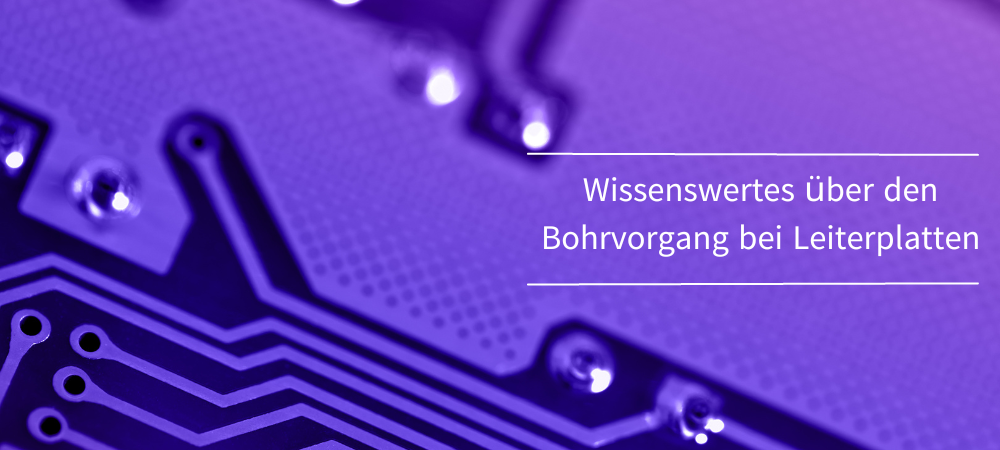
Sobald der Laminierungsvorgang abgeschlossen ist, beginnt die Bohrphase der Leiterplatte, welche gemäß den Anweisungen in den NC‑Bohrdateien für die Leiterplatte erfolgt. Es werden Löcher in die Leiterplatte gebohrt, um die Positionierung der Bauelemente, das Erstellen von Durchkontaktierungen und die elektrische Verbindung zwischen den einzelnen Schichten der Leiterplatte zu erleichtern. Von allen Schritten der Herstellung einer Leiterplatte ist das Bohren wahrscheinlich der kostspieligste und zeitraubendste Vorgang. Dieser Schritt muss mit höchster Präzision erfolgen, da schon der kleinste Fehler katastrophale Auswirkungen auf die Qualität der Leiterplatte haben kann.
Durch die progressive Miniaturisierung und der Anstieg in der Dichte der elektronischen Bauelemente wird die Phase des Leiterplattenbohrens noch kritischer und heikler. Bei ein- und zweiseitigen Leiterplatten erfolgt der Bohrvorgang sofort nach dem Schneiden, während er bei mehrschichtigen Leiterplatten erst auf die Laminierung folgt.
Spezielle digital gesteuerte CNC‑Bohrmaschinen entschlüsseln die in der Gerber- oder ODB‑Bohrdatei enthaltenen Informationen wie Koordinaten (X, Y) und Größe (Durchmesser und Tiefe) der Löcher und wenden diese an. Während des Bohrvorgangs werden die Löcher einzeln gebohrt, wodurch dieser Schritt einige Zeit dauert. Um den Betrieb zu optimieren, werden mehrere Leiterplattenpanels gleichzeitig gebohrt.
Nach dem Bohren startet der Bürst- und Entgratvorgang; dieser dient dazu, das überschüssige Kupfer an den Kanten der Löcher zu entfernen. Das Entgraten kann mithilfe unterschiedlicher Techniken wie Bürsten oder Plasmareinigung durchgeführt werden. Alle Löcher müssen vollkommen frei von Rückständen sein, um eine reibungslose und gleichmäßige Beschichtung zu ermöglichen.
Bohrtechniken
Die Löcher auf der Leiterplatte können über elektrochemisches Ätzen und mechanische Vorgänge wie Bohren, Laserschneiden oder Stanzen erzeugt werden. Die höhere Dichte der Durchstecklöcher und ihre progressive Größenreduktion erfordern Bohrtechniken, die auch sehr kleine Löcher mit hoher Präzision und Wiederholbarkeit erzeugen können.
Mechanisches Bohren
Das Bohrelement besteht aus einem pneumatischen Futter, das mit einer Geschwindigkeit von fast 300 000 rpm rotiert. Um die Genauigkeit bei hoher Geschwindigkeit beizubehalten, was für hohe Präzision auch in kleinen Löchern wichtig ist, wird die Bitvibration innerhalb eines Bereichs von 10 μm kontrolliert. Um die exakte Position des Lochs auf der Leiterplatte beizubehalten, wird die Bohrmaschine auf ein servomechanisches System montiert, das sich entlang der x‑ und y‑Achse bewegen kann. Zur Steuerung der Bewegung der Leiterplatte entlang der z‑Achse wird ein spezieller Stellantrieb verwendet. Ein Bohren mit hoher Geschwindigkeit gewährleistet saubere und glatte Lochwände und ist für eine gute Beschichtung der Lochwände erforderlich.
