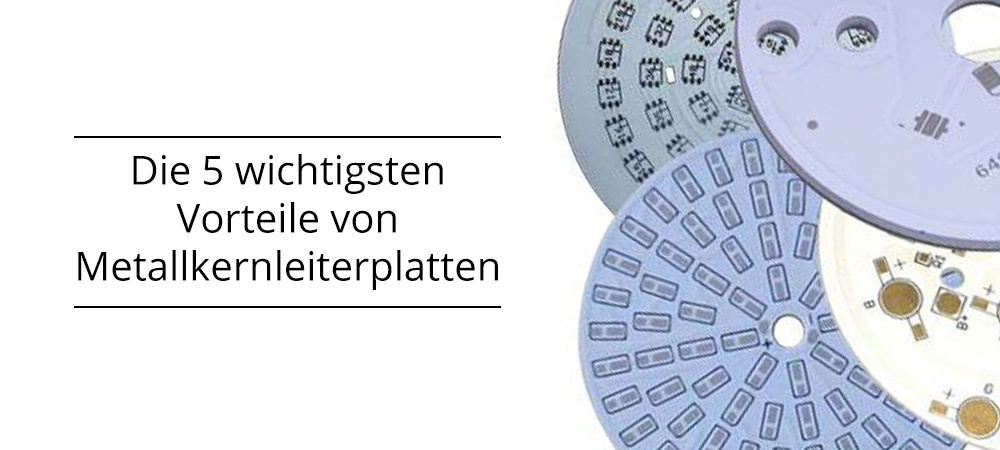
Für diese Kategorie von Leiterplatten gibt es mehrere Bezeichnungen wie Metallleiterplatte, isoliertes Metallsubstrat (IMS oder IMPCB), Metallkernleiterplatte (MCPCB), aluminiumummantelte Leiterplatte, Leiterplatte mit Aluminiumbasis etc. Trotz dieser scheinbar unterschiedlichen Namen beziehen sich all diese Definitionen auf den gleichen Leiterplattentyp und ihre technischen Merkmale sind die gleichen. Im Vergleich zur herkömmlichen FR-4-Leiterplatte auf Basis von Epoxid und Glasfaser bieten Metallleiterplatten durch ihre 5 bis 10 Mal so hohe Wärmeleitfähigkeit und bis zu 10 Mal geringere Dicke gegenüber herkömmlichen Architekturen vor allem eine bessere Wärmeverteilung. Die besonders effiziente Übertragung von Wärmeenergie ermöglicht es Metallleiterplatten, mit sehr leichten Kupferschichten auszukommen, wodurch bei dieser Lösung sowohl die Kosten als auch die Dicke reduziert werden.
Metallleiterplatten bestehen aus einer dielektrischen Schicht, die eine hohe Wärmeleitfähigkeit (und somit eine hohe Wärmeverteilung) bieten kann, einer Metallschicht und einer Kupferfolie mit hoher Wärmeverteilungskapazität und mechanischer Stärke, die für die Lithographie des Kreises verwendet wird. Meist werden für die Herstellung von Metallschichten Aluminium und Kupfer verwendet, doch in einigen Anwendungen kann auch Edelstahl verwendet werden. Kupfer bietet bessere Leistung und elektrische Eigenschaften als Aluminium, doch die Kosten dafür sind höher. Die Metallschicht kann vollständig aus Metall oder aus einer Kombination aus Glasfaser (FR-4) und Metall bestehen. Metallleiterplatten können einseitig oder doppelseitig sein; die mehrschichtige Version ist jedoch aufgrund der hohen Fertigungskomplexität seltener. Bei mehrschichtigen Metallleiterplatten müssen die Schichten im Hinblick auf die innere Metallschicht gleichmäßig verteilt sein; bei einer Leiterplatte mit 12 Schichten befindet sich die Metallschicht in der Mitte des Stapels, wobei sich 6 Schichten darüber und 6 Schichten darunter befinden.
Da Metall Wärme durch Subtraktion aus Hochleistungskomponenten problemlos leiten kann, umfassen die typischen Anwendungen von Metallleiterplatten Netzteile, Leistungswandler, LED-Beleuchtungssysteme und Schaltungen in Automobilumgebungen (Scheinwerfer, Beleuchtung, Kühlung, Klimaanlage etc.). Diese Art von Technologie ermöglicht zusätzlich zum effizienten Wärmemanagement eine Verlängerung der Lebensdauer der Komponenten (wie LED), wodurch die Zuverlässigkeit des gesamten Kreises verbessert wird.
