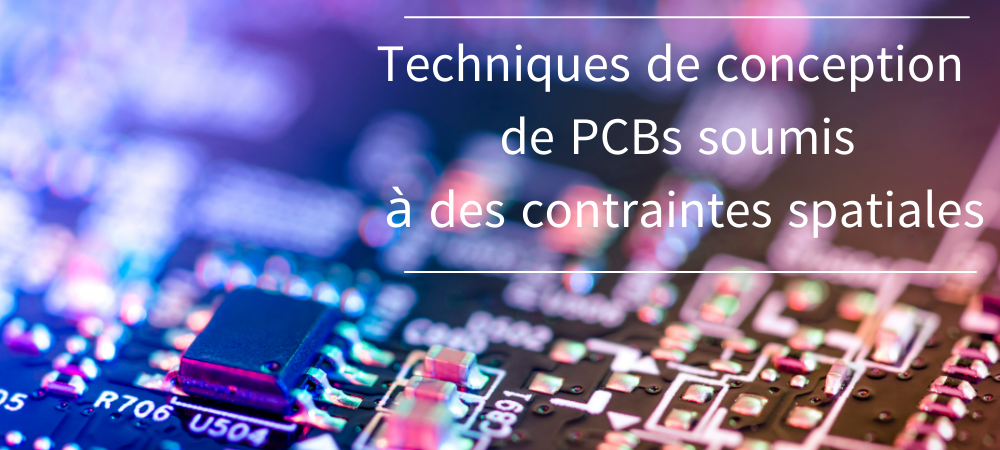
Grâce aux progrès réalisés dans le domaine des puces électroniques, la conception des circuits imprimés a beaucoup évolué en matière de taille et de forme. Ces changements ont entraîné une forte demande de performances optimisées dans un espace réduit, ce qui pose un certain nombre de problèmes aux méthodes traditionnelles de conception des circuits imprimés.
Afin d’optimiser l’espace alloué à la topologie, il est nécessaire de prendre des décisions importantes sur de nombreux aspects pendant la phase de conception du circuit. Ces choix seront déterminants pour la qualité du produit tout au long de sa vie. Les contraintes liées au routage des circuits imprimés constituent donc l’un des éléments les plus importants dans le domaine des circuits imprimés, ce qui confère une grande valeur ajoutée à la conception.
et recevez un devis pour votre projet de PCBA dans les 10 prochaines minutes !
Par conséquent, le phénomène de miniaturisation touche tous les secteurs d’activité et pose de nouveaux problèmes de conception aux ingénieurs chargés d’intégrer des solutions dans des systèmes soumis à de fortes contraintes spatiales. Ainsi, le concepteur doit garantir toutes les performances souhaitées du circuit électrique et des circuits imprimés, tout en respectant les limites imposées en matière d’espace.
Conception et tracé des circuits imprimés
Le tracé du circuit imprimé constitue la première des étapes de sa création, et l’une des plus importantes. Il est essentiel de créer une épure contenant les différentes zones du circuit imprimé ainsi que les limites de hauteur et de largeur, les composants du circuit et le nombre de pistes utilisées. En effet, ce schéma correspond à la configuration mécanique finale de la carte à fabriquer.
Découpes : Les plans doivent être réalisés avec précision dans la couche mécanique de manière à représenter la taille et la forme exactes de la découpe. Au cours de ce processus, il convient de respecter les cotes appropriées ainsi que les éventuelles tolérances électriques spécifiques. Dans un premier temps, le concepteur peut créer le contour en utilisant une ligne fine (0,50 mm de large) dont le centre peut servir à représenter le contour exact de la découpe.
Coins internes d’une découpe : La découpe doit être fraisée à l’aide d’un outil de 2,00 mm afin de s’assurer que le rayon de l’angle interne est supérieur ou égal à 1,00mm. En cas de nécessité d’un rayon inférieur, il convient de modifier la couche mécanique en conséquence.
Taille des fentes : Sur les circuits imprimés, on entend par « fentes » les trous qui sont trop grands pour être formés par des méthodes normales de perçage. Celles-ci doivent être réalisées avec précision dans la couche mécanique de manière à représenter la taille et la largeur exactes de la fente, ainsi que leurs tolérances. Il existe principalement deux types de fentes :
- Fentes métallisées : Dans la fabrication des circuits imprimés, les fentes métallisées consistent en un dépôt de cuivre. Lorsque les fentes du circuit imprimé sont revêtues de cuivre en bas et en haut, il s’agit de fentes métallisées.
- Fentes non métallisées : Les fentes non métallisées consistent en un trou plus grand que la taille du cuivre du point de contact. Dans les fentes non métallisées, on retrouve des superpositions de points de contact, car le fabricant perce la partie non métallisée après le procédé de dépôt autocatalytique de cuivre.
