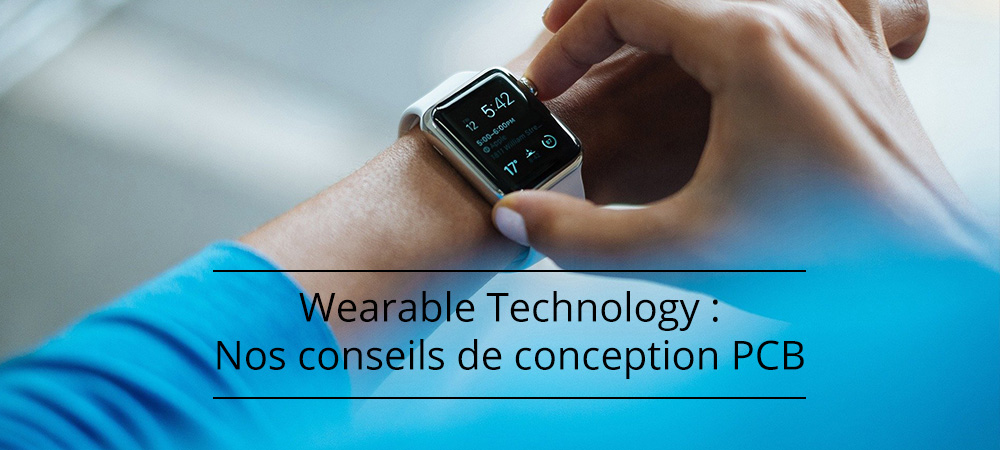
Ces dernières années, les appareils mobiles sont devenus de plus en plus populaires, grâce aux énormes progrès réalisés dans le domaine électronique et à la disponibilité de composants électroniques intégrés permettant une efficacité et des performances croissantes, ainsi qu’une empreinte réduite. Au cœur de chaque appareil portable, que ce soit une montre connectée, un tracker d’activité ou un appareil électro-médical (EMD), il y a un circuit imprimé dont la conception représente l'un des défis les plus difficiles pour les ingénieurs en électronique. La petite taille et le poids, la faible absorption de puissance, la fiabilité et la faible production thermique sont quelques-unes des exigences qui doivent être satisfaites pour créer un appareil portable réussi. En raison de leur taille extrêmement compacte et de leur introduction relativement récente sur le marché, il n'existe toujours pas de véritable norme applicable à la conception de circuits imprimés pour ce type d’appareil. Cependant, il est possible d'appliquer les mêmes techniques et recommandations valables pour des circuits aux caractéristiques similaires, en tirant parti de l'expérience acquise dans le développement et la production de PCB de haute technologie.
Contraintes mécaniques
La différence la plus évidente entre un appareil électronique standard et un appareil portable est certainement la taille. Les appareils portables doivent en fait être très petits et légers, tout en garantissant les mêmes fonctionnalités qu'un appareil plus grand. Minimiser la taille et le poids, tout en choisissant la forme géométrique la plus appropriée, n'est pas une tâche facile. En effet, il est nécessaire d'optimiser la position des composants sur le PCB et d'acheminer efficacement les pistes. Le routage automatique ne convient pas toujours à cette fin, le routage manuel est donc préférable. Le PCB doit pouvoir s'adapter à la forme du contenant. En effet, il est très rare qu’un circuit destiné à ce type d’appareil portable ait une forme rectangulaire rigide ; il est plus courant de rencontrer des circuits multicouches fins aux contours incurvés, conditionnés pour s’adapter et rentrer dans le boitier du produit fini. Le choix des composants joue également un rôle fondamental, préférant les boîtiers avec une empreinte réduite et des boîtiers à profil bas pour minimiser l'épaisseur du produit.
Etroitement lié aux contraintes mécaniques, un autre aspect doit être pris en compte par les concepteurs PCB : l'humidité, qui peut potentiellement endommager ou altérer le fonctionnement des circuits électroniques, surtout s'ils sont de haute impédance. L'appareil mobile, étant la plupart du temps en contact direct avec le corps humain (qui a tendance à libérer de l'humidité), doit avoir un PCB développé et fabriqué pour gérer l'humidité. Selon le cas, les concepteurs peuvent choisir entre une solution essentiellement mécanique, pour laquelle le boîtier ou l'emballage du produit est hermétiquement scellé afin que l'humidité ne puisse pas y pénétrer, ou bien une solution électronique dans laquelle le PCB est tropicalisé avec un revêtement conforme, empêchant l'humidité de pénétrer dans le dispositif.
De plus, la suppression des courants de fuite est particulièrement importante dans les appareils portables où le courant de fonctionnement peut être de quelques nanoampères. Il est également à noter que des composants mal isolés peuvent disperser de l'électricité dans différentes parties de l'appareil, situation à éviter compte tenu de la proximité avec la peau de l'utilisateur. Une mauvaise isolation des composants peut entraîner une électrocution, une fuite de la batterie ou une surchauffe, ce qui peut causer de graves blessures.