Das mechanische Bohren erzeugt qualitativ hochwertige Löcher ohne Konizität an den Enden. Außerdem ist die Geschwindigkeit beim mechanischen Bohren höher als bei anderen Methoden, wodurch das Verfahren der Leiterplattenfertigung beschleunigt wird. Sind die Löcher jedoch besonders klein, kann der Bit während des Bohrens brechen. Darüber hinaus muss jedes Loch danach entgratet werden, um beim Bohrvorgang übrig gebliebenes Kupfer zu entfernen.
Abbildung 1 zeigt eine digital gesteuerte Maschine für das mechanische Bohren.
Abbildung 1: CNC‑Maschine für das mechanische Bohren
Laserbohren
Beim Leiterplattenbohren verwendete Laserbohrer basieren auf einer komplexen Reihe von Optiken, die Löcher und Microvias mit einem Durchmesser von unter 200 μm und sehr hoher Präzision erzeugen können. Dir Größe bzw. der Durchmesser des in die Leiterplatte gebohrten Lochs wird durch die Laserstrahlöffnung festgelegt, während die Tiefe des Lochs durch die Belichtungszeit bestimmt wird. Zur Konzentration des Laserstrahls exakt auf jenem Punkt der Leiterplatte, auf dem gebohrt werden soll, wird ein spezielles Linsenset verwendet. Neben dem Bohren extrem kleiner Löcher (wie Microvias und blinden Durchkontaktierungen) bietet das Laserbohren den Vorteil, eine Delaminierung zu vermeiden.
Beim Laserbohren wird zum Erzeugen von Löchern in einer Leiterplatte ein Laserstrahl mit hoher Intensität eingesetzt. Je nach dem Leiterplattenmaterial werden unterschiedliche Arten von Lasern verwendet; am häufigsten jedoch sind es UV‑ und CO₂‑Laser.
Der wichtigste Vorteil des Laserbohrens ist es, dass zahlreiche Materialien abgetragen werden können, da diese Methode kleine Löcher bohren kann, die mit dem herkömmlichen mechanischen Bohren nicht zu erzeugen sind. Außerdem handelt es sich beim Laserbohren um eine kontaktlose Technik, für die keine komplexe Auswahl an Bohrsätzen erforderlich ist, die dies beim mechanischen Bohren der Fall ist.
Zu den Nachteilen des Laserbohrens gehören die Schwierigkeit, eine präzise Kontrolle über die Tiefe des Lochs zu erhalten, wenn keine Stoppschicht aus Metall verwendet wird, sowie der vom Laser erzeugte Verbrennungseffekt an den Lochrändern, die in der Regel dunkler werden.
Wie beim mechanischen System können auch beim Laserbohren je nach Dicke mehrere Panels übereinandergelegt werden. Die derzeitigen Laserbohrmaschinen können Durchstecklöcher mit einem Durchmesser zwischen 50 und 150 μm erzeugen.
Abbildung 2 zeigt einige Löcher, die mit einer Laserbohrmaschine für Leiterplatten erzeugt wurden. Beachten Sie die extreme Genauigkeit der Löcher, die trotz ihrer geringen Größe praktisch frei von Fehlern und Rückständen sind.
Abbildung 2: Beispiele für Löcher und Microvias, die mit dem Lasersystem erzeugt wurden (Quelle: Hitachi High-Tech)
Neue Bohrtechniken
Die Anzahl der in eine Leiterplatte zu bohrenden Löcher ist in den vergangenen Jahren deutlich angestiegen. Während die Leiterplatte eines normalen Mobiltelefons 30 000 bis 50 000 Löcher benötigt, können für eine CSP‑Leiterplatte (Chip Scale Package) auch 300 000 Löcher oder mehr erforderlich sein. Aus diesem Grund wird für die Leiterplattenfertigung eine Bohrtechnik benötigt, die einen hohen Durchsatz bietet.
Die Direktbelichtung ist eine neue Technik, mit der Löcher in die Leiterplatte gebohrt werden können. Diese neue Methode basiert auf dem Prinzip der Bildverarbeitung und erhöht sowohl die Genauigkeit als auch die Geschwindigkeit, da ein digitales Bild der Leiterplatte erzeugt und in eine Karte aus einzelnen Positionen konvertiert wird, welche der Laser als Referenzen für die zu bohrenden Löcher verwendet. Die Technik der Direktbelichtung verbessert die Genauigkeit der Lochausrichtung, da das digitale Bildverarbeitungssystem die mögliche Expansion, Kontraktion und Deformation der Leiterplatte bzw. des Panels berücksichtigt. Abbildung 3 zeigt moderne Ausstattung für die Leiterplattenfertigung mithilfe der Direktbelichtungsmethode.
