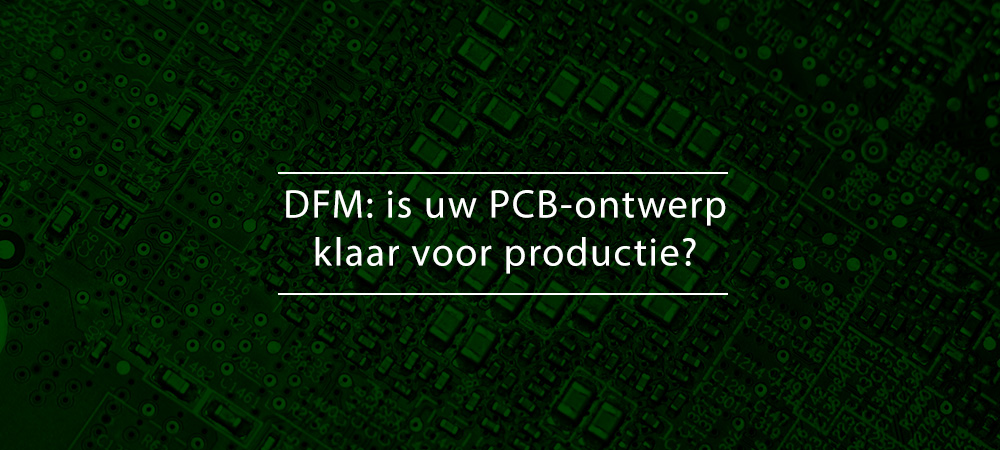
De term DFM (Design For Manufacturing) verwijst naar het proces waarbij een product wordt ontworpen met het precieze doel de productie ervan te vereenvoudigen, zodat een beter product ontstaat tegen lagere kosten. Idealiter wordt DFM al toegepast tijdens de eerste fasen van het project en wordt het hele productontwikkelingsteam erbij betrokken en niet alleen de hardware-ontwerpers. Naarmate het project vordert in de verschillende stadia van de levenscyclus van het product, neemt elke wijziging aan het oorspronkelijke project steeds meer gewicht en kosten met zich mee, en soms kan het zelfs bijzonder complex worden om het uit te voeren. Anderzijds kan door de toepassing van DFM in de beginfase van de ontwikkeling van een printplaat elke mogelijke wijziging snel worden doorgevoerd, tegen zo laag mogelijke kosten en met behoud van de oorspronkelijke prestaties van het product. Technologie speelt een sleutelrol in veel aspecten van ons leven. Smartphones, smartwatches, huishoudelijke apparaten, verbonden auto’s, ... alles maakt gebruik van slimme technologie en connectiviteit. Deze en andere toepassingen vereisen printplaten van toenemende complexiteit, met de vraag om ze te produceren tegen de laagste kosten, in de kortst mogelijke tijd en met een hoog kwaliteitsniveau.
Voordelen van DFM
Aangezien de productie van printplaten in verschillende stappen verloopt, moet men er ruim op voorhand zeker van zijn dat er geen ‘Design for Manufacturing’ (DFM)-kwesties zijn met de printplaat die
ernstige problemen kunnen veroorzaken. Tijdens de ontwikkelingsfase moeten de ontwerpers rekening houden met elektrische beperkingen, zoals de waarde van de betrokken spanningen en stromen, het stroomverbruik en het thermisch beheer. In de echte wereld spelen echter ook andere factoren een rol, zoals de nauwkeurigheid of de tolerantie van de machines voor de productie van printplaten en de kenmerken van de gebruikte materialen. DFM is nu juist het proces dat het mogelijk maakt de lay-out van de printplaat te organiseren met de bedoeling er zeker van te zijn dat hij kan worden geproduceerd. Een voorbeeld hiervan is de ringvormige ring, of het koperen padgebied dat overblijft nadat er een gat in is geboord. De ring wordt gemeten van de rand van de pad tot de rand van het gat en vormt een fundamentele parameter in het ontwerp van de printplaat, omdat de plating die erop wordt aangebracht de elektrische verbinding tussen de ene en de andere zijde van het gat mogelijk maakt. In het geval van meerlagige kaarten moeten de ringvormige ringen worden uitgelijnd met een voldoende overlapping om de verbinding tussen de verschillende lagen mogelijk te maken. Een perfecte uitlijning bestaat alleen op papier: zelfs de modernste laserboren kunnen geen nauwkeurigheid van 100% bereiken. Het DFM-proces zorgt ervoor dat de breedte van de ringvormige ring zodanig is dat een kleine afwijking tussen de lagen mogelijk is zonder de elektrische verbinding in gevaar te brengen.
De belangrijkste voordelen van DFM toegepast op het ontwerp en de productie van printplaten zijn de volgende
- hogere productkwaliteit - DFM vermindert het aantal wijzigingen dat nodig is om het oorspronkelijke ontwerp aan te passen aan de productieprocessen en -installaties van de printplaten, wijzigingen die de productkwaliteit in gevaar kunnen brengen;
- verkorting van de tijd tot de markt - het productieproces is onderverdeeld in talrijke fasen, die elk een bron van potentiële fouten kunnen zijn. DFM helpt vertragingen te beperken die worden veroorzaakt door defecte producten, fouten en tijd die wordt besteed aan het controleren van projectbesprekingen en documentatie;
- kostenverlaging - dankzij DFM kunnen printplaatontwerpers printplaten ontwerpen die gemakkelijk kunnen worden geproduceerd, zelfs bij grote productievolumes. De lagere kosten vloeien ook voort uit het lagere aantal fouten dat tijdens het productieproces van de printplaat wordt gedetecteerd.