Image 1 : Taille de fente du circuit imprimé
Source : protoexpress.com
Contraintes relatives au routage dans les circuits imprimés
Ces derniers temps, le routage des circuits imprimés est devenu un problème majeur en raison de la complexité croissante des circuits électroniques. Différentes règles s’appliquent à la conception et à la production d’un circuit imprimé. Elles permettent au concepteur de relier les différents composants présents dans le circuit et facilitent la communication des données entre les différentes parties du circuit et la sortie souhaitée. Ces règles permettent d’éviter les problèmes au cours du processus de production et de fabrication en série afin de garantir des performances électriques de haut niveau.
Vous trouverez ci-dessous une liste de certains paramètres de contraintes de routage dans les circuits imprimés.
Composants : Il existe diverses contraintes que les concepteurs peuvent réglementer pour les composants tels que les résistances, les condensateurs, les transistors et les circuits intégrés, notamment les distances par rapport aux autres éléments et objets, les parties découpées de la carte de circuit imprimé, etc. Sauf indication contraire, le dégagement recommandé pour les composants est de 0,25 mm. Les composants de taille d’empreinte inférieure à 0603 pouces (1,6 x 0,8 mm) doivent avoir un dégagement de 0,15 mm. Des contraintes peuvent être définies par le concepteur pour la partie du circuit imprimé qui doit être limitée à une zone particulière en raison de divers facteurs électriques tels que les niveaux de puissance et le transfert de chaleur.
Largeur des pistes :
Image 2 : Largeur des pistes
Source :designwanted.com
Les concepteurs peuvent définir la largeur d’une piste pour différentes sections du circuit. La largeur des pistes est principalement utilisée pour contrôler l’impédance. Lorsque la puissance varie, la piste de routage doit avoir des largeurs très importantes et pour les projets de type RF, les largeurs doivent changer fréquemment.
Routage des pistes :
Image 3 : Routage des pistes
Source : pcbdesignworld.com
Outre la largeur et le dégagement de base, les circuits imprimés nécessitent un contrôle plus minutieux de la façon dont la piste est tracée. Grâce au routage en serpentin, le concepteur peut faire correspondre la longueur d’une piste à une autre piste, ce qui peut également inclure les longueurs minimale et maximale d’une piste. Les contraintes en matière de topologie peuvent également s’appliquer au circuit imprimé pour s’assurer qu’il respecte un schéma particulier, comme la topologie en T.
Plans : Il est possible d’assurer une bonne décharge thermique avec des réglementations qui autorisent les connexions entre les plans d’alimentation et de masse. Il est possible d’autoriser une quantité minimale de largeurs de métal dans le plan ainsi que ses différents motifs. Les plans présentent un certain nombre d’avantages, notamment :
- Amélioration du découplage entre les circuits: La surface d’un plan peut agir comme un condensateur de découplage à plaques parallèles entre la couche isolante et la masse, ce qui permet d’éviter la propagation du bruit à travers l’alimentation vers différentes parties du circuit.
- Chemins de retour courts: Les chemins de retour plus courts offrent une meilleure compatibilité électromagnétique (CEM) en raison de la facilité à suivre un via, de la couche du signal au plan de puissance, et du plan de puissance à l’alimentation du circuit.
- Capacité de transport de puissance plus élevée : Les plans peuvent supporter une plus grande quantité de transport de courant par rapport aux pistes, ce qui réduit la température de fonctionnement du circuit imprimé.
Haute densité d’interconnexion (HDI)
Dans le domaine des circuits imprimés, le sigle HDI correspond à la technologie haute densité d’interconnexion (High-Density Interconnect) qui permet de fabriquer des circuits imprimés de petite taille, légers et compacts. À l’heure actuelle, les dispositifs électroniques ne cessent de gagner en miniaturisation et en compacité. Ces petits dispositifs permettent d’effectuer en local des calculs complexes. Dans ces conditions, les circuits imprimés multicouches fabriqués selon le procédé habituel créent des problèmes tels que la diaphonie et la mauvaise intégrité des signaux. La technologie HDI, destinée aux dispositifs de petite taille et compacts, permet de résoudre ces problèmes.
Pourquoi utiliser la technologie HDI ?
Les circuits imprimés HDI présentent une plus grande densité de câblage que les circuits imprimés classiques ce qui permet de fabriquer des dispositifs électroniques plus petits et plus légers tout en étant performants. Comparée aux circuits imprimés traditionnels, la technologie HDI utilise des matériaux fins et des couches minimales dans sa composition, ce qui en fait la solution idéale pour les dispositifs complexes de petite taille.
