 : Circuit imprimé LED en aluminium
Cependant, la mise en place d’une partie centrale métallique peut alourdir les cartes et les rendre plus onéreuses que les cartes FR-4 classiques, ce qui restreint leur emploi dans certains appareils électroniques grand public où le poids et le coût sont des facteurs déterminants. En outre, la partie centrale métallique réduit la souplesse des circuits imprimés par rapport aux des substrats souples tels que le polyimide.
Nouvelles technologies
La conductivité électronique exceptionnelle et la solidité du graphène lui ouvrent des perspectives intéressantes pour les circuits imprimés haut de gamme. De tels circuits, exploitant le graphène formé d’un maillage hexagonal d’atomes de carbone, disposent de caractéristiques remarquables susceptibles de transformer le domaine de l’électronique.
La conductivité électrique supérieure du graphène en fait un candidat idéal pour des circuits imprimés de pointe. Sa capacité à assurer un transfert plus libre des électrons dans les matériaux traditionnels accélère la transmission des signaux et l’optimise, ce qui constitue un avantage significatif pour les systèmes avancés de communication, ainsi que pour les processeurs nécessitant un transfert rapide des données.
Qui plus est, la conductivité thermique du graphène favorise la dissipation de la chaleur, solutionnant ainsi l’une des difficultés majeures lors de la conception d’appareils électroniques. Pour les applications à forte puissance, les circuits à base de graphène sont susceptibles de limiter les risques de surchauffe et d’accroître la fiabilité et la longévité des composants électroniques.
La structure atomique bidimensionnelle du graphène permet de réaliser des circuits imprimés extrêmement minces et légers, idéaux pour les dispositifs où l’espace et le poids sont restreints, ouvrant ainsi la voie à des appareils électroniques encore plus compacts. De nombreux secteurs, tels que l’aéronautique, les télécommunications, le matériel médical et l’électronique grand public, pourraient tirer profit des atouts électriques et thermiques des circuits à base de graphène.
La généralisation des circuits imprimés en graphène doit lever de multiples défis. La production de graphène de qualité en grandes quantités exige un procédé de fabrication qui soit économiquement viable. L’intégration du graphène dans les procédés de fabrication existants soulève des questions d’adaptabilité et de compatibilité avec les équipements industriels actuels.
De plus, bien qu’il se distingue par une résistance mécanique exceptionnelle, le graphène manque de souplesse par rapport à d’autres matériaux de type polymères. Cette limite risque de restreindre son usage dans les applications nécessitant une certaine souplesse ou capacité à épouser des formes complexes, comme les dispositifs portables ou les écrans souples.
Les substrats à base de polymère à cristaux liquides (LCP) sont eux loués pour leur performance et leur adaptabilité dans le domaine des circuits imprimés. Présentant une faible constante diélectrique et un faible facteur de dissipation, le LCP se distingue dans les fréquences élevées, assurant une transmission des signaux sans faille, un atout majeur dans les télécommunications, l’aviation et la transmission de données à haut débit.
En outre, son endurance face à la chaleur, grâce à sa température de transition vitreuse élevée et à son excellente conservation des propriétés structurelles et électriques sur de grands écarts de température, le rend particulièrement indiqué dans l’électronique embarquée automobile et l’automatisation industrielle.
Les caractéristiques mécaniques du LCP le rendent incontournable dans la conception de circuits imprimés. En raison de sa capacité à former des feuilles à la fois minces et souples, le LCP est prisé pour la fabrication de circuits à la fois souples et rigides. Cette polyvalence est précieuse dans des domaines tels que le médical et l’électronique portable, où il est essentiel de concevoir des dispositifs adaptatifs et légers.
Le LCP est utilisé dans de nombreux secteurs, allant des prothèses médicales à l’électronique de consommation, en passant par les systèmes de communication à haute fréquence et les antennes. Sa capacité à répondre aux exigences des technologies électroniques modernes en fait un matériau de choix.
Toutefois, la production de circuits imprimés à base de LCP tend à être plus onéreuse que celle employant des matériaux standard comme le FR-4. Cet écart peut peser dans la balance lors du choix des matériaux, surtout pour les produits électroniques grand public où la maîtrise des coûts est essentielle.
07.03.2024