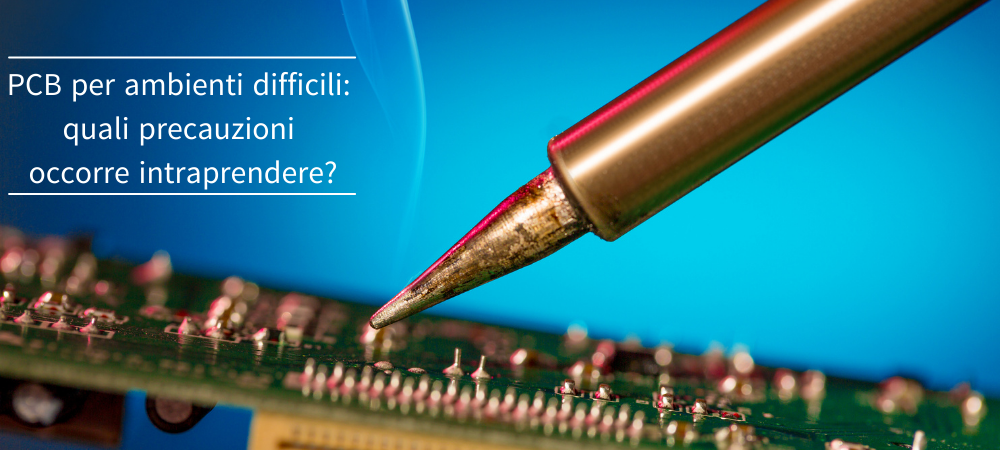
Alcune categorie di dispositivi elettronici devono operare in condizioni particolarmente difficili, come presenza di nebbia salina, salsedine, polvere, sabbia, o temperature estreme. Per garantire che il circuito elettronico continui a funzionare come nelle condizioni normali, è necessario che il PCB sia stato progettato per sopportare anche questi eventi senza subire danni.
I circuiti impiegati nei settori automotive, industriale e aerospaziale, ad esempio, sono continuamente sottoposti a vibrazioni, sollecitazioni meccaniche, escursioni termiche molto ampie e altro ancora. Ad esclusione di alcune classi di elettromedicali, pochi dispositivi elettronici operano in ambienti privi di polvere, vibrazioni, umidità e con temperature strettamente controllate. Nella realtà, occorre avere a che fare con:
- vibrazioni e sollecitazioni meccaniche;
- variazioni estreme di pressione (legate a variazioni di altitudine);
- variazioni estreme di temperatura;
- polvere, grasso o altri agenti chimici;
- umidità;
- radiazioni ionizzanti;
- interferenze elettromagnetiche, sia radiate che condotte;
- scariche elettrostatiche e transitori di tensione/corrente.
e riceverete un preventivo per il vostro progetto di PCBA entro 10 minuti!
Le sfide da affrontare
Le principali sfide che i PCB per ambienti difficili devono affrontare possono essere così sintetizzate:
- umidità, polvere e sporcizia: per contrastare questi fattori ambientali, è spesso necessario trattare il PCB con un processo speciale noto come rivestimento conforme (o conformal coating). Con esso, il PCB viene ricoperto dopo la fase di assemblaggio da un sottile strato di materiale protettivo non conduttivo come silicio, acrilico, uretano o p-xilene. Il rivestimento consente di prolungare la durata del circuito elettronico proteggendolo dagli agenti contaminanti esterni;
- temperature elevate: se il PCB deve operare in modo continuativo a temperature superiori allo standard, è meglio utilizzare layer con uno spessore di rame maggiore (heavy copper). Spessori di rame superiori a 3 once per piede quadrato vengono tipicamente abbinati all’applicazione del rivestimento conforme per fornire alla scheda un elevato livello di protezione nel caso di funzionamento ininterrotto alle alte temperature. L'impiego di layer con temperatura di transizione vetrosa (Tg) più elevata (come l’FR-4 TG140 o TG170), fornisce al PCB un’ulteriore protezione dalla temperatura;
- radiazioni ionizzanti: i PCB per applicazioni aerospaziali sono bombardati da particelle di vario tipo, oltre alle onde elettromagnetiche generate dal sole e da altri corpi celesti. Queste radiazioni possono causare disturbi temporanei (come inversione dei bit o cancellazione della memoria) o danni permanenti ai componenti;
- urti e vibrazioni, soprattutto nelle applicazioni automotive e aerospaziali;
- corrosione: è una delle principali insidie per ogni parte metallica. La corrosione si verifica quando l'ossigeno e il metallo si legano tra loro tramite un processo noto come ossidazione. Questo produce ruggine e fa sì che il metallo perda le sue proprietà chimiche, decomponendosi con il passare del tempo. Poiché i PCB contengono un’elevata quantità di metallo, se esposti all'ossigeno sono soggetti a corrosione.
Rivestimento conforme
Per prevenire i danni causati dagli agenti atmosferici, al PCB viene applicato dopo l’assemblaggio un rivestimento protettivo non conduttivo noto come rivestimento conforme (Figura 1). Questo viene comunemente applicato ai PCB per i dispositivi consumer, elettrodomestici e mobile, dove è comune operare in presenza di umidità, polvere o altri fattori ambientali difficili. Lo strato protettivo applicato al PCB permette all’umidità presente nei layer del PCB di fluire verso l’esterno, evitando tuttavia che gli agenti esterni possano raggiungere la scheda e i suoi componenti, compromettendone il funzionamento. Oltre ad aumentare l’affidabilità, il rivestimento conforme estende la durata del circuito.
