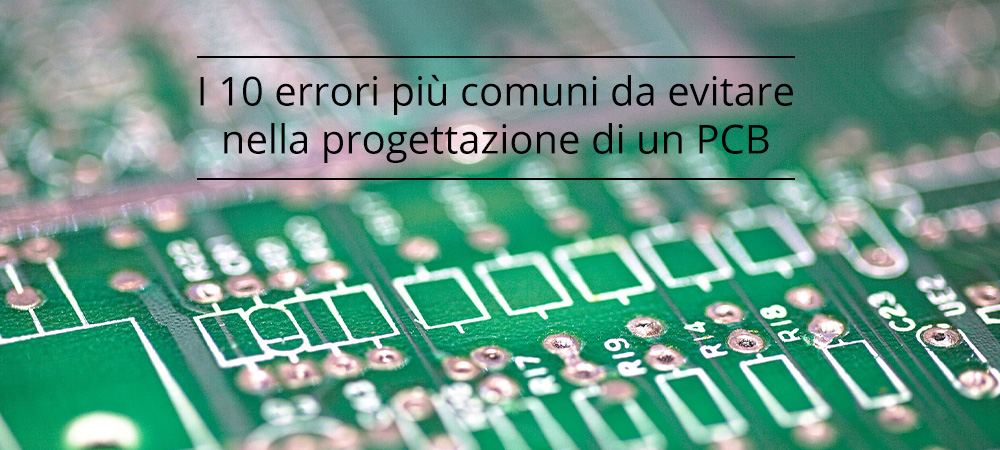
Il circuito stampato, o PCB, rappresenta il cuore e l’anima di ogni circuito elettronico. Essendo responsabile del collegamento elettrico tra i componenti e dell’interfacciamento del dispositivo con il mondo esterno, è evidente che anche il più piccolo errore di progettazione può causare ritardi o costi addizionali durante la fabbricazione, o addirittura condurre al malfunzionamento o al completo fallimento del circuito. I più recenti e innovativi strumenti di fabbricazione consentono ai produttori di circuiti stampati di ridurre sensibilmente, rispetto al passato, i costi di produzione. In alcune occasioni, tuttavia, i costi di produzione possono aumentare a causa degli errori commessi nella fase di progettazione del PCB. Detto ciò, occorre sottolineare come gli errori non siano improbabili nemmeno per i progettisti di PCB più esperti; il nostro consiglio è quello di seguire alcune semplici regole per evitare di ripetere i dieci errori di progettazione più comuni, che ora descriveremo.
1 – Errata geometria delle tracce
Le tracce di un PCB hanno la responsabilità di trasmettere i segnali elettrici tra i vari componenti del circuito, rispettando precisi vincoli legati a velocità, intensità di corrente e frequenza del segnale. In questo contesto assume un ruolo fondamentale la geometria di ogni traccia; in particolare, è necessario dimensionare opportunamente larghezza e spessore di ogni traccia. Quando la corrente che attraversa una traccia supera il valore indicativo di 0,5 A, si può parlare di linea di trasmissione di potenza, o ad elevata corrente. In tal caso, non è più possibile utilizzare la larghezza standard usata nei circuiti di bassa potenza, ma questa deve essere opportunamente dimensionata utilizzando, ad esempio, i calcolatori basati sullo standard IPC-2221 o successivi per tracce interne (stripline) ed esterne (microstrip). Occorre inoltre osservare che le tracce poste sugli strati esterni del PCB possono trasportare, a parità di spessore, una corrente superiore, in quanto possono trarre vantaggio da un flusso d’aria e una dissipazione termica superiori. La larghezza della traccia dipende dalla quantità di rame utilizzata per quello strato. Oltre alla larghezza, anche lo spessore di ogni traccia deve essere opportunamente dimensionato. La maggior parte dei produttori di PCB consente di scegliere tra vari strati di rame, da 0,5 oz/ft2 a 2,5 oz/ft2 e oltre. Molti progettisti scelgono spesso come spessore il valore standard, pari a un'oncia di rame (1 oz, corrispondente a 35 µm). Tuttavia, questo valore potrebbe non essere sufficiente per le tracce di alta potenza, dove si utilizza tipicamente uno spessore di 2 oppure 3 once. Il vantaggio di uno spessore maggiore è quello di presentare una minore resistenza al passaggio della corrente, con conseguente miglioramento della dissipazione termica. Gli svantaggi sono legati a maggiore peso e necessità di maggiore isolamento delle tracce.
