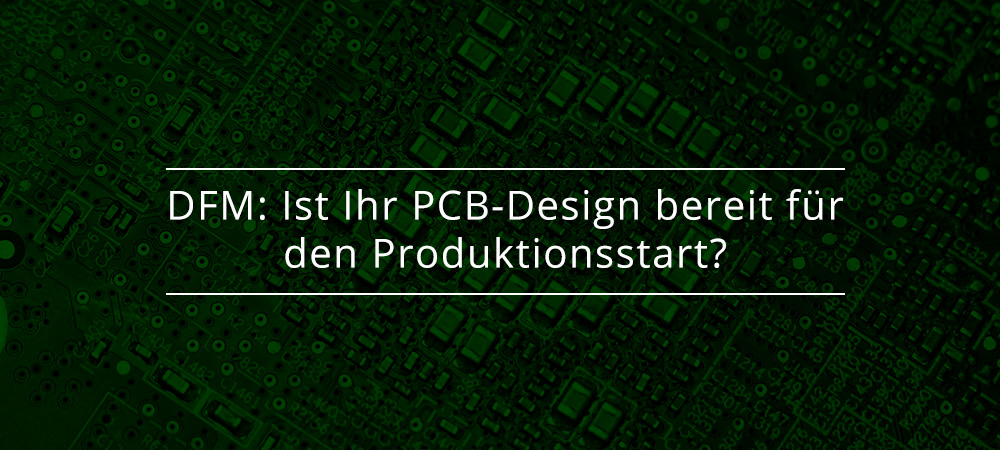
Der Begriff DFM (Design For Manufacturing) bezieht sich auf den Prozess, durch den ein Produkt mit dem spezifischen Zweck entworfen wird, seine Herstellung zu vereinfachen, um ein besseres Produkt zu geringeren Kosten zu produzieren. Idealerweise sollte DFM bereits in der Anfangsphase des Projekts angewandt werden und das gesamte Produktentwicklungsteam und nicht nur die Hardware-Designer einbeziehen.
Mit dem Fortschreiten des Projekts durch die verschiedenen Phasen des Produktlebenszyklus wird jede Änderung immer wichtiger und kostspieliger (jede Änderung macht sie komplexer und teurer), bis zu dem Punkt, an dem die Umsetzung besonders schwierig werden kann. Auf der anderen Seite ermöglicht die Anwendung von DFM in den frühen Phasen der Leiterplattenentwicklung alle möglichen Modifikationen schnell und zu den geringstmöglichen Kosten durchzuführen, wobei die ursprüngliche Leistung des Produkts erhalten bleibt.
Technologie spielt in vielen Aspekten unseres Lebens eine Schlüsselrolle: Smartphones, angeschlossene Uhren, angeschlossene Geräte, angeschlossene Autos... sie alle nutzen intelligente Technologie und Konnektivität. Diese und viele andere Produkte erfordern immer komplexere gedruckte Schaltungen, die zu den geringsten Kosten, in kürzester Zeit und mit hoher Qualität hergestellt werden müssen.
Vorteile des DFM
Da die Leiterplattenherstellung in mehrere Stufen unterteilt ist und um größere Probleme bei der Herstellung (DFM) zu vermeiden, muss im Vorfeld sichergestellt werden, dass eine Leiterplatte nicht von Designproblemen betroffen ist. Während der Entwicklungsphase müssen sich die Konstrukteure mit elektrischen Randbedingungen auseinandersetzen, wie dem Wert der beteiligten Spannungen und Ströme, dem Stromverbrauch und dem Wärmemanagement.
Bei der tatsächlichen Nutzung spielen jedoch andere Faktoren eine Rolle, wie z. B. die Genauigkeit oder Toleranz der Maschinen zur Herstellung von Leiterplatten und die Eigenschaften der verwendeten Materialien. DFM bezeichnet genau den Prozess, mit dem das PCB-Layout organisiert werden kann, um seine Durchführbarkeit zu gewährleisten. Nehmen Sie zum Beispiel einen Restring oder den Kupferpelletbereich, der nach dem Bohren eines Lochs in ihm verbleibt. Die Größe des Rings wird von der Kante des Pads bis zum Rand der Bohrung gemessen und stellt einen grundlegenden Parameter beim Design der Leiterplatte dar, da die darauf abgeschiedene Metallisierung eine elektrische Verbindung auf beiden Seiten ermöglicht.
Bei Mehrschichtplatten müssen die verbleibenden Ringe mit ausreichender Überlappung ausgerichtet werden, um eine Verbindung zwischen verschiedenen Schichten zu ermöglichen. Eine perfekte Ausrichtung gibt es nur in der Theorie: Selbst die modernsten Laserbohrer können nicht 100% genau sein. Das DFM-Verfahren stellt sicher, dass die Breite des Rings eine leichte Fehlausrichtung zwischen den Lagen erlaubt, ohne die elektrische Verbindung zu beeinträchtigen.
Die wichtigsten Vorteile des DFM beim Design und Herstellung von PCB sind:
- Bessere Produktqualität: DFM reduziert die Anzahl der Modifikationen, die erforderlich sind, um das ursprüngliche Design an die Fertigungsprozesse und PCB-Anlagen anzupassen, um eine Beeinträchtigung der Produktqualität zu vermeiden;
- Verkürzung der Markteinführungszeit: Der Herstellungsprozess ist in mehrere Stufen unterteilt, von denen jede potentielle Fehler verursachen kann. DFM trägt dazu bei, Verspätungen durch fehlerhafte Produkte, Fehler und den Zeitaufwand für die Überprüfung von Zeitschriften und Projektunterlagen zu verringern.
