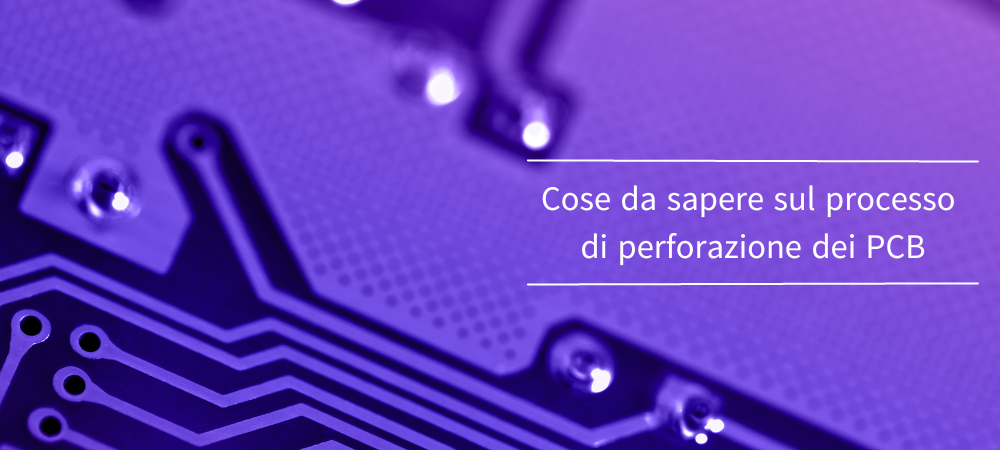
Completato il processo di laminazione, il PCB viene sottoposto alla fase di perforazione, che avviene seguendo le specifiche contenute nei file di perforazione (PCB NC drill file). Il processo di creazione dei fori nel circuito stampato viene eseguito per facilitare il posizionamento dei componenti, la realizzazione dei fori di via e la connessione elettrica tra i vari layer del PCB. Tra le varie fasi su cui si articola la produzione di un PCB, la perforazione è probabilmente la più costosa e dispendiosa in termini di tempo. Questo processo deve infatti essere eseguito con la massima precisione, poiché anche il più piccolo errore può avere effetti disastrosi sulla qualità del PCB.
La progressiva miniaturizzazione e l’incremento della densità di componenti dei dispositivi elettronici ha reso ancora più critica e delicata la fase di perforazione del PCB. Nel caso di circuiti stampati a singola o doppia faccia, il processo di foratura viene eseguito immediatamente dopo il taglio del PCB, mentre nel caso più generale di circuiti stampati multistrato, la foratura segue il processo di laminazione.
Opportune macchine perforatrici a controllo numerico (CNC) decodificano e applicano le informazioni contenute nel file di perforazione Gerber/ODB, come coordinate (X,Y) e dimensione dei fori. Durante il processo di perforazione, viene praticato un foro alla volta, rendendo questa fase piuttosto lenta. Per ottimizzare le operazioni, più pannelli PCB vengono sottoposti contemporaneamente alla perforazione.
Dopo la fase di perforazione, viene eseguito il processo di sbavatura, la cui funzione è quella di rimuovere le eccedenze di rame rimaste vicino ai bordi di ogni foro. La fase di sbavatura può essere eseguita utilizzando diverse tecniche, come la spazzolatura o la pulizia al plasma. Tutti i fori dovranno essere completamente privi di detriti per garantire una placcatura liscia e uniforme.
Tecniche di perforazione
I fori sul PCB possono essere creati utilizzando sia l’incisione elettrochimica (fresatura chimica), sia mediante mezzi meccanici come perforazione, taglio laser o punzonatura. L'aumento della densità dei fori passanti e la progressiva riduzione delle loro dimensioni, richiede tecniche di perforazione in grado di creare fori anche molto piccoli con accuratezza e ripetibilità.
Perforazione meccanica
L’elemento perforante è costituito da un mandrino pneumatico che ruota a velocità prossime a 300.000 giri/min. Per mantenere la precisione alle alte velocità, essenzaili per raggiungere la qualità del foro richiesta, la vibrazione della punta è controllata entro un intervallo di 10 micron. Per mantenere l'esatta posizione del foro sul PCB, il trapano è montato su un sistema servomeccanico che può muoversi lungo gli assi X e Y. Uno specifico attuatore viene invece utilizzato per controllare il movimento del PCB lungo l'asse Z. La perforazione ad alta velocità assicura pareti dei fori pulite ed è necessaria per ottenere una buona placcatura sulle pareti dei fori.
