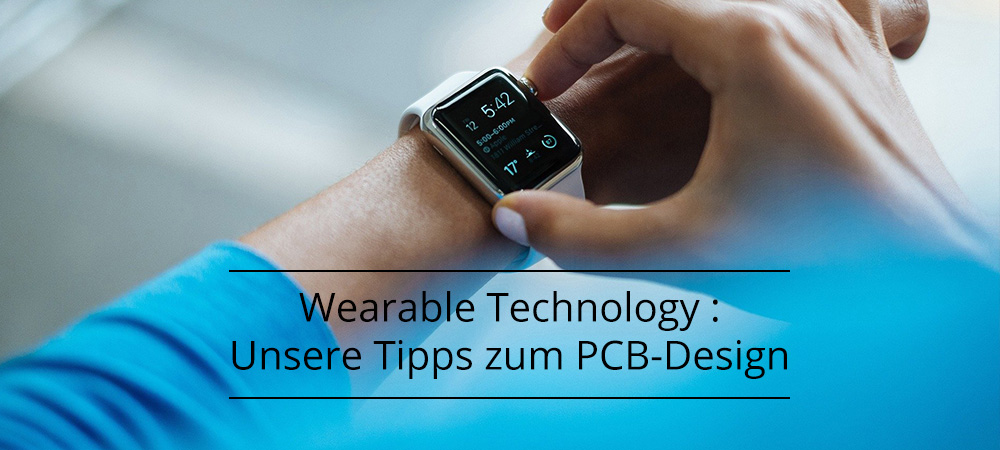
In den letzten Jahren sind mobile Geräte dank enormer Fortschritte in der Elektronik und der Verfügbarkeit integrierter elektronischer Komponenten, die eine höhere Effizienz und Leistung sowie einen kleineren Platzbedarf ermöglichen, immer beliebter geworden. Das Herzstück eines jeden tragbaren Geräts, sei es eine Smartwatch, ein Aktivitätstracker oder ein elektromedizinisches Gerät (EMD), ist eine Leiterplatte, deren Design eine der schwierigsten Herausforderungen für Elektronikingenieure darstellt. Kleine Größe und Gewicht, geringe Leistungsaufnahme, Zuverlässigkeit und geringe Wärmeabgabe sind einige der Anforderungen, die erfüllt werden müssen, um ein erfolgreiches tragbares Gerät zu schaffen. Kleine Größe und Gewicht, geringe Leistungsaufnahme, Zuverlässigkeit und geringe Wärmeabgabe sind einige der Anforderungen, die erfüllt werden müssen, um ein leistungsfähiges tragbares Gerät zu entwickeln. Aufgrund ihrer extrem kompakten Größe und ihrer relativ jungen Markteinführung gibt es noch keinen wirklichen Standard für das Design von Leiterplatten für diese Art von Geräten. Es ist jedoch möglich, die gleichen Techniken und Empfehlungen anzuwenden, die für Schaltungen mit ähnlichen Eigenschaften gelten, wobei die bei der Entwicklung und Herstellung von High-Tech-Leiterplatten gesammelten Erfahrungen genutzt werden können.
Mechanische Einschränkungen
Der auffälligste Unterschied zwischen einem elektronischen Standardgerät und einem tragbaren Gerät ist sicherlich die Größe. Tragbare Geräte müssen in der Tat sehr klein und leicht sein, aber dennoch die gleiche Funktionalität wie ein größeres Gerät gewährleisten. Größe und Gewicht zu minimieren und gleichzeitig die am besten geeignete geometrische Form zu wählen, ist keine leichte Aufgabe. Es ist in der Tat notwendig, die Position der Komponenten auf der Leiterplatte zu optimieren und die Leiterbahnen effizient zu verlegen. Das automatische Routing ist für diesen Zweck nicht immer geeignet, sodass ein manuelles Routing vorzuziehen ist. Das PCB muss sich an die Form des Gehäuses anpassen können. Tatsächlich ist es sehr selten, dass eine Schaltung für diese Art von tragbarem Gerät eine starre rechteckige Form hat; häufiger trifft man auf dünne mehrschichtige Leiterplatten mit gekrümmten Konturen, die so gestaltet sind, dass sie in das Gehäuse des Endprodukts passen. Auch die Wahl der Komponenten spielt eine grundlegende Rolle, wobei Gehäuse mit einer reduzierten Fläche und mit niedriger Bauhöhe zur Minimierung der Gesamtdicke des Produkts bevorzugt werden.
