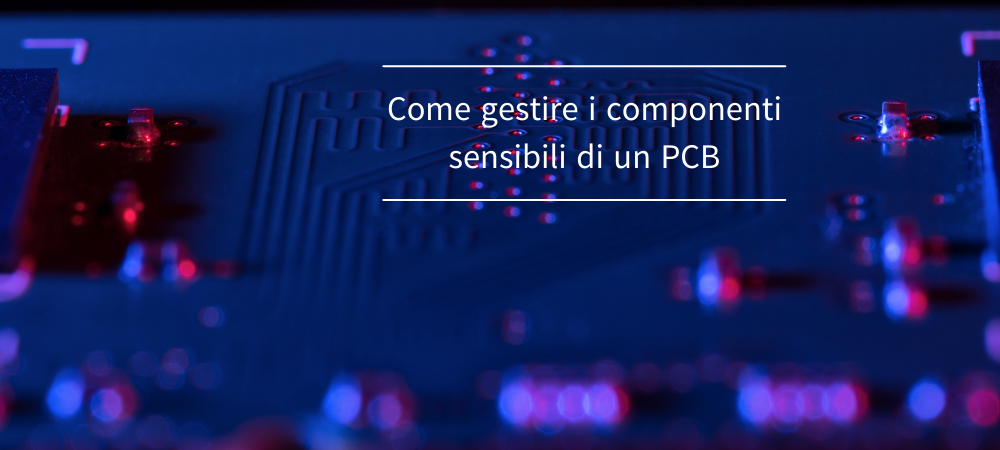
Negli ultimi anni, i dispositivi elettronici hanno subito una continua evoluzione che ha portato a dimensioni sempre più ridotte, accompagnate da prestazioni e velocità sempre più elevate. PCB sempre più piccoli, complessi e densi, ricchi di componenti miniaturizzati ad elevate prestazioni, richiedono un’opportuna protezione delle parti elettroniche ai fini di evitare possibili fenomeni di corrosione quando vengono esposti a umidità e agenti contaminanti. Ciò può degradare le prestazioni del circuito, o causare cortocircuiti e guasti.
La presenza di umidità, ad esempio, può causare diversi tipi di guasti su un PCB, a seconda di quali componenti o tracce conduttive entrano in contatto con essa. I più comuni problemi legati all'umidità includono un rallentamento della velocità dei segnali e aumento dei ritardi di propagazione. Superata una determinata soglia, il circuito potrebbe smettere di funzionare del tutto.
I dispositivi elettronici possono subire danni interni se non vengono maneggiati e conservati applicando gli standard specifici del settore. I componenti con package BGA (Ball Grid Array) e chip scale sono particolarmente sensibili all'umidità e il danno a questi componenti può essere difficile da rilevare anche in fase di ispezione. In Figura 1 è visibile un esempio di danni prodotti sul PCB dall’umidità.
Figura 1: Danni prodotti dall’umidità sul PCB
Componenti sensibili e MSD
Per danneggiare irrimediabilmente un PCB possono bastare poche gocce d’acqua, ma anche una quantità ancora inferiore di umidità. L'umidità rappresenta un problema non solo durante il funzionamento del circuito, ma anche durante lo stoccaggio e la conservazione delle schede, prima che esse vengano installate.
L'acqua pura o demineralizzata ha una resistività pari a circa 1,8 x 107 Ωxm a 25°C, il che la rende un isolante molto migliore di un conduttore di elettricità. In realtà, l'acqua con cui può venire a contatto un circuito stampato contiene sali e minerali disciolti, cloruri, solfati e carbonati. La presenza di questi materiali rende l'acqua altamente conduttiva, rappresentando una potenziale minaccia per l’integrità del circuito stampato, provocando cortocircuiti e processi di corrosione.
Una minaccia ancora peggiore è rappresentata dalla condensa, che si crea quando la superficie del PCB è più fredda dell'ambiente circostante. La condensa può formarsi sia sulle facce esterne della scheda, sia all’interno dei package dei componenti, che devono pertanto essere selezionati tenendo in debita considerazione questo aspetto.
I componenti elettronici particolarmente sensibili all’umidità, identificati con l’acronimo MSD (Moisture Sensitive Device) richiedono una protezione adeguata sia durante le fasi di assemblaggio del PCB, sia durante la fase di stoccaggio in magazzino delle schede finite. Quando un componente ha un coefficiente di assorbimento dell’umidità troppo elevato, c'è il rischio potenziale di danneggiare la scheda, i componenti, o le connessioni tra di essi. Una presenza eccessiva di umidità durante il processo di saldatura può provocare danni al materiale utilizzato per il substrato della scheda. Il problema è che questi tipi di difetti non sono facilmente rilevabili e hanno la tendenza a manifestarsi solo sul prodotto finale o dopo un certo tempo di utilizzo, riducendo drasticamente la possibilità di porvi rimedio.
