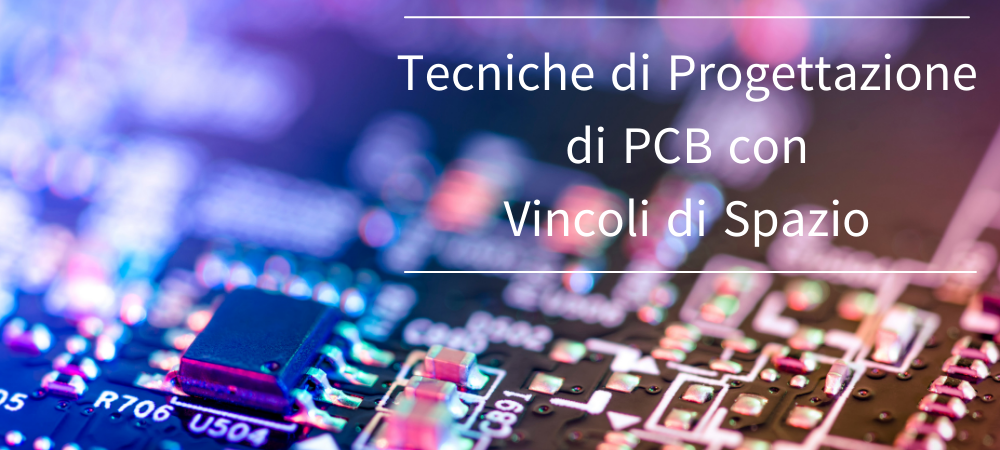
In seguito ai miglioramenti ottenuti nel campo delle tecnologie elettroniche, la progettazione dei circuiti stampati ha subito dei cambiamenti significativi in termini di dimensioni e forma. Tali cambiamenti hanno comportato una crescente domanda per circuiti stampati con elevate prestazioni e fattore di forma ridotto, imponendo delle sfide maggiori rispetto alle tradizionali tecniche di progettazione dei PCB.
Durante la fase di progettazione del PCB, l’assegnamento dello spazio richiesto per il layout del circuito richiede che il progettista assuma alcune decisioni importanti sotto diversi punti di vista. Tali decisioni avranno un effetto determinante sulla qualità del prodotto lungo tutto il suo ciclo di vita. Ne consegue che i vincoli a cui deve sottostare il layout di un circuito stampato rappresentano uno dei fattori chiave per determinare il valore della progettazione di un circuito stampato.
e riceverete un preventivo per il vostro progetto di PCBA entro 10 minuti!
Le esigenze di miniaturizzazione interessano tutti i settori dell’elettronica, creando nuove sfide ai progettisti e agli ingegneri impegnati a trovare soluzioni adatte in circuiti con vincoli di spazio. I progettisti devono pertanto garantire il corretto funzionamento del circuito elettronico e del circuito stampato anche in presenza di vincoli di spazio.
Progettazione e struttura di un PCB
La definizione della struttura del circuito stampato è uno dei primi e più importanti passaggi della progettazione di un PCB. È importante che il progettista crei un contorno del circuito stampato contenente le aree del PCB soggette a limiti di altezza o larghezza, i componenti utilizzati e le relative tracce di collegamento. I contorni e l’area occupata dal PCB determineranno la forma meccanica finale della scheda da produrre.
Cut-out: la progettazione deve essere eseguita molto accuratamente a livello meccanico, in modo tale da rappresentare le dimensioni e la forma esatte di ogni cut-out. Durante questa fase, devono essere rispettate le corrette dimensioni e le eventuali tolleranze elettriche specifiche. Inizialmente, il progettista può creare il contorno del cut-out utilizzando una linea sottile (0,50 mm di larghezza), il cui centro può essere utilizzato per rappresentare il contorno esatto del cut-out.
Angoli interni di un cut-out: Ogni cut-out deve essere fresato utilizzando un utensile da 2,00 mm, assicurandosi che l'angolo interno abbia un raggio minimo di 1,00 mm. Se è richiesto un raggio di dimensioni più piccole, occorre apportare delle opportune modifiche a livello meccanico.
Dimensione degli slot: nei circuiti stampati, gli slot sono dei fori o fessure troppo ampi per essere ottenuti tramite le tradizionali tecniche di perforazione. Gli slot dovrebbero essere definiti accuratamente a livello meccanico, specificandone l’esatta dimensione, ampiezza e tolleranza. Esistono due tipi principali di slot:
- Slot placcati: nel processo di fabbricazione del PCB, questi slot sono ottenuti tramite placcatura in rame. Quando gli slot di un PCB sono placcati in rame sia nella parte superiore, sia in quella inferiore, si parla di slot placcati.
- Slot non placcati: gli slot non placcati sono formati da un foro più grande rispetto alla dimensione in rame del Negli slot non placcati, si creano delle sovrapposizioni di pad, in quanto il produttore crea gli slot non placcati dopo aver eseguito il processo elettrolitico.
