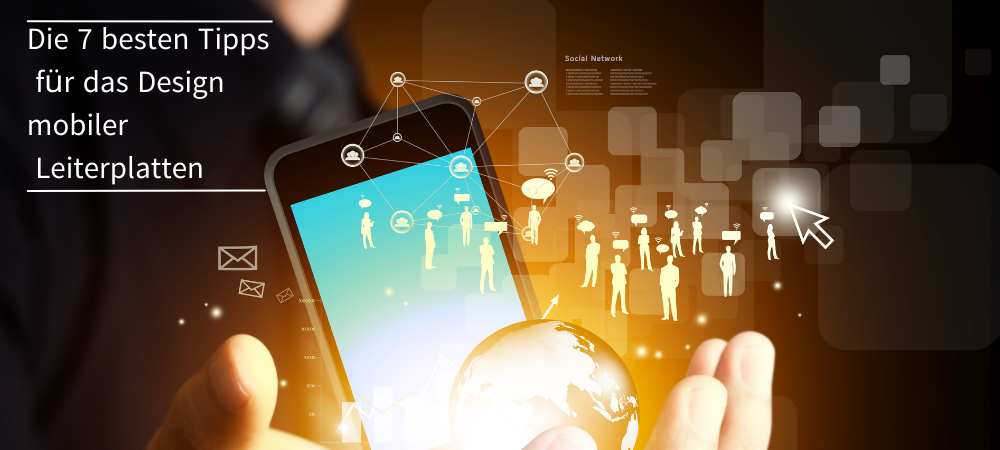
Die fortschreitende Erweiterung der Funktionen, die in die neueste Generation mobiler Geräte integriert sind, stellt immer höhere Anforderungen an das Design von Leiterplatten. Wi-Fi- und Bluetooth-Konnektivität, die Unterstützung von 4G- und 5G-Mobilfunknetzen und die Integration mit einer stetig wachsenden Anzahl von Sensoren stellen für Elektronikdesigner beispiellose technologische Herausforderungen dar. Mobile Geräte, beginnend mit Smartphones, entwickeln sich zunehmend in Richtung höhere Intelligenz, Miniaturisierung und Multifunktionalität, was zunehmend komplexe Leiterplatten erfordert, die diese Anforderungen erfüllen können (der vom Markt auferlegte Trend besteht darin, immer dünnere Geräte mit einer Dicke von normalerweise weniger als einem Zentimeter zu haben).
und erhalten Sie innerhalb von 10 Minuten ein Angebot für Ihr PCBA-Projekt
Technische Herausforderungen
Der Entwicklungstrend aktueller Smartphones erfordert zwangsläufig mehrlagig gedruckte Schaltungen (bestehend aus 10 oder mehr Lagen), um das Motherboard und eine oder mehrere Leiterplatten mit einer reduzierten Anzahl von Schichten für Zusatzplatinen herzustellen, möglicherweise mit starr-flexiblen Leiterplatten. Der zunehmende Einsatz von SIP(System-in-Package)-Komponenten und Multi-Core-SoCs (System-on-Chip), ebenfalls mit 64‑Bit-Architektur erhältlich, sowie die Reduzierung des Kontaktabstands von 0,4 mm auf 0,35 mm, sind wahrscheinlich dazu bestimmt, dem Wachstum der Lagenanzahl entgegenzuwirken, wenn nicht sogar zu deren Reduzierung zu führen.
Designer von mobilen Leiterplatten müssen die technologischen Aspekte schon in den ersten Phasen der Entwicklung genau berücksichtigen. Die wichtigsten Faktoren, die es beim Entwurf dieser Leiterplattenklasse zu berücksichtigen gilt, sind:
- Definition des Leiterplattenlayouts, der Positionierungsbohrungen und der für die automatische Produktion und Montage erforderlichen Bezugsmarken
- Definition des in der Produktionsphase der Leiterplatte erforderlichen Panels
- Auswahl der für die Substrate verwendeten Materialien, Auswahl der richtigen Komponenten und deren Verpackung
- Positionierung der Komponenten und relativer Abstand zwischen diesen
1 – Layout
Die Positionierung muss bei den höheren Leistungskomponenten beginnen, die so nah wie möglich an den begleitenden Teilen platziert werden müssen, dass möglichst kurze Hochstromleiterbahnen entstehen. Außerdem müssen Sie einen gewissen Mindestabstand zu den Leiterbahnen einhalten, auf denen Hochgeschwindigkeitssignale übertragen werden, da sie empfindlicher auf Störungen und Nebensprechphänomene reagieren.
