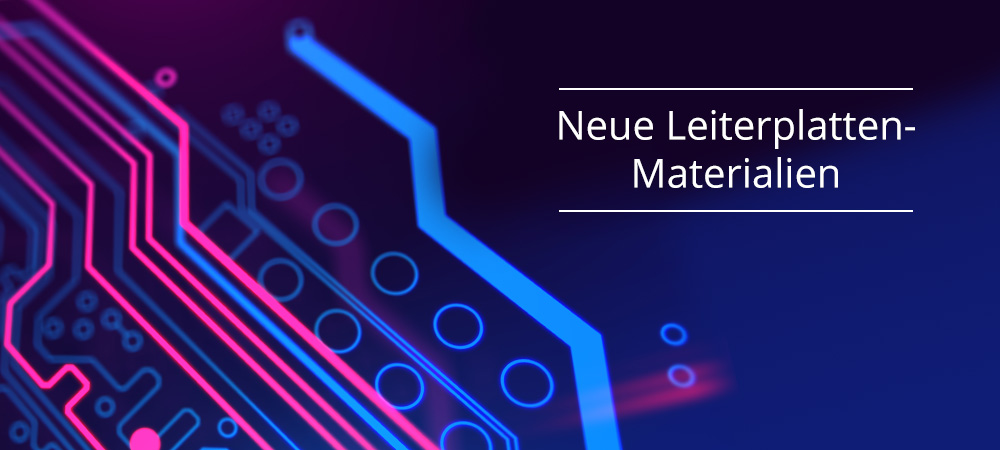
In den letzten Jahren haben wir bedeutende Fortschritte bei verschiedenen elektronischen Anwendungen erlebt, die zur Einführung immer innovativerer Technologien geführt haben. Zu den Sektoren, in denen die größte Entwicklung erzielt wurde, gehören die mobile Kommunikation (Smartphones und Tablet-PC), tragbare Geräte (einschließlich Geräte für virtuelle Realität und Augmented Reality) und elektromedizinische Geräte. Weitere wichtige Fortschritte wurden in der Automobil- und der Luft- und Raumfahrtindustrie erzielt. Der Innovationsschub in Verbindung mit der Verfügbarkeit neuer Fertigungstechnologien ermöglichte die Einführung neuer Materialien für die Herstellung immer dünnerer, leichter und, falls erforderlich, flexibler gedruckter Leiterplatten, die in der Lage sind, elektrische Signale mit immer höherer Geschwindigkeit und Frequenz zu übertragen.
Der Bedarf für neue Materialien
Traditionelle Materialien und Substrate bestehen aus gewebtem Glasgewebe, Kunststoff (Harz) und Kupfer. Bei der Herstellung von Leiterplatten kommen verschiedene Arten von Harz und Glas zum Einsatz und die Art und Weise, wie sie kombiniert werden, beeinflusst die elektrischen und mechanischen Eigenschaften des Materials. Die beiden wichtigsten elektrischen Eigenschaften, die ein Material definieren, sind die Dielektrizitätskonstante (Dk) und die Verlusttangente (auch als Verlustfaktor oder Df bekannt), die beide erheblich von der Temperatur und der Frequenz abhängen, denen das Material oder Substrat ausgesetzt ist. Die Dielektrizitätskonstante gibt die Ladungsmenge an, die zwei Leiter halten können, wenn eine bestimmte Spannung an sie angelegt wird. Die Konstante Dk bestimmt auch die Geschwindigkeit, mit der ein bestimmter Strom in einem Leiter fließt. Der Verlusttangens liefert stattdessen ein Maß für die vom dielektrischen Material absorbierte elektromagnetische Energie.
Die modernsten elektronischen Anwendungen erfordern Materialien mit anderen Eigenschaften als die Materialien und Substrate, die üblicherweise bei der Herstellung von Leiterplatten eingesetzt werden. Auch wenn die Gründe, die für die Auswahl ausschlaggebend sind, vielfältig sind und strikt von der spezifischen Anwendung abhängen, umfasst eine mögliche Liste:
- die Notwendigkeit, elektrische Signale mit immer höheren Frequenzen zu verwalten;
- die Erhöhung der Integrationsdichte von elektronischen Komponenten;
- die Verfügbarkeit neuer Gehäuse für viele Komponenten, mit Auswirkungen auf die Routing-Techniken;
- die Notwendigkeit, Leistungsverluste zu minimieren, insbesondere bei Anwendungen mit geringer Leistung oder batteriebetriebenen Anwendungen;
- die Notwendigkeit, die Leiterplatte mit einem angemessenen Wärmemanagement auszustatten, um die abzuführende Wärme zu minimieren;
- die Notwendigkeit, die Gerätekonnektivität (typischerweise drahtlos) zu verwalten, ein kritischer Aspekt für das Leiterplatten-Design.