Ein weiterer Aspekt, der eng mit den mechanischen Anforderungen zusammenhängt, muss von den PCB-Designern berücksichtigt werden: Feuchtigkeit, die die Funktion von Leiterplatten potenziell beschädigen oder verändern kann, insbesondere wenn diese eine hohe Impedanz aufweisen. Da das mobile Gerät die meiste Zeit in direktem Kontakt mit dem menschlichen Körper steht (der dazu neigt, Feuchtigkeit abzusondern), muss eine Leiterplatte entwickelt und hergestellt werden, um mit der Feuchtigkeit klarzukommen. Je nach Fall haben die Entwickler die Wahl zwischen einer im Wesentlichen mechanischen Lösung, bei der das Gehäuse oder die Produktverpackung wasserdicht verschlossen ist, sodass keine Feuchtigkeit eindringen kann, oder einer elektronischen Lösung, bei der die Leiterplatte mit einer angepassten Beschichtung gegen das Eindringen von Feuchtigkeit geschützt ist.
Darüber hinaus ist die Vermeidung von Leckströmen besonders wichtig bei tragbaren Geräten, bei denen der Betriebsstrom nur wenige Nanoampere betragen kann. Es ist auch zu beachten, dass schlecht isolierte Komponenten Elektrizität in verschiedene Teile des Geräts streuen können, eine Situation, die aufgrund der Nähe zur Haut des Benutzers vermieden werden sollte. Nicht richtig isolierte Komponenten können einen Stromstoß, ein Auslaufen der Batterie oder eine Überhitzung verursachen, was zu schweren Verletzungen führen kann.
Auswahl des Leiterplattenmaterials
Die durch Prepreg voneinander isolierten PCB-Schichten können aus Laminaten bestehend aus FR4, Polyimid oder Rogers-Material hergestellt werden. Da tragbare Geräte ein hohes Maß an Zuverlässigkeit erfordern und oft Hochgeschwindigkeits- und Hochfrequenzsignale verarbeiten müssen, werden technologisch anspruchsvollere Materialien verwendet als das FR4, welches in der Regel die gängigste und preiswerteste Lösung darstellt. Das FR4-Material hat eine Dielektrizitätskonstante (Dk) von 4,5, wobei moderne Materialien wie Rogers 4003 und Rogers 4350 eine Dk von 3,55 bzw. 3,66 haben. Beim Umgang mit Hochfrequenzsignalen ist es notwendig, die Leistungsverluste zu begrenzen, weshalb ein Material wie Rogers 4350 vorzuziehen ist. Darüber hinaus hat das FR4 einen höheren Dissipationsfaktor (Df) als Rogers-Materialien, insbesondere bei hohen Frequenzen.
Dies bedeutet, dass bei der Verwendung eines FR4-Laminats mit Hochfrequenzsignalen erhebliche Einfügeverluste entstehen, die die Leistung und Übertragungskapazität der elektrischen Signale reduzieren. Auch wenn die Senkung der Produktionskosten ein wichtiger Faktor bei der Entwicklung eines solchen Produkts ist, sollte beachtet werden, dass eine mit Rogers' Laminaten hergestellte Leiterplatte eine bessere Leistung und Zuverlässigkeit als das herkömmliche FR4 bietet, und das zu akzeptablen Gesamtkosten. Für Verbraucheranwendungen, bei denen der Konkurrenzdruck stärker ist, kann immer noch eine Hybrid-Leiterplattenlösung verwendet werden, die durch die Kombination von FR4 auf Epoxidbasis mit Rogers und anderen Schichten aus Standard-FR4-Material erreicht wird. Rogers-Werkstoffe, wie z.B. die der Serie 4000, haben auch einen besonders stabilen Wärmeausdehnungskoeffizienten (WAK). Dies bedeutet, dass bei einem kalten, heißen und sehr heißen Reflow-Zyklus der Leiterplatte die Ausdehnung und Kontraktion der Leiterplatte innerhalb eines begrenzten, engen Raumes gehalten wird, insbesondere im Vergleich zu dem des normalen FR4-Materials. Diese Stabilität wird auch mit zunehmender Frequenz und Temperatur erreicht.