DFM versus DRC
Printplaatontwerpers voeren vaak een procedure uit die Design Rule Checking (DRC) wordt genoemd. We kunnen ons dan ook afvragen of, na het succesvol uitvoeren van de DRC, er een noodzaak is om ook de DFM uit te voeren. Het antwoord op die vraag is ja, want de twee procedures zijn eigenlijk verschillend, en beide zijn nodig om het project van een printplaat met succes in productie te brengen. DRC is immers een automatisch analyseproces dat het project vergelijkt met de regels die door de gieterij zijn opgelegd. Deze regels bepalen de minimale fysieke vereisten voor de printplaat, de lagen en de netten, die een invloed kunnen hebben op de prestaties van het systeem. Het doel van de DRC is om eventuele afwijkingen of fouten op te sporen. De DFM identificeert dan weer alle aspecten die problemen kunnen veroorzaken tijdens het productieproces van de printplaat. Als het DRV-proces een fout detecteert, zal deze op elk exemplaar van de printplaat aanwezig zijn. De problemen waarop DFM daarentegen stuit, kunnen zich slechts voordoen op enkele exemplaren van de printplaat en zelfs pas een lange tijd na de productie.
Hoe de DFM-beginselen toepassen op printplaten
Hoewel de normen voor de productie van printplaten voor elke fabrikant anders kunnen zijn, zijn er enkele algemene DFM-regels waaraan moet worden voldaan voordat een productieproces wordt toegepast. Om een printplaatontwerp klaar voor productie te verklaren, moeten enkele basis-DFM-beginselen worden toegepast. Hier is een lijst van de meest relevante richtlijnen:
- afstand tussen componenten - componenten die te dicht bij elkaar op de printplaat zitten, kunnen problemen veroorzaken voor de automatische systemen die voor de assemblage worden gebruikt, zoals ‘pick & place’-machines, waardoor het herwerken van het ontwerp nogal problematisch wordt. Hetzelfde geldt voor de connectoren, die correct moeten worden geplaatst om de verbindingen van de printplaat met de buitenkant te vereenvoudigen;
- plaatsing en rotatie van de componenten - de wijze waarop de componenten op de printplaat zijn geplaatst kan van invloed zijn op het soldeerproces, vooral als de componenten onregelmatig of ongelijkmatig zijn gerangschikt. Alle gelijksoortige componenten moeten in dezelfde richting georiënteerd zijn, zodat alle componenten goed gelast zijn wanneer ze door de soldeeroven gaan;
- onjuiste padgrootte van componenten - onjuiste padgroottes kunnen leiden tot ongelijkmatige verwarming van de pad tijdens het reflow-solderen. Dit kan op zijn beurt leiden tot gedeeltelijk loskomen van de component van de printplaat, een fenomeen dat bekend staat als "tombstoning";
- zuurvallen - bij de routing van de printplaatsporen moeten scherpe hoeken worden vermeden, omdat die ernstige problemen kunnen veroorzaken bij het verwijderen van etschemicaliën van de printplaat, waardoor de dikte van de sporen zelf afneemt. Door ervoor te zorgen dat de hoeken tussen de sporen altijd kleiner zijn dan 90 graden, wordt vermeden dat sporen van de printplaat delamineren na de productie van de printplaat;
- optimalisatie van gaten: veel printplaatontwerpen gebruiken te veel verschillende groottes van gaten, een aspect dat moet worden vermeden om de productiekosten van de printplaat te verminderen
- gebrek aan soldeermasker tussen pads, wat soldeerbruggen kan vormen en mogelijk kortsluiting kan veroorzaken tussen twee pads die niet met elkaar mogen worden verbonden. Controleer daarom altijd zorgvuldig of elk pad een voldoende soldeermasker heeft om de vereiste speling te garanderen;
- silkscreen op pads: de overlapping, zelfs gedeeltelijk, van de silkscreen op de pads veroorzaakt problemen tijdens het solderen, met mogelijk rampzalige gevolgen op lange termijn. Figuur 3 toont een voorbeeld van deze toestand die absoluut moet worden vermeden;
Figuur 1: voorbeeld van silkscreen op pads
- open-luscontrole: deze toestand doet zich typisch voor wanneer het oorspronkelijke project wordt herwerkt om enkele wijzigingen aan te brengen.. In feite creëert het aansluiten van een nieuw net zonder het bestaande te verwijderen, typisch een eindeloze lus;
- validatie van de voor het project gebruikte bestanden: ondanks het feit dat het een vrij oud bestandsformaat is, wordt Gerber nog steeds in veel printplaatprojecten gebruikt. Hoewel Gerber-bestanden wijdverbreid zijn, kunnen ze problemen opleveren wanneer het project wordt vertaald naar een fysiek object. Het gebruik van Gerber-bestanden vereist bijvoorbeeld een afzonderlijk bestand voor elke laag van de printplaat: dit betekent dat u een groot aantal bestanden moet bijhouden om te vermijden dat ze door elkaar worden gehaald of met elkaar worden verward.