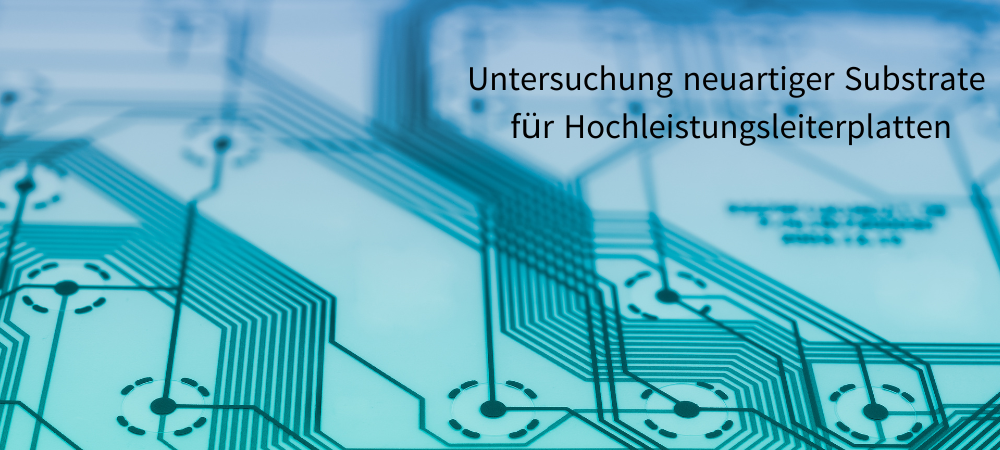
Leiterplatten (PCB) dienen als grundlegende Infrastruktur für elektronische Geräte und erleichtern die Verbindung verschiedener elektronischer Komponenten. Die Weiterentwicklung elektronischer Geräte erfordert Leiterplatten mit verbesserter Leistung, optimierten Designs und erweiterten Funktionen. Die Untersuchung neuer Substrate für Hochleistungsleiterplatten ist ein entscheidender Faktor für die Erreichung dieser Ziele. In diesem Artikel werden die Fortschritte und potenziellen künftigen Entwicklungen im Zusammenhang mit der Verwendung neuartiger Materialien als Leiterplattensubstrate untersucht.
Herkömmliche Substrate
FR‑4 (Flame Retardant 4) war aufgrund seiner niedrigen Kosten und relativ ausgezeichneten Leistung in der Vergangenheit das Standardmaterial für Leiterplatten. Mit den immer komplexer und kompakter werdenden elektronischen Geräten sind jedoch die Einschränkungen herkömmlicher Substrate wie die eingeschränkte Wärmeleitfähigkeit und die schlechte Signalintegrität bei hohen Frequenzen deutlich geworden.
Als flammhemmendes Material erfüllt FR‑4 die Brandschutznormen und wird häufig in Anwendungen eingesetzt, in denen Feuerbeständigkeit eine entscheidende Anforderung ist. Die Dielektrizitätskonstante von FR‑4 liegt typischerweise zwischen 4,2 und 4,7. Diese Eigenschaft ist entscheidend, da sie bestimmt, wie schnell Signale durch ein Material übertragen werden können. In Bezug auf die thermische Stabilität bietet FR‑4 eine hervorragende Leistung und hält einem großen Temperaturbereich ohne wesentliche Verschlechterung stand. Darüber hinaus verfügt FR‑4 über eine außergewöhnliche mechanische Festigkeit und Langlebigkeit. Es ist nicht nur ein kostengünstiges und weitverbreitetes Substratmaterial, sondern wird auch für eine Vielzahl von allgemeinen Anwendungen bevorzugt.
FR‑4 weist jedoch folgende Einschränkungen auf:
- Relativ geringe Wärmeleitfähigkeit im Vergleich zu einigen modernen Substraten. Bei Hochleistungsanwendungen kann diese Einschränkung zur Wärmeentwicklung beitragen und die Leistung und Zuverlässigkeit des Geräts beeinträchtigen.
