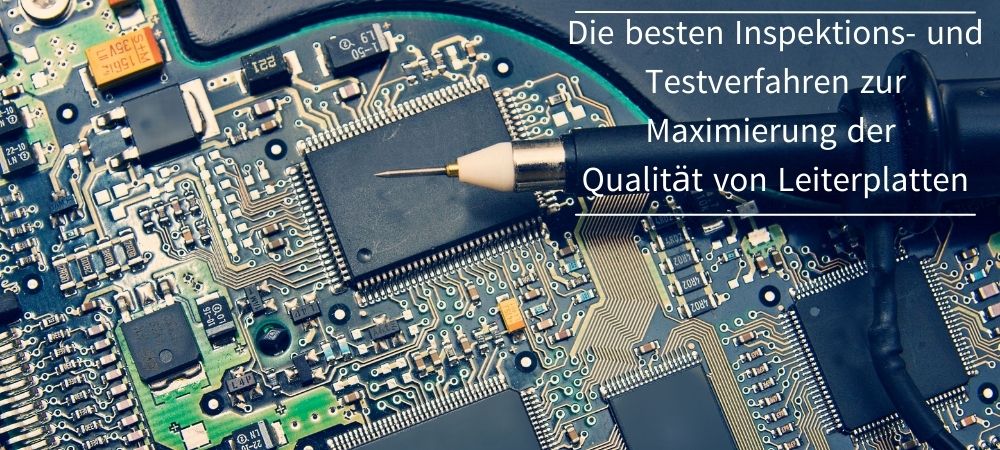
Inspektion und Test decken zwei wesentliche Phasen der Herstellung jeder Leiterplatte ab und ermöglichen so eine objektive Bewertung der Qualität des Endprodukts. Selbst wenn Ingenieure alle Regeln und Ratschläge für ein gutes Design befolgen, besteht immer das Risiko von Störungen, Bugs oder menschlichen Fehlern. Die Identifizierung und Lösung dieser Probleme, die vor dem Erreichen der letzten Entwicklungsstufe der Leiterplatte durchgeführt wird, ist eine grundlegende Anforderung, um die Leistung, Funktionalität und Zuverlässigkeit des Produkts sicherzustellen.
Heute gibt es Geräte, die vollautomatische Leiterplattentests durchführen können und direkt in der gleichen Fertigungsumgebung wie die Leiterplatte ausgeführt werden können. Zu den derzeit verfügbaren Haupttechniken gehören Funktionstests, optische Untersuchung mit Kameras und Röntgeninspektion. Es besteht auch die Möglichkeit, die Leiterplatte nach Durchführung der Bestückungsphase zu testen, wobei alle Komponenten richtig positioniert und gelötet sein müssen.
Die optische Inspektion scannt die Leiterplatte auf mögliche Lötprobleme, wie Brücken, Kurzschlüsse oder schlechte elektrische Verbindungen. Diese Systeme verwenden hochauflösende mobile Kameras, die oft sogar falsch positionierte oder fehlende Komponenten erkennen können. Einige Testsysteme verwenden auch eine 3‑D-Röntgeninspektion, die in der Lage ist, Probleme zu erkennen, die bei der standardmäßigen optischen Inspektion nicht sichtbar sind. So können Röntgensysteme beispielsweise Unvollkommenheiten beim Löten unter integrierten BGA-Schaltungen (Ball Grid Array) und Flip-Chips erkennen (ein Beispiel für ein Flip-Chip-Paket ist in Abbildung 1 dargestellt).
Abbildung 1: eine integrierte Schaltung mit einem Flip-Chip-Gehäuse
und erhalten Sie innerhalb von 10 Minuten ein Angebot für Ihr PCBA-Projekt
Automatische optische Inspektion
Die automatische optische Inspektion, auch AOI genannt, verwendet das optische Signal, das von einer einzelnen Kamera (2‑D-Sicht) oder von mehreren Kameras (3‑D-Sicht) erkannt wird, um Fehler in Leiterplatten mit einer Auflösung von bis zu wenigen µm zu überwachen. Diese Methode liefert Ergebnisse, die nur auf Leiterplatten gültig sind, bei denen Lötpunkte, Kontakte, Pads und zu überwachende Leiterbahnen optisch steuerbar sind. Die AOI-Technik erweist sich auch als sehr nützlich für die Früherkennung von Bestückungsproblemen wie Kurzschlüsse, Stromkreisunterbrechungen, Ausdünnungslöten, Kratzern auf Leiterbahnen und mehr.
Die hochauflösenden Bilder, die von 2‑D−/3‑D-Kameras aufgenommen werden, werden mit Bildern von einer Modellplatine (auch „goldene Platine“ genannt) oder einer Bilddatenbank mit guten und defekten Platinen verglichen. Die AOI-Technik ist in der Lage, alle Prüfungen (die sonst manuell durchgeführt werden müssten) vollautomatisch, präzise und schnell durchzuführen. Darüber hinaus ist es möglich, die korrekte Positionierung der Komponenten nach der Bestückungsphase sowohl auf der Leiterplattenebene als auch entlang der vertikalen Achse zu erkennen (die AOI-3‑D-Technik ermöglicht auch die Erfassung der Komponenten). AOI hat den Vorteil, dass es direkt am Ende der PCB-Produktionslinie angehängt werden kann, um mögliche Fehler frühzeitig zu erkennen. Da es sich jedoch um ein passives Verfahren handelt, kann es nur Defekte auf der Leiterplattenoberfläche erkennen.