Figura 1: Dimensioni di uno slot sul PCB
Fonte: protoexpress.com
Vincoli di routing nei PCB
A causa della crescente complessità dei circuiti elettronici, la fase di routing del PCB ha assunto un ruolo di importanza fondamentale. Nella progettazione di un circuito stampato, esistono diverse regole che possono aiutare il progettista a definire i collegamenti esistenti tra i vari componenti, consentendo la trasmissione di dati e segnali dall’ingresso all’uscita del circuito. Queste regole vengono utilizzate per prevenire problemi durante il processo di fabbricazione o la produzione su larga scala, garantendo prestazioni elettriche ai massimi livelli.
Di seguito sono elencati alcuni tra i parametri che possono rappresentare dei vincoli per la fase di routing di un PCB.
Componenti: esistono diversi vincoli, a cui il progettista deve adeguarsi, relativi al posizionamento e alla spaziatura di componenti come resistenze, condensatori, transistor, circuiti integrati e altro ancora. Qualora non diversamente specificato, la distanza ideale tra i componenti dovrebbe essere almeno pari a 0,25 mm. I componenti con dimensioni inferiori a quelle di un package SMD 0603 (lunghezza di 0,060 pollici e larghezza di 0,030 pollici) dovrebbero avere uno spazio libero di 0,15 mm. I vincoli possono anche essere imposti dal progettista a una specifica e limitata porzione del PCB, a causa di vari fattori di natura elettrica come livelli di potenza, trasferimento di calore, ecc.
Ampiezza della traccia:
Figura 2: Ampiezza di una traccia
Fonte: designwanted.com
I progettisti hanno la possibilità di impostare la larghezza delle tracce in ogni parte del circuito. La larghezza della traccia riveste un ruolo fondamentale nel controllo dell'impedenza. In tutti i casi cui la potenza può assumere un valore variabile, le tracce del PCB devono avere una larghezza maggiore. Nelle applicazioni a radiofrequenza (RF), è molto comune trovare tracce con larghezze differenti tra loro.
Routing delle tracce:
Figura 3: Routing delle tracce
Fonte: pcbdesignworld.com
Oltre ai valori minimi di larghezza e distanza tra le tracce, la progettazione di un PCB richiede che il routing sia eseguito in modo molto accurato. Utilizzando ad esempio il classico percorso a serpentina, il progettista può accoppiare la lunghezza di una traccia con quella di un'altra traccia, soddisfacendo in questo modo i vincoli legati alla lunghezza minima e massima per ogni traccia. Anche i vicoli relativi alla topologia possono essere applicati al routing di un PCB, assicurandosi che esso segua un particolare modello, come la topologia a T.Piani: un’opportuna gestione termica del PCB può essere ottenuta attraverso un collegamento con i piani di massa e quelli di alimentazione. Ad ogni piano può essere associato uno spessore minimo di rame e una propria conformazione. I piani di massa o di alimentazione comportano alcuni vantaggi, tra cui:
- Migliore disaccoppiamento tra i circuiti: La superficie di un piano può fungere da condensatore di disaccoppiamento a piastre parallele tra lo strato isolante e la massa. Questo aspetto è molto utile, in quanto aiuta a prevenire la propagazione, in diverse parti del circuito, del rumore generato dalle linee di alimentazione.
- Percorsi di ritorno della corrente più brevi: Percorsi di ritorno della corrente più brevi offrono una migliore compatibilità elettromagnetica (EMC), dovuta alla maggiore facilità di trovare un cammino tra il layer del segnale e il piano di alimentazione.
- Maggiore capacità di trasferimento dell’energia: I piani sono in grado di sopportare correnti di intensità maggiore rispetto alle tracce, riducendo di conseguenza le temperature di esercizio del PCB.
Interconnessioni ad Alta Densità (HDI)
In ambito PCB, il termine HDI (acronimo di High-Density Interconnect) identifica una tecnologia che aiuta a produrre PCB più piccoli, leggeri e compatti. Nello scenario attuale, i dispositivi elettronici stanno diventando sempre più piccoli e compatti, integrando tuttavia funzionalità sempre più complesse. Per rispondere a queste esigenze, l'utilizzo di PCB multistrato realizzati con le tecniche tradizionali può creare dei problemi come la diafonia, o compromettere l’integrità del segnale. Tali problemi possono essere affrontati e risolti grazie alla tecnologia HDI, utilizzata soprattutto nei dispositivi compatti con dimensioni molto ridotte.
Perché HDI?
La principale differenza tra i PCB convenzionali e i PCB prodotti utilizzando la tecnologia HDI, è che questi ultimi hanno una maggiore densità di cablaggi per unità di superficie rispetto ai PCB normali, consentendo così la produzione di dispositivi elettronici performanti più piccoli e leggeri. La tecnologia HDI utilizza materiali e layer con spessori molto ridotti rispetto ai normali PCB, consentendo la realizzazione di dispositivi piccoli e complessi.