Der Anstieg der Frequenz der Signale, die sich über eine Leiterplatte ausbreiten, scheint unaufhaltsam zu sein. Diese Eigenschaft in Verbindung mit immer niedrigeren Versorgungsspannungen (insbesondere bei hochintegrierten digitalen Komponenten wie MCU, SoC und FPGA) führt zu großen Problemen bei der Signalintegrität. Anwendungen dieser Art umfassen Glasfaserübertragungskarten und -geräte, Computer und die meisten eingebetteten Systeme, die mit einer Verarbeitungseinheit ausgestattet sind.
und erhalten Sie innerhalb von 10 Minuten ein Angebot für Ihr PCBA-Projekt
Neue Materialien und Substrate
Auf der Grundlage der im vorigen Absatz genannten Überlegungen können wir die beiden Schlüsselfaktoren identifizieren, die die Auswahl des für die spezifische Anwendung am besten geeigneten Materials und Substrats bestimmen: die maximale Leistung und die Wärmemenge, die die Leiterplatte aushalten kann. Obwohl diese Regel allgemein gilt und auf alle Arten von Materialien anwendbar ist, lassen sich durch den Einsatz folgender innovativer Materialien größere Vorteile erzielt werden:
- Fluorpolymere: Leiterplatten, die mit Substraten aus diesem Material hergestellt werden, verfügen über eine hohe Beständigkeit gegen Korrosion, mechanische Belastung und hohe Temperaturen. Darüber hinaus besitzen Fluorpolymere hervorragende mechanische Eigenschaften hinsichtlich Verschleißfestigkeit, geringer Haftung und langer Lebensdauer. Unter Berücksichtigung der nicht zu vernachlässigenden Kosten eignet sich dieser Materialtyp für die Fertigung von Leiterplatten für Anwendungen in der medizinischen, pharmazeutischen und Lebensmittelindustrie;
Polyimid: dieses Material, auch als PI bekannt, hat in letzter Zeit dank der zunehmenden Beliebtheit von flexiblen und Starrflex-Leiterplatten einen großen Erfolg errungen. Diese Leiterplatten revolutionieren verschiedene elektronische Anwendungen, indem sie ehemals kritische elektrische Verbindungsprobleme auf effektive und einfache Weise lösen, insbesondere in Bezug auf die Zuverlässigkeit. Diese Aufgabe wird durch die Flexibilität erzielt, sich in engen oder unregelmäßig geformten Räumen zu biegen und zu wickeln. Im Gegensatz zu herkömmlichen starren Leiterplatten lassen sich flexible Leiterplatten biegen, ohne die Übertragung der von ihnen übertragenen elektrischen Signale zu verändern. Flexible Leiterplatten, die aus einem dünnen Polyimidfilm bestehen, der auf ein Substrat mit Leiterbahnen aufgebracht ist, kommen häufig in Smartphones, tragbaren Geräten, elektromedizinischen Geräten und überall dort zum Einsatz, wo flexible Verdrahtungslösungen benötigt werden, die für enge Räume geeignet sind. Neben der mechanischen Flexibilität weist das so erhaltene Material eine ausgezeichnete Beständigkeit gegen Wärme und atmosphärische Einflüsse auf. Starrflex-Leiterplatten, wie beispielsweise in Abbildung 1, werden durch Kombination eines starren Teils mit einem flexiblen Teil hergestellt. Diese Lösung verursacht derzeit höhere Kosten als herkömmliche Leiterplatten und kommt in der Automobil- und Motorradindustrie, im militärischen Bereich sowie in der Luft- und Raumfahrt zum Einsatz.
Abbildung 1: Eine starrflexible Leiterplatte.
