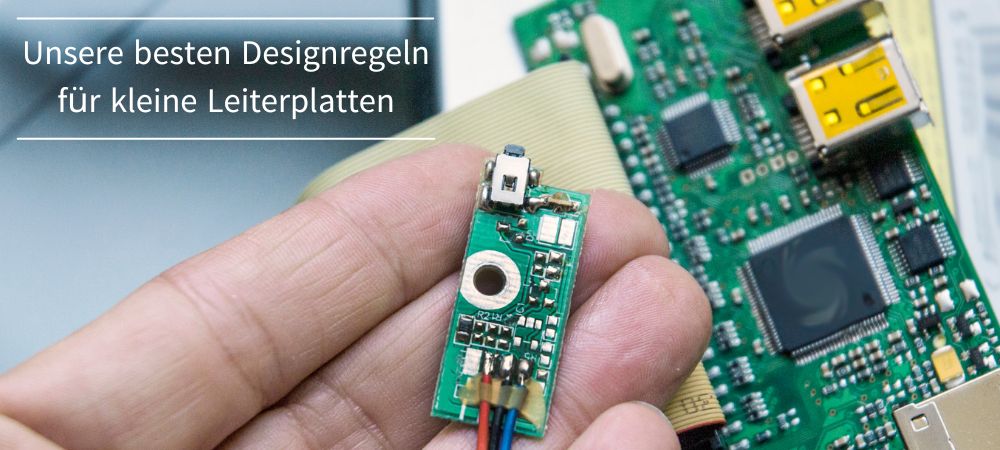
In den letzten Jahren ermöglichte die Entwicklung neuer elektronischer Technologien durch immer kleinere und leistungsstärkere Leiterplatten die laufende Miniaturisierung elektronischer Bauelemente. In diesem Artikel wird erläutert, welche Vorteile die Größenreduktion einer elektronischen Schaltung neben der Platzersparnis mit sich bringt.
Das Designen einer kleinen Leiterplatte kann jedoch für zahlreiche Designer zur Herausforderung werden. Neben kleineren Durchkontaktierungen und Leiterbahnen (die Breite einer Leiterbahn kann 50 µm oder weniger betragen) sind neue Designregeln erforderlich, um die steigende Komplexität dieser kleinen Leiterplatten zu bewältigen.
Ein weiterer wichtiger Aspekt betrifft die Kosten der Leiterplatte. In den meisten Fällen führt die Größenreduktion einer Leiterplatte auch zu einer Reduktion der Produktionskosten. In diesem Artikel werden die wichtigsten Richtlinien beschrieben, mit denen Designer die Größe der Leiterplatte reduzieren können, ohne Kompromisse bei Betrieb und Zuverlässigkeit eingehen zu müssen.
Vorteile einer kleineren Leiterplatte
Eine kleinere Leiterplatte bietet viele wertvolle Vorteile wie unter anderem:
- Geringere Kosten: Der Einsatz miniaturisierter Komponenten und einer Leiterplatte mit geringerer Größe ermöglicht es Ihnen, Materialkosten einzusparen. Obwohl die Anfangskosten im Hinblick auf die Entwicklung höher sein könnten, wirkt sich dies langfristig positiv auf die Produktionskosten der Leiterplatte aus. Je mehr Einheiten produziert werden, desto mehr wird eingespart.
- Weniger Platzbedarf: In platzbeschränkten Anwendungen wie Mobiltelefonen und tragbaren Geräten stellt eine kleinere Leiterplatte einen wichtigen Vorteil dar.
- Umweltfreundlichere Lösung: Durch eine Reduktion der für die Produktion erforderlichen Materialien werden die CO₂‑Emissionen aus der Herstellung reduziert und es muss weniger Material entsorgt/recycelt werden, wenn das Produkt das Ende seines Lebenszyklus erreicht hat.
- Mehr Effizienz: Eine miniaturisierte Leiterplatte ist in der Regel effizienter als eine größere Leiterplatte. Dies rührt daher, dass das komplexere Design bereits auf die wichtigsten Probleme hinsichtlich der Effizienz der Leiterplatte (wie Wärmeerzeugung und ‑verteilung, Leistungsabsorption und Leistungsverlust) eingegangen ist und diese gelöst hat.
Designherausforderungen
Die erste Herausforderung, der sich der Designer bei der Größenreduktion einer Leiterplatte stellen muss, liegt in der Geometrie der Leiterbahnen.
Wird die Breite einer Leiterbahn reduziert, muss meist auch ihre Dicke reduziert werden. Dies sollte nicht allzu schwer sein, wenn die die Leiterbahn durchlaufende Stromstärke nicht zu hoch ist. In diesem Fall können breitere Leiterbahnen nur auf Leiterbahnenpfaden verwendet werden, die mit hoher Stromstärke durchlaufen werden. Der Referenzstandard für den Designer zur Feststellung der korrekten Geometrie der Leiterbahnen ist jedenfalls IPC-2221.
