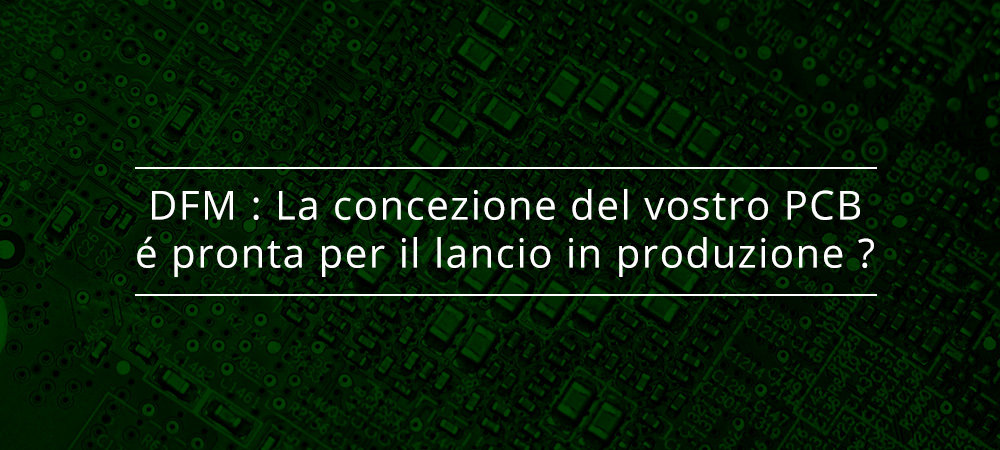
Il termine DFM (Design for Manufacturing) fa riferimento al processo grazie al quale un prodotto é concepito con lo scopo preciso di semplificare la fabbricazione al fine di realizzare un prodotto migliore con un costo inferiore. Idealmente, il DFM, dovrebbe essere già applicato nel corso iniziale del progetto e dovrebbe implicare tutto il team di sviluppo dei prodotti e non unicamente gli ideatori. Man mano che il progetto progredisce attraverso i differenti stadi del ciclo di vita del prodotto, ogni modifica acquista un peso e un costo crescente (ogni modifica lo rende più complesso e aumenta il suo costo), fino a che non diventa sempre più difficile da realizzare.
D’altra parte, l’applicazione del DFM durante le prime fasi di sviluppo del PCB permette di effettuare rapidamente tutte le eventuali modifiche, al costo più basso possibile, mantenendo sempre le performances d’origine del prodotto. La tecnologia ha un ruolo chiave in numerosi aspetti delle nostre vite : smartphones, orologi connessi, elettrodomestici, auto connesse.. utilizzano tutti una tecnologia e una connettività intelligente. Questi prodotti e altri ancora, necessitano di circuiti stampati molto complessi che devono essere prodotti al minor costo possibile, in tempi sempre più brevi e con un livello di qualità sempre più alto.
Vantaggi del DFM
La fabbricazione del PCB é divisa in più tappe e al fine di evitare problemi importanti durante la fabbricazione (DFM), é necessario assicurarsi in anticipo che un circuito non sia affetto da nessun problema di concezione. Durante la fase di sviluppo, i creatori, devono sottomettersi a degli impedimenti elettrici e alla gestione termica.
Nell’utilizzo reale, cio’ nonostante, altri fattori entrano in gioco, come la precisione la tolleranza delle macchine di fabbricazione dei circuiti stampati. E le caratteristiche dei materiali utilizzati. Il DFM designa perfettamente il processo che permette d’organizzare la disposizione del pcb per assicurarsi che sia realizzabile. Prendiamo per esempio un anello residuo o la zona delle pasticche di rame che restano all’interno dopo aver realizzato un foro.
La taglia dell’anello é misurata dal bordo della pastiglia al bordo del foro e rappresenta un parametro fondamentale nella concezione del PCB, poiché la metallizzazione posata sopra permette la connessione elettrica da una parte all’altra dei suoi lati. In questo caso nei pcb multistrato, gli anelli residui devono essere allineati con una strato coprente sufficiente per permettere la connessione fra strati differenti.
L’allineamento pefetto non esiste per permettere la connessione fra strati differenti. L’allineamento perfetto non esiste che in teoria : anche le foratrici più moderne non possono avere una precisione al 100%. Il porcesso DFM garantisce che la larghezza dell’anello permetta un leggero disallineamento fra gli strati senza compromettere la connessione elettrica.
I principali vantaggi del DFM applicato alla concezione e alla fabbricazione dei PCB sono i seguenti :
- Una migliore qualità del prodotto : DFM riduce il numero di modifiche necessarie per adattare la concezione originale al processo di fabbricazione e alle fabbriche dei pcbs , per evitare di compromettere la qualità del prodotto ;
- Riduzione del tempo di messa sul mercato : il processo di fabbricazione é diviso in più tappe, ognuna puo’ essere all’origine di errori potenziali. DFM aiuta a ridurre i ritardi causati da prodotti difettosi, gli errori e il tempo trascorso a verificare la revisione e la documentazione dei progetti ;
- Riduzione dei costi : DFM permette agli ideatori del PCB di concepire dei circuiti che possono essere facilmente prodotti anche in grandi volumi di produzione. Il numero più basso di errori detectati durante il proceso di fabbricazione dei PCBs permette di ridurre i costi.