- Acrylatklebstoffe: hoch geschätzt, da sie auch nach der Polymerisation ihre Formbarkeit behalten, daher stellen diese Materialien eine ausgezeichnete Lösung für alle dynamischen Anwendungen dar. Acrylatklebstoffe haben einen höheren Ausdehnungskoeffizienten als andere Materialien, die als Leiterplatten-Substrate verwendet werden. Darüber hinaus beginnen Acrylatklebstoffe bei Temperaturen nahe 180°C weich zu werden, was zu einer potenziellen Ablösung von Leiterplattenschichten in Kontakt mit Leiterbahnen führen kann. Wenn eine hohe Flammbeständigkeit erforderlich ist, müssen dem Substrat chemische Flammhemmer zugesetzt werden, dies birgt jedoch das Risiko, die dynamischen Eigenschaften des Materials zu verringern;
- Epoxidklebstoffe: Im Gegensatz zu Akrylatklebstoffen polymerisieren Epoxidklebstoffe zu einem starren Material und sind daher für viele dynamische Anwendungen ungeeignet. Aufgrund ihres relativ niedrigen Ausdehnungskoeffizienten und ihrer hohen Klebkraft stellen sie jedoch eine ausgezeichnete Lösung für den Aufbau mehrlagiger Leiterplatten dar, die hohen Betriebstemperaturen standhalten können. Epoxidklebstoffe werden dank ihrer hohen Chemikalienbeständigkeit und ihrer Fähigkeit, Feuchtigkeit zu absorbieren, häufig als Substrate für Leiterplatten verwendet, bei denen Sensoren in Kontakt mit Feuchtigkeit kommen können, wie z.B. in der Medizin und im Gesundheitswesen sowie in vielen Fitness- und tragbaren Geräten;
- Flüssigkristallpolymere: auch als LCP (eng. Liquid Crystal Polymers) bekannt, werden häufig bei der Herstellung von Multilayer-Leiterplatten verwendet, bei denen eine reduzierte Dicke eine grundlegende Anforderung ist. LCP werden aus einem extrem inerten, nicht reaktiven Material mit hoher Flammbeständigkeit hergestellt. Sie sind leicht und flexibel und verfügen über außergewöhnliche elektrische Eigenschaften, die sie zur idealen Lösung für Hochfrequenzanwendungen machen, insbesondere wenn Gewicht und Dicke der Leiterplatte begrenzt werden müssen. Flüssigkristallpolymere haben auch gute dielektrische Eigenschaften, mit sehr geringen Verlusten und Feuchtigkeitsaufnahme;
- Aluminium: Aluminiumleiterplatten, auch als metallummantelte Leiterplatten oder IMS (Insulated Metal Substrate) bekannt, bestehen aus einer dünnen Schicht eines wärmeleitenden, aber elektrisch isolierenden dielektrischen Materials, das als Zwischenschicht zwischen einer Metallbasis und einer Kupferfolie verwendet wird. Die Kupferfolie wird mit dem gewünschten Leiterplatten-Layout graviert, während die Metallbasis die Funktion hat, die von der Leiterplatte erzeugte Wärme durch die dünne dielektrische Schicht zu absorbieren. Der Hauptvorteil von Aluminium-Leiterplatten besteht in der besseren Wärmeableitung im Vergleich zu herkömmlichen Leiterplatten auf der Basis von FR-4-Material. Die ursprünglich für elektronische Hochleistungsanwendungen konzipierten metallkaschierten Leiterplatten entwickelten sich zu einer idealen Lösung zur Unterstützung von LED-Beleuchtungssystemen mit hoher Helligkeit, sowohl im Verbraucher- als auch im Automobilbereich. Abbildung 2 zeigt eine Aluminiumleiterplatte für Anwendungen im Bereich der ultrahellen LED-Beleuchtung.
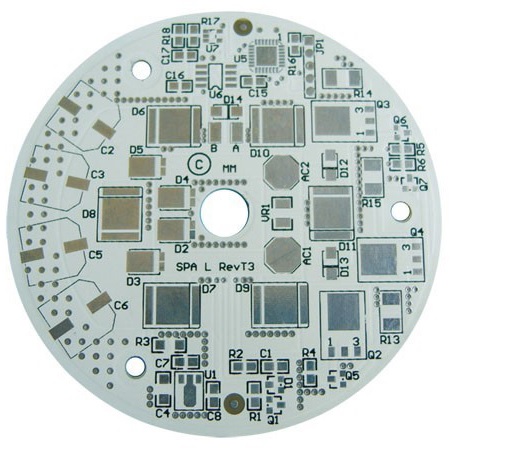
Abbildung 2: Beispiel einer metallkaschierten Leiterplatte.
Die neuen Materialien ermöglichen im Vergleich zu den traditionellen eine bessere Leistung und werden ständig und zunehmend weiterentwickelt, da sich viele mit der Signalintegrität zusammenhängende Aspekte verbessern lassen. Ein niedrigerer Dk-Wert verbessert Impedanzkontrolle, Übersprecheffekte, Flackern und Signalverzerrung. Ein niedrigerer Df-Wert hilft dagegen, die Anstiegs- und Abfallzeiten und die Gesamtdämpfung zu verbessern.