Eine weitere Herausforderung für den Designer stellen die Durchkontaktierungen dar. Diese kleinen Löcher verfügen über physische Dimensionen, die nicht unterschritten werden können. Unter 2 mil (etwa 50µm) ist es beispielsweise schwierig, die gesamte Wand zu beschichten, wodurch Funktionalität und Leistung reduziert werden. Außerdem wird durch die Dicke des Laminats auch der Mindestdurchmesser der Durchkontaktierungen festgelegt.
Richtlinien
Beim Designen einer kleinen Leiterplatte müssen gewisse Faktoren berücksichtigt werden. Dazu gehören die Mindestbreite der Leiterbahnen, die Mindestbreite der Siebdruckvorlage für die Leiterplatte, der Mindestplatzbedarf für die Lötmaske, die Größe der Durchkontaktierungen und Pads etc. Nachfolgend werden die wichtigsten Faktoren analysiert, die zur Ermittlung der Mindestgröße einer Leiterplatte beitragen.
Microvias
Microvias sind besonders kleine Durchkontaktierungen, die ausschließlich durch Laserbohren hergestellt werden. Microvias sind besonders praktisch zur Herstellung von Verbindungen zwischen den unterschiedlichen Schichten einer mehrlagigen Leiterplatte und weisen in der Regel einen Durchmesser von etwa 2 – 3 mil auf (normalerweise spricht man von Microvias, wenn der Lochdurchmesser weniger als 6 mil beträgt), während die Länge meist nicht mehr als 0,25 mm beträgt. Diese Lösung (ein Beispiel dafür wird in Abbildung 1 gezeigt) wird meist verwendet, um die Größe der Leiterplatte zu reduzieren, da sie Verbindungen zwischen Leiterbahnen unterschiedlicher Schichten erstellt und so die äußere Oberfläche der Leiterplatte reduziert.
Abbildung 1: Microvias werden meist in mehrlagigen Leiterplatten verwendet
Dicke des Laminats
Zur Herstellung von kleinen Leiterplatten können die häufigsten Leiterplattenlaminate verwendet werden. Da sie jedoch einige Einschränkungen mit sich bringen, müssen Designer darauf achten, dass die ausgewählten Materialien wie das häufig verwendete FR-4 über eine ausreichende Dicke verfügen, um Microvias zu ermöglichen, sowie erforderliche Stärke- und Steifheitseigenschaften aufweisen.
In der Regel werden Leiterbahnen und Rückleiter von hohen Stromstärken durchlaufen und müssen deshalb dicker sein. Diese Leiterbahnen sollten deshalb über die beiden Außenseiten geführt werden, während Leiterbahnen, die nur von niedrigen Stromstärken bzw. analogen und digitalen Signalen durchlaufen werden, in den innersten Schichten geführt werden sollten.
Abbildung 2: Karte mit mehrschichtiger Leiterplatte
Muss in der zu designenden Schaltung viel Wärme verteilt werden, können die großen Kupferbereiche, die oft als Wärmeableiter dienen, durch eine Größenreduktion der Karte und dickere Kupferschichten (wie es bei der Dickkupfertechnologie der Fall ist) eliminiert werden.
Abstand zwischen den Leiterbahnen
Fortschrittliche CAD‑Designtools unterstützen den Designer bei der Optimierung und Größenreduktion der Leiterplatte. So kann beispielsweise der Abstand zwischen zwei Leiterbahnen auf 0,006″ oder weniger reduziert werden.
Außerdem hängt die Größe der Leiterplatte stark von der endgültigen Anwendung, den Eigenschaften des Gehäuses, in dem die Leiterplatte platziert wird, der Größe der ausgewählten Elektronikkomponenten und dem möglichen Vorhandensein von Wärmeableitern ab.
Partielle oder vergrabene Durchkontaktierungen
Neben Microvias verdienen auch herkömmliche Durchkontaktierungen viel Aufmerksamkeit, da sie zu einer signifikanten Größenreduktion einer Leiterplatte beitragen. Um das Routing zu optimieren und dabei zu vermeiden, dass die Größe der Leiterplatte aus dem Ruder läuft, bewährt sich die Lösung mit blinden Durchkontaktierungen. Parallel dazu ermöglicht der Einsatz von vergrabenen Durchkontaktierungen die Verbindung zwischen mehreren internen Schichten.
Es muss hier jedoch zwischen Kosten und Vorteilen abgewogen werden. Die Kosten für interne Durchkontaktierungen sind aufgrund der höheren Komplexität in der Fertigung vergleichsweise hoch. Wird die Leiterplatte in hoher Stückzahl produziert, können diese Kosten leicht auf die Anzahl der Leiterplatten aufgeteilt werden. Handelt es sich um eine kleinere Produktionscharge oder müssen Sie nur einige Prototypen produzieren, können die Auswirkungen der Kosten von blinden und vergrabenen Durchkontaktierungen nicht mehr vernachlässigt werden.
