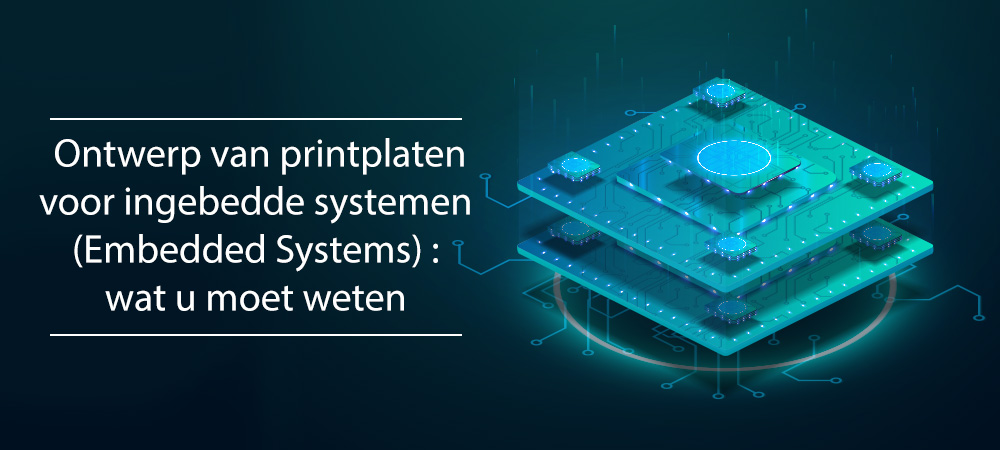
In de afgelopen jaren heeft de groeiende vraag naar mobiele, draagbare en elektromedische apparatuur geleid tot een geleidelijke verkleining van de omvang van ingebedde elektronische schakelingen. De eisen met betrekking tot de nieuwe functies, waaronder draadloze connectiviteit en het gebruik van displays met hoge resolutie, hebben onvermijdelijk geleid tot een grotere dichtheid van de componenten, waardoor elektronische ontwerpers voor ongekende uitdagingen zijn komen te staan. Hoge integratie, een laag stroomverbruik en uitstekend thermisch beheer zijn slechts enkele van de eisen waaraan veel ingebedde toepassingen van de laatste generatie moeten voldoen. De verkleining van printplaten maakt het niet alleen mogelijk om aan de vraag naar miniaturisatie vanuit de markt te voldoen, maar ook om aanzienlijke besparingen op de productiekosten te realiseren. Dit artikel geeft een overzicht van de belangrijkste fabricagetechnieken en de trucs die ontwerpers kunnen gebruiken om met succes een printplaat voor ingebedde toepassingen te maken.
Grootte van de printplaten
Grootte is een van de meest voor de hand liggende en belangrijkste beperkingen bij het ontwerp van printplaten. De lay-out en de afmetingen van de printplaat moeten worden afgestemd met de mensen die betrokken zijn bij het mechanisch ontwerp, zodat de schakeling gemakkelijk in de behuizing van het eindproduct kan worden ingebouwd. De printplaat mag in geen geval te klein zijn, omdat hij de juiste plaatsing van de componenten moet garanderen en oververhitting van de printplaat moet worden voorkomen. Aangezien de meeste discrete componenten in een ingebed systeem passief zijn, is het gebruik van SMD-technologie vrijwel verplicht. Hierdoor worden de voetafdruk en de afstand tussen de componenten verkleind, wat resulteert in een zeer compacte lay-out van de printplaten. Een tweede aspect waaraan de ontwerper kan werken om de grootte van de printplaat te optimaliseren is de routering. Wanneer de beschikbare ruimte dit toelaat, is het een wijdverbreide trend om dubbelzijdige printplaten te maken. Deze oplossing maakt een eenvoudige assemblage van SMD-componenten aan beide zijden van de printplaat mogelijk, brengt een niet bijzonder grote complexiteit van de routering met zich mee en vereenvoudigt het testen, repareren en opnieuw bewerken van de schakeling aanzienlijk. Een groter aantal lagen vergroot de beschikbare ruimte voor de plaatsing van de sporen en maakt bijgevolg een efficiëntere routering mogelijk. Dit verklaart waarom de meeste sterk geïntegreerde wearables, zoals smartwatches, een printplaat hebben met tot wel zes lagen. Er is echter een nadeel: hoe meer lagen, hoe complexer de schakeling en hoe meer tijd nodig is voor het debuggen of het aanbrengen van wijzigingen in het oorspronkelijke ontwerp. Een goed compromis, voor veel soorten ingebedde systemen, wordt vertegenwoordigd door printplaten met vier lagen, waarvan de typische structuur (ook wel stackup genoemd) wordt weergegeven in figuur 1. De twee buitenste zijden worden niet alleen gebruikt voor de plaatsing en voor het verbinden van de componenten via microstripsporen, maar ook om aardingsvlakken (GND) te creëren. De binnenlagen worden daarentegen gebruikt voor de routering van signalen via striplijnsporen en om voedingsvlakken (POWER) te creëren.