La perforazione meccanica crea fori di elevata qualità, privi di conicità alle estremità. Inoltre, la velocità di perforazione è maggiore rispetto ad altri metodi, consentendo di velocizzare il processo di produzione dei PCB. Se, tuttavia, i fori hanno dimensioni eccessivamente piccole, potrebbe accadere che la punta si rompa durante il processo di perforazione. Inoltre, ogni foro dovrà essere sottoposto a successiva sbavatura per rimuovere gli eccessi di rame lasciati dal processo di perforazione.
In Figura 1 è visibile una macchina a controllo numerico per la perforazione meccanica.
Figura 1: Macchina CNC per la perforazione meccanica
Perforazione laser
I trapani laser utilizzati nel processo di perforazione dei PCB sono basati su un complesso set di ottiche, in grado di eseguire con elevatissima precisione fori e microvie con diametro inferiori a 200 μm. La dimensione, o diametro, del foro da praticare nel PCB è determinata dall'apertura raggio laser, mentre la pofondità del foro è determinata dal tempo di esposizione. Un particolare set di lenti viene utilizzato per concentrare l'energia del raggio laser esattamente nel punto del PCB da perforare. Oltre a consentire la realizzazione di fori estremamente piccoli (come microvia e blind via), la perforazione laser presenta il vantaggio di eliminare la delaminazione.
La perforazione laser utilizza un raggio laser ad alta densità per realizzare dei fori nel PCB. Ance se esistono vari tipi di laser, utilizzati a seconda del tipo di materiale da tagliare, i due più comuni sono UV e CO2.
Il principale vantaggio della perforazione laser è quello di consentire l’ablazione di un'ampia gamma di materiali, riuscendo a praticare fori di diametro ridotto, non gestibili attraverso una perforazione meccanica di tipo convenzionale. Inoltre, la perforazione laser è una tecnica senza contatto e, come tale, non richiede una complessa selezione degli utensili di foratura come avviene con il processo manuale.
Tra gli svantaggi del processo di perforazione laser rientrano la difficoltà di ottenre un controllo accurato della profondità del foro se non è presente un layer di arresto in metallo e l’effetto bruciatura prodotto dal laser sui bordi del foro, che solitamente assumono un aspetto scuro o marroncino.
Come avviene con il sistema meccanico, anche con la perforazione laser è possibile sovrapporre più pannelli, a seconda del loro spessore. Le attuali macchine per la perforazione laser sono in grado di creare fori passanti con diamentro compreso tra 50 e 150 micrometri.
In Figura 2 sono visibili alcuni fori realizzati con una macchina per la perforazione laser dei PCB. Si noti l’estrema accuratezza dei fori, praticamente privi di imperfezioni o residui, nonstante le dimensioni molto piccole.
Figura 2: Esempi di fori e microvia realizzati con il sistema laser (Sorgente: Hitachi High-Tech)
Nuove tecniche di perforazione
Il numero di fori da praticare sui PCB è cresciuto in modo vertiginoso negli ultimi anni. Se il circuito stampato di un normale cellulare può richiedere da 30.000 a 50.000 fori, una scheda con componenti chip-scale package (CSP) può richiedere 300.000 o più fori. Occorrono quindi tecniche di perforazione in grado di fornire un elevato throughput per la produzione dei PCB.
Una nuova tecnica utilizzabile per praticare fori nel circuito stampato è l’esposizione diretta (nota anche come direct imaging). Basata sul principio di elaborazione delle immagini, questo nuovo metodo incrementa sia la precisione, sia la velocità, creando un'immagine digitale del PCB e convertendola in una mappa di posizioni utilizzate dal laser come riferimenti per i fori da praticare. La tecnica di esposizione diretta migliora la precisione dell'allineamento dei fori in quanto il sistema di elaborazione digitale delle immagini tiene conto della possibile espansione, contrazione e deformazione subita dalla scheda. In Figura 3 è visibile una moderna apparecchiatura per la fabbricazione di PCB con esposizione diretta.