Struktur und Anwendungen
Die ursprünglich in den 1960er-Jahren für Hochleistungsanwendungen entwickelte MCPCB-Technologie wird heute häufig in Anwendungen verwendet, bei denen eine niedrige Betriebstemperatur beibehalten werden muss. Das dielektrische Isolationsmaterial, das den Kern jeder Metallleiterplatte ausmacht, wurde entwickelt, um eine weit höhere Wärmeleitfähigkeit (meist zwischen 1 und 9 W/mK) zu bieten als jene von FR-4-Leiterplatten, wodurch eine effiziente Wärmeableitung gewährleistet wird. Die hohe Wärmeleitfähigkeit und die geringere Dicke der Isolationsschicht (das Standardmaß ist 100 µm) ermöglichen eine rasche und effektive Ableitung der entwickelten Wärme. Der übliche Wert für die Wärmeleitfähigkeit der dielektrischen Schicht ist 2 W/mK; dies ist deutlich höher als bei FR-4-Leiterplatten. Die besten Ergebnisse werden durch eine möglichst dünne dielektrische Schicht erzielt. Dies ermöglicht einen möglichst kurzen Weg der Wärmeableitung von jenen Punkten, an denen sie generiert wird, bis hin zur Metallschicht, die deutlich wärmeleitfähiger ist als das dielektrische Material.
Abbildung 1 zeigt die Struktur einer herkömmlichen Metallleiterplatte. Die obere Schicht besteht aus einer dünnen Kupferfolie, auf der Spuren eingeätzt werden, wie dies auch bei herkömmlichen Leiterplatten üblich ist. Die typische Dicke dieser Schicht beträgt zwischen 1 und 4 oz.; sie kann jedoch auch dicker sein. Die innerste Schicht besteht aus dem dielektrischen Material, dessen Funktion es ist, die Metallschicht elektrisch von der Kupferschicht zu isolieren und gleichzeitig eine rasche Wärmeableitung zwischen den beiden Schichten zu ermöglichen. Schließlich gibt es noch die Metallschicht, die meist aus Aluminium besteht und eine Dicke zwischen 1 und 3,2 mm (typischer Wert: 1,6 mm) aufweist.
Abbildung 1: Typische Struktur einer Metallleiterplatte.
Zu den wichtigsten Anwendungen von Metallleiterplatten gehören LED-Beleuchtung, Motorsteuerung bei Elektro- und Hybridfahrzeugen, Halbleiterrelais, Netzteile, Wandler, Spannungsregler, Solarpanels und Photovoltaikzellen. Im Allgemeinen eignet sich diese Technologie für Anwendungen, die viel Energie benötigen und somit viel Hitze erzeugen. Ist für die Leiterplatte ein rasches Abkühlen erforderlich, ist es besser, anstelle eines herkömmlichen FR-4-Substrats eine Metallleiterplatte zu verwenden. Aluminium, das am häufigsten für die Metallschicht verwendete Metall, besitzt sehr vorteilhafte elektrische Eigenschaften wie eine hervorragende Wärmeleitfähigkeit zwischen 2 und 5 W/mK (Watt pro Meter und Kelvin), eine hohe Durchschlagspannung (3 kV und mehr) und eine hohe Zugfestigkeit.
Die 5 wichtigsten Vorteile von MCPCB
Zusätzlich zu der hervorragenden Wärmeverteilung bieten Metallleiterplatten eine höhere Leistungsdichte, eine hohe elektromagnetische Abschirmung und eine bessere kapazitive Kopplung. Die Wärmedämmleistung kann durch den Einsatz von thermischen Durchkontaktierungen noch weiter verbessert werden, wie dies auch bei herkömmlichen Leiterplatten der Fall ist. Nachfolgend sehen Sie eine Auflistung der fünf wichtigsten Vorteile dieser Technologie.