I rischi maggiori si verificano durante il processo di saldatura a rifusione, quando i componenti MSD vengono collocati sul PCB. Anche ampie e improvvise variazioni della temperatura ambiente possono provocare una dilatazione o fessurazione del package. Un effetto molto comune prodotto dall’umidità è la delaminazione interna del materiale utilizzato per la realizzazione del PCB. Il comune FR-4, ad esempio, è un materiale fortemente igroscopico ed è pertanto particolarmente sensibile all’umidità ambientale, indipendentemente dalle modalità di confezionamento. L’eventuale umidità non eliminata durante le fasi di saldatura si trasforma in vapore, causando delaminazioni e microcavità nelle zone più sensibili della sheda.
Standard IPC per i componenti sensibili
I primi standard relativi al controllo dell’umidità nei PCB sono stati rilasciati nel 2010 dall’IPC, inizialmente noto come Institute for Printed Circuits. Seguendo questi standard, le schede elettroniche possono durare più a lungo, a condizione che vengano utilizzate delle tecniche adeguate per diffondere l'umidità. Inoltre, le schede protette da un opportuno rivestitimento possono mantenere la loro saldabilità per periodi più lunghi, a condizione che vengano prese misure per evitare che l'umidità penetri al loro interno.
Secondo le stesse linee guida, la cottura al forno è un metodo pratico per rimuovere l'umidità dai PCB nel caso in cui non fosse stato possibile impedirne in precedenza l’ingresso. Tuttavia, la cottura comporta inevitabilmente un aumento dei costi, un allungamento dei tempi di produzione e una minore saldabilità. Tale metodo dovrebbe pertanto essere evitato il più possibile, ricorrendo invece a tecniche di manutenzione preventiva durante l'assemblaggio e lo stoccaggio dei PCB.
Attualmente esistono due standard emanati da ICP in grado di guidare i produttori elettronici nella gestione dei componenti sensibili all'umidità: IPC/JEDEC J-STD-020E e IPC/JEDEC J-STD-033D.
IPC/JEDEC J-STD-020E
Questo standard offre un sistema di classificazione per determinare la qualifica di affidabilità iniziale. Dopo l'identificazione, i produttori possono imballare, conservare e manipolare i dispositivi per ridurre i danni termici e meccanici durante il processo di rifusione.
IPC/JEDEC J-STD-033D
Questo standard fornisce una metodologia rivolta agli utenti finali per la manipolazione, l'imballaggio, la spedizione e l'applicazione di MSD, nonché procedure per aumentare la resa e limitare il degrado dell'affidabilità.
Entrambi gli standard suddividono i livelli di sensibilità all'umidità, o MSL (Moisture Sensitivity Level), in classi numerate da 1 a 6 a seconda della loro suscettibilità al danno indotto dall'umidità. I livelli più alti si applicano ai componenti sensibili che offrono una maggiore resistenza all’umidità. In particolare, per ogni classe, è indicato per quanto tempo il componente può rimanere al di fuori di un sistema di protezione dell’umidità prima di essere sottoposto a cottura per rimuovere l’umidità assorbita.
Come visibile nella tabella di Figura 2, il livello MSL 6 corrisponde ai componenti più sensibili, che richiedono di essere sottoposti a cottura prima di essere utilizzati.
Figura 2: Le classi MSL (Fonte: TI)
I PCB, come anche le schede finite, dovrebbero invece essere conservati e spediti utilizzando delle apposite buste protettive (in genere forniscono protezione sia ESD, sia dall’umidità), come le buste MBB (Moisture Barrier Bag) visibili in Figura 3.
Figura 3: Buste protettive MBB in alluminio
Come proteggere componenti e PCB
Per proteggere i PCB dall'umidità, l’approccio migliore è quello di intervenire opportunamente in tutte le fasi di produzione del PCB, come nelle successive fasi di stoccaggio e spedizione.
Fabbricazione
Durante la produzione dei PCB, il processo di laminazione deve essere condotto in un ambiente a temperatura e umidità controllate utilizzando, se necessario, degli opportuni agenti essiccanti. Il personale dovrebbe sempre indossare guanti puliti ogni volta che viene iniziato un nuovo ciclo di produzione, evitando così a contaminazione tra i diversi componenti. Durante il processo di laminazione del PCB, i diversi strati che compongono il PCB vengono posizionati e incollati in modo da formare un’unica scheda. Durante questa fase, alcuni produttori applicano un effetto di vuoto a bassa pressione, evitando la formazione di spazi vuoti che potrebbero intrappolare l'umidità al loro interno.