Figura 3: Apparecchiatura per la produzione di PCB con esposizione diretta
Tipi di fori
Quando si devono praticare dei fori nel PCB, occorre tenere in considerazione due aspetti importanti. Il primo è l’aspect ratio, che influisce direttamente sulla capacità di eseguire la placcatura di rame all’interno dei fori. Questo processo diventa infatti problematico quando si diminuisce il diametro e si aumenta la profondità del foro. L’aspect ratio (AR), definito come il rapporto tra la profondità del foro ed il suo diametro, assume il valore tipico di 10:1 per i fori passanti e 0,75:1 per i microvia. Il valore di AR dovrebbe in generale essere mantenuto molto piccolo, in modo tale da semplificare il processo di perforazione ed evitare un’eccessiva usura della punta nel caso di perforazione meccanica.
Il secondo aspetto riguarda la distanza che intercorre tra il bordo di un foro e la più vicina area di rame sul PCB (traccia, piazzola o altro). Il valore minimo di tale distanza, al fine di evitare possibili malfunzionamenti del circuito, è normalmente pari a 8 mil.
I principali tipi di fori praticabili sul PCB possono essere suddivisi in tre categorie:
- Fori di via. Questi piccoli fori con placcatura metallica sono utilizzati per trasmettere segnali elettrici, segnali di alimentazione e massa attraverso i vari layer del PCB. A seconda del tipo, si possono avere via passanti (through-hole, attraversano completamente più layer del PCB), buried (fori interni allo stackup, senza estensione sui due layer superficiali), ciechi (blind, partono dai layer superficiali per interrompersi poi su un layer interno) e micro via (più piccoli dei precedenti, realizzati esclusivamente con apparecchiature laser)
- Fori per il passaggio dei componenti through-hole. Questi componenti includono connettori, switch e altri component meccanici che richiedono un assemblaggio robusto garantito da un package through-hole. Questo tipo di package è molto adatto ai componenti di potenza come grandi resistenze, condensatori, amplificatory operazionali e regolatori di tensione, i quali generano una quantità non trascurabile di corrente e calore
- Fori meccanici. Si tratta in questo caso dei fori praticati per il montaggio meccanico del contenitore, ventole, radiatori, o altro. Inoltre, questi fori possono essere praticati per facilitare l’allineamento del PCB con le macchine per la produzione automatizzata.
Fasi della foratura
Il processo di perforazione del PCB può essere suddiviso in quattro fasi, descritte di seguito.
1 - Fori di posizionamento
I fori di posizionamento servono come punti di riferiamento durante il processo di produzione e test di un PCB. Prima di eseguire la perforazione, il pannello di supporto, il substrato e un foglio di alluminio vengono posizionati sul tavolo della perforatrice ad alta velocità, ordinati dal basso verso l'alto. In base alle specifiche di produzione, sul bordo della scheda vengono praticati alcuni fori di posizionamento con diametro di alcuni millimetri.
2- Inserimento dei perni
Per aumentare l'efficienza produttiva, più schede vengono sovrapposte le une alle altre prima di eseguire la perforazione. Le schede vengono fissate sul tavolo della perforatrice utilizzando gli appositi perni, evitando così possibili spostamenti durante la perforazione.
3- Esecuzione dei fori
Il processo di perforazione è eseguito da apparecchiature automatiche a controllo numerico. Pertanto, è sufficiente inserire i file contenenti i parametri di perforazione convertiti in comandi CAM per eseguire i fori corrispondenti. La perforazione meccanica è uno dei metodi più comunemente utilizzati per praticare fori nei PCB. La punta del trapano, ruotando ad alta velocità, esegue diversi tipi di fori, inclusi i fori passanti placcati (PTH), i fori passanti non placcati (NPTH) e i fori passanti. Prima della perforazione, viene posizionato un pannello di supporto sotto il pannello da forare per proteggere la superficie del trapano, mentre sulla parte superiore viene posato un foglio di alluminio per rendere più piatti i fori nella lamina di rame ed evitare il surriscaldamento della punta.
4- Ispezione dei fori
Terminata la perforazione, occorre controllare la posizione e l'apertura di ogni foro. Dopo aver verificato che non vi siano problemi come fori extra, fori mancanti o spostamento della posizione dei fori, il PCB è pronto per essere sottoposto alla fase di produzione successiva.
10.05.2023
e riceverete un preventivo per il vostro progetto di PCBA entro 10 minuti!