- Signalintegrität bei hohen Frequenzen: FR‑4 ist möglicherweise nicht in der Lage, die optimale Signalintegrität bei hohen Frequenzen aufrechtzuerhalten, was zu Signalverlust und ‑verzerrung führt.
- FR‑4 ist aufgrund seiner mangelnden Flexibilität nicht für formbare oder biegbare elektronische Geräte geeignet. Bei Anwendungen, die Flexibilität erfordern, wird Polyimid häufig durch andere Materialien ersetzt.
Fortschrittliche Substrate
Polyimid
Polyimid, ein vielseitiges und hoch entwickeltes Substratmaterial für Leiterplatten, hat sich aufgrund seiner charakteristischen Eigenschaften in der Elektronikindustrie zu einer Prominenz entwickelt. Polyimid, bekannt für seine außerordentliche thermische Stabilität und Flexibilität, ist eine entscheidende Komponente in einer Vielzahl von Anwendungen.
Polyimid, das sich durch seine hohe Temperaturbeständigkeit auszeichnet, ist auch in schwierigen Umgebungen stabil. Diese Eigenschaft macht es ideal für Anwendungen in der Luft- und Raumfahrt, Automobilindustrie und Industrien, in denen elektronische Komponenten hohen Temperaturen ausgesetzt sein können.
Die Flexibilität von Polyimid ist ein weiteres bemerkenswertes Merkmal. Polyimid ermöglicht im Gegensatz zu herkömmlichen starren Substraten die Herstellung von formbaren und biegbaren Leiterplatten. Diese Qualität ist besonders bei Anwendungen von Vorteil, bei denen der Platz begrenzt oder konformes Design erforderlich ist.
Polyimidleiterplatten werden häufig in der Luft- und Raumfahrtindustrie verwendet, da sie leicht sind und sich komplexen Geometrien anpassen können. In Automobilanwendungen, in denen Vibrationen und thermische Spannungen vorherrschen, gewährleistet die Flexibilität von Polyimid die Haltbarkeit der Leiterplatten. Abbildung 1 zeigt eine flexible Leiterplatte mit Polyimidsubstraten.
Abbildung 1: Flexible Leiterplatte, hergestellt aus Polyimidsubstraten (Quelle: Cadence)
Zusätzlich zu seinen physikalischen Eigenschaften besitzt Polyimid hervorragende dielektrische Eigenschaften. Es sorgt für eine gleichbleibende elektrische Leistung und eignet sich daher für Hochfrequenzanwendungen. In der Telekommunikation und anderen Branchen, in denen die Signalintegrität von größter Bedeutung ist, sind Polyimidleiterplatten nützlich, um Spitzenleistungen aufrechtzuerhalten.
Polyimid hat jedoch einige Einschränkungen. Obwohl es in Umgebungen mit hohen Temperaturen außergewöhnlich gut funktioniert, ist seine Wärmeleitfähigkeit im Vergleich zu anderen Optionen relativ geringer. Bei Anwendungen mit intensiver Wärmeerzeugung können zusätzliche Maßnahmen erforderlich sein, um Wärme effektiv zu steuern und abzuleiten.
Darüber hinaus kann Polyimid teurer als herkömmliche Substrate wie FR‑4 sein. Dieser Kostenfaktor kann sich auf die Auswahl des Substratmaterials auswirken, insbesondere in Massenprodukten für Unterhaltungselektronik, bei denen Kostenerwägungen von entscheidender Bedeutung sind.
Hochfrequenzlaminate von Rogers Corporation
Die Hochfrequenzlaminate von Rogers Corporation stellen eine bedeutende Weiterentwicklung im Bereich der Leiterplattensubstrate dar und bieten eine einzigartige Reihe von Eigenschaften, welche die strengen Anforderungen von Hochfrequenzanwendungen erfüllen.