- Kostenreduzierung: DFM ermöglicht es PCB-Designern, Leiterplatten zu entwerfen, die auch bei hohen Produktionsvolumen problemlos hergestellt werden können. Die geringere Anzahl von Fehlern, die während des PCB-Herstellungsprozesses entdeckt werden, senkt ebenfalls die Kosten.
DFM versus RDC
PCB-Designer führen oft ein Verfahren durch, das Design Rule Check (DRC) genannt wird. Aber ist es nach der erfolgreichen Durchführung der RDC auch notwendig, DFM durchzuführen? Ja, weil die beiden Verfahren tatsächlich unterschiedlich sind und notwendig sind, um mit der PCB-Produktion zu beginnen. Der RDC ist in der Tat ein automatischer Analyseprozess, der das Projekt mit den von der Gießerei auferlegten Regeln vergleicht. Diese Regeln definieren die minimalen physikalischen Anforderungen an die Leiterplatte, Schichten und Verbindungen, die die Systemleistung beeinflussen können.
Der Zweck des RDC ist es, eventuelle Diskrepanzen oder Fehler aufzudecken. Das DFM hingegen identifiziert alle Aspekte, die während des PCB-Herstellungsprozesses zu Problemen führen können: Wenn der DRC-Prozess einen Fehler feststellt, ist dieser auf jeder Kopie der PCB vorhanden. Die Probleme der DFM hingegen können nur bei bestimmten Einheiten auf der Leiterplatte und selbst nach einer langen Produktionszeit auftreten.
und erhalten Sie innerhalb von 10 Minuten ein Angebot für Ihr PCBA-Projekt
Wie man DFM-Prinzipien auf PCBs anwendet
Obwohl die Herstellungsstandards für PCBs von Hersteller zu Hersteller unterschiedlich sein können, müssen bestimmte allgemeine DFM-Regeln befolgt werden, bevor ein Herstellungsprozess angewendet wird. Um ein PCB-Design für fertigungsreif zu erklären, müssen bestimmte grundlegende DFM-Prinzipien angewendet werden. Hier ist eine Liste der wichtigsten Richtlinien:
- Abstand zwischen den Bauteilen: Bauteile, die auf der Leiterplatte zu nahe beieinander liegen, können Probleme mit den für die Montage verwendeten automatischen Systemen wie Pick-and-Place-Maschinen aufweisen, wodurch die Anpassung der Konstruktion problematisch wird. Das Gleiche gilt für die Steckverbinder, die korrekt positioniert werden müssen, um die Verbindung der Leiterplatte mit den äußeren Elementen zu vereinfachen.
- Positionierung und Drehung der Bauteile: Die Positionierung der Bauteile auf der Leiterplatte kann den Lötprozess beeinträchtigen, insbesondere wenn sie unregelmäßig oder uneinheitlich angeordnet sind. Alle ähnlichen Bauteile müssen in die gleiche Richtung orientiert sein, wobei sicherzustellen ist, dass sie korrekt im Lötofen gelötet wurden.
- Größe der Komponenten-Pads: Bei falscher Größe kann es beim Reflow-Löten zu unregelmäßiger Erwärmung kommen, was wiederum zu einer teilweisen Ablösung der Komponente führen kann. Dieses Phänomen ist als Manhattan- oder Tombstone-Effekt bekannt;
- Säurefänger: Bei der Leiterbahnführung auf Leiterplatten müssen scharfe Ecken vermieden werden, die bei der Reinigung der für das Ätzen der Leiterplatte verwendeten Chemikalien zu ernsthaften Problemen führen können, was eine Verringerung der Dicke der Leiterbahnen selbst zur Folge hat. Durch die Sicherstellung, dass die Winkel zwischen den Leiterbahnen immer weniger als 90 Grad betragen, werden Delaminationsmarkierungen nach der Herstellung der Leiterplatte vermieden;
- Bohrungsoptimierung: Viele PCB-Designs verwenden zu viele verschiedene Bohrungsgrößen, was vermieden werden sollte, um die Produktionskosten zu senken;
- Fehlende Lötstoppmaske zwischen den Pads: Dies kann zu Lötbrücken führen und möglicherweise zwei Pads kurzschließen, die nicht verbunden werden sollten. Prüfen Sie daher immer sorgfältig, ob jedes Pellet genügend Lack enthält, um den erforderlichen Abstand zu gewährleisten;
- Siebdruck auf Pellets: Selbst eine teilweise Überlappung des Siebdrucks auf die Pellets führt beim Löten zu Problemen, die langfristig katastrophale Folgen haben können. Bild 1 zeigt ein Beispiel für eine Überlappung, die vermieden werden muss;
Bild 1: Beispiel für Siebdruck auf Pellets.
- Open-Loop-Kontrolle: Dies geschieht normalerweise, wenn das ursprüngliche Projekt überarbeitet wird, um Änderungen vorzunehmen. Das Erstellen einer neuen Verbindung, ohne die bestehende zu löschen, erzeugt normalerweise eine Endlosschleife;
- Validierung der für das Projekt verwendeten Dateien: Gerber-Dateien müssen besonders sorgfältig geprüft werden, da sie bei der Übersetzung des Projekts in ein physisches Objekt Probleme bereiten können. Für jede Ebene der Leiterplatte wird eine separate Datei benötigt: Das bedeutet, dass Sie die vielen Dokumente im Auge behalten und vermeiden müssen, sie miteinander zu vermischen oder zu verwechseln.