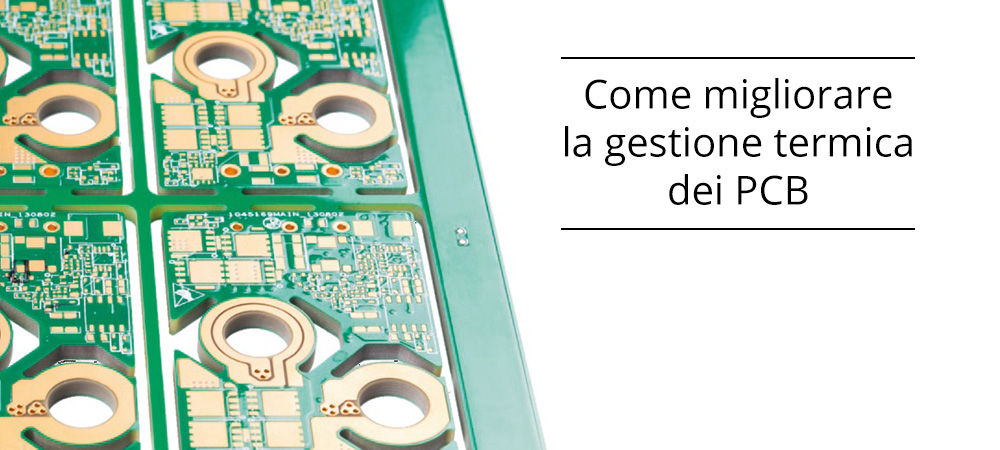
I circuiti stampati, il cuore di ogni dispositivo elettronico, sono progettati per consentire la conduzione elettrica e la trasmissione di segnali analogici e digitali tra differenti componenti elettronici. Durante il suo tragitto all’interno del PCB, l’elettricità genera una quantità più o meno elevata di calore, funzione della quantità di resistenza che essa incontra. Oltre alle tracce, i principali responsabili della produzione di calore sono i componenti di potenza, come transistor MOSFET, IGBT, convertitori e circuiti driver. Anche se le tensioni di alimentazione dei dispositivi logici ad elevata integrazione, come DSP, SoC e FPGA stanno progressivamente diminuendo, anche questi dispositivi sviluppano una quantità di calore non trascurabile, dovuta sia alle elevate frequenze operative che all’uso intensivo di algoritmi ad elevata complessità computazionale. La gestione termica è uno degli aspetti più critici e insidiosi che i progettisti devono affrontare durante la progettazione di un PCB. Da un lato, occorre garantire il corretto funzionamento e l’affidabilità del circuito con ogni valore di tensione, corrente e frequenza ammissibile, dall’altro occorre rispettare i vincoli di budget imposti dal produttore, limitando l’utilizzo di ingombranti e costose soluzioni di raffreddamento come dissipatori, ventole o raffreddamento con liquido.
Importanza della gestione termica
Gli attuali componenti basati sul silicio presentano una temperatura di giunzione compresa tra circa 125°C e 200°C. Occorre tuttavia evitare di raggiungere tale valore, pena un rapido degrado della vita residua del componente. Si stima infatti che un incremento della temperatura operativa di 20°C, dovuto a una inefficiente gestione termica, possa ridurre la durata del componente fino al 50%. I led ad elevata luminosità utilizzati nel settore dell’illuminazione convertono in calore oltre il 60% della potenza assorbita e pertanto richiedono dei circuiti stampati particolari in grado di gestire elevate temperature senza danneggiare i componenti. La crescente diffusione dei semiconduttori wide bandgap (WBG), come arseniuro di gallio (GaN) e carburo di silicio (SiC), ha permesso ai componenti di raggiungere temperature di esercizio e potenze più elevate rispetto alla tecnologia basata sul silicio. Ciò, tuttavia, non ha eliminato la necessità di un’accurata gestione termica, in grado di distribuire uniformemente il calore sviluppato, evitare la formazione di pericolosi punti di accumulo del calore (‘hot-spot’) e minimizzare le perdite di potenza. In Figura 1 è visibile l’immagine di un circuito elettronico sottoposto a scansione termica tramite telecamera a raggi infrarossi: le parti colorate di rosso corrispondono ai punti di maggiore accumulo del calore.
Figura 1: Scansione termica di un circuito elettronico.
Consigli per una corretta gestione termica
Il primo passo per raggiungere una gestione termica soddisfacente anche in presenza di elevati carichi di potenza consiste nell’individuare, in base alle caratteristiche tecniche di ogni componente, la temperatura di giunzione TJ del semiconduttore e la resistenza termica RT. Il primo valore può essere dedotto dal datasheet del componente, mentre il secondo è definito come la differenza di temperatura che si verifica lungo il cammino percorso dal calore. In particolare, RT può essere minimizzata riducendo la lunghezza del cammino percorso dal calore, oppure aumentando la conduttività termica del materiale e l’area delle piazzole del PCB. Entrambi questi fattori riguardano il layout del PCB, che pertanto deve essere progettato sin dall’inizio per soddisfare questi requisiti. La crescente corsa verso la miniaturizzazione dei circuiti di potenza pone dei seri limiti all’aumento dell’area delle piazzole. Pertanto, per migliorare la gestione termica, il progettista può intervenire sui seguenti due fattori:
- la lunghezza del percorso seguito dal calore sul PCB deve essere più corta possibile;
- i materiali e i substrati che compongono il PCB, come gli eventuali dissipatori, devono possedere una conduttività termica più elevata possibile.
Il primo requisito può essere soddisfatto adottando particolari accorgimenti durante la progettazione del circuito stampato, mentre il secondo richiede un’accurata scelta dei materiali da compiersi durante le fasi preliminari del progetto, ad esempio lo studio di fattibilità.