Eine niedrige Dielektrizitätskonstante ist eine der charakteristischen Eigenschaften der Laminate von Rogers Corporation, die zur effizienten Übertragung von Signalen beitragen. Diese Eigenschaft macht sie ideal für Anwendungen, bei denen die Aufrechterhaltung der Signalintegrität bei hohen Frequenzen entscheidend ist, wie Kommunikationssysteme, Radarsysteme und Hochfrequenzschaltungen.
Der geringe Verlustfaktor dieser Laminate ermöglicht die Herstellung von Hochleistungsleiterplatten mit minimalem Signalverlust. Diese Eigenschaft ist entscheidend für Anwendungen, bei denen die Präzision und Zuverlässigkeit der übertragenen Signale entscheidend ist, wie drahtlose Kommunikationsgeräte und fortschrittliche Radarsysteme.
Diese außergewöhnliche Dimensionsstabilität der Laminate von Rogers (Abbildung 2) gewährleistet, dass die elektrischen Eigenschaften des Materials über einen Bereich von Temperaturen und Umgebungsbedingungen konstant bleiben. Diese Stabilität ist entscheidend für die Aufrechterhaltung der Wirksamkeit von Hochfrequenzschaltungen, insbesondere bei Anwendungen mit erheblichen Temperaturschwankungen.
Abbildung 2: RO4500-Laminate (Quelle: Rogers Corporation)
Diese Hochfrequenzlaminate haben bei der Entwicklung und Herstellung von Antennen, Satellitenkommunikationssystemen und Hochfrequenzsensoren eine breite Anwendung gefunden. Insbesondere die Telekommunikationsbranche profitiert von den überlegenen elektrischen Eigenschaften der Laminate der Rogers Corporation für eine optimale Datenübertragungsleistung.
Die fortschrittlichen Eigenschaften dieser Hochfrequenzlaminate gehen jedoch häufig mit einem höheren Preis als für herkömmliche Substratmaterialien einher. Dies kann sich auf die Gesamtkosten des elektronischen Geräts auswirken und somit Entscheidungen in Massenproduktion für Unterhaltungselektronik beeinflussen.
Darüber hinaus kann die Herstellbarkeit von Hochfrequenzlaminaten den Einsatz spezialisierter Prozesse erfordern, was Herausforderungen in Bezug auf Skalierbarkeit und Integration in bestehende Fertigungsabläufe mit sich bringen kann.
Pyralux von DuPont
Pyralux, ein flexibles Schaltkreismaterial von DuPont, zeichnet sich als bahnbrechendes Substrat für Leiterplatten aus. Pyralux zeichnet sich durch seine Flexibilität aus, die es Designer ermöglicht, Schaltkreise zu erstellen, die unorthodoxen Formen und Designs entsprechen. Diese Qualität ist besonders in Branchen von Vorteil, in denen Platzbeschränkungen und komplexe Formfaktoren entscheidend sind.
Pyralux besteht typischerweise aus einer Polyimidschicht, die als flexible Basis fungiert, und Kupferschichten für Leiterbahnen. Diese Zusammensetzung sorgt für eine außergewöhnliche thermische Stabilität und gewährleistet, dass das Material einem Temperaturbereich standhält, ohne dass die Leistung beeinträchtigt wird. Pyralux eignet sich für Anwendungen in der Luft- und Raumfahrt, in der Automobilindustrie und in medizinischen Geräten, bei denen Flexibilität und Zuverlässigkeit aufgrund seiner robusten thermischen Stabilität von größter Bedeutung sind.
Die Anwendungen von Pyralux umfassen miniaturisierte und leichte elektronische Geräte. Seine Flexibilität ermöglicht die Herstellung biegsamer Schaltkreise und ist somit ideal für den Einsatz in tragbaren Technologien, flexiblen Displays und medizinischen Sensoren. Insbesondere die Medizinindustrie profitiert von Pyralux bei der Erstellung flexibler Schaltkreise für Implantate und Diagnosegeräte.
