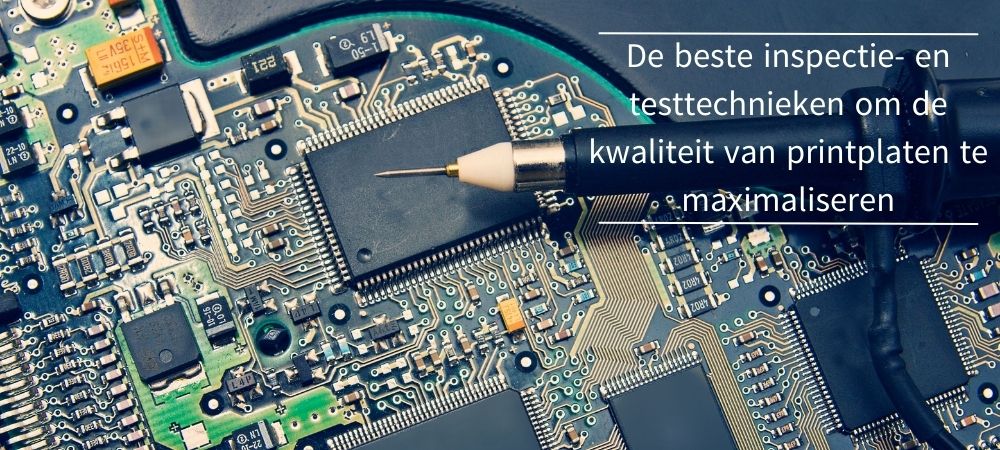
Inspectie en testen zijn twee essentiële fasen van de fabricage van printplaten die een objectieve evaluatie van de kwaliteit van het eindproduct mogelijk maken. Zelfs als ingenieurs alle regels en adviezen voor goed ontwerp opvolgen, bestaat er nog het risico op fouten, bugs of menselijke fouten. Het opsporen en oplossen van deze problemen, voordat de printplaat het eindstadium van de ontwikkeling bereikt, is een fundamentele vereiste om de prestaties, de functionaliteit en de betrouwbaarheid van het product te waarborgen.
Vandaag zijn er apparaten die volautomatische printplaattests kunnen uitvoeren die meteen in dezelfde productieomgeving als de printplaat kunnen worden uitgevoerd. De belangrijkste technieken die momenteel beschikbaar zijn, zijn functioneel testen, optisch onderzoek met camera's en röntgeninspectie. Het is ook mogelijk de printplaat te testen na de assemblagefase, met alle componenten naar behoren aangebracht en gesoldeerd.
Optische inspectie scant de printplaat op zoek naar mogelijke soldeerproblemen, zoals bruggen, kortsluitingen of elektrische verbindingen van slechte kwaliteit. Deze systemen maken gebruik van mobiele camera's met hoge resolutie, die vaak zelfs verkeerd geplaatste of ontbrekende componenten kunnen opsporen. Sommige testsystemen maken ook gebruik van röntgeninspectie in drie dimensies, waarmee problemen kunnen worden opgespoord die niet zichtbaar zijn met standaard optische inspectie. Met röntgensystemen kunnen bijvoorbeeld onvolkomenheden worden opgespoord in solderingen onder BGA (Ball Grid Array)-geïntegreerde schakelingen en flip-chips (een voorbeeld van een flip-chippakket is te zien in figuur 1).
Figuur 1: een geïntegreerde schakeling met een flip-chippakket
Automatische optische inspectie
Bij automatische optische inspectie, ook bekend als AOI, wordt gebruik gemaakt van het optische signaal dat wordt gedetecteerd door één camera (2D-visie) of door meerdere camera's (3D-visie) om te controleren op defecten in printplaten, met een resolutie tot enkele µm. Deze methode levert resultaten op die alleen geldig zijn op printplaten waarop de te controleren solderingen, verbindingen, pads en sporen optisch controleerbaar zijn. De AOI-techniek blijkt ook zeer nuttig te zijn voor de vroegtijdige opsporing van assemblageproblemen, zoals kortsluitingen, open schakelingen, dun soldeerwerk, krassen op sporen enzovoort.
De hogeresolutiebeelden die door 2D/3D-camera's worden verkregen worden vergeleken met beelden van een modelprintplaat (ook bekend als het "golden board") of met een beeldbank met goede en defecte printplaten. De AOI-techniek is in staat om alle controles (die anders handmatig zouden moeten worden uitgevoerd) op een volledig automatische, nauwkeurige en snelle manier uit te voeren. Bovendien is het mogelijk om na de assemblagefase de juiste positionering van de componenten te detecteren, zowel op het printplaatvlak als langs de verticale as (met de AOI 3D-techniek kan ook de hoogte van de componenten worden gedetecteerd). AOI heeft het voordeel dat het direct aan het eind van de productielijn van de printplaat kan worden toegevoegd, zodat eventuele defecten vroegtijdig kunnen worden gedetecteerd. Omdat het echter een passieve methode is, kunnen alleen defecten op het printplaatoppervlak worden gedetecteerd.