Röntgeninspektion
Im Vergleich zu anderen Prüfmethoden erkennt die AXI(Automatic X-Ray)-Technologie PCB-Unvollkommenheiten, die mit dem bloßen Auge oder mit einem optischen AOI-System nicht sichtbar sind. Röntgenstrahlen können tatsächlich sowohl die Leiterplattenlagen als auch das Komponentenpaket durchdringen und so sehr detaillierte 2‑D- oder 3‑D-Bilder erzeugen. Dies ermöglicht zum Beispiel die Erkennung von Lötproblemen auf Kugelgitteranordnungen (BGA) oder auf versteckten Pads. Bei der Herstellung kleiner Leiterplattenchargen oder während der Prototypingphase reicht es oft aus, nur die Komponenten mit nicht sichtbaren Pads einer Röntgeninspektion zu unterziehen.
Während dies wahrscheinlich die beste Technik ist, welche die besten Ergebnisse liefert, erfordert AXI ordnungsgemäß geschultes Personal und es ist ein langer und teurer Prozess. Dies rechtfertigt den Einsatz für Leiterplatten, die in großem Maßstab hergestellt werden oder für besonders kritische und komplexe Anwendungen. Für BGA-Komponenten bietet diese Technik hervorragende Ergebnisse (ein Beispiel ist in Abbildung 2 zu sehen), wodurch die Prüfung der versteckten Lötpunkte zwischen der Komponente selbst und der Leiterplattenoberfläche ermöglicht wird.
Abbildung 2: Röntgeninspektion einer BGA-Komponente
Inspektion mit Infrarotstrahlen
Bei der Inspektion einer Leiterplatte mit Infrarotstrahlung (auch Thermografie genannt) wird die von den Komponenten und der Leiterplatte selbst abgegebene Wärme genutzt. Diese Technik ist besonders relevant für Leistungsanwendungen, bei denen die beteiligten Ströme höher sind. Infrarotthermografie, die mit speziellen Wärmebildkameras (wie FLIR) durchgeführt werden, können Informationen liefern, die sonst bei optischen Inspektionen nicht verfügbar sind.
Bestimmte Leiterplattendefekte wie beispielsweise unzureichende Lötarbeiten können den elektrischen Widerstand an bestimmten Stellen des Stromkreises erhöhen, was zu einem Temperaturanstieg führt, der von einer Infrarotkamera erkannt werden kann.
Ein häufig verwendetes Verfahren in der Thermografie ist die Bildsubtraktion. Die entsprechende Software erfasst ein Bild vor dem Einschalten des Geräts und erstellt so ein ideales Wärmeprofil. Dieses Referenzbild wird dann von den nachfolgenden Bildern subtrahiert, die nach dem Einschalten des Geräts erhalten werden, wodurch die statisch reflektierten Temperaturwerte eliminiert werden und nur die realen Temperaturdeltas aufgrund der Erwärmung der Platine und ihrer Komponenten übrig bleiben.
Es ist wichtig zu betonen, dass sowohl die Thermografie als auch die Röntgeninspektion es ermöglichen, mögliche Fälschungen oder das unbefugte Klonen der Leiterplatte zu erkennen.
In-Circuit-Test
In-Circuit-Testing (auch bekannt als ICT) ist ein vollautomatischer Test, der in der Lage ist, Fehler in der Leiterplattenfertigung oder in der Bestückung durch einen genauen Überprüfungsprozess mit dem Schaltplan zu erkennen.
Durch die Platzierung der Leiterplatte auf einem Nagelbett greift dieser Test auf bestimmte Punkte der Schaltung zu und misst die Leistung jeder einzelnen Komponente völlig unabhängig von den anderen daran angeschlossenen Komponenten. Parameter wie Widerstand, Kapazitiv, Impedanz und mehr können zusammen mit dem Betrieb einiger analoger Komponenten wie Operationsverstärker gemessen werden. Es ist auch möglich, das Verhalten einiger digitaler Schaltungen zu messen, obwohl ihre Komplexität in der Regel eine vollständige Überprüfung unwirtschaftlich macht. Mithilfe der ICT-Technik ist es möglich, einen vollständigen Test der Leiterplatte durchzuführen, um sicherzustellen, die Schaltung korrekt ausgeführt wurde. Zu den festgestellten Defekten gehören Kurzschlüsse und Stromkreisunterbrechungen, fehlende oder falsch ausgerichtete Komponenten, Lötfehler und mehr. Für große Leiterplattenchargen ist es möglich, kundenspezifische Testmasken zu erstellen, um ICT schneller und effizienter durchzuführen. Ein weiterer Vorteil ist die hohe Fehlerabdeckung, die bis zu 98 % erreichen kann.