Figura 1: applicazione del rivestimento conforme
I tipi più comuni di rivestimento conforme sono silicone, resina acrilica, poliuretano e p-xilene, ognuno in grado di fornire un determinato livello di protezione. Il silicone, ad esempio, è in grado di coprire la più ampia gamma di temperature e rappresenta quindi la scelta più adatta per le applicazioni con temperature estreme. Per contro, il silicone ha uno scarso potere adesivo su alcuni tipi di substrato e resistenza chimica inferiore rispetto alla resina acrilica. Quest’ultima, a causa della sua struttura rigida, non è particolarmente indicata in presenza di urti e vibrazioni. I poliuretani offrono un’elevata resistenza a umidità, abrasione e vibrazioni, sopportano bene le basse temperature ma non le temperature elevate. Ne consegue che essi sono utilizzati soprattutto nelle applicazioni con temperature da -40°C a +120°C. Il p-xilene è un materiale consistente che offre elevata protezione, ma è costoso ed essendo sensibile agli agenti contaminanti deve essere applicato sottovuoto.
Per quanto riguarda l’applicazione del rivestimento conforme al PCB, si possono utilizzare quattro tecniche: immersione, rivestimento selettivo automatizzato, spruzzatura e spazzolatura. Ognuna di queste alternative raggiunge lo stesso obiettivo: coprire completamente il PCB compresi gli spigoli vivi e tutti i bordi della scheda. Dopo l’applicazione, il rivestimento conforme viene polimerizzato tramite essiccazione all'aria, forno o mediante luce UV.
Temperature elevate
La crescente densità dei componenti presenti sul PCB comporta un inevitabile aumento delle temperature operative, una condizione che a lungo andare può compromettere l’integrità delle saldature o degli stessi layer a causa della dilatazione e contrazione di materiali con proprietà fisiche differenti. Un PCB per alte temperature dovrebbe pertanto utilizzare un dielettrico con temperatura di transizione vetrosa (Tg) almeno pari a 170°C. Una regola normalmente applicata è quella di consentire temperature operative fino a circa 25°C inferiori rispetto al valore Tg del materiale utilizzato. Oltre alla scelta del materiale, la temperatura elevata del PCB può essere gestita rimuovendo il calore prodotto e trasferendolo in altre zone del PCB. Se il componente caldo è montato sul lato superiore del PCB e ha una superficie sufficientemente ampia, su di esso può essere installato un dissipatore di calore in grado di rimuovere il calore prima per conduzione (dal componente al dissipatore) e, successivamente, per convezione (dalle superfici del dissipatore verso l’aria circostante, più fredda). Se il componente caldo è montato sul lato inferiore del PCB e non è possibile montare un dissipatore di calore, la tecnica normalmente utilizzata dai progettisti consiste nell'inserire sul PCB un elevato numero di via termici per trasferire il calore lontano dal componente caldo verso uno strato di rame sul lato superiore del PCB, da dove può essere trasferito ulteriormente a un dissipatore di calore adeguato. Normalmente, i dissipatori di calore montati sui PCB sono grandi, con superfici alettate o corrugate per aumentare l’area di dissipazione. Le ventole possono essere aggiunte per migliorare il raffreddamento per convezione forzata, rispetto al raffreddamento per convezione naturale.
Uno dei metodi tradizionalmente impiegati per contrastare gli effetti prodotti dalle alte temperature è quello utilizzare la tecnologia heavy copper. Questa aumenta la corrente massima sopportabile dalle tracce del PCB e, a causa della minore resistenza, riduce le perdite di calore.
Misure antiradiazione
Per le missioni spaziali a lungo termine, l'unica opzione disponibile è quella di utilizzare componenti resistenti alle radiazioni ("rad-hard"). Questi componenti sono molto più rari e di conseguenza più costosi rispetto ai componenti standard. Per le missioni spaziali a breve termine (fino a un anno) può essere consentito l’utilizzo di componenti commerciali standard, previa analisi e verifica della loro capacità di sopportare le radiazioni. Ciò consente di ridurre i costi di progettazione delle apparecchiature spaziali e di espandere la selezione dei componenti disponibili per la progettazione. Applicando diverse tecniche di progettazione hardware si possono contrastare gli effetti prodotti dalle radiazioni. A livello di progettazione del PCB, è ad esempio importante assicurare un adeguato collegamento a terra di tutte le parti metalliche.
Protezione meccanica e corrosione
Per fornire protezione contro urti e vibrazioni, il PCB può essere installato in un contenitore in cui viene versata la resina per incapsularlo completamente. Maggiore è lo strato di resina, migliore è il grado di protezione. A meno che tutti i componenti sul PCB non abbiano un'altezza uniforme, lo spessore dello strato di resina varierà tuttavia lungo la scheda, fornendo livelli di protezione leggermente diversi per ogni componente. Lo strato di resina più sottile corrisponde dunque, nel caso peggiore, al livello di protezione offerto su tutta la scheda. Prima ancora di considerare l'incapsulamento con la resina, il PCB deve essere pulito a fondo. La contaminazione superficiale può avere un impatto negativo sui livelli di protezione offerti dall'incapsulamento, in particolare nei casi di resistenza chimica (in quanto fornisce un percorso più facile per la penetrazione delle sostanze chimiche). Inoltre, i contaminanti influenzeranno negativamente la capacità della resina di assorbire shock fisici e termici a causa della debole formazione di strati tra la resina e il PCB, che alla fine porta alla delaminazione. Mantenere il PCB pulito e asciutto assicura inoltre protezione contro la ruggine e la contaminazione ionica. La corrosione può essere evitata sia con l’applicazione del rivestimento conforme, sia tramite finiture superficiali come HASL (il PCB viene immerso in una lega di stagno e piombo liquefatto e successivamente i depositi della lega vengono livellati con dei getti ad aria calda) e ENIG (immersione in oro). In Figura 2 è visibile il particolare di un PCB con finitura ENIG.
Figura 2: PCB con finitura ENIG