Trotz seiner zahlreichen Vorteile ist Pyralux nicht ohne Nachteile. Dieses hoch entwickelte Material kann teurer als herkömmliche starre Substrate sein, was sich auf die Gesamtkosten des elektronischen Geräts auswirkt. Darüber hinaus können sich die Herstellungsverfahren für Pyralux von starren Leiterplatten unterscheiden, was den Einsatz spezieller Geräte und Fachkenntnisse erfordert. Dies kann insbesondere für Industriezweige mit hohem Produktionsvolumen Schwierigkeiten hinsichtlich Skalierbarkeit und Massenproduktion mit sich bringen.
Metallkernleiterplatten
Leiterplatten mit Metallkern, auch als Metallkernleiterplatte (MCPCB) bekannt, haben einen einzigartigen Ansatz für das Design von Leiterplatten, indem sie einen Metallkern enthalten, typischerweise Aluminium oder Kupfer. Diese Designentscheidung bietet eine Reihe von Eigenschaften, die Metallkernleiterplatten besonders geeignet für Anwendungen mit hohen Energieanforderungen oder hohen thermischen Bedingungen machen.
Metallkernleiterplatten leiten aufgrund ihrer verbesserten Wärmeleitfähigkeit effektiv die von elektronischen Komponenten erzeugte Wärme ab. Das Innere aus Metall dient als Kühlkörper und erleichtert die Wärmeableitung von wichtigen Komponenten. Diese Wärmemanagementfunktion ist in Anwendungen wie LED‑Beleuchtung, Netzteilen und Automobilelektronik unerlässlich, in denen eine effektive Wärmeableitung für die Zuverlässigkeit und Langlebigkeit des Geräts von entscheidender Bedeutung ist.
Der Metallkern trägt nicht nur zur mechanischen Robustheit von Metallkernleiterplatten bei, sondern bietet auch eine robuste Komponentenunterstützung. Dies ist besonders bei Anwendungen vorteilhaft, die physischen Belastungen oder Vibrationen ausgesetzt sind, wie es in der Automobilindustrie und in der Industrie üblich ist.
Metallkernleiterplatten (Abbildung 3) werden in Bereichen mit hoher Leistungsdichte eingesetzt, wie Stromwandler und Motorantriebe. Der thermische Wirkungsgrad von Metallkernleiterplatten gewährleistet, dass elektronische Komponenten unter schwierigen Bedingungen optimal funktionieren können, wodurch die Gefahr einer Überhitzung verringert und die Gesamtleistung des Systems verbessert wird.
Abbildung 3: LED‑Leiterplatte auf Aluminiumbasis
Der Metallkern kann diese Platinen jedoch schwerer und potenziell teurer machen als herkömmliche FR‑4‑Platinen, wodurch ihre Anwendung in bestimmten Unterhaltungselektroniken eingeschränkt wird, bei denen Gewicht und Kosten von entscheidender Bedeutung sind. Darüber hinaus reduziert der Metallkern die Flexibilität dieser Leiterplatten im Vergleich zu flexiblen Substraten wie Polyimid.
Neue Technologien
Die elektrische Leitfähigkeit und mechanische Robustheit von Graphen machen es vielversprechend für Hochleistungsleiterplatten. Diese Leiterplatten verwenden Graphen, ein sechseckiges Gitter aus Kohlenstoffatomen, um viele einzigartige Eigenschaften zu bieten, die elektrische Geräte revolutionieren könnten.
Dank seiner elektrischen Leitfähigkeit eignet sich Graphen hervorragend für Hochleistungsleiterplatten. Die erhöhte Elektronenmobilität als bei typischen Materialien macht Graphen bei der Signalübertragung schneller und effizienter. Diese Eigenschaft profitiert von fortschrittlichen Kommunikationssystemen und Datenverarbeitungseinheiten, die einen schnellen Datentransport benötigen.
Die hohe Wärmeleitfähigkeit von Graphen sorgt für eine effiziente Wärmeableitung und löst eines der größten Probleme bei der Konstruktion elektrischer Geräte. In Hochleistungsanwendungen können Leiterplatten auf Graphenbasis eine Überhitzung reduzieren und die Zuverlässigkeit und Haltbarkeit elektronischer Komponenten verbessern.