DFM contro RDC
Gli ideatori di circuiti stampati eseguono spesso una procedura chiamata : verificazione delle regole di concezione (DRC : design rule check). Ma dopo aver lanciato con successo la RDC, é necessario ugualmente realizzare il DFM ? Si, poiché le due procedure sono differenti ma sono entrambe necessarie per lanciare la produzione del PCB. L’RDC é un processo d’analisi automatico che compara il progetto alle regole imposte dalla fonderia.Queste regole definiscono l’esigenze fisiche minimali per i PCB, gli strati e le connessioni che possono avere un impatto sulle performances del sistema.
Lo scopo dell’ RDC é di detectare tutti gli scarti o errori eventuali. Quanto al DFM, questo identifica, tutti gli aspetti che potrebbero generare problematiche importanti durante il processo di fabbricazione dei PCBs : se il porcesso DRC detecta un errore, questo sarà presente ugualmente su ogni esemplare del circuito stampato. I problemi riscontrati dal DFM, d’altro canto, non possono prodursi che su certe unità della carta e anche dopo un lungo periodo di produzione.
e riceverete un preventivo per il vostro progetto di PCBA entro 10 minuti!
Come applicare i principi DFM e PCBs
Anche se le norme di fabbricazione dei PCB possono essere diverse per ogni fabbricante, certe regole generali DFM devono essere rispettate prima di applicare tutti i processi di fabbricazione. Al fine di dichiarare una concezione del PCB pronta per la produzione, certi principi di base DFM devono essere applicati. Ecco una lista delle direttive più pertinenti :
- Spazio fra i componenti : i componenti troppo vicini gli uni agli altri sul circuito stampato possono creare problemi al sistema automatico utilizzato per l’assemblaggio, anche per le macchine pick and place, rendendo il ritocco della concezione problematico. La stessa cosa puo’ accadere per i connettori, che devono essere correttamente posizionati, al fine di semplificare le connessioni della carta con l’esterno.
- Posizionamento e rotazione dei componenti : la maniera con cui i componenti sono posizionati sul PCB puo’ inficiare sul processo di sudura e in particolare se sono disposti in maniera irregolare o disuguale. Tutti i componenti similari devono essere orientati nella stessa direzione assicurandosi che siano correttamente saldati una volta che saranno passati nel forno per la brasatura.
- La taglia dei pads dei componenti : se non corretta, puo’ provocare un riscaldamento irregolare durante la brasatura a refusione che puo’ provocare a sua volta il distacco parziale del componente. Questo fenomeno é conosciuto come ‘’ effetto Manhattan”.
- Trappole da acido : il posizionamento delle piste del PCB deve evitare degli angoli ‘’vivi’’che possono provocare gravi problemi di pulizia del prodotto chimico utilizzato per le incisioni sul PCB, creando inesorabilmente una riduzione dello spazio fra le piste stesse. Assicurandosi che gli angoli fra le piste siano sempre inferiori a 90°, evitiamo le tracce di delaminazione dopo la produzione del PCB.
- Ottimizzazione dei fori : numerose concezioni di PCB utilizzano troppe taglie di fori diversi, questo é da evitare assolutamente al fine di ridurre i costi di produzione.
- Assenza di maschera di sudura fra i pads : questo puo’ provocare dei ponti di sudura e potenzialemente corto-circuitare due borchie che non devono essere connesse. Di conseguenza, verificate sempre scrupolosamente che ogni pasticca abbia solder a sufficienza per garantire lo spazio richiesto.
- Serigrafia sulle pasticche : la sovrapposizione, anche parziale, della serigrafia sulle pasticche crea problemi di brasatura, con delle conseguenze potenzialmente disastrose a lungo termine. La figura 1 mostra un esempio di sovrapposizione che bisogna assolutamente evitare.
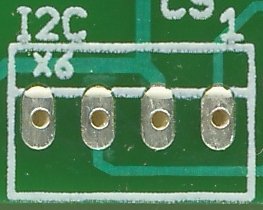
Figura 1 : Esempio di serigrafia su pasticche
- Controllo a ciclo aperto : questa situazione si presenta generalmente quando il progetto d’orgine é rilavorato per apportare delle modifiche. Creare delle nuove connessioni senza il preesistente puo’ generare un ciclo senza fine.
- Validazione dei files utilizzati per il porgetto : I gerber devono essere l’oggetto di una vigilanza particolare poiché presentano dei problemi quando un progetto si traduce in un oggetto fisico. Un file separato é necessario per ogni strato del PCB : questo significa che dovete mantenere numerosi documenti evitando che si mescolino o si confondano gli uni con gli altri.