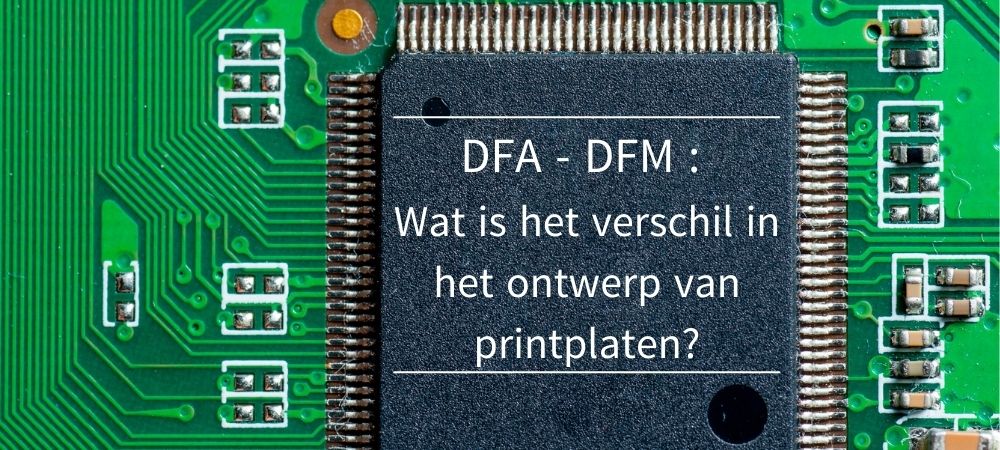
In de huidige markten is er grote druk op elektronische bedrijven om steeds meer geminiaturiseerde producten te ontwikkelen en te produceren, in steeds kortere tijd en met steeds lagere kosten. Om de vereiste kwaliteitsnormen te kunnen garanderen, is het noodzakelijk het aantal ontwerpiteraties tot een minimum te beperken, concurrerend te blijven en de marktintroductietijd zoveel mogelijk te verkorten.
Met betrekking tot het ontwerp van een printplaat zijn er in feite twee basiseisen waaraan elk project moet voldoen:
- de printplaat moet betrouwbaar op grote schaal kunnen worden geproduceerd
- de printplaat moet zonder problemen kunnen worden geassembleerd.
Door het grootschalige gebruik van componenten met ultra kleine verpakkingen en de toenemende dichtheid van componenten op de printplaat wordt het steeds moeilijker om aan deze eisen te voldoen. De ontwerpers moeten daarom passende controles invoeren die tijdens de verschillende stappen van de ontwikkelingscyclus worden uitgevoerd en herhaald, om ervoor te zorgen dat het eindproduct werkt en uitvoerbaar is zoals bedoeld. Het is belangrijk op te merken dat bij dit proces over het algemeen niet alleen de ontwerpers betrokken zijn, maar ook de fabrikanten en assembleurs van de printplaat.
DFM en DFA
De twee concepten die de bovenstaande eisen samenvatten zijn DFM en DFA. DFM, acroniem voor Design for Manufacturing, zorgt ervoor dat het printplaatontwerp voldoet aan de eisen die door het fabricageproces worden gesteld, op basis van kenmerken als minimale spoorbreedte, minimale afstand tussen sporen, minimale gatbreedte en meer, die moeten worden geverifieerd voordat de printplaat in productie gaat. Het komt er dus op aan te anticiperen op mogelijke problemen op het niveau van de printplaatlay-out door middel van een reeks regels of controles die de naam DRC (Design Rule Checking) dragen.
DFA, acroniem voor Design for Assembly, heeft daarentegen tot doel de effecten te evalueren die de ontwerpkeuzen zullen hebben op de assemblagefase van de printplaat. Het doel van DFA is een product te verkrijgen met een optimaal aantal componenten en waarvoor processen en materialen nodig zijn die de assemblage kunnen vereenvoudigen en de totale kosten kunnen verlagen.
Daarom vullen DFM- en DFA-analysetechnieken de mogelijke leemten op tussen het ontwerp van een printplaat en de productie- en assemblagefasen daarvan, op basis van de controle van enkele parameters en sleutelfactoren die tegenwoordig grotendeels met automatische hulpmiddelen kunnen worden uitgevoerd. De kosten die gepaard gaan met de afwezigheid of ontoereikendheid van de DFM- en DFA-analyse kunnen de uiteindelijke kosten van de printplaat aanzienlijk beïnvloeden (tot 20%). Daarom is het van essentieel belang dat de DFM- en DFA-analyse vroeg worden uitgevoerd, voordat de eerste prototypes worden gemaakt, zodat problemen of onverwachte kosten tijdens de productie- en assemblagestappen worden voorkomen.