Röntgeninspectie
In vergelijking met andere inspectiemethoden detecteert AXI-technologie (Automatic X-Ray Inspection) onvolkomenheden in printplaten die niet zichtbaar zijn met het blote oog of met een optisch AOI-systeem. Röntgenstralen zijn namelijk in staat om zowel door de printplaatlagen als het componentenpakket te dringen, waardoor zeer gedetailleerde 2D- of 3D-beelden worden gegenereerd. Dit maakt het bijvoorbeeld mogelijk om soldeerproblemen op te sporen op Ball Grid Arrays (BGA's) of op verborgen pads. Bij de productie van kleine partijen printplaten of tijdens de prototyperingsfase is het vaak voldoende om de röntgeninspectie alleen uit te voeren op de componenten met niet-zichtbare pads.
Hoewel dit waarschijnlijk de techniek is die de beste resultaten oplevert, is voor AXI goed opgeleid personeel nodig en is het een lang en duur proces. Dit rechtvaardigt het gebruik ervan voor printplaten die op grote schaal worden geproduceerd of voor bijzonder kritische en complexe toepassingen. Voor BGA-componenten biedt deze techniek uitstekende resultaten (zie figuur 2 voor een voorbeeld), omdat hiermee de verborgen soldeerpunten tussen de component zelf en het printplaatoppervlak kunnen worden gecontroleerd.
Figuur 2: Röntgeninspectie van een BGA-component
Inspectie met infraroodstraling
De inspectie van een printplaat met infraroodstraling (ook bekend als thermografie) maakt gebruik van de warmte die door de componenten en door de printplaat zelf wordt afgegeven. Deze techniek is bijzonder geschikt voor stroomtoepassingen waarbij de betrokken stromen hoger zijn. Infraroodinspectie, uitgevoerd met speciale thermische camera's (zoals FLIR), kan informatie opleveren die anders met optische inspecties niet beschikbaar zou zijn.
Bepaalde defecten aan printplaten, zoals onvoldoende soldeerwerk, kunnen de elektrische weerstand op specifieke punten van de schakeling verhogen, met als gevolg een temperatuurstijging die door een infraroodcamera kan worden gedetecteerd.
Een veelgebruikt proces bij thermografie is beeldsubtractie. De relevante software neemt een beeld voordat het apparaat wordt ingeschakeld, waardoor een ideaal thermisch profiel wordt gecreëerd. Dit referentiebeeld wordt vervolgens ‘afgetrokken’ van de volgende beelden, die worden verkregen na het inschakelen van het apparaat, waardoor de statische gereflecteerde temperatuurwaarden worden geëlimineerd en alleen de werkelijke temperatuurverschillen ten gevolge van de verhitting van de printplaat en de componenten overblijven.
Het is belangrijk te benadrukken dat zowel thermografie als röntgeninspectie het ook mogelijk maken eventuele vervalsingen of ongeoorloofde klonen van de printplaat op te sporen.
In-circuittest
In-circuittesten (ook bekend als ICT) is een volledig geautomatiseerde test die in staat is fabricage- of assemblagefouten van printplaten op te sporen door middel van een nauwkeurig verificatieproces met het schema.
Door de printplaat op een spijkerbed te plaatsen, krijgt deze test toegang tot specifieke punten van de schakeling en meet hij de prestaties van elke afzonderlijke component op een volledig onafhankelijke manier ten opzichte van de andere componenten die ermee verbonden zijn. Parameters zoals weerstand, capaciteit, impedantie en meer kunnen worden gemeten, samen met de werking van sommige analoge componenten, zoals op-amps. Het is ook mogelijk het gedrag van bepaalde digitale schakelingen te meten, hoewel hun complexiteit een volledige controle meestal oneconomisch maakt. Met behulp van de ICT-techniek is het mogelijk een volledige test van de printplaat uit te voeren, waarbij men zich ervan kan vergewissen dat de schakeling correct is gemaakt. De gevonden defecten omvatten kortsluitingen en open schakelingen, ontbrekende of verkeerd georiënteerde componenten, soldeerfouten en dergelijke meer. Voor grote partijen printplaten is het mogelijk aangepaste testmaskers te maken om de ICT sneller en efficiënter uit te voeren. Een ander voordeel is de hoge dekkingsgraad van de defecten, die kan oplopen tot 98%.