2 – Layout inadeguato
Poiché la domanda per circuiti stampati con dimensioni sempre più miniaturizzate è in continua crescita, i progettisti sono costretti a utilizzare componenti con footprint più piccolo e a ridurre la distanza tra i componenti. Se si utilizza un layout inefficiente, c'è il rischio di incontrare problemi di connessione o di non conformità. Ciò è particolarmente vero quando si utilizzano componenti con passo più piccolo e con maggiore numero di pin. Per garantire la funzionalità desiderata, è molto importante selezionare una tecnica di layout adatta alle esigenze del particolare circuito. Un espediente molto utile è quello di inserire sul PCB uno spazio sufficiente per componenti addizionali (o alternativi a quelli attuali), che potrebbero essere necessari in un immediato futuro. Nel caso in cui questi componenti aggiuntivi non siano utilizzati, è sempre possibile rimuoverli prima della fabbricazione.
e riceverete un preventivo per il vostro progetto di PCBA entro 10 minuti!
3 – Errata posizione dei condensatori di disaccoppiamento
I condensatori di disaccoppiamento sono necessari sulle linee di alimentazione del PCB, al fine di garantire a tutti i componenti della scheda una alimentazione stabile ed esente da transitori o oscillazioni. È assolutamente necessario che tali condensatori siano collegati sempre in parallelo con l'alimentazione e posti il più possibile vicino ai pin dei componenti che richiedono l’alimentazione. La linea di alimentazione proveniente dalla sorgente di alimentazione deve essere instradata correttamente sul PCB, in modo da arrivare al condensatore di disaccoppiamento prima di andare al pin che necessita di una tensione stabile. Si osservi come, in caso contrario, la funzione di disaccoppiamento non possa funzionare regolarmente; tutti i regolatori di tensione utilizzano infatti un circuito di retroazione che può oscillare se non adeguatamente stabilizzato.
4 – Errori relativi ai landing pattern
Anche se i termini landing pattern e footprint sono spesso utilizzati in modo interscambiabile, esiste una sottile differenza tra di essi. Più precisamente, i landing pattern si riferiscono alla dimensione dei pad e, per ogni componente, dovrebbero sempre avere un’area leggermente superiore a quella del corrispondente footprint. Anche un errore di mezzo millimetro nella misurazione della spaziatura da pad a pad può dimostrarsi fatale nella saldatura durante il processo di produzione, causando disallineamenti tra componenti e PCB. I migliori software CAD PCB includono un’ampia raccolta di librerie che includono sia il simbolo schematico che il landing pattern per ogni componente. Se si utilizza un componente non incluso in queste librerie, occorre disegnare a mano il simbolo elettrico e il landing pattern per il PCB. In questa fase, non è rara la possibilità di commettere qualche errore; ad esempio, se la distanza tra due pad è inferiore al millimetro, i pin non si allineano correttamente, rendendo impossibile la saldatura. In Figura 1 sono visibili le dimensioni relative al landing pattern per un componente con package PG-TQFP-64-19, ricavate direttamente dal datasheet. Normalmente, i produttori di componenti elettronici seguono i requisiti contenuti nello standard IPC-7351B (“Generic Requirements for Surface Mount Design and Land Pattern Standards”).
Figura 1: Esempio di specifiche per un landing pattern (Fonte: NXP).