Sie können zum Beispiel für die Positionierung der Komponenten in der folgenden Reihenfolge vorgehen: Steckverbinder, Stromversorgungskomponenten, empfindliche Komponenten, kritische Komponenten, verbliebener Teil der Komponenten. Alle ähnlichen Komponenten sollten in die gleiche Richtung ausgerichtet sein, um die Wahrscheinlichkeit von Lötproblemen zu verringern. Platzieren Sie auf der gelöteten Seite der Platine keine anderen Komponenten in der Nähe der Durchkontaktierungsbohrungen (PTH), die sich auf der gegenüberliegenden Seite der Platine befinden. SMDs (Surface Mount Components) sollten auf der gleichen Seite der Leiterplatte konzentriert werden; dieselbe Regel sollte auf PTH-Komponenten angewendet werden, was den Bestückungsaufwand vereinfacht und reduziert.
Fahren Sie nach dem Positionieren der Komponenten mit dem Verlegen der Leiterbahnen in Bezug auf Leistung, Signale und Masse fort. Das Leiterbahnrouting sollte nach Leistungspegeln und Störanfälligkeit priorisiert werden. Die Leistungskomponenten sollten zur besseren Wärmeableitung Masse- oder Stromversorgungslagen verwenden, während die Signalspuren so kurz und gerade wie möglich sein sollten, um zu vermeiden, dass sie über lange Strecken parallel verlaufen, um Kopplungsphänomene zu vermeiden. Entkopplungskondensatoren sollten in der Nähe der (oder unter den) Netzteilstifte positioniert werden, damit sie alle falschen Leistungsspitzen absorbieren können.
Signale tragende Leiterbahnen, die ein hohes Maß an Isolation erfordern, sollten auf separaten Lagen verlegt werden, möglicherweise orthogonal zueinander, wobei sie durch eine Bodenebene getrennt sind. Die orthogonale Positionierung der Leiterbahnen minimiert die kapazitive Kopplung, während die Bodenebene eine elektrische Abschirmung bietet. Diese Technik wird häufig verwendet, um Leiterbahnen mit kontrollierter Impedanz zu erhalten, wobei die charakteristische Impedanz an jedem Punkt der Leiterbahn konstant bleibt (z. B. 50 Ω). Zwei sehr häufige Arten impedanzgesteuerter Leiterbahnen sind Mikrostreifen und Streifenleitungen, die trotz unterschiedlicher geometrischer Strukturen ähnliche Ergebnisse liefern. Die Impedanzregelung, die über eines der vielen online verfügbar Tools durchgeführt werden kann, erfordert oft die Notwendigkeit, die Länge der Leiterbahnen auszugleichen. In extremen Fällen kann dies die Einführung geeigneter „Serpentinen“ auf der Leiterplatte erfordern, wie in Abbildung 1 gezeigt.
Abbildung 1: Einführung von „Serpentinen“ zum Ausgleich der Leiterbahnlänge
2 – Trennung
Der HF-Abschnitt einer mobilen Leiterplatte muss angemessen getrennt und von den Stromversorgungs- und digitalen oder analogen Niedrigleistungsabschnitten isoliert sein. Empfindliche analoge Signale sollten auch so weit entfernt wie möglich von digitalen Hochgeschwindigkeits- und HF-Signalen gehalten werden. Digitale und analoge Signale sollten ebenfalls über eigene Masseanschlüsse verfügen.
Analoge und digitale Schaltungen sollten, wo immer möglich, getrennt gehalten werden. Tatsächlich könnten die schnell ansteigenden Flanken der digitalen Signale Stromspitzen verursachen und Rauschen erzeugen. Zwei Faktoren, die möglicherweise analoge Schaltungen beschädigen können. Abbildung 2 zeigt ein Beispiel dafür, wie die Trennung zwischen dem analogen und dem digitalen Abschnitt einer Leiterplatte durchgeführt werden kann.
Abbildung 2: Trennung zwischen analogem und digitalem Abschnitt (Quelle: Altium)
3 – Durchkontaktierungen und Bezugsmarken
Hochstromspuren, insbesondere solche, die mehrere Lagen durchlaufen, sollten mindestens zwei bis vier Durchgangsbohrungen umfassen. Dies verbessert die Wärmeableitung und reduziert sowohl induktive als auch Widerstandsverluste. Durch die Verwendung größerer Bohrungen kann die Platine höheren Strömen standhalten und verbessert die Wärmeleitung. Bei Bahnen mit hohen Stromstärken ist es außerdem besser, mehrere Bohrungen anstelle einer einzelnen Bohrung zu verwenden.
Im Allgemeinen sollte jede Seite der Leiterplatte mindestens zwei Bezugsmarken enthalten. Diese sollten in der Regel kreisförmig mit einem Durchmesser von 1 mm (40 mil) sein. Darüber hinaus sollten die Bezugsmarken die gleiche Farbe für den inneren Hintergrund haben und somit kompatibel mit der übrigen Kupferbeschichtung bleiben.