Gewoonlijk zijn de sporen die stroomsignalen geleiden of als aardingsretourpaden worden gebruikt, de sporen met de hoogste stromen en moeten ze daarom dikker zijn dan de andere sporen. Hun breedte is over het algemeen niet kleiner dan 40 mil en kan worden berekend met behulp van een van de verschillende calculators voor de spoorbreedte, die ook online beschikbaar zijn. Deze sporen kunnen op de twee buitenste lagen worden geplaatst, terwijl sporen die signalen met een laag vermogen geleiden meer geschikt zijn om de binnenste lagen te bezetten.
Figuur 1: een printplaat opgebouwd uit 4 lagen
Bijzondere aandacht moet worden besteed aan de hoogte van de componenten (in het bijzonder elektrolytische condensatoren en connectoren), een aspect dat vaak over het hoofd wordt gezien omdat de meeste software voor het ontwerp van printplaten in twee dimensies werkt, met een bovenaanzicht van de lay-out.
Plaatsing van de componenten
De plaatsing van de componenten moet in overeenstemming zijn met de algemene regels die gelden voor het ontwerp van printplaten, zoals uitlijning (wat zowel het soldeer- als het assemblageproces moet vereenvoudigen) en scheiding tussen analoge en digitale componenten. Verder moet worden vermeden om zwaardere componenten in de buurt van de randen van de printplaat te plaatsen, aangezien de printplaat dan de neiging heeft te buigen. Om de mechanische spanning op de soldeerpunten te verminderen, moeten deze componenten worden geplaatst aan de zijde van de printplaat die normaal naar boven is gericht. Indien mogelijk moeten de vermogenscomponenten niet op één plaats worden geconcentreerd, maar zo gelijkmatig mogelijk over de printplaat worden verdeeld, wat de thermische dissipatie bevordert. De keuze van het juiste pakket voor elke component is eveneens zeer belangrijk. Passieve SMD-componenten zijn verkrijgbaar in een groot aantal pakketten met zeer verschillende voetafdrukken, zoals te zien is in figuur 2.
Terwijl bij het ontwerp van een prototype de voorkeur wordt gegeven aan pakketten met een grotere voetafdruk (wat de assemblage en het testen van de schakeling vereenvoudigt), is het voor de productieversie raadzaam pakketten te gebruiken die minder ruimte innemen. De ontwerpers moeten ook nagaan welk pakket door het assemblageproces minimaal wordt ondersteund, aangezien niet alle pick-and-place machines alle soorten formaten aankunnen.