Het grootste nadeel van deze techniek zijn de hoge kosten, die alleen te rechtvaardigen zijn bij grootschalige productie. Bovendien moet voor elke printplaat een speciaal spijkerbed worden gemaakt en kan de controle alleen worden uitgevoerd op bepaalde punten van de printplaat die overeenkomen met de door de ontwerper opgegeven testpunten.
Bewegende-sondetest
In vergelijking met de in-circuittest heeft de bewegende-sondetest het voordeel dat de kosten lager zijn. Bij deze techniek wordt gebruik gemaakt van een bewegende sonde die volledig automatisch en op configureerbare wijze in contact wordt gebracht met de op de printplaat aanwezige elektrische aandachtspunten. Deze punten omvatten componentpinnen, via’s, pads en dergelijke meer. In vergelijking met ICT heeft de bewegende-sondetest het voordeel dat hij een groot aantal punten op de printplaat kan testen en niet alleen de testpunten die door de ontwerper op de printplaat zijn aangebracht. Bovendien is er geen op maat gemaakt apparaat nodig (zoals het spijkerbed) en eventuele wijzigingen aan de componenten of aan het oorspronkelijke printplaatontwerp vereisen slechts een software-update.
Dankzij het grote aantal punten dat kan worden gecontroleerd, garandeert de bewegende-sondetest een hogere defectdekking dan de ICT-test. Het is echter een veel trager proces, dat onaanvaardbaar kan worden voor grootschalige printplaatproductie. Figuur 3 toont apparatuur voor het automatisch testen van printplaten met een bewegende sonde.
Figuur 3: Printplaattest met bewegende sonde
Functionele test
De functionele test van een printplaat wordt normaliter uitgevoerd in de eindfase van het project, waarbij de functionaliteit en het gedrag van de printplaat onder verschillende op de testbank gesimuleerde bedrijfsomstandigheden worden geverifieerd. De functionele test wordt zeer vaak uitgevoerd om specifiek gedrag te verifiëren dat door de klant wordt aangegeven, waarbij de printplaat wordt blootgesteld aan verschillende vormen van elektrische en omgevingsstress.
Deze test moet ervoor zorgen dat het Device Under Test (DUT) werkt zoals verwacht. Afhankelijk van de complexiteit van het project en de eisen die moeten worden getest, kan de functionele test variëren van een eenvoudige voedingstest (inschakelen/uitschakelen) tot een complete test met specifieke communicatieprotocollen en speciale testsoftware. Vanwege de flexibiliteit kan functioneel testen worden gebruikt ter vervanging van duurdere testprocedures. Door een nauwkeurige simulatie van de werkelijke bedrijfsomgeving levert de functionele test onmiddellijke resultaten op over de kwaliteit van het project, en om deze reden wordt hij steeds meer gebruikt bij de productie van kleine partijen, om er zo voor te zorgen dat elke printplaat die de productielijn verlaat, klaar is voor gebruik in het veld.
Hoewel het een vrij goedkope procedure is die op elk type printplaat kan worden toegepast, biedt de functionele test een dekking van defecten die strikt afhankelijk is van de tijdens de test uitgevoerde controles. Bovendien kan de printplaat, wanneer hij aan hoge stress wordt blootgesteld, het al snel na het slagen voor de functionele test begeven.
Inbrandtest
De inbrandtest (of burn-in test), die een aantal punten gemeen heeft met de functionele test, controleert de prestaties van een printplaat en zoekt naar niet-zichtbare defecten voordat de printplaat het veld ingaat. Tijdens de inbrandtests worden de printplaten blootgesteld aan extreme omstandigheden die de nominale bedrijfsomstandigheden overschrijden. Het doel is mogelijke storingen vroegtijdig op te sporen en de werking van de apparatuur onder zware belasting te testen, zodat kan worden geanticipeerd op mogelijke problemen die zich bij werkelijk gebruik kunnen voordoen. In tegenstelling tot andere inspectiemethoden, waarbij alleen indicatoren van mogelijke defecten worden gecontroleerd, simuleert de inbrandtest extreme bedrijfsomstandigheden die mogelijke defecten kunnen veroorzaken.
Deze extreme bedrijfsomstandigheden omvatten meestal variaties in temperatuur, spanning, stroom, bedrijfsfrequentie, of andere bedrijfsomstandigheden die relevant zijn voor de DUT. De resultaten van deze test zijn zeer nuttig voor ontwerpers, die nauwkeurige informatie kunnen krijgen om de oorzaak van de defecten te begrijpen en het ontwerp- of fabricageproces te optimaliseren.