Hinsichtlich der Struktur der Leiterplatte verwenden mobile Geräte typischerweise eine Leiterplatte mit vier bis acht Lagen, die ausreichend Masse und Leistung für die Routing-Lagen bietet. Auf diese Weise wird das Crosstalk, das zwischen benachbarten Spuren auftreten kann, minimiert, und die elektromagnetische Verträglichkeit wird durch die Reduzierung der Auswirkungen elektromagnetischer Interferenz (EMI) verbessert. Was die Struktur der Platine betrifft, so ist die Platzierung der Bodenplatte in der Nähe der Stromverteilungsebene. Dadurch wird das Störsignal praktisch auf null reduziert, ein sehr wichtiger Aspekt, insbesondere bei Radiofrequenz (RF)-Subsystemen.
und erhalten Sie innerhalb von 10 Minuten ein Angebot für Ihr PCBA-Projekt
Design von Leiterplatten
Die Fertigung der Leiterplatte eines mobilen Geräts ist nicht auf die Leiterplatte selbst beschränkt und muss auch andere Materialien wie Gewebe, Kunststoff, starr-flexible Platten und Geflechte berücksichtigen. Im Gegensatz zu herkömmlichen starren Leiterplatten sind flexible und starr-flexible Leiterplatten robuster und bieten eine höhere Beständigkeit gegen Hitze, Feuchtigkeit, Wetter und Vibrationen. Diese innovativen Lösungen haben nicht nur den Vorteil, flexibel zu sein, sondern nehmen auch weniger Platz in Anspruch, sind leichter und haltbarer. Bild 1 zeigt ein Beispiel einer starrflexiblen Leiterplatte, die für tragbare Geräte geeignet ist.
Bild 1: Beispiel einer starr-flexiblen Leiterplatte.
Die Verwendung von starr-flexiblen Leiterplatten erfordert jedoch einige Ratschläge und Vorsichtsmaßnahmen. Zunächst muss insbesondere auf die perfekte Anpassung geachtet werden, die zwischen den Elementen bestehen muss, aus denen die Schaltung besteht, in dem Bewusstsein, dass die Leiterplatte den begrenzten verfügbaren Platz einnehmen wird. Ein weiterer besonders heimtückischer Aspekt ist das Stackup-Design. Die flexiblen und starren Teile der Schaltung müssen integriert werden, wobei ihre endgültige Position im Gerät vorausbestimmt werden muss. Dies wird durch die Verfügbarkeit geeigneter Programme erleichtert, die in der Lage sind, ein 3D-Modell der Leiterplatte oder des gesamten Geräts zu erstellen. Die mit Hochfrequenzsignalen verbundenen Leiterbahnen sollten nicht in der Nähe der Masseebenen platziert werden, sondern zwischen den Versorgungsbussen, um den durch das Signalrauschen erzeugten Flimmern zu glätten. Besondere Aufmerksamkeit muss der Impedanzkontrolle geschenkt werden, wobei zu bedenken ist, dass im Hochfrequenzbereich eine sehr kleine Impedanzfehlanpassung zu Problemen bei der Signalübertragung und beim Signalempfang mit den daraus resultierenden Verzerrungen führen kann.
Bei der Gestaltung einer Leiterplatte für tragbare Geräte sind Mikrostreifenleitungen, abgehängte Streifenleitungen und koplanare Wellenleiter weit verbreitet, da diese Verbindungsmethoden in der Lage sind, das für HF-Systeme typische Rauschen zu unterdrücken. Generell ist es auch ratsam, Tiefpassfilter, Entkoppelkondensatoren und ausreichende Masseflächen einzuführen. Das Tiefpassfilter unterdrückt die durch Rauschen erzeugte Restwelligkeit und reduziert das unerwünschte Signalübersprechen; der Entkopplungskondensator sollte in der Nähe der Versorgungsleitungen platziert werden. Bild 2 zeigt die Leiterplatte einer Smartwatch, die eine hohe Dichte an Komponenten aufweist, einschließlich Prozessor, HF-Transceiver, Audiocodec, Energieverwaltung, Basisbandprozessor und mehrere drahtlose Antennen.
Bild 2: Die Platine einer Smartwatch (Quelle: Samsung).