Uno dei fattori più critici nella tecnologia HDI è rappresentato dall'integrità del segnale, a causa della ridotta distanza tra le tracce del circuito. Questo problema può essere risolto con l’utilizzo di microvie, che offrono una capacità parassita e un'induttanza molto piccole a causa delle loro ridotte dimensioni. Le microvie hanno un diametro inferiore a 150 micron e sono quindi ottenute tramite perforazione laser. È così possibile utilizzare più layer senza aumentare la diafonia e il rumore, garantendo un’elevata integrità del segnale.
Figura 4: Tipi differenti di via
Fonte: mistralsolutions.com
Scelta dei materiali per l’HDI
Nello scegliere il materiale più adatto alla realizzazione del PCB, occorre preferire materiali per il substrato che abbiano una bassa costante dielettrica. Ciò consente di ridurre il rischio di accoppiamento capacitivo tra due layer adiacenti, anche nel caso in cui i segnali viaggino molto più velocemente rispetto ai PCB tradizionali. Ne consegue che l'integrità del segnale viene conservata, riducendo la diafonia tra layer adiacenti. Questo aspetto è particolarmente importante nella tecnologia HDI, dove un elevato numero di tracce è concentrato in un'area piccola e densa.
Come substrato, viene tipicamente utilizzato l'etere epossidico, grazie al suo basso costo e alle buone proprietà termiche, chimiche ed elettriche. Oltre a questo materiale, a causa dei loro bassi valori Dk (costante dielettrica) e Df (fattore di perdita dielettrica), vengono utilizzate anche resine poliimmidiche e esteri di cianato. Oltre alle resine termoindurenti, per la loro natura flessibile vengono utilizzate anche resine termoplastiche come la poliimmide (PI) e il politetrafluoroetilene (PTFE).
Tecnologia dei PCB flessibili
I circuiti stampati flessibili (FPC) rappresentano un importante progresso nel campo della tecnologia PCB e permettono di risolvere la maggior parte dei problemi legati ai vincoli di spazio. Molte tipologie di cablaggi, utilizzate nei PCB per applicazioni differenti, sono state sostituite con successo dai circuiti stampati flessibili, i quali riducono i costi di cablaggio elettrico di quasi il 70%. Grazie alla loro compattezza e flessibilità, gli FPC consentono di eseguire con successo un elevato numero di connessioni elettriche.
Figura 5: Circuito Stampato Flessibile
Fonte: raypcb.com
Struttura di un circuito stampato flessibile
Analogamente a un normale PCB rigido, i circuiti stampati flessibili possono essere suddivisi in PCB a singola faccia, doppia faccia, o multistrato. Rispetto al circuito stampato rigido, lo spazio per il tracciamento del pad, la spaziatura e larghezza della traccia e la dimensione del pad rimangono gli stessi. Ciò è possibile grazie ai materiali flessibili e al processo di placcatura utilizzati per la fabbricazione degli FPC. La composizione di un circuito stampato flessibile è la seguente:
- Pellicola di substrato dielettrico: la pellicola di substrato dielettrico è il materiale base che compone il substrato. La poliammide (PI), è il materiale maggiormente utilizzato per la realizzazione della pellicola, grazie alla sua elevata resistenza alla trazione e alla temperatura.
- Conduttori elettrici: I conduttori elettrici, composti da rame, sono utilizzati per realizzare le tracce di un FPC.
- Materiali adesivi: Realizzati in polietilene o resina epossidica, i materiali adesivi vengono utilizzati per unire tra loro le varie parti che compongono un FPC.
Figura 6: Struttura di un Circuito Stampato Flessibile
Fonte:proto-electronics.com
Conclusioni
Per risolvere i problemi legati ai vincoli di spazio, occorre assicurarsi che i componenti posizionati sul PCB abbiano uno spazio libero sufficiente rispetto agli altri componenti (ad esempio 0,25 mm) e che il routing delle tracce sia stato eseguito tenendo in debita considerazione la larghezza di ogni traccia, ottenuta eseguendo appropriati calcoli basati su vari parametri elettrici. I microvia possono essere utilizzati per garantire che la temperatura della scheda rimanga sotto controllo, migliorando in questo modo la capacità di trasferimento della potenza e il disaccoppiamento tra le varie parti del circuito.
La tecnologia HDI consente di realizzare PCB con spessori molto ridotti ed elevata densità di interconnessioni. L’utilizzo di microvia migliora la gestione termica e garantisce che l'integrità dei segnali sulla scheda rimanga inalterata.
Una valida alternativa per risolvere i problemi di spazio limitato nei PCB è quella di utilizzare i circuiti stampati flessibili (FPC). Questi circuiti trovano applicazione in numerosi dispositivi che utilizziamo nella nostra vita quotidiana, come smartphone, fotocamere, tablet, stampanti, laptop e possono persino essere inseriti all'interno del corpo umano per realizzare pacemaker e altri dispositivi elettromedicali.
11.04.2022