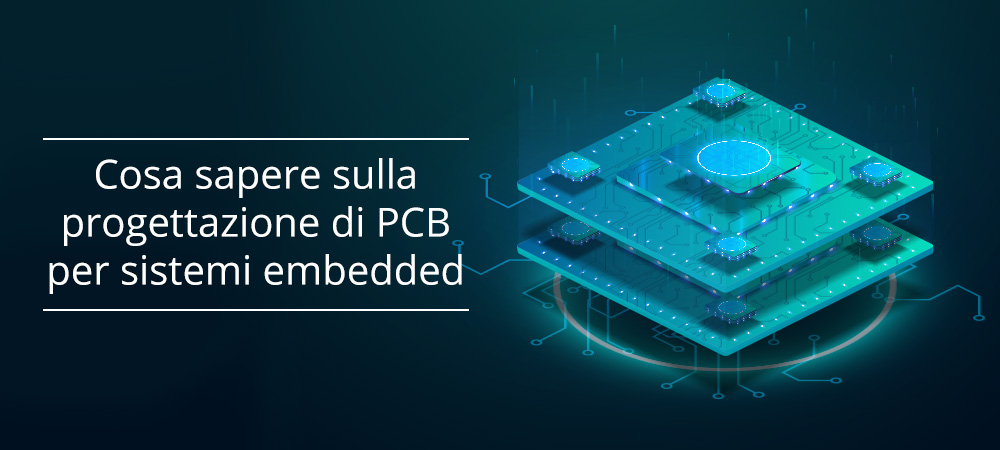
Negli ultimi anni, la crescente domanda di dispositivi mobili, indossabili ed elettromedicali ha comportato una progressiva riduzione delle dimensioni dei circuiti elettronici embedded. I requisiti legati alle nuove funzionalità introdotte, inclusa la connettività wireless e l’utilizzo di display ad elevata risoluzione, hanno inevitabilmente aumentato la densità dei componenti, imponendo sfide senza precedenti ai progettisti elettronici. Elevata integrazione, basso assorbimento di potenza ed eccellente gestione termica sono solo alcuni dei requisiti che molte applicazioni embedded di ultima generazione devono soddisfare. La riduzione delle dimensioni del PCB non solo permette di soddisfare le richieste di miniaturizzazione provenienti dal mercato, ma consente anche di conseguire un significativo risparmio sui costi di produzione. In questo articolo verranno presentate le principali tecniche di fabbricazione e gli accorgimenti che i progettisti possono utilizzare per realizzare con successo un circuito stampato destinato alle applicazioni embedded.
Dimensione del PCB
La dimensione rappresenta uno dei vincoli progettuali più ovvi e importanti nella progettazione di un PCB. Il layout e le dimensioni del PCB devono essere concordati con chi si occupa della progettazione meccanica, in modo tale da consentire un’agevole installazione del circuito all’interno del contenitore. In ogni caso, il PCB non può essere troppo piccolo, in quanto deve garantire il corretto posizionamento dei componenti ed evitare il surriscaldamento della scheda. Poiché la maggior parte dei componenti discreti presenti in un sistema embedded è di tipo passivo, l’utilizzo della tecnologia SMD è praticamente obbligatorio. Ciò consente di ridurre il footprint e la distanza tra i componenti, ottenendo un layout del PCB molto compatto. Un secondo aspetto su cui il progettista può lavorare per ottimizzare la dimensione del PCB è il routing. Laddove i requisiti di spazio lo consentono, una tendenza diffusa è quella di realizzare PCB doppia faccia. Questa soluzione consente infatti un agevole montaggio dei componenti SMD su entrambe le facce, comporta una complessità del routing non particolarmente elevata e semplifica notevolmente le fasi di test, riparazione ed eventuale rilavorazione del circuito. Utilizzando un numero maggiore di layer, si incrementa lo spazio disponibile per il posizionamento delle tracce e, di conseguenza, si può ottenere un routing più efficiente. Ciò spiega perché la maggior parte dei dispositivi indossabili ad elevata integrazione, come ad esempio gli smartwatch, hanno un PCB con fino a sei layer. Esiste, tuttavia, un inconveniente da tenere presente: con il crescere del numero di layer, aumenta la complessità del circuito ed il tempo richiesto per eseguire il debug o per apportare eventuali modifiche. Un buon compromesso, per molte tipologie di sistemi embedded, è rappresentato dai PCB con quattro layer, la cui tipica struttura (stackup) è visibile in Figura 1. Le due facce esterne sono utilizzate non solo per il posizionamento e per la connessione dei componenti con tracce di tipo microstrip, ma anche per realizzare piani di massa (GND). I layer interni sono invece utilizzati per l’istradamento dei segnali tramite tracce di tipo stripline e per realizzare i piani di potenza (POWER).
Normalmente, le tracce che portano i segnali di alimentazione e i percorsi di ritorno a terra sono quelle percorse dalle correnti di maggiore intensità e, pertanto, hanno uno spessore maggiore rispetto alle altre tracce, con una larghezza in genere non inferiore a 40 mil (questa può essere calcolata tramite uno degli appositi calcolatori disponibili anche online). Queste tracce possono essere collocate sui due layer esterni, mentre le tracce per i segnali di bassa potenza sono più adatte ad occupare i layer interni.
Figura 1: Stackup di un PCB a 4 strati.