5 – Eccessivo affidamento sul routing automatico
Per i PCB che presentano una complessità non elevata, la tendenza di alcuni progettisti è quella di affidarsi alla funzionalità di sbroglio automatica, oggi offerta dalla maggior parte degli strumenti di progettazione dei PCB. Tuttavia, lo sbroglio automatico tende ad occupare un’area del PCB superiore a quella desiderabile e a creare fori di via di dimensioni maggiori rispetto a quanto ottenibili con il routing manuale. È un dato di fatto che il numero di tracce del PCB, insieme al numero di fori di via, influisce direttamente sul costo di fabbricazione del PCB.
6 – Fori di via ciechi o interrati
I fori di via sono molti comodi, in quanto permettono di risolvere molte situazioni di routing complesse e migliorano lo scambio termico del PCB; tuttavia, essi vanno utilizzati con cautela e giudizio. I fori di via ciechi (tipo “1” in Figura 2) devono essere utilizzati per collegare un layer esterno con uno interno, mentre i fori di via interrati (tipo “2” in Figura 2) per collegare tra loro due layer interni. I fori di via passanti (tipo “3” in Figura 2) devono invece essere utilizzati soltanto per collegare i due layer esterni del PCB ed eventualmente qualche layer interno. Per creare un foro di via, è necessario specificare la dimensione, la dimensione del foro, le tolleranze e altri attributi. Essi possono essere creati a partire da modelli, oppure è possibile definirli al volo. Si tenga inoltre presente come i fori di via ciechi e interrati comportino un maggiore costo di produzione, per cui si consiglia di pianificarne in anticipo l’utilizzo in modo tale da rispettare il budget allocato al PCB.
Figura 2: Tipi di fori di via (Fonte: Altium).
7 – Lunghezza eccessiva delle tracce
Le tracce che portano segnali ad alta velocità dovrebbero essere più corte e rettilinee possibile. Se si eccede con la lunghezza, si possono incontrare seri problemi come riflessione del segnale (con conseguenze dirette sull’integrità del segnale), maggiore sensibilità alle interferenze elettromagnetiche (EMI) e, ovviamente, costi maggiori. Se la lunghezza di una traccia supera un decimo della lunghezza d’onda del segnale che la attraversa, si può parlare di linea di trasmissione. In questo caso, oltre alla lunghezza, diventa fondamentale eseguire un calcolo dell’impedenza (utilizzando uno dei numerosi tool disponibili) in modo tale da garantire l’accoppiamento di impedenza ed evitare perdite di potenza del segnale.
8 – Interferenze elettromagnetiche (EMI)
Le interferenze elettromagnetiche sono spesso causate da una progettazione impropria del PCB. Per ridurre l'EMI su un PCB, si consiglia di raggruppare gli elementi in base alla loro funzionalità, ad esempio blocchi analogici e digitali, sezione di alimentazione, circuiti a bassa velocità, circuiti ad alta velocità, e così via. Inoltre, è necessario ridurre, o meglio eliminare, gli angoli retti sulle tracce, utilizzando contenitori metallici e cavi schermati per assorbire le interferenze.
9 – Layout incorretto dell’antenna
Nel caso in cui il PCB includa antenne per la comunicazione wireless, occorre prestare molta attenzione per non commettere errori di layout. Al fine di massimizzare il trasferimento di potenza, occorre anzitutto adattare l’impedenza tra il transceiver e l’antenna. Normalmente, la linea di trasmissione che collega il transceiver con l'antenna dovrebbe avere un'impedenza di 50 Ω. Per una regolazione accurata dell'impedenza, è preferibile posizionare tra l'antenna e il transceiver un filtro accordatore a Pi greco (LC), oppure un qualsiasi altro circuito di adattamento.
10 – Mancanza di revisione del progetto
Spesse volte sottovalutata, la revisione del progetto è in realtà uno degli elementi più importanti nel processo di sviluppo del PCB. Le revisioni periodiche del progetto permettono di verificare la conformità con i requisiti di alto livello del progetto, le funzionalità assegnate al PCB e le interconnessioni tra i vari circuiti. Ciò consente di evitare, o individuare in anticipo, gli errori di progettazione più comuni; una peer review eseguita da altri membri del team di sviluppo è spesso in grado di individuare errori il progettista non aveva notato in precedenza.