Außerdem ist es nicht immer möglich oder einfach, zur Verbindung von zwei internen Leiterplattenschichten einen direkten Pfad zu finden, der in der Regel von vergrabenen Durchkontaktierungen verwendet wird, da dies von der Anzahl der Leiterplattenschichten und der Art und Weise, wie die Signale auf den unterschiedlichen Leiterbahnen geroutet werden, abhängt.
Abbildung 3: Blinde, vergrabene und Lochdurchkontaktierungen
Gehäusegröße
Die Auswahl der Komponenten und ihrer Gehäuse ist beim Design einer kompakten Leiterplatte von entscheidender Bedeutung. In der Elektronik sind Komponenten (meist Widerstände und Kondensatoren) mit unterschiedlich großen Gehäusen verfügbar.
In der Regel verwenden frühe Prototypen einer Leiterplatte Komponenten mit größerem Gehäuse und werden deshalb mit größerem Abstand platziert als dies möglich wäre. Dies ergibt sich vor allem dadurch, dass das Löten und Bestücken einfacher von der Hand gehen soll und das Testen und Debuggen der Leiterplatte vereinfacht werden sollen.
Geht die Leiterplatte dann von der Prototypen- in die Produktionsphase über, können die Komponenten durch ähnliche mit kleinerem Gehäuse ersetzt werden, wodurch die Größe der Leiterplatte reduziert wird. Da bei standardmäßigen Pick-and-Place-Maschinen, die zur Bestückung von elektronischen Schaltungen verwendet werden, Einschränkungen hinsichtlich der Mindestgehäusegröße gelten, sollten keine Komponenten mit einer Gehäusegröße unter 0402 verwendet werden.
Ein weiterer Faktor, der sich auf den Gehäusetyp auswirkt, ist das Leistungsniveau. Kleinere Gehäuse eignen sich möglicherweise nicht für die erforderliche Stromstärke, sodass zu viel Wärme entwickelt wird oder Schäden auftreten können. Die Verwendung von SMD‑Komponenten ermöglicht durch größere Pads, die mit mehreren Gehäuseformaten kompatibel sind, eine etwas flexiblere Auswahl des Gehäuses.
Eine weitere Lösung, die sich vor allem für Schaltungen mit Leistungstransistoren eignet, ist der Einsatz von Leistungsmodulen (oder Gehäusen mit mehreren Komponenten) anstelle von diskreten Komponenten. Heute gibt es Module, die bei sehr geringem Platzbedarf ganze Schaltungen (wie Leistungsfaktorkorrektoren für die Stromversorgung oder AC‑DC- und DC‑DC‑Wandler) ersetzen, für die ansonsten sehr viele diskrete Komponenten sowie mehr Platz auf der Leiterplatte erforderlich wären.
Ähnliches gilt für Widerstände. Verwendet die Schaltung mehrere Widerstände des gleichen Typs in aneinander angrenzenden Bereichen der Leiterplatte, könnte es praktisch sein, sie durch eine einzelne Komponente wie ein Widerstandsnetzwerk (Abbildung 4) zu ersetzen.
Abbildung 4: Ein SMD‑Widerstandsnetzwerk (4 × 10 kOhm, 0,0625 W)
Entfernen von Testpunkten
Beim Designen einer Leiterplatte für eine neue Karte ist es sehr praktisch, viele Testpunkte, Pads, Steckverbinder oder Stifte zu verwenden, um das Debuggen und Testen der Schaltung zu vereinfachen. Diese Hilfsmittel ermöglichen (durch ein Oszilloskop oder ein anderes Instrument) eine rasche Signalaufnahme ohne fliegendes Löten oder Clips, die kompliziert im Umgang sind. Hat die Karte die Funktionstests bestanden und ist sie bereit für die Produktion, können die Testpunkte entfernt werden.
Es ist jedoch eine gute Idee, Testpunkte und exponierte Pads zu behalten, um ein automatisches Testen der Karte über ein Nagelbett zu ermöglichen oder eventuelle Wartungsarbeiten an der Hardware zu erleichtern.
Auswahl der Steckverbinder
Steckverbinder erfüllen nicht nur die Funktion der elektrischen Verbindung, sondern sind auch eine mechanische Komponente und benötigen als solche einigen Platz. Während sich dem Designer bei manchen Steckverbindern im Standardformat keine Alternative (wie Ethernet-, USB‑, BNC‑Stecker etc.) bietet, gibt es für andere (beispielsweise für den Anschluss der Kabel an die Karte) unterschiedliche Alternativen auf dem Markt. Sehr oft ermöglichen 90°‑Winkelstecker oder Terminalblöcke eine Reduktion der Kartengröße, wobei die Kosten dafür höher sein können als bei einer herkömmlichen Lösung.
Auch in diesem Fall muss also der Designer den richtigen Kompromiss zwischen geringer Größe und Kosten der gewählten Lösungen finden, um im erwarteten Budget zu bleiben.
22.02.2023
und erhalten Sie innerhalb von 10 Minuten ein Angebot für Ihr PCBA-Projekt