4 – Wärmemanagement
Wärmemanagement ist ein wichtiger Aspekt, der besondere Aufmerksamkeit verdient, da ein unsachgemäßes Wärmemanagement die Leiterplatte schwächen oder sogar beschädigen könnte. Der Designer sollte daher (durch Durchsicht der entsprechenden Datenblätter) die Wärmewiderstandwerte für jede Komponente bewerten und bestimmen, welche Komponenten die meiste Wärme abführen. Es muss dann sichergestellt werden, dass die kritischsten Komponenten in einem ausreichend großen Abstand von jenen Bauteilen positioniert werden, die Wärme erzeugen.
Die Verwendung größerer Bahnen ist der erste Trick bei der Bekämpfung der Wärmeentwicklung. Leistungskomponenten, die einer größeren Überhitzung ausgesetzt sind, sollten in der Mitte der Platine positioniert werden, um die Wärme abzuleiten und gleichzeitig von anderen heißen Komponenten getrennt zu bleiben. Wenn die Größe des Designs es zulässt, sollten schließlich auch Kühllüfter, Kühlkörper, feste Boden- und Stromversorgungslagen und eine ausreichende Anzahl von thermischen Durchkontaktierungen berücksichtigt werden. Es kann auch notwendig sein, die Dicke der Laminate zu erhöhen oder verschiedene Materialien mit besserer Festigkeit und Wärmeableitung zu verwenden.
5 – Erdebenen
Eine Erdebene bietet eine gemeinsame Referenzspannung, bietet Abschirmung, ermöglicht die Wärmeableitung und reduziert die parasitäre Induktivität (obwohl die parasitäre Kapazität zunimmt). Idealerweise sollte jede Leiterplatte mindestens über eine Lage verfügen, die vollständig der Erdebene gewidmet ist. Die besten Ergebnisse werden erzielt, wenn diese Ebene fest ist, das heißt, ohne Unterbrechungen.
Da Erdebenen in der Regel eine große Oberfläche der Leiterplatte belegen, ist ihr Widerstand minimal. Bei hohen Frequenzen nimmt der Strom den Pfad mit dem niedrigsten Widerstand, während bei hohen Frequenzen der Strom dem Pfad mit der niedrigsten Impedanz folgt. Die Erd- und Stromversorgungslagen sollten symmetrisch, zentriert und in den innersten Lagen der Leiterplatte positioniert sein.
6 – Materialien
Die Technologie, die für die Herstellung von mehrlagigen Leiterplatten verwendet wird, ist in medizinischen Anwendungen weit verbreitet. Bei der Herstellung einer mehrlagigen Leiterplatte wird ein subtraktives Verfahren angewendet, um die Leiterplattenlagen zu erzeugen. Die Verschaltung zwischen den Lagen wird durch Stufen der Laminierung, des mechanischen Bohrens, der chemischen Kupferbeschichtung und der Kupferbeschichtung erreicht. Der Prozess wird durch die Erstellung der Lötmaske, der Schutzbeschichtung der Leiterplatte (Conformal Coating) und des Siebs abgeschlossen.
Die heutigen mehrlagigen Leiterplatten sind außergewöhnlich dünn, haben eine sehr geringe Leiterbahnbreite und einen sehr geringen Leiterabstand und zeichnen sich durch eine besonders hohe Komponenten- und Leiterplattendichte aus.
7 – Panel
Ein guter Leiterplattendesigner sollte die Freigabe eines Paneldesigns für die Montagephase in die Entwicklung einbeziehen. Sobald das Leiterplattendesign abgeschlossen ist, besteht der nächste Schritt darin, die leiterplattenbezogenen Informationen an ein Fertigungsunternehmen zu senden, zusammen mit einer Spezifikation für das Paneldesign, um sicherzustellen, dass das Leiterplatten-Empfangsformat wie beabsichtigt ist. Diese Informationen sollten Folgendes umfassen:
- die maximale Plattengröße, die von den Produktionsmaschinen verwaltet werden kann
- zusätzliche Bezugsmarken, damit die visuellen Ausrichtungssysteme der Maschine genau wissen, wo sich die Leiterplatte befindet. Die Standardpraxis besteht darin, in drei der vier Ecken auf beiden Seiten der Leiterplatte drei Bezugsmarken am Panel hinzuzufügen, damit die Maschine feststellen kann, ob die Leiterplatte richtig geladen wurde oder nicht.
- Fügen Sie, falls von der Maschine erforderlich, spezielle Bohrungen (Werkzeugbohrungen) in der Nähe der Kanten der Platte ein, um die Verarbeitung der Leiterplatte zu ermöglichen.
- Winkeln Sie die Ecken der Platte so ab, dass die Ecken nicht brechen können, wenn die Leiterplattenpanels vakuumverpackt sind.
Abbildung 3 zeigt ein Beispiel für ein korrekt gestaltetes Panel.
Abbildung 3: Beispiel eines Leiterplattenpanels
26/11/2021