Sélection des matériaux PCB
Les couches du PCB, isolées les unes des autres par pré-preg, peuvent être composées de stratifiés de matériau FR4, Polyimide ou Rogers. Étant donné que les appareils portables nécessitent un haut degré de fiabilité et doivent souvent gérer des signaux à haute vitesse et haute fréquence, des matériaux plus avancés sur le plan technologique sont utilisés que le FR4, solution habituellement la plus courante et la plus économique. Le matériau FR4 a une constante diélectrique (Dk) de 4,5, tandis que des matériaux avancés tels que Rogers 4003 et Rogers 4350 ont respectivement un Dk de 3,55 et 3,66. Lors de la manipulation de signaux haute fréquence, il est nécessaire de limiter les pertes de puissance et donc un matériau comme le Rogers 4350 est préférable. De plus, le FR4 a un facteur de dissipation (Df) plus élevé que les matériaux Rogers, en particulier aux hautes fréquences.
Cela signifie qu'en utilisant un stratifié FR4 avec des signaux haute fréquence, des pertes d’insertion non négligeables sont créées, réduisant ainsi la puissance et la capacité de transmission des signaux électriques. Bien que la réduction des coûts de production soit un facteur important dans le développement d'un tel produit, il convient de noter qu'un PCB fabriqué avec des stratifiés Rogers offre des performances et une fiabilité supérieures à celles du FR4 traditionnel, et à un coût global acceptable. Pour les applications grand public, où la concurrence est plus rude, une solution PCB hybride peut toujours être utilisée, obtenue en combinant du FR4 à base d'époxy avec du Rogers et d'autres couches de matériau FR4 standard. Les matériaux Rogers, tels que ceux appartenant à la série 4000, ont également un coefficient de dilatation thermique (CTE) particulièrement stable. Cela signifie que lorsque le PCB subit un cycle de refusion à froid, chaud et très chaud, la dilatation et la contraction du circuit imprimé sont maintenues dans un espace étroit limité, en particulier par rapport à celles du matériau FR4 standard. Cette stabilité est également assurée avec une fréquence et une température croissantes.
En ce qui concerne la structure du PCB, les appareils mobiles utilisent généralement un circuit entre quatre et huit couches, fournissant suffisamment de masse et d'alimentation pour les couches de routage. De cette manière, les phénomènes de diaphonie qui peuvent se produire entre des pistes adjacentes sont minimisés, et la compatibilité électromagnétique est améliorée en réduisant les effets produits par les interférences électromagnétiques (EMI). En ce qui concerne la structure de la carte, le plan de masse est placé à proximité du niveau de distribution d'énergie. Cela réduit pratiquement le bruit à zéro, un aspect très important, en particulier dans les sous-systèmes de radiofréquence (RF).
et recevez un devis pour votre projet de PCBA dans les 10 prochaines minutes !
Conception de circuits imprimés
La réalisation du circuit électronique d'un appareil mobile n'est pas limitée au PCB, et doit prendre en compte d'autres matériaux tels que le tissu, le plastique, les cartes rigides-flexibles et la maille. Contrairement aux circuits imprimés rigides traditionnels, les circuits imprimés flexibles et flexibles rigides sont plus durables et offrent une plus grande résistance à la chaleur, à l'humidité, aux intempéries et aux vibrations. Ces solutions avancées ont non seulement l'avantage d'être flexibles, mais elles occupent également moins d'espace, sont plus légères et plus durables. La figure 1 montre un exemple de PCB rigide-flex adapté aux appareils portables.
Image 1 : Exemple d’un PCB Flex-Rigide.
Cependant, l'utilisation d'un PCB rigide-flex nécessite quelques astuces et précautions. Tout d'abord, il faut porter une attention particulière à l'alignement parfait qui doit exister entre les éléments qui composent le circuit, sachant que le PCB occupera l'espace limité disponible. Un autre aspect particulièrement insidieux concerne la conception de l'empilement (stackup). Les parties flexibles et rigides du circuit doivent être intégrées, prédisant leur position finale dans le dispositif. Cette opération est facilitée par la disponibilité de logiciels appropriés, capables de fournir un modèle 3D du PCB ou de l'ensemble de l'appareil. Les pistes associées aux signaux haute fréquence ne doivent pas être placées à proximité des plans de masse, mais doivent être disposées entre les bus d’alimentation pour lisser la gigue générée par le bruit du signal. Une attention particulière doit être portée au contrôle de l'impédance, en gardant à l'esprit qu’en haute fréquence, une très petite discordance d'impédance peut générer des problèmes de transmission et de réception des signaux, avec une distorsion conséquente.
Dans la conception d'un PCB pour dispositifs portables, les lignes microrubans (microstrip lines), les rubans suspendus (suspended striplines) et les guides d'ondes coplanaires (coplanar waveguides) sont largement utilisés, car ces méthodes de connexion sont capables de supprimer le bruit typique des systèmes RF. En règle générale, il est également conseillé d'introduire des filtres passe-bas, des condensateurs de découplage et suffisamment de plans de masse. Le filtre passe-bas supprime l'ondulation produite par le bruit et réduit les phénomènes de diaphonie ; le condensateur de découplage doit être placé à proximité des lignes d’alimentation. La figure 2 montre le circuit imprimé d'une montre connectée : on y voit une haute densité des composants, y compris le processeur, l'émetteur-récepteur RF, le codec audio, la gestion de l'alimentation, le processeur de bande de base et les multiples antennes sans fil.
Image 2: Le PCB d'une montre connectée (Source: Samsung).