Layout del PCB
Le tecniche che il progettista elettronico ha a disposizione per ridurre la lunghezza del cammino termico sul PCB sono diverse. Anzitutto, si consiglia di aumentare la distanza tra le tracce, ottenendo così una distribuzione più uniforme del calore sul layer, riducendo il rischio che si creino degli hot spot. Questa soluzione, tuttavia, è spesso limitata dall’esigenza (come avviene nel caso degli indossabili) di ottenere dimensioni del PCB miniaturizzate. Oltre alla distanza, anche la geometria delle tracce è un fattore molto importante. Le tracce che uniscono componenti di potenza dovrebbero essere più corte e larghe possibile, utilizzando spessori di rame spesso per le tracce percorse dalle correnti più elevate. I valori minimi raccomandati per l’ampiezza delle tracce, funzione dell’intensità della corrente che le attraversa, possono essere ricavati dai diagrammi dello standard IPC-2221 (e successive versioni) per la progettazione dei PCB. Se si utilizzano delle tracce troppo piccole per una determinata corrente, si corre il rischio di ottenere un degrado delle prestazioni o addirittura la rottura dei componenti; nel dubbio, è sempre preferibile utilizzare delle tracce di larghezza più ampia. Un’altra tecnica comunemente utilizzata è quella di inserire dei vias termici lungo i cammini di dissipazione del calore. I vias termici, che possono essere placcati o non placcati, collegano tra loro layer differenti, favorendo la circolazione di aria fresca ed evacuando il calore. I vias termici placcati sono più efficienti, in quanto il rivestimento di rame permette di accumulare una quantità maggiore di calore. Oltre ai vias termici, un’altra tecnica in grado di sottrarre calore ai componenti consiste nel creare nel PCB ampi piani di rame, aumentando così la superficie utile in grado di disperdere il calore. Anche se la dissipazione migliore si ottiene con piani di rame realizzati sugli strati superiore e inferiore del PCB, dove è maggiore la quantità di calore scambiata con l’ambiente circostante, tali piani possono essere creati anche sugli strati interni del PCB. Nelle applicazioni di potenza, un modo per ottenere un’efficace dissipazione del calore consiste nell’utilizzo della tecnologia heavy copper, sviluppata per incrementare la massima corrente tollerabile e la resistenza alla temperatura del PCB, senza incorrere in guasti o funzionamenti degradati. Mentre i PCB standard hanno tracce con spessore compreso tra circa 0.5 e 3 once (105 µm), la tecnologia heavy copper utilizza tracce con spessore che può arrivare a 60 once (2,1 mm), in grado di sopportare correnti di diversi ampere. In Figura 2 è visualizzato un esempio di PCB realizzato con la tecnologia heavy copper.
Figura 2: Esempio di PCB heavy copper.
Scelta dei materiali
Anche se l’FR-4 (Flame Retardant Level 4) è in grado di soddisfare i requisiti di dissipazione termica per molte tipologie di circuiti elettronici, esistono numerose applicazioni dove è necessario utilizzare materiali e substrati specifici. Tali applicazioni includono i circuiti dove sono presenti segnali di elevata frequenza e/o potenza, le applicazioni a radio frequenza (RF) e i dispositivi dove, a causa del footprint estremamente ridotto, non è possibile utilizzare dissipatori o altri sistemi di raffreddamento (elettromedicali e indossabili). Per ottenere una migliore dissipazione termica, il materiale deve possedere una elevata costante dielettrica (Dk). Anche se comportano un costo superiore, i laminati Rogers soddisfano questo requisito grazie a un valore di Dk compreso tra circa 6,15 e 11, rispetto a un Dk di circa 4,5 offerto dall’FR-4. Inoltre, questo materiale presenta una stabilità elevata al variare della temperatura e della frequenza, riducendo così le perdite di potenza in ogni condizione operativa. Un’altra tecnica costruttiva, nota come MCPCB (Metal Core Printed Circuit Board), consiste nel combinare substrati di materiali con differenti conduttività termiche con piani metallici, tipicamente di rame. La tecnologia MCPCB utilizza un prepreg termicamente conduttivo posto tra gli strati del PCB, con la funzione di sottrarre calore ai componenti per instradarlo verso i piani metallici. La tecnica MCPCB, che può impiegare un piano metallico singolo oppure doppio (entrambe le facce superiore e inferiore del PCB), è ampiamente utilizzata nelle applicazioni di illuminazione con led di potenza o ad alta luminosità. Se il calore prodotto è concentrato in un numero ristretto di componenti, si può inoltre utilizzare la tecnica copper coin. Sfruttando l’elevata conducibilità termica del rame, si inseriscono dei pezzi dello stesso metallo all’interno o sulla superficie del PCB, tipicamente sotto i componenti di elevata potenza.
e riceverete un preventivo per il vostro progetto di PCBA entro 10 minuti!
Conclusioni
Una gestione termica di successo inizia con una corretta progettazione del PCB. I progettisti hanno oggi a disposizione un’ampia varietà di tecniche in grado di ridurre la quantità di calore prodotto e migliorarne la dispersione. La scelta dei materiali, delle tecniche di fabbricazione e la definizione del layout sono i principali passi che occorre percorrere per ottenere risultati soddisfacenti. La disponibilità di strumenti software in grado di eseguire una analisi termica CFD (Computational Fluid Dynamics), anche in 3D, permette ai progettisti di simulare come avviene il trasferimento di calore nell’intero circuito, orientandoli in anticipo verso la soluzione più adatta alla specifica applicazione.