Die zweidimensionale Struktur der Graphenschichten ermöglicht ultradünne und leichte Leiterplatten, wodurch sie ideal für Geräte mit begrenzter Fläche und Gewicht sind. Dies könnte zu einer kleineren, leichteren Elektronik führen. Viele Industrien könnten von Leiterplatten auf Graphenbasis profitieren. Die elektrischen und thermischen Eigenschaften von Graphen verbessern elektronische Systeme in Flugzeugen, Telekommunikation, medizinischen Geräten und Unterhaltungselektronik.
Leiterplatten auf Graphenbasis stehen zahlreichen Hindernissen für die allgemeine Implementierung gegenüber. Eine qualitativ hochwertige Graphensynthese in großem Umfang erfordert kostengünstige Fertigungstechnologien. Die Anpassung und Optimierung von Graphen in Leiterplattenproduktionsmethoden stellt die Skalierbarkeit und Kompatibilität mit aktuellen Fertigungsanlagen infrage.
Trotz der bemerkenswerten mechanischen Festigkeit von Graphen fehlt ihm zudem die Flexibilität bestimmter Polymerwerkstoffe. Diese Einschränkung kann seine Anwendbarkeit auf Geräte beeinträchtigen, die Flexibilität oder Anpassbarkeit erfordern, wie tragbare Elektronik oder flexible Displays.
Flüssigkristallpolymer(LCP)-Substrate sind anpassungsfähige und leistungsstarke Leiterplattenmaterialien. Elektrische Merkmale wie niedrige Dielektrizitätskonstante und Verlustfaktor machen Flüssigkristallpolymer berühmt. Flüssigkristallpolymersubstrate sind ideal für Hochfrequenzanwendungen, die Signalintegrität erfordern. Telekommunikation, Flugzeuge und Hochgeschwindigkeitsdatenkommunikation profitieren von der zuverlässigen Signalübertragung von Flüssigkristallpolymeren bei hohen Frequenzen.
Ein weiterer Vorteil von Flüssigkristallpolymer ist die Wärmestabilität. Das Flüssigkristallpolymer hat eine hohe Glasübergangstemperatur und behält seine strukturellen und elektrischen Eigenschaften bei vielen Temperaturen bei. Flüssigkristallpolymerensubstrate sind aufgrund ihrer Wärmebeständigkeit ideal für die Automobilelektronik und industrielle Steuersysteme.
Die mechanischen Eigenschaften von Flüssigkristallpolymer tragen zu seiner weitverbreiteten Verwendung im Leiterplattendesign bei. Flüssigkristallpolymerensubstrate können als dünne, flexible Folien hergestellt werden, welche die Herstellung von flexiblen und starr‑flexiblen Leiterplatten ermöglichen. Diese Anpassungsfähigkeit ist besonders in Branchen wie medizinische Geräte und tragbare Elektronikgeräte von Vorteil, in denen konformes und leichtes Design von entscheidender Bedeutung ist.
Flüssigkristallpolymerensubstrate werden in einer Vielzahl von Branchen eingesetzt. Von medizinischen Implantaten über tragbare Elektronik bis hin zu Hochfrequenzkommunikationsgeräten und Antennen – die Vielseitigkeit von Flüssigkristallpolymer erfüllt die Anforderungen moderner Elektroniksystem.
Die Kosten für die Herstellung von Leiterplatten auf Flüssigkristallpolymerbasis können jedoch höher als bei herkömmlichen Materialien wie FR‑4 sein. Dieser Kostenfaktor kann die Auswahl des Substratmaterials beeinflussen, insbesondere in der Unterhaltungselektronik, wo Kostenerwägungen eine wichtige Rolle spielen.
07.03.2024
und erhalten Sie innerhalb von 10 Minuten ein Angebot für Ihr PCBA-Projekt