Der Hauptnachteil dieser Technik sind die hohen Kosten, die nur für die Großproduktion gerechtfertigt sind. Hinzu kommt die Notwendigkeit, ein spezielles Nagelbett für jede Leiterplatte vorzubereiten, um die Möglichkeit, die Überprüfung nur an bestimmten Punkten der Leiterplatte durchzuführen, die den vom Designer bereitgestellten Testpunkten entsprechen.
Flying-Probe-Test
Im Vergleich zum In-Circuit-Test hat der Flying-Probe-Test den Vorteil, dass er kostengünstiger ist. Bei dieser Technik wird eine mobile Sonde verwendet, die vollständig automatisch und konfigurierbar in Kontakt mit den entsprechenden elektrischen Punkten von Interesse auf der Leiterplatte platziert wird. Zu diesen Punkten gehören Komponentenstifte, Durchkontaktierungen, Pads und mehr. Im Vergleich zu ICT hat der Flying-Probe-Test den Vorteil, dass eine große Anzahl von Punkten auf der Leiterplatte getestet werden kann und nicht nur die vom Designer auf der Leiterplatte bereitgestellten Testpunkte. Darüber hinaus ist kein maßgeschneidertes Gerät erforderlich (z. B. das Nagelbett) und Änderungen an den Komponenten oder am ursprünglichen Leiterplattendesign erfordern lediglich ein Software-Update.
Dank der hohen Anzahl an verifizierten Punkten garantiert der Flying-Probe-Test eine höhere Fehlerabdeckung als der ICT. Es handelt sich jedoch um einen viel langsameren Prozess, der für die große Leiterplattenproduktion inakzeptabel werden kann. Abbildung 3 zeigt Geräte für die automatische Leiterplattenprüfung mit einer fliegenden Sonde.
Abbildung 3: Leiterplattenprüfung mit fliegender Sonde
Funktionstest
Der Funktionstest einer Leiterplatte wird in der Regel in der Endphase des Projekts durchgeführt und überprüft die Funktionalität und das Verhalten der Leiterplatte unter verschiedenen auf dem Prüfstand simulierten Betriebsbedingungen. Sehr oft wird der Funktionstest durchgeführt, um das vom Kunden angegebene spezifische Verhalten zu überprüfen und die Leiterplatte unterschiedlichen elektrischen und Umweltbelastungen auszusetzen.
Mit diesem Test soll sichergestellt werden, dass der Prüfling (DUT) wie erwartet funktioniert. Je nach Komplexität des Projekts und den zu testenden Anforderungen kann der Funktionstest von einem einfachen Netzteiltest (Strom ein/Strom aus) bis hin zu einem kompletten Test mit spezifischen Kommunikationsprotokollen und spezieller Software zum Testen reichen. Aufgrund seiner Flexibilität können Funktionstests als Ersatz für teurere Testverfahren eingesetzt werden. Durch eine genaue Simulation der tatsächlichen Betriebsumgebung liefert der Funktionstest sofortige Ergebnisse zur Qualität des Projekts und aus diesem Grund wird es zunehmend in der Produktion von Kleinserien eingesetzt, wodurch sichergestellt wird, dass jede einzelne Platine, welche die Produktionslinie verlässt, für den Feldeinsatz bereit ist.
Obwohl es sich um ein relativ kostengünstiges Verfahren handelt und für jede Art von Leiterplatte anwendbar ist, bietet der Funktionstest eine Fehlerabdeckung, die strikt von den während des Tests durchgeführten Prüfungen abhängt. Außerdem kann die Platine, die hohen Belastungen ausgesetzt ist, kurz nach bestandenen Funktionstests scheitern.
Burn-in-Test
Der Burn-in-Test, der einige Punkte mit dem Funktionstest gemeinsam hat, prüft die Leistung einer Leiterplatte und sucht nach nicht offensichtlichen Defekten, bevor die Platine zum Einsatz kommt. Während der Burn-in-Tests werden die Platinen extremen Bedingungen ausgesetzt, welche die Nennbetriebsbedingungen überschreiten. Ziel ist es, mögliche Ausfälle frühzeitig zu erkennen und den Gerätebetrieb unter hoher Last zu testen und so mögliche Probleme zu antizipieren, die während des realen Gebrauchs auftreten können. Im Gegensatz zu anderen Inspektionsmethoden, bei denen nur die Indikatoren für potenzielle Ausfälle überprüft werden, simuliert der Burn-in-Test extreme Betriebsbedingungen, die mögliche Ausfälle auslösen können.
Zu diesen extremen Betriebsbedingungen gehören in der Regel Schwankungen von Temperatur, Spannung, Strom, Betriebsfrequenz oder anderen für den Prüfling relevanten Betriebsbedingungen. Die Ergebnisse dieses Tests sind sehr nützlich für Designer, die genaue Informationen erhalten können, um die Ursache der Fehler zu verstehen und die Design- oder Fertigungsprozess zu optimieren.
10.12.2021