L’un des principaux enjeux de cette technologie est l’intégrité des signaux, car les dispositifs sont très proches les uns des autres. Cette difficulté se résout par l’utilisation de microvia qui présentent une capacité et une inductance parasites plus faibles en raison de leur petite taille. Le diamètre des microvia étant inférieur à 150 µm, leur perçage s’effectue par laser. Par conséquent, il est possible d’empiler de nombreuses couches sans pour autant accroître le niveau de couplage de la diaphonie et du bruit. L’intégrité du signal est ainsi préservée.
Image 4 : Différents via de circuit imprimé
Source :mistralsolutions.com
Matériaux utilisés pour la technologie HDI
En sélectionnant les matériaux pour la fabrication du circuit imprimé, il convient de noter que la constante diélectrique du substrat doit être faible. La faible valeur de la constante diélectrique réduit le couplage capacitif entre deux couches adjacentes et permet aux signaux de circuler beaucoup plus rapidement dans les circuits. En conséquence, la réduction de la diaphonie entre les couches adjacentes permet de préserver l’intégrité du signal. Ce facteur est primordial dans le cas de la technologie HDI, car les pistes sont toutes regroupées dans une zone restreinte et dense.
L’éther époxy est le substrat le plus utilisé en raison de son faible coût et de ses bonnes propriétés thermiques, chimiques et électriques. En outre, les résines de polyimide et d’ester cyanate sont également utilisées en raison de leurs faibles valeurs de constante diélectrique (Dk) et de facteur de perte diélectrique (Df). Outre ces résines thermodurcissables, les résines thermoplastiques telles que le polyimide (PI) et le polytétrafluoroéthylène (PTFE) sont également utilisées en raison de leur souplesse.
Circuits imprimés souples
Les circuits imprimés souples (FPC) constituent une avancée dans le secteur. Ils permettent de résoudre la plupart des problèmes causés par les contraintes spatiales dans les circuits imprimés. Les nombreux types de câblage réalisés sur les circuits imprimés destinés à de multiples applications ont été remplacés avantageusement par les circuits imprimés souples, qui réduisent de près de 70 % les coûts de câblage électrique. Grâce à leur compacité et à leur flexibilité, un grand nombre de connexions électriques et de techniques de connexion peuvent être réalisées au moyen de FPC.
Image 5 : Carte de circuit imprimé souple
Source :raypcb.com
Structure d’une carte de circuit imprimé souple
À l’instar des circuits imprimés rigides, les circuits imprimés souples se déclinent en circuits à couche simple, à couche double et à couche multiple. Par rapport au circuit imprimé rigide, l’espace nécessaire aux pistes, l’espacement de la largeur des pistes et la taille des points de contact sont identiques. Cela tient aux matériaux souples utilisés et au processus de métallisation employé dans la fabrication des FPC. Un circuit imprimé souple se compose comme suit :
- Film de substrat diélectrique: Il s’agit du matériau de base du film de substrat. Le polyamide (PI) est le matériau le plus couramment utilisé pour fabriquer ce film en raison de sa grande résistance à la traction et à la température.
- Conducteurs électriques: Les conducteurs électriques sont fabriqués en cuivre. Ils sont utilisés pour réaliser les pistes du FPC.
- Matériau adhésif : Fabriqués en polyéthylène ou en résine époxy, les matériaux adhésifs servent à assembler les différentes parties des FPC.
Image 6 : Structure d’une carte de circuit imprimé souple
Source :proto-electronics.com
Conclusion
Il est possible de résoudre certaines des contraintes spatiales en s’assurant que les composants sont placés de manière à respecter un dégagement complet par rapport aux autres composants, soit 0,25 mm, et en appliquant des contraintes de routage adéquates pour la largeur des pistes, calculées en fonction des différents paramètres électriques. Il est possible de mettre en place des plans pour assurer une bonne régulation de la température sur la carte. Ceux-ci permettront éventuellement d’améliorer la capacité de transport de puissance et le découplage entre les circuits.
Les circuits imprimés HDI assurent que les pistes et les via des circuits imprimés fabriqués sont minces et de petite taille afin de garantir l’intégrité des signaux.
La meilleure solution aux problèmes de contraintes spatiales des circuits imprimés peut consister à utiliser des circuits imprimés souples (FPC). On les retrouve dans presque tous les appareils que nous utilisons au quotidien, qu’il s’agisse de smartphones, d’appareils photo, de tablettes, d’imprimantes ou d’ordinateurs portables. Il est même possible de les insérer dans le corps humain dans le cas des stimulateurs cardiaques et de divers implants.
11/04/2022