Un’altra tecnica comune è quella di utilizzare piani di rame con struttura intrecciata (meshed), in modo da creare dei legami più resistenti e impedire lo spostamento dell’umidità tra i diversi strati del PCB. Occorre tuttavia osservare come questi piani possono influire sulle prestazioni elettriche della scheda e il loro utilizzo deve, pertanto, essere opportunamente considerato.
Terminata la fabbricazione del PCB, è possibile applicare una finitura superficiale a scopo protettivo. In questo modo si mantengono integre le proprietà del PCB fino alla successiva fase di assemblaggio.
Assemblaggio
Per evitare che l'umidità presente nell’ambiente abbia effetti negativi sul PCB, la saldatura dei componenti dovrebbe essere eseguita a temperature elevate con un livello di umidità inferiore allo 0,1%, oppure a basse temperature con livello di umidità inferiore allo 0,2%. La saldatura ad alta temperatura viene eseguita intorno a 260°C, mentre la saldatura a bassa temperatura avviene intorno a 230°C.
Dopo aver completato il montaggio dei componenti sulla scheda, la cottura è una pratica comune ed efficace per rimuovere l'umidità. Occorre tuttavia assicurarsi di non oltrepassare il coefficiente di dilatazione termica (CTE) del materiale utilizzato per il PCB, evitando così che si creino delaminazioni o fessurazioni.
Probabilmente, la forma migliore di protezione di un PCB assemblato è quella di applicare uno tra i diversi tipi di rivestimento conforme. Questo rivestimento protegge non solo dall'umidità, ma anche da fluidi, agenti contaminanti e persino dai raggi ultravioletti.
Il rivestimento conforme consiste in una sottile pellicola polimerica applicata al PCB per proteggere la scheda e i suoi componenti dall'ambiente e dalla corrosione. La pellicola ha in genere uno spessore compreso tra 25 e 250 µm e ha la proprietà di adattarsi alla forma della scheda e dei suoi componenti, coprendo e proteggendo i punti di saldatura, i terminali e i pin dei componenti elettronici, le tracce esposte e altre aree metallizzate dalla corrosione, prolungando la vita operativa del PCB.
In Figura 4 sono visibili gli effetti corrosivi prodotti sul PCB dall’umidità o da altri agenti aggressivi nel caso di una scheda senza rivestimento conforme (immagine a sinistra) e con rivestimento conforme (immagine a destra). Questi rivestimenti formano uno strato uniforme che copre le superfici di un componente, garantendo una straordinaria repellenza a umidità, oli, sporco, impronte e altri contaminanti ambientali. I rivestimenti conformi forniscono protezione da diversi agenti corrosivi come umidità, acqua, nebbia salina, foschia e zolfo.
Figura 4: Scheda con e senza rivestimento conforme (Fonte: 3M)
Anche l'incapsulamento, che consiste nell’inserimento completo di una scheda assemblata all'interno di un involucro protettivo, può rivelarsi un metodo molto efficace, a condizione che l'involucro consenta all’umidità intrappolata di fuoriuscire verso l’esterno, ad esempio attraverso delle prese d'aria.
Un’alternativa all’incapsulamento completo consiste nel rivestimento parziale della scheda tramite opportune resine epossidiche che coprono solo alcune aree del PCB particolarmente sensibili all’umidità.
Stoccaggio
I PCB, assemblati o non, devono essere conservati nelle apposite buste protettive MBB e non in involucri che forniscono soltanto una protezione ESD.
È inoltre opportuno che i progettisti osservino le linee guide contenute negli standard IPC, le quali forniscono validi suggerimenti per l'imballaggio e la conservazione delle schede, riducendo al minimo la possibilità di diffusione dell'umidità.
La mancata applicazione della protezione dall'umidità del PCB alle schede può causare guasti alla scheda elettronica e costi inutili per riparazioni o sostituzioni. Tuttavia, applicando le tecniche elencate sopra per la fabbricazione, l'assemblaggio e l'imballaggio o stoccaggio, è possibile ridurre notevolmente la possibilità che l'umidità e altri agenti simili minaccino il funzionamento e l'affidabilità del PCB.
Conclusioni
Con l’attuale tendenza alla miniaturizzazione e alla crescita della densità di componenti, i progettisti devono affrontare nuove sfide per fornire ai PCB un adeguato livello di protezione dall’umidità e dagli agenti corrosivi. I dispositivi sensibili all'umidità, o MSD, hanno una maggiore sensibilità all'umidità che può rendere i dispositivi inutilizzabili.
Nell’articolo sono state illustrate le principali tecniche che, applicate durante le fasi di produzione, assemblaggio, immagazzinamento e spedizione della scheda consentono di fornire una valida e duratura protezione al circuito elettronico.
20.03.2023
e riceverete un preventivo per il vostro progetto di PCBA entro 10 minuti!