1 – Wärmeableitung
MCPCB gehören zu den Leiterplattenoptionen mit einer höheren Wärmeleitfähigkeit. Da so viel Wärme wie möglich von den Leistungskomponenten ferngehalten wird, werden potenzielle Schäden am Kreis vermieden und es können hochdichte Kreise mit höherem Leistungsniveau genutzt werden. Aluminium ist eines der bei dieser Art von Substrat am häufigsten verwendeten Materialien: Neben seinen elektrischen Eigenschaften bietet Aluminium den Vorteil, recyclingfähig und kostengünstig zu sein. Metallkernleiterplatten leiten Wärme um 8 bis 9 Mal schneller ab als FR-4-Leiterplatten. Die dielektrische Schicht muss sehr dünn sein, um den kürzesten Weg zwischen der Wärmequelle und der stützenden Metallplatte zu ermöglichen. Die Dicke beträgt in der Regel zwischen 0,003 und 0,006″. Ein Test mit einer MCPCB mit integrierter 1-W-LED zeigte beispielsweise, dass die Temperatur ziemlich nah an der Umgebungstemperatur von 25 °C blieb, während eine LED der gleichen Stärke an einer FR-4-Leiterplatte eine Temperatur von 12 °C über der Umgebungstemperatur erreichte.
2 – Bessere Stärke und Stabilität
Die aktuelle, rasche Entwicklung der LED-Technologie vor allem bei der Hochleistungsbeleuchtung mit LED hat Bedenken aufgrund der Wärmeverteilung ausgelöst. Da diese LED meist direkt auf die Leiterplatte angebracht werden, können sie für den Kreis im Hinblick auf Stabilität und Zuverlässigkeit ein Problem darstellen. Ohne die richtige Technik kann die Wärmeverteilung die Leistung von elektronischen Geräten beeinträchtigen, die mit hoher Leistung betrieben werden. Der Einsatz von Metallleiterplatten bei diesen Anwendungen löst dieses Problem effektiv. Neben der Gewährleistung einer hohen Haltbarkeit ist Aluminium sehr leicht und verleiht der Leiterplatte Stärke und Widerstandsfähigkeit ohne zusätzliches Gewicht.
3 – Dimensionsstabilität
Die Größe von Metallleiterplatten bleibt bei veränderlichen Umgebungsbedingungen stabiler als jene von Leiterplatten aus traditionellen Materialien wie bei FR-4. Bei einer Erwärmung von 30 °C auf etwa 150 °C ändert sich die Größe von Leiterplatten mit Metallschichten (wie Aluminium) nur geringfügig um etwa 2,5 bis 3,0 %.
und erhalten Sie innerhalb von 10 Minuten ein Angebot für Ihr PCBA-Projekt
4 – Geringeres Gewicht und bessere Recyclingfähigkeit
Leiterplatten mit Metallsubstraten sind leichter, halten länger und sind leitfähiger als herkömmliche Leiterplatten aus Epoxidmaterialien. Außerdem sind sie umweltfreundlicher, da die verwendeten Metalle einschließlich Aluminium nicht toxisch sind und einfach recycelt werden können. Aluminium kann einfach gewonnen und raffiniert werden, wodurch es deutlich günstiger ist als andere Metalle. Aus diesem Grund können auch die Fertigungskosten von Leiterplatten mit Aluminiumsubstraten reduziert werden. Aluminiumleiterplatten sind auch eine kostengünstige Alternative zu den teureren und platzraubenden Wärmeableitern. Aluminium ist als nicht toxisches und vollkommen recyclingfähiges Metall bekannt. In der Kette zwischen dem Produzenten und dem Endverbraucher trägt der Einsatz von Aluminium in Metallleiterplatten zum Schutz unseres Planeten bei.
5 – Längere Lebensdauer
Aluminium bietet eine größere Stärke und Haltbarkeit als die üblicherweise bei der Leiterplattenfertigung verwendeten Materialien wie Keramik und Glasfaser. Es ist ein sehr robustes Metall, welches das Risiko eines versehentlichen Bruchs während der unterschiedlichen Fertigungsphasen, der Montage oder der normalen Nutzung des Endproduktes reduziert. Abbildung 2 zeigt eine Aluminiumleiterplatte für Anwendungen im Bereich der LED-Beleuchtung.
Abbildung 2: Einige Beispiele für Aluminiumleiterplatten.