Abbildung 3: Ausstattung für die Leiterplattenfertigung mithilfe der Direktbelichtung
Arten von Löchern
Beim Bohren von Löchern in eine Leiterplatte müssen zwei wichtige Dinge berücksichtigt werden. Das erste ist das Seitenverhältnis, welches sich direkt auf die Möglichkeit der Kupferbeschichtung im Inneren der Löcher auswirkt. Dies wird bei sinkendem Durchmesser und steigender Tiefe des Loches problematisch. Das Seitenverhältnis, also in diesem Fall das Verhältnis zwischen der Tiefe des Loches und seinem Durchmesser, beträgt typischerweise 10 : 1 bei Durchstecklöchern und 0,75 : 1 bei Microvias. Im Allgemeinen sollte das Seitenverhältnis sehr klein gehalten werden, um den Bohrvorgang zu vereinfachen und eine übermäßige Abnutzung des Bits beim mechanischen Bohren zu vermeiden.
Der zweite Aspekt betrifft den Abstand zwischen dem Rand eines Loches und dem nächsten Kupferbereich auf der Leiterplatte (dies kann eine Leiterbahn, ein Pad etc. sein). Der Mindestwert dieses Abstandes sollte in der Regel 8 μm betragen, um mögliche Fehlfunktionen der Schaltung zu vermeiden.
Die wichtigsten Löcher, die in eine Leiterplatte gebohrt werden können, lassen sich in drei Kategorien einteilen:
- Durchkontaktierungslöcher. Diese kleinen, metallbeschichteten Löcher werden zur Übertragung von elektrischen Signalen, Leistung und Erdung durch die unterschiedlichen Schichten der Leiterplatte verwendet. Abhängig vom Typ gibt es Durchkontaktierungen mit Durchstecklöchern (die vollständig durch mehrere Schichten der Leiterplatte verlaufen), vergrabene Durchkontaktierungen (Löcher, die sich vollständig innerhalb des Leiterplattenaufbaus befinden und nicht an die beiden äußersten Schichten geführt werden), blinde Durchkontaktierungen (die an der obersten Schicht beginnen und an einer Innenschicht enden) und Microvias (die kleiner als die vorherigen sind und nur durch Laserbohren erzeugt werden können).
- Löcher zum Durchführen von Bauelementen wie Anschlüssen, Schaltern und anderen mechanischen Bauelementen, für die eine robuste Bestückung in einem Durchgangsgehäuse erforderlich ist. Diese Art von Gehäuse eignet sich hervorragend für Leistungsbauelemente wie große Widerstände, Kondensatoren, aktive Leistungsverstärker und Spannungsregler, die viel Stromstärke und Wärme erzeugen.
- Mechanische Löcher. Dabei handelt es sich um Löcher, die zur mechanischen Montage von Gehäuse, Lüftern, Wärmeableitern etc. dienen. Außerdem können diese Löcher gebohrt werden, um die Ausrichtung der Leiterplatte an automatisierten Fertigungsmaschinen zu erleichtern.
Bohrvorgang
Der Bohrvorgang an der Leiterplatte kann in vier Schritte unterteilt werden, die nachfolgend beschrieben werden.
1 – Positionierungslöcher
Die Positionierungslöcher dienen während der Fertigung und Überprüfung der Leiterplatte als Referenzpunkte. Vor dem Bohren werden von unten nach oben Bohrunterlage, Substrat und Aluminiumfolie auf den Hochgeschwindigkeitsbohrtisch gelegt. Abhängig von den Produktionsanforderungen werden einige Positionierungslöcher mit einem Durchmesser von wenigen Millimetern in die Ränder der Leiterplatte gebohrt.
2 – Einsetzen der Stifte
Um die Produktionseffizienz zu erhöhen, werden mehrere Leiterplatten oder Panels vor dem Bohren übereinandergelegt. Die Panels werden auf dem Bohrmaschinentisch mit geeigneten Stiften fixiert, um ein mögliches Verrutschen während des Bohrvorgangs zu verhindern.
3 – Bohren der Löcher
Der Bohrvorgang erfolgt durch automatische, digital gesteuerte Maschinen. Aus diesem Grund genügt es, die Dateien mit den in CAM‑Befehle konvertierten Bohrparametern einzugeben, um die entsprechenden Löcher zu bohren. Das mechanische Bohren ist eine der am häufigsten verwendeten Methoden zum Bohren von Löchern in Leiterplatten. Das Bohrbit rotiert mit hoher Geschwindigkeit und bohrt unterschiedliche Arten von Löchern einschließlich beschichteter Durchstecklöcher (PTH) und nicht beschichteter Durchstecklöcher (NPTH). Vor dem Bohren wird eine Unterlage unter das zu bohrende Panel gelegt, um die Oberfläche des Bohrers zu schützen, während eine Aluminiumfolie darübergelegt wird, um die Löcher in der Kupferfolie flacher zu machen und ein Überhitzen des Bohrers zu vermeiden.
4 – Überprüfen der Löcher
Nach dem Bohren muss die Position und Öffnung jedes Loches genau überprüft werden. Wurden keine Probleme wie zusätzliche Löcher, fehlende Löcher oder eine falsche Lochposition festgestellt, kann die Leiterplatte zum nächsten Fertigungsschritt weitergehen.
und erhalten Sie innerhalb von 10 Minuten ein Angebot für Ihr PCBA-Projekt