Figuur 2: SMD-componenten met verschillende pakketten
Thermisch beheer
Wanneer een stroom met een hoge intensiteit door een spoor van een printplaat gaat, wordt een niet te verwaarlozen hoeveelheid warmte geproduceerd. Om de thermische dissipatie te verbeteren en toch de grootte van de printplaat zo klein mogelijk te houden, kan de ontwerper gebruik maken van twee technieken, die eventueel met elkaar gecombineerd kunnen worden:
- de dikte van de sporen vergroten;
- op de printplaat zones of volledige koperen vlakken creëren met het doel de warmte af te voeren.
Zoals de IPC2221A-standaard suggereert, moeten de koperen vlakken 10 oz (35 µm) dik zijn, maar deze waarde kan eventueel worden verhoogd. Door bijvoorbeeld de dikte te verdubbelen (20 oz of 70 µm), kan de spoorbreedte met 50% worden verminderd, met behoud van dezelfde stroomwaarde. Bovendien verbetert een dikte van 20 oz de thermische dissipatie aanzienlijk. Indien het ingebedde systeem hoge stromen moet aankunnen, zoals in het geval van omvormers, inverters of motoraandrijvingen, kan zware kopertechnologie worden gebruikt, waarbij koperdiktes tussen 4 en 10 oz worden gebruikt.
De vorming van punten met een hoge concentratie aan warmte, de zogenaamde hot spots, moet worden vermeden door de maximumtemperatuur die de printplaat bereikt onder 170 °C te houden. Deze toestand kan worden opgespoord door een thermografische analyse uit te voeren met een warmtebeeldcamera, of met behulp van een geschikt model en software voor thermische simulatie. Een andere techniek die vaak wordt gebruikt om de warmtedissipatie te verbeteren bestaat uit het aanbrengen van geschikte gaten in de sporen, de zogenaamde thermische via’s. In het geval van dubbelzijdige printplaten verbinden thermische via’s de bovenste en onderste lagen met elkaar, waardoor zowel het oppervlak als het volume dat warmte kan afvoeren wordt vergroot. In het geval van een meerlaagse printplaten verbinden thermische via’s verschillende lagen met elkaar, zelfs binnenin de printplaat. Om doeltreffend te zijn, moeten de thermische via’s zo dicht mogelijk bij de componenten worden geplaatst die de grootste hoeveelheid warmte ontwikkelen, eventueel eronder.
Ingebedde componenten
De laatste generatie ingebedde systemen worden gekenmerkt door een hoge dichtheid van de componenten en een uiterst kleine voetafdruk. Om zowel het ontwerp als de assemblagefasen van de printplaat te vereenvoudigen, passen steeds meer ontwerpers de ingebedde componententechnologie toe.
Bij deze techniek worden inductoren, weerstanden en condensatoren rechtstreeks in de printplaat ingebed. Dit vermindert de lengte van de sporen, het aantal soldeerpunten en de kosten, en verbetert de elektrische prestaties en de betrouwbaarheid van de schakeling. Weerstanden, condensatoren en spoelen worden tijdens het vervaardigingsproces van de printplaat op de binnenste lagen geplaatst, door ze te bedrukken of te etsen. Vervolgens worden zij in de printplaat ingebouwd tijdens het lamineren van de meerlaagse gedrukte schakeling. Tot de inductoren behoren ook modellen met een magnetische kern. Ferromagnetische kernen worden ingebed in een printplaatsubstraat, terwijl inductieve wikkelingen worden gemaakt via fotolithografie en andere standaard processen voor de fabricage van printplaten. De componenten worden niet één voor één gebouwd, maar op een printplaatpaneel gelegd en via een geautomatiseerd proces vervaardigd. In de meeste gevallen heeft de ingebedde kern de vorm van een ring (toroïde). Toroïdevormige kernen zijn relatief gemakkelijk te vervaardigen en over het algemeen niet duur in vergelijking met andere vormen van kernen. Veel gebruikte materialen zijn geperste keramische ferrieten en amorfe metalen gewikkeld op tape. Figuur 3 toont een spoel die uit tien windingen bestaat, volledig ingebed in de printplaat.
Figuur 3: een voorbeeld van in een printplaat ingebedde componenten