Particolare attenzione deve essere posta all’altezza dei componenti (in particolare condensatori elettrolitici e connettori), un aspetto spesso trascurato in quanto la maggior parte degli strumenti software per la progettazione dei PCB operano in due dimensioni, con vista del layout dall’alto.
e riceverete un preventivo per il vostro progetto di PCBA entro 10 minuti!
Posizionamento dei componenti
Il posizionamento dei componenti deve rispecchiare le regoli generali per la progettazione di un PCB, come l’allineamento (che deve semplificare sia la saldatura che l’assemblaggio) e la separazione tra componenti analogici e digitali. Inoltre, occorre evitare di posizionare i componenti più pesanti in prossimità dei bordi del PCB, in quanto la scheda tenderebbe ad incurvarsi. Al fine di ridurre gli stress meccanici sui punti di saldatura, questi componenti andrebbero posizionati sul lato del PCB normalmente rivolto verso l’alto. Se possibile, i componenti di potenza non devono essere concentrati nella stessa zona, ma distribuiti il più possibile uniformemente sul piano della scheda, favorendo così la dissipazione termica. Molto importante è anche la scelta del package corretto per ogni componente. I componenti passivi SMD sono disponibili in un elevato numero di package con footprint anche molto differente, come visibile in Figura 2. Mentre nella progettazione del prototipo è preferibile utilizzare package con dimensioni maggiori (che semplificano l’assemblaggio e il test del circuito), per la versione di produzione è consigliabile utilizzare package che occupano uno spazio inferiore. Occorre inoltre assicurarsi quale sia il package minimo supportato dal processo di assemblaggio, in quanto non tutte le macchine pick-and-place gestiscono tutti i tipi di formati.
Figura 2: Componenti SMD con differenti formati.
Gestione termica
Quando una traccia è percorsa da una corrente di elevata intensità, viene prodotta una quantità di calore non trascurabile. Per migliorare la dissipazione termica mantenendo le dimensioni del PCB il più possibile ridotte, il progettista ha a disposizione due tecniche, combinabili tra loro:
- aumentare lo spessore delle tracce;
- creare delle aree o interi piani di rame con lo scopo di dissipare il calore.
Come suggerito dallo standard IPC2221A, i piani di rame dovrebbero avere uno spessore di 10 oz (35 µm), ma questo spessore può essere incrementato. Raddoppiando ad esempio lo spessore (20 oz o 70 µm), la larghezza della traccia potrebbe essere ridotta del 50% a parità di corrente. Inoltre, uno spessore di 20 oz migliora enormemente la dissipazione termica. Se il sistema embedded deve gestire potenze elevate, come nel caso di convertitori, inverter o driver per motori, si può utilizzare la tecnica heavy copper che comporta spessori del rame compresi tra 4 e 10 oz.
La formazione di punti con elevata concentrazione del calore, detti hot-spot, dovrebbe essere evitata, mantenendo la temperatura massima raggiunta dal PCB inferiore a circa 170°C. Questa condizione può essere rilevata conducendo un’analisi termografica con una termocamera, oppure attraverso un opportuno modello e software per la simulazione termica. Un’altra tecnica comunemente utilizzata per migliorare la dissipazione del calore consiste nell’inserimento sulle tracce di opportuni fori, detti via termici. Nel caso di PCB a doppia faccia, i via termici collegano tra loro i layer superiore ed inferiore, aumentando così sia la superficie che il volume in grado di dissipare il calore. Nel caso invece di un PCB multistrato, i via termici collegano tra loro più layer, anche interni al PCB. Affinché siano efficaci, i via termici devono essere posizionati il più possibile vicini ai componenti che sviluppano la quantità maggiore di calore, possibilmente al di sotto di essi.
Componenti embedded
I sistemi embedded di ultima generazione sono caratterizzati da elevata densità di componenti e footprint estremamente ridotto. Per semplificare sia la fase di progettazione del PCB che quella di assemblaggio, sempre più progettisti stanno adottando la tecnologia basata sui componenti embedded. Attraverso questa tecnica, induttori, resistenze e condensatori vengono in incorporati direttamente nel PCB. Ciò consente di ridurre la lunghezza delle tracce, il numero di saldature e i costi, migliorando le prestazioni elettriche del circuito e la sua affidabilità. Resistenze, condensatori e induttori sono posizionati sui layer interni, tramite stampa o etching, durante il processo di fabbricazione del PCB. Successivamente, essi vengono incorporati nel PCB con il processo di laminazione del circuito stampato multistrato. Gli induttori includono anche i modelli dotati di nucleo magnetico. I nuclei ferromagnetici sono incorporati in un substrato del PCB, mentre gli avvolgimenti induttivi sono realizzati tramite fotolitografia e altri processi standard per la fabbricazione dei PCB. Anziché essere costruiti uno alla volta, i componenti sono disposti su un pannello PCB e fabbricati utilizzando un processo automatico. Nella maggior parte dei casi, il nucleo embedded ha la forma di un anello (toroide). I nuclei toroidali sono relativamente facili da produrre e generalmente poco costosi rispetto ad altre forme di nucleo. I materiali comunemente utilizzati sono le ferriti ceramiche pressate e i metalli amorfi avvolti su nastro. In Figura 3 è visibile un avvolgimento di induttore composto da dieci spire, interamente integrato in un PCB.
Figura 3: Un esempio di componenti embedded nel PCB.