De belangrijkste voordelen van DFM- en DFA-analyse kunnen als volgt worden samengevat:
- vermindering van het aantal iteraties dat vereist is voor productontwikkeling
- verkorting van de marktintroductietijd
- vermindering van het percentage defecten dat tijdens de productie- en assemblagestappen wordt gevonden
- verhoging van de betrouwbaarheid en duurzaamheid van het product
- kostenvermindering
DFM-analyse
Elk PCB-project produceert als output een reeks Gerber-bestanden die gedetailleerde informatie bevatten over:
- gebruikte materialen en hun eigenschappen
- type stackup en eigenschappen van elke afzonderlijke laag
- aantal, positie en eigenschappen van de gaten
- aantal, positie en eigenschappen van de testpunten
- de oppervlakte-afwerking die op de printplaat moet worden aangebracht
- informatie over soldeermasker en silkscreen
- informatie over printplaatpanelisering
Door het uitvoeren van de DFM-analyse kan de fabrikant aan de hand van deze informatie beoordelen of een printplaat daadwerkelijk kan worden vervaardigd met de beschikbare apparatuur en processen. In deze fase kunnen potentiële problemen worden opgespoord die het fabricageproces ernstig kunnen beïnvloeden. De DFM-analyse kan bijvoorbeeld de aanwezigheid van scherpe hoeken op de sporen aan het licht brengen, die mogelijk zuur kunnen vasthouden tijdens het etsproces van de printplaat. Het opgesloten zuur zou verbindingsproblemen kunnen veroorzaken, met name open stroomkringen. We weten dat de oplossing voor dit probleem is om alle scherpe hoeken te vervangen door bogen, of door een paar hoeken van 45°. Hoewel dit een zeer eenvoudig voorbeeld is, zijn er vele andere problemen die niet gemakkelijk te identificeren zijn tijdens de printplaatontwikkelingsfase.
Hieronder volgt een selectie van de meest voorkomende problemen:
- zuurvallen - we hebben al geanticipeerd op dit klassieke printplaattopologieprobleem. Dit probleem doet zich meestal voor bij alle scherpe hoeken (zoals in het voorbeeld van figuur 1), waarbinnen het zuur kan stagneren, tijdens de wasfase, zonder weg te vloeien zoals het hoort. Als gevolg van een ‘overets’-fenomeen (niet bijzonder moeilijk met 4 of 5 mil dikke sporen) kunnen sommige sporen worden onderbroken
Figuur 1: Voorbeeld van een zuurval (bron: TI) - koper- of soldeermaskersplinters - deze fragmenten (geleidend in het geval van koper, of niet-geleidend in het geval van soldeermasker) kunnen zich afzetten op de printplaat en zo potentiële kortsluitingen veroorzaken. Als ze groot zijn, kunnen ze echte antennes vormen, met als gevolg het ontstaan van ruis of interferentie, vooral als ze sporen beïnvloeden waarop hogesnelheidssignalen worden overgedragen. De beste manier om dit probleem op te lossen is het vermijden van te dunne kopergebieden, vooral waar de sporen de pads kruisen. Een minimumresolutie van het etsproces van 0,004-0,006" voorkomt probleemverbindingen
- (ook bekend als ‘uitgehongerde thermiekbellen’) die geïsoleerd blijven van het voedingsvlak - deze verbindingen verbinden meestal de thermische pads met de thermische dispersievlakken, die nodig zijn om de warmte tijdens het soldeerproces doeltreffend af te voeren. Soms kan er een leemte ontstaan tussen het thermisch pad en het vlak, waardoor er een slechte verbinding ontstaat en de warmteoverdracht minder doeltreffend is. Uitgehongerde thermiekbellen kunnen problemen veroorzaken zowel tijdens het lassen als tijdens het assemblageproces. Onjuiste warmteoverdracht kan ook leiden tot oververhitting en daaruit voortvloeiende schade aan de printplaat
- onvoldoende ringvormige ring - indien de grootte van een gat groter is dan die van de ronde pad waarin het moet worden geboord, kan dit een ontkoppeling van de pin of een kortsluiting veroorzaken. Daarom moet in de fase van de lay-outdefinitie voldoende ruimte worden voorzien voor elke ringvormige ring, zoals aangegeven in figuur 2
Figuur 2: ringvormige ring op ronde pads (bron: Altium) - koper te dicht bij de randen van de printplaat - ook in dit geval moet een gepaste afstand worden gelaten tussen elk koperspoor of -vlak en de randen van de printplaat. Anders bestaat de mogelijkheid dat er kortsluiting of elektrische ontladingen ontstaan wanneer de printplaat onder spanning wordt gezet
- ontbrekend of ontoereikend soldeermasker - ook al is de toepassing van het soldeermasker niet strikt noodzakelijk in alle toepassingen, het biedt het voordeel dat het de schakeling beschermt tegen oxidatie en atmosferische agentia, waardoor de soldeerfase eenvoudiger en betrouwbaarder wordt
- gebruik van ongeschikte materialen en substraten - de laatste generatie elektronische apparatuur gebruikt digitale signalen en klokbronnen bij steeds hogere frequenties, die steeds dichter bij het radiofrequentiebereik komen. In veel gevallen kan een traditioneel substraat zoals FR-4, goedkoop en gemakkelijk verkrijgbaar, ontoereikend blijken en aanleiding geven tot gevaarlijke oververhitting, thermische drift of zelfs beschadiging. De materialen die voor de substraten worden gebruikt, eventueel in combinatie met elkaar, moeten op de juiste wijze worden gekozen voordat met de productie van de printplaat wordt begonnen.
Hoewel de mogelijke fouten die de ontwerper kan maken bij het definiëren van de lay-out talrijk zijn, kunnen deze door het uitvoeren van de DFM-analyse al in een vroeg ontwikkelingsstadium worden opgespoord. Er zijn tegenwoordig verscheidene DFM-tools beschikbaar op de markt, die de ontwerper in deze delicate fase kunnen bijstaan en zo hoge herontwerpkosten kunnen vermijden. Dergelijke tools kunnen worden gebruikt door ontwerpers die niet noodzakelijk bekwaam zijn in fabricage. Bovendien is het mogelijk vooraf gedefinieerde parameters en regels voor elke fabrikant te configureren, zodat de DFM-analyse kan worden aangepast aan de werkelijke kenmerken en systemen van degenen die daadwerkelijk met de productie te maken zullen krijgen.
DFA-analyse
Assemblage kan worden beschouwd als het meest tijdrovende en kostbare fabricageproces van printplaten. De ontwerp- en ontwikkelingsfasen van een printplaat omvatten twee assemblagefasen: de assemblage van de prototypeprintplaat en de assemblage van de productieprintplaat. Beide fasen moeten worden opgenomen in de DFA-analyse bij het ontwerpen van de printplaat.
Hoewel het doel van de DFA-analyse verschilt van dat van de DFM-analyse, zijn veel technieken en strategieën uitwisselbaar toepasbaar op alle fasen van het ontwerp van een printplaat. De DFA-analyse is gericht op de assemblagefase en houdt in de eerste plaats rekening met de kenmerken en eigenschappen van de componenten die op de printplaat zullen worden gemonteerd, met het doel hun aantal en types te minimaliseren en de voorkeur te geven aan standaard, betrouwbare, gemakkelijk te vinden en eenvoudig te assembleren componenten.
De DFA-analyse leidt in het algemeen tot een verbetering van de betrouwbaarheid van de printplaat door bijvoorbeeld alleen componenten te selecteren van fabrikanten die garanties bieden voor een betrouwbare nauwkeurigheid, stabiliteit en levering. Als uit de DFA-analyse bijvoorbeeld blijkt dat een bepaalde component verouderd is, moet de ontwerper informatie verstrekken over een mogelijke geschikte vervanging.
Hoewel de tijdens de DFA-analyse uitgevoerde controles divers en talrijk zijn, is een mogelijke selectie als volgt:
- overeenstemming tussen elke component en de bijbehorende pads
- minimale afstand tussen componenten
- juiste aanwezigheid van soldeermasker en vaste merktekens
- juiste afmetingen en positie van de gaatjes
- beschikbaarheid van voldoende vrije ruimte aan de randen van de printplaat
- juiste toepassing van thermische reliëfs
- beschikbaarheid van componenten, nu en op middellange termijn
- mogelijkheid tot panelisering van de printplaat voor grootschalige productie
- testbaarheid van de printplaat
- weerstand tegen trillingen en mechanische spanningen, afhankelijk van de specifieke toepassing.
Indien ontwerpers de toepassing van de DFA-techniek als integraal onderdeel van het PCB-ontwerp verwaarlozen, is de kans veel groter dat zij op toekomstige problemen stuiten bij de assemblage van de printplaat, met als gevolg een verlenging van de productiecyclus en hogere kosten.
Het gebruik van DFM en DFA-analyses garandeert niet alleen een optimale werking van de schakeling, maar zorgt er ook voor dat deze laatste op grote schaal kan worden geproduceerd en geassembleerd, zonder